MikeG.
Established Member
As an experiment, I am going to post a small part of my on-going renovation project here: the porch.
Here is the front of the house, with the porch base almost ready:
Oops, looks like the lens needs a wipe.
Here is the porch, ready to assemble:
And here is what I am going to build:
First job was to bring the 2 inch blocks up level with the top of the bricks. I too the novel approach of laying them over-height, and trimming them off afterwards. It wasn't a complete success.
As always, start with the sole plate:
There is a little sloped rebate to the outside. A couple of passes of the circular saw, a clean up with a plane and scraper, and that was easy:
Best James May voice Now, look out for the schoolboy error. Lulled into a false sense of adequacy by the first rebate, on the outside to the plate, I went and ran one on the inside all the way to the end of the piece of wood, without stopping it. The little chamfer on the bottom right hand side of the following piccie:
It was my wife's fault. She called "lunch", and I thought I'd just squeeze the chamfer in before we all sat down...... I knew what I'd done straight away, which rather spoiled lunch. There was only one good solution, I thought: time to do a mitred bridle joint. I don't think I've done one before in oak framing, and it's in a pretty prominent position. What could possibly go wrong?
Note the other rebates in the above image, which shows the plate upside-down. The triangular rebate is simply somewhere for the mortar to go when this piece is bedded, such that if there is any shrinkage or movement there won't be a straight joint through under the plate. The small rectangular rebate is for some lead. more of that in a week or two.
Schoolboy error number two: I did the rebates prior to marking out for the mortises!! This meant I didn't have an edge to work to with my square and mortise gauge. How many years have I been doing this stuff? Oh, and I didn't mention that the wood wasn't straight:
Here are the mortises, and some big notes to myself so I don't make any more cock-ups:
The male side of the mitred bridle joint, with half a mortise:
Here's the other one, sitting in situ:
I knew this wasn't going to be easy:
Not perfect, but OK for the first one. I've got 8 to make, so I'll make a template:
Here is the front of the house, with the porch base almost ready:
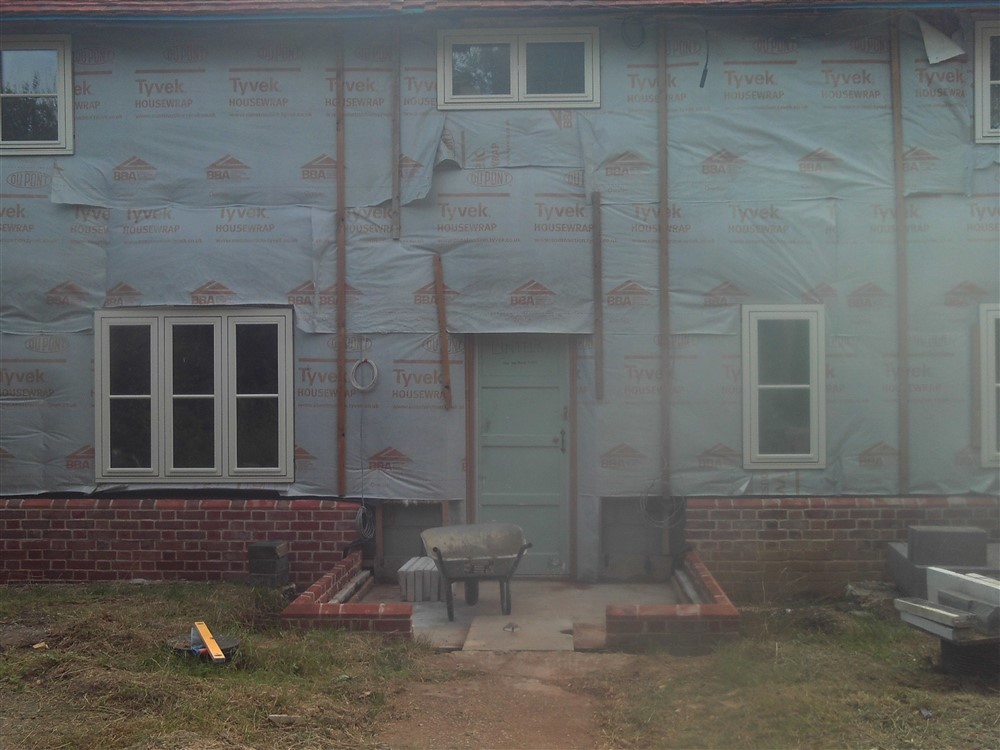
Oops, looks like the lens needs a wipe.
Here is the porch, ready to assemble:
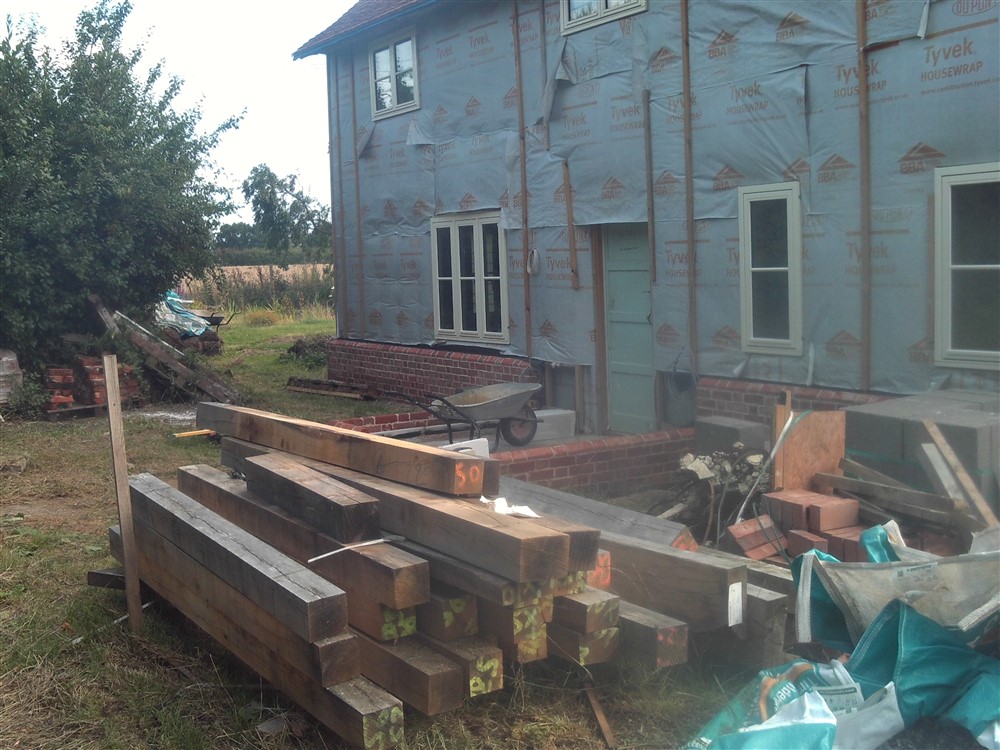
And here is what I am going to build:
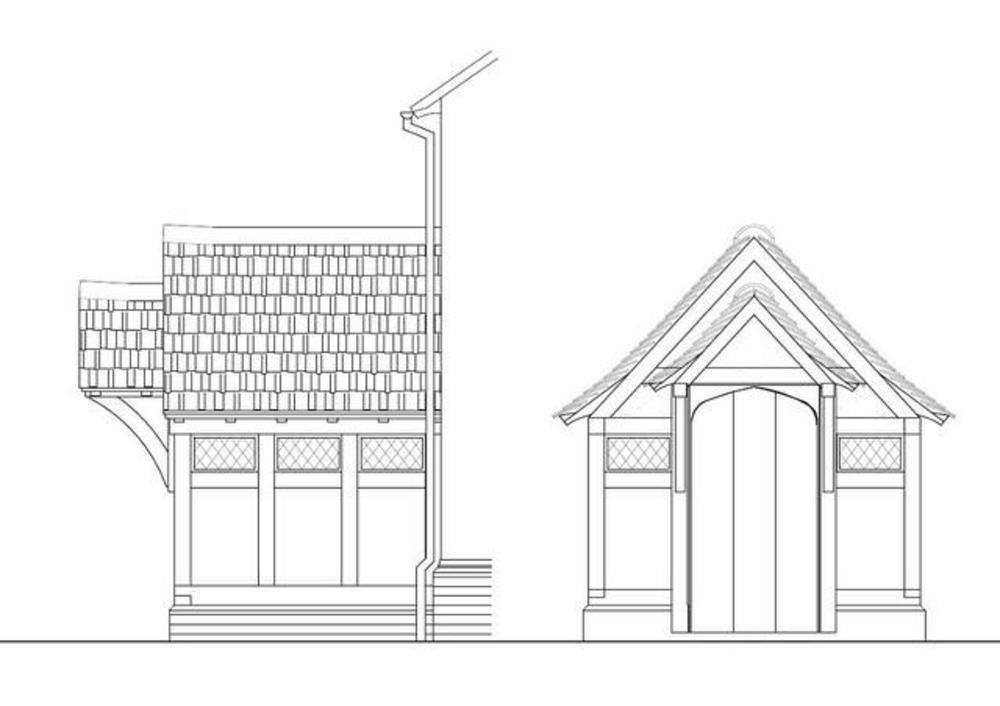
First job was to bring the 2 inch blocks up level with the top of the bricks. I too the novel approach of laying them over-height, and trimming them off afterwards. It wasn't a complete success.
As always, start with the sole plate:
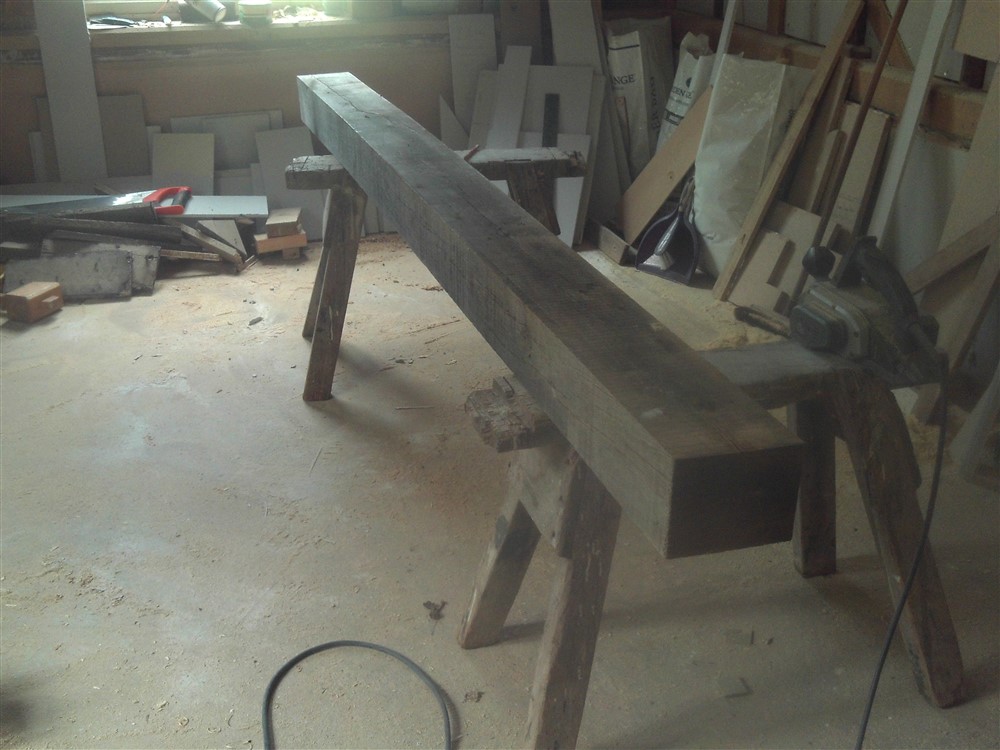
There is a little sloped rebate to the outside. A couple of passes of the circular saw, a clean up with a plane and scraper, and that was easy:
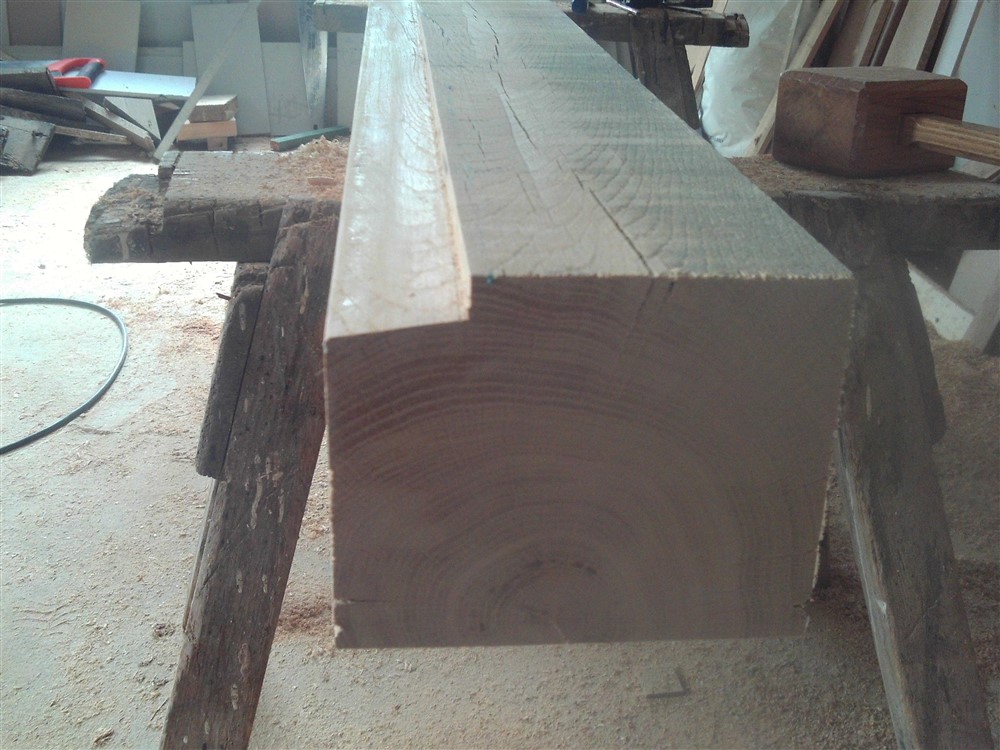
Best James May voice Now, look out for the schoolboy error. Lulled into a false sense of adequacy by the first rebate, on the outside to the plate, I went and ran one on the inside all the way to the end of the piece of wood, without stopping it. The little chamfer on the bottom right hand side of the following piccie:
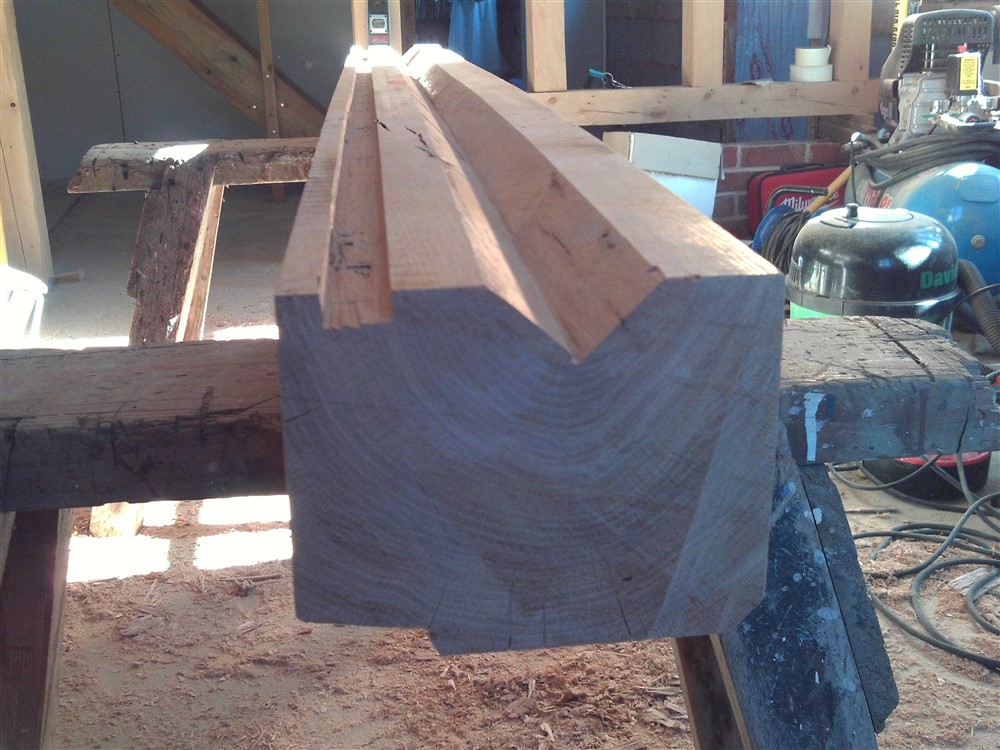
It was my wife's fault. She called "lunch", and I thought I'd just squeeze the chamfer in before we all sat down...... I knew what I'd done straight away, which rather spoiled lunch. There was only one good solution, I thought: time to do a mitred bridle joint. I don't think I've done one before in oak framing, and it's in a pretty prominent position. What could possibly go wrong?
Note the other rebates in the above image, which shows the plate upside-down. The triangular rebate is simply somewhere for the mortar to go when this piece is bedded, such that if there is any shrinkage or movement there won't be a straight joint through under the plate. The small rectangular rebate is for some lead. more of that in a week or two.
Schoolboy error number two: I did the rebates prior to marking out for the mortises!! This meant I didn't have an edge to work to with my square and mortise gauge. How many years have I been doing this stuff? Oh, and I didn't mention that the wood wasn't straight:
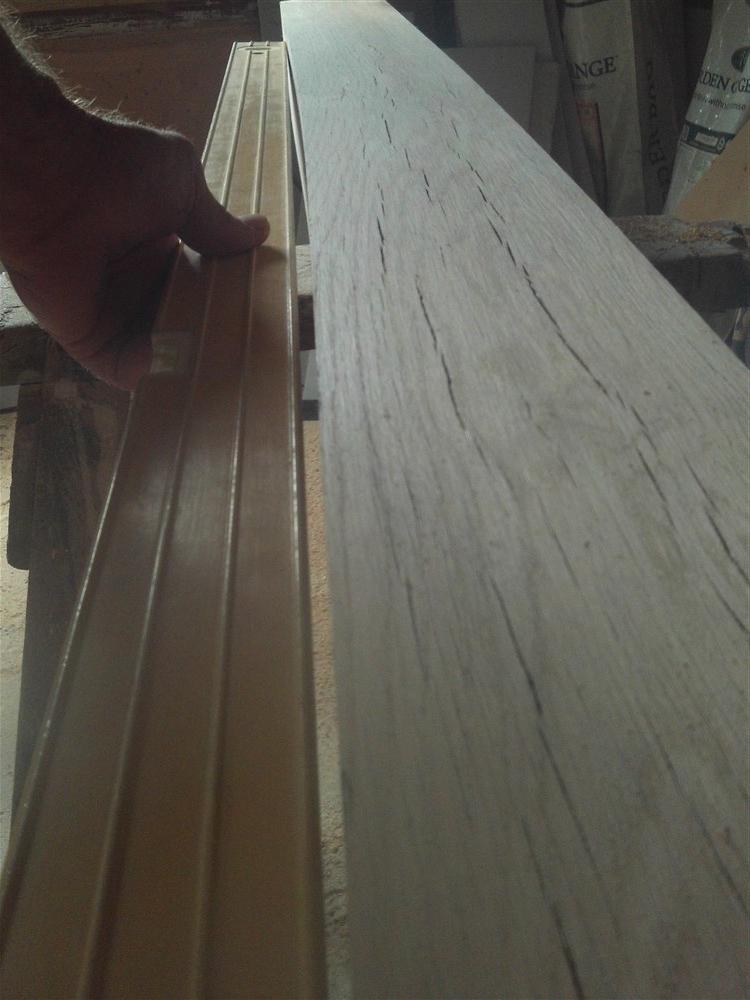
Here are the mortises, and some big notes to myself so I don't make any more cock-ups:
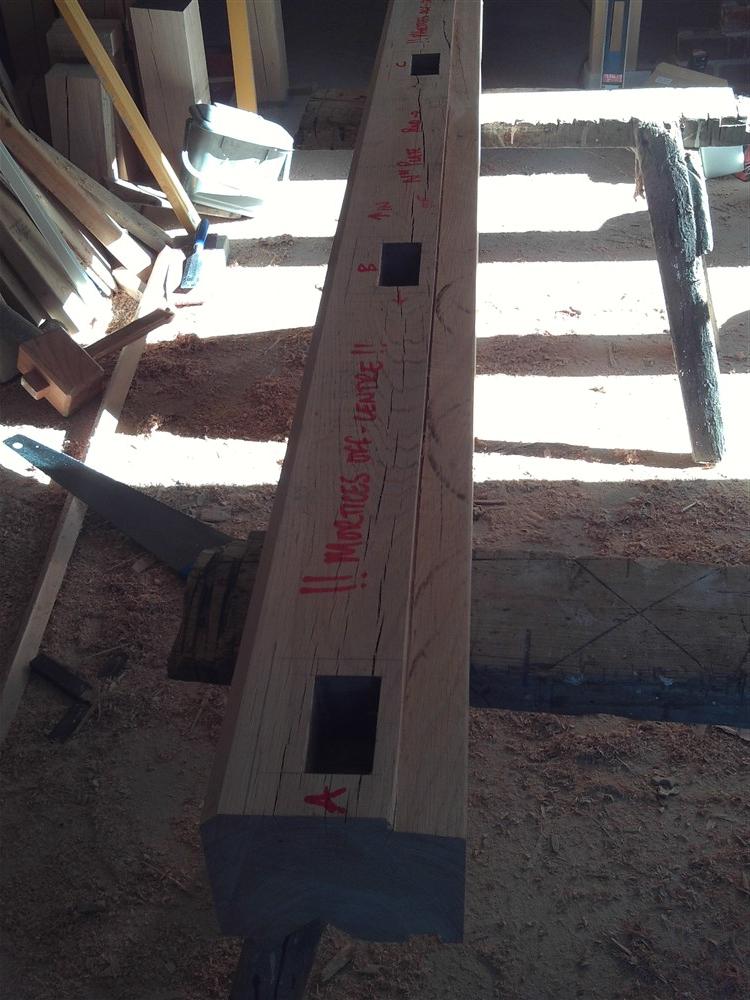
The male side of the mitred bridle joint, with half a mortise:
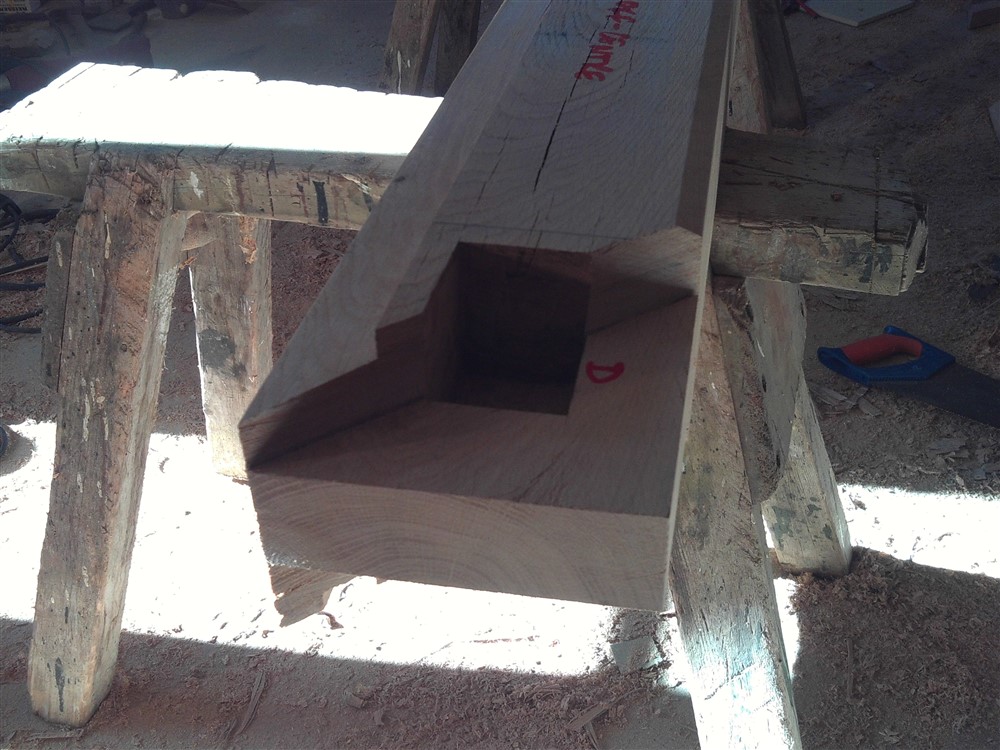
Here's the other one, sitting in situ:
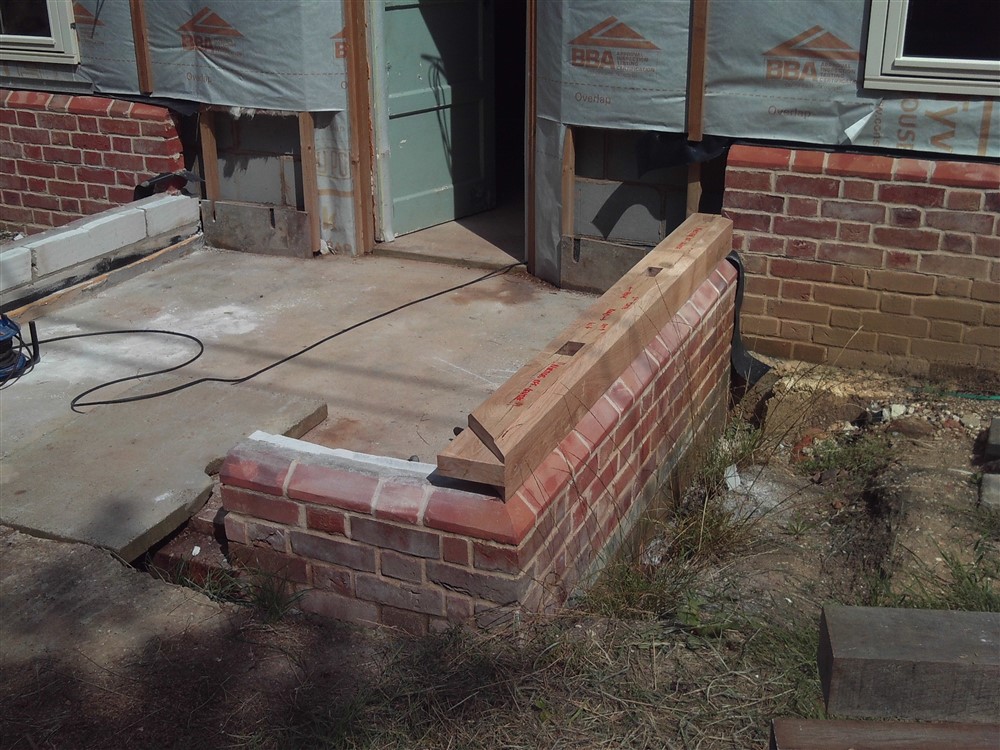
I knew this wasn't going to be easy:
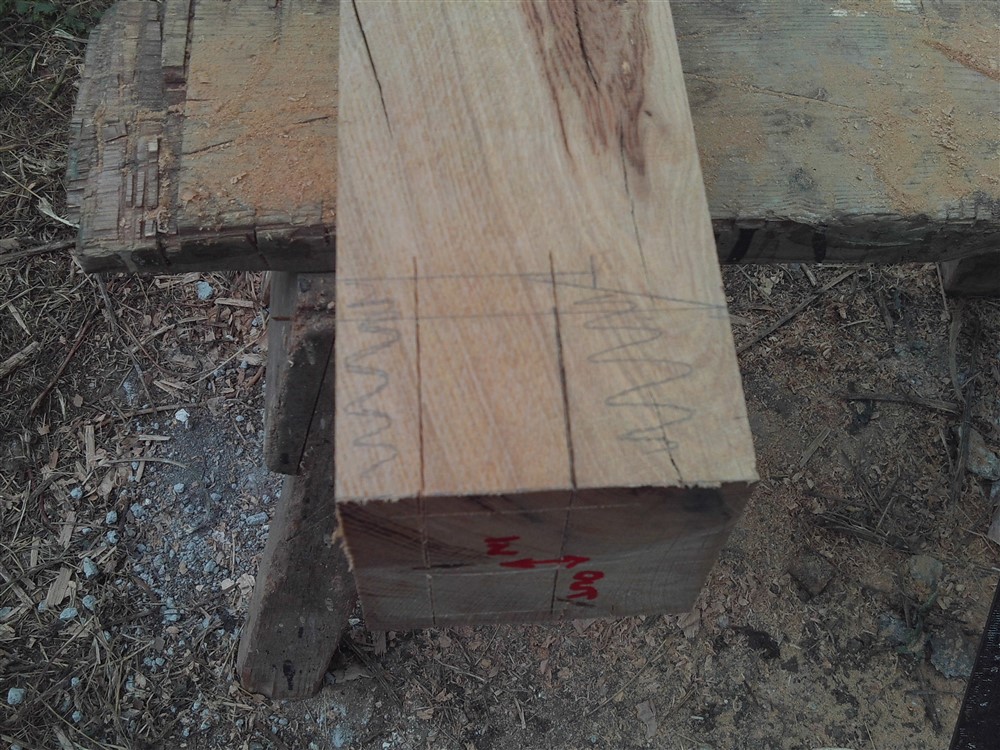
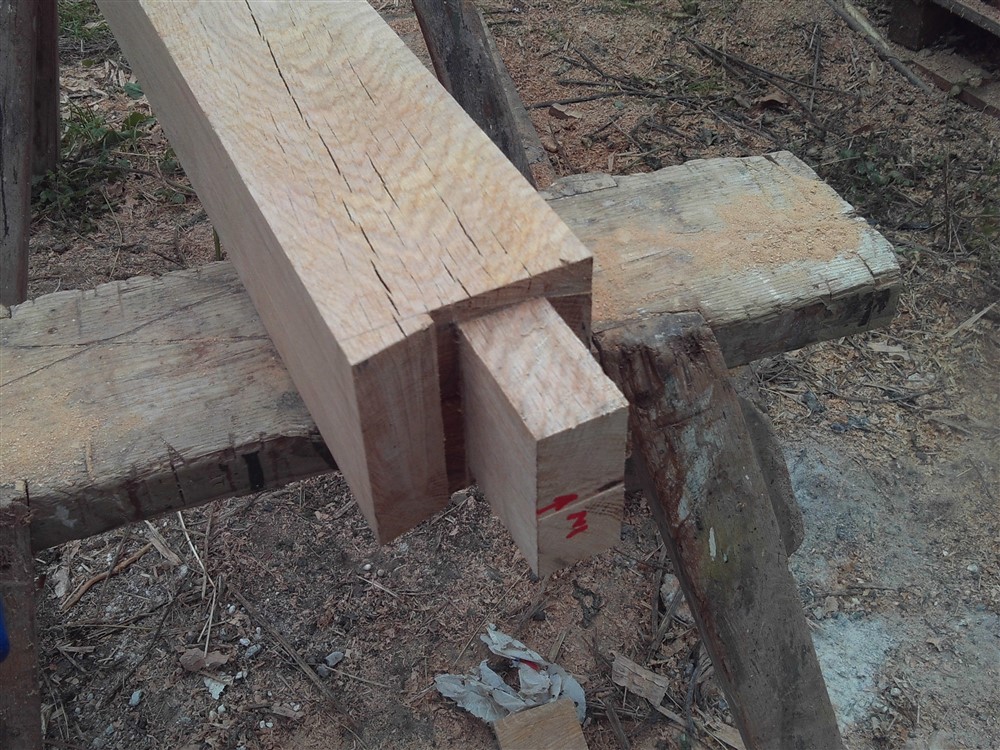
Not perfect, but OK for the first one. I've got 8 to make, so I'll make a template:
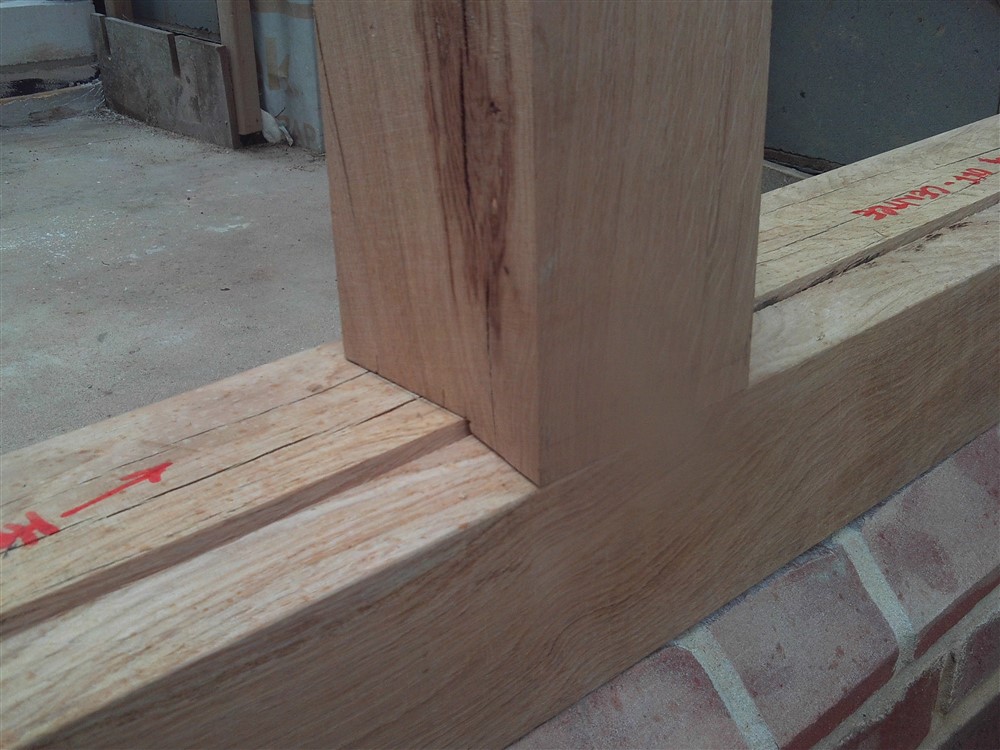