StarGazer
Established Member
After a conversation with Dodge at the recent visit to Axminster I promised to put up some pictures of my first attempt at anything requiring some accuracy in hardwood and also my first attempt at any sort of musical instrument.
As a family we spend a lot of time at weekends during the summer doing historical reenactments and my daughter (already a harpist) wanted something in period to play at shows. Evidence of harps from the 11th century comes mainly from manuscripts, for instance the Winchcombe Psalter and Junius manuscript.
and
My version is based heavily on a similar replica by Simon Chadwick but with my own construction details and increasing the number of strings to two full octaves. As I had never made one before I kept it simple with oak as the main hardwood and no carvings. I know oak is not ideal as a soundboard but I had nothing better to hand at the time. The strings are gut and wrapped around tapered beech dowel tuning pegs. The soundboard is 2mm thick and seems to take the quite substantial tension OK.
Here is my daughter playing the harp
and
If members are interested I have a selection of WIP pictures showing the construction methods.
StarGazer
As a family we spend a lot of time at weekends during the summer doing historical reenactments and my daughter (already a harpist) wanted something in period to play at shows. Evidence of harps from the 11th century comes mainly from manuscripts, for instance the Winchcombe Psalter and Junius manuscript.
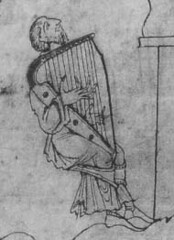
and
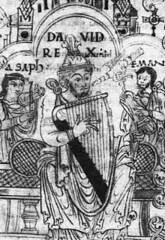
My version is based heavily on a similar replica by Simon Chadwick but with my own construction details and increasing the number of strings to two full octaves. As I had never made one before I kept it simple with oak as the main hardwood and no carvings. I know oak is not ideal as a soundboard but I had nothing better to hand at the time. The strings are gut and wrapped around tapered beech dowel tuning pegs. The soundboard is 2mm thick and seems to take the quite substantial tension OK.
Here is my daughter playing the harp
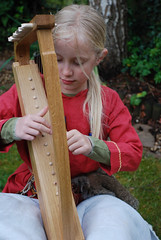
and
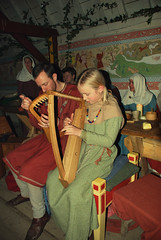
If members are interested I have a selection of WIP pictures showing the construction methods.
StarGazer