Ironballs
Established Member
Right then this is my WIP competition entry for't big compo. As a reminder, my brief was to design and make a stand for the TV that would also hold the assorted paraphernalia that lives with the TV. The need arose following the demise of our behemoth of a CRT TV that had a dedicated stand, we decided to get a reasonable flat screen and went for a 37" LCD, which is not too heavy (about 12.5kg).
So the stand has to safely hold the TV at a good viewing height and underneath hold the several other boxes. The look had to be reasonably modern and as elegant as possible. So a fairly free reign.
Okay, that was about 3 ish months ago and to be fair, progress has been slow. In fact your average alpine glacier has made more progress, but that's okay, I have a reputation to uphold for speed.
Job number one then, manage the poor readers expectations (and here I feel like a bit of a charlatan), there is no progress. Well not exactly none, but close. I have in the traditional fashion gone and purchased some wood before the design is finalised. Why? Well, because I had a wood buying scratch to itch, you know what it's like...
What I have done is spent some time beavering away on Scribble It (Patent Pending) and come with some world class half assed drawings. These Da Vince-esque sketches have been beautifully rendered and at least allowed me to flesh out some thoughts and put them in front of the in-house design authority. Initial approval granted so I can move to the next stage. Erm, more scribbling.
I have a little time off coming up, so I plan to work on a few projects that need a boot up the rear, this being one. However, my design thoughts have thrown up a few questions so part of my process is to chuck some of these ideas and questions on here and consult the UKW hive mind. You know, cheat.
Anyway, here are some out of focus pictures for you to squint at:
Quality work I'm sure you'll agree.
You'll be pleased to hear that I'm not planning to making wavy legs, I just had to draw them to prove that a) they didn't look right and b) they'd snap. I will be going for a gentle curve in the legs and a useful debate with Colin on his curved legs (on his project, not the things below his waist) has given me a few ideas for getting round the short grain issues.
I plan to join them at the bottom with through dovetail pins and attach them to the top with wedged through tenons. Rear legs/support are very much a fluid idea at the minute and could be one leg or two; as is the top, I need to lay out the various boxes and see what shape I have to work around. The top itself will be glued boards of approx 200-250mm and may be biscuited, I'm trying to decide if I need a batten underneath to give additional support. Sagulator and glue strength indicator says no, but I don't want to gamble with a TV - top width will be approx 20mm IIRC.
Components below will sit on 2 glass shelves, again numerous design issues to work though there, don't want the top expanding so much that it moves the legs apart and the shelves drop out of the supports.
Any road, all comments welcomed, if you see me heading down a blind alley or approaching the cliff of design stupidity please feel free to tap me on the shoulder before I motor on over it
So the stand has to safely hold the TV at a good viewing height and underneath hold the several other boxes. The look had to be reasonably modern and as elegant as possible. So a fairly free reign.
Okay, that was about 3 ish months ago and to be fair, progress has been slow. In fact your average alpine glacier has made more progress, but that's okay, I have a reputation to uphold for speed.
Job number one then, manage the poor readers expectations (and here I feel like a bit of a charlatan), there is no progress. Well not exactly none, but close. I have in the traditional fashion gone and purchased some wood before the design is finalised. Why? Well, because I had a wood buying scratch to itch, you know what it's like...
What I have done is spent some time beavering away on Scribble It (Patent Pending) and come with some world class half assed drawings. These Da Vince-esque sketches have been beautifully rendered and at least allowed me to flesh out some thoughts and put them in front of the in-house design authority. Initial approval granted so I can move to the next stage. Erm, more scribbling.
I have a little time off coming up, so I plan to work on a few projects that need a boot up the rear, this being one. However, my design thoughts have thrown up a few questions so part of my process is to chuck some of these ideas and questions on here and consult the UKW hive mind. You know, cheat.
Anyway, here are some out of focus pictures for you to squint at:
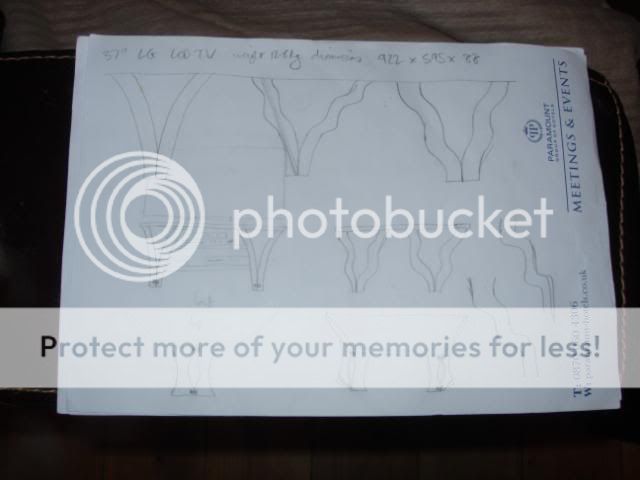
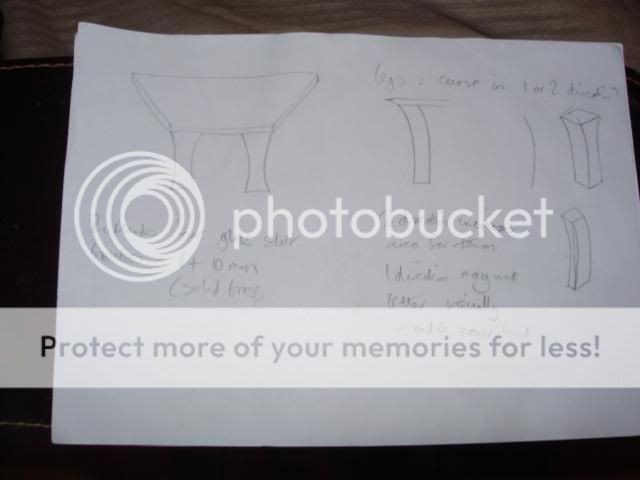
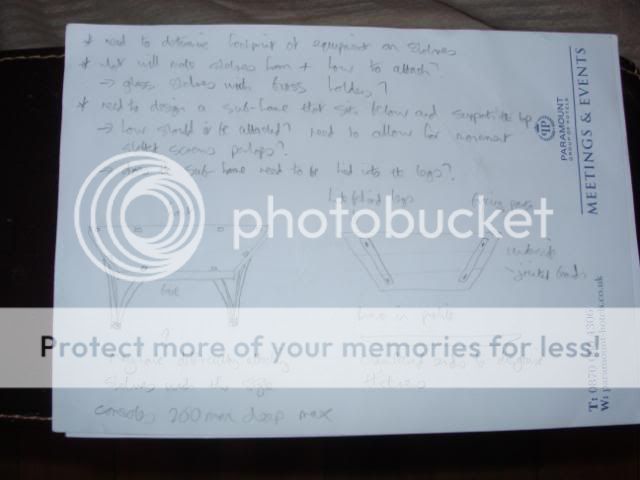
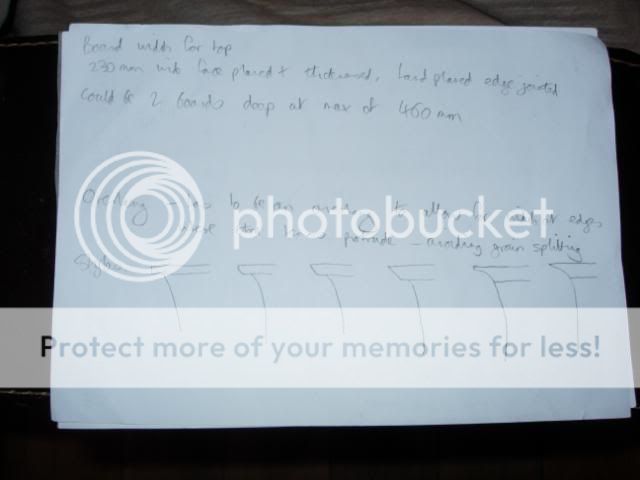
Quality work I'm sure you'll agree.
You'll be pleased to hear that I'm not planning to making wavy legs, I just had to draw them to prove that a) they didn't look right and b) they'd snap. I will be going for a gentle curve in the legs and a useful debate with Colin on his curved legs (on his project, not the things below his waist) has given me a few ideas for getting round the short grain issues.
I plan to join them at the bottom with through dovetail pins and attach them to the top with wedged through tenons. Rear legs/support are very much a fluid idea at the minute and could be one leg or two; as is the top, I need to lay out the various boxes and see what shape I have to work around. The top itself will be glued boards of approx 200-250mm and may be biscuited, I'm trying to decide if I need a batten underneath to give additional support. Sagulator and glue strength indicator says no, but I don't want to gamble with a TV - top width will be approx 20mm IIRC.
Components below will sit on 2 glass shelves, again numerous design issues to work though there, don't want the top expanding so much that it moves the legs apart and the shelves drop out of the supports.
Any road, all comments welcomed, if you see me heading down a blind alley or approaching the cliff of design stupidity please feel free to tap me on the shoulder before I motor on over it