RogerS
Established Member
In another thread, I talked about how I went about getting some custom spindle moulder cutters made. But I cocked up. Can you see where ? PM me if you can.
To recap
This is the architrave I wished to make
My working drawing
Tarted up and submitted to Whitehill
Draft cutter schematic from Whitehill
I then suggested that they could extend the cutters (shown shaded) to avoid me having to make a third pass with a rebate cutter
Second draft
They missed one !
Final signed off cutter drawing
Neither they nor I spotted the oversight aka cock-up which didn't become apparent until I'd finished moulding two sets of architrave
Can you spot it ? As I said, PM me if you can.
Not a complete disaster and not that obvious on the finished product and I doubt that anyone would notice it. It's easily fixable for the remaining 12 sets.
To recap
This is the architrave I wished to make
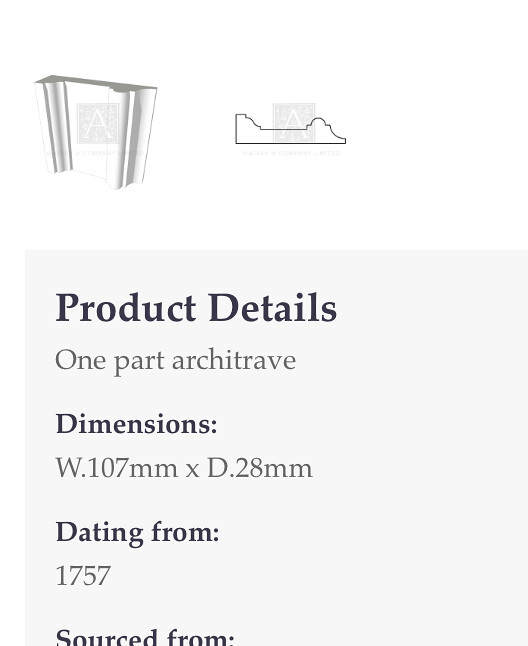
My working drawing
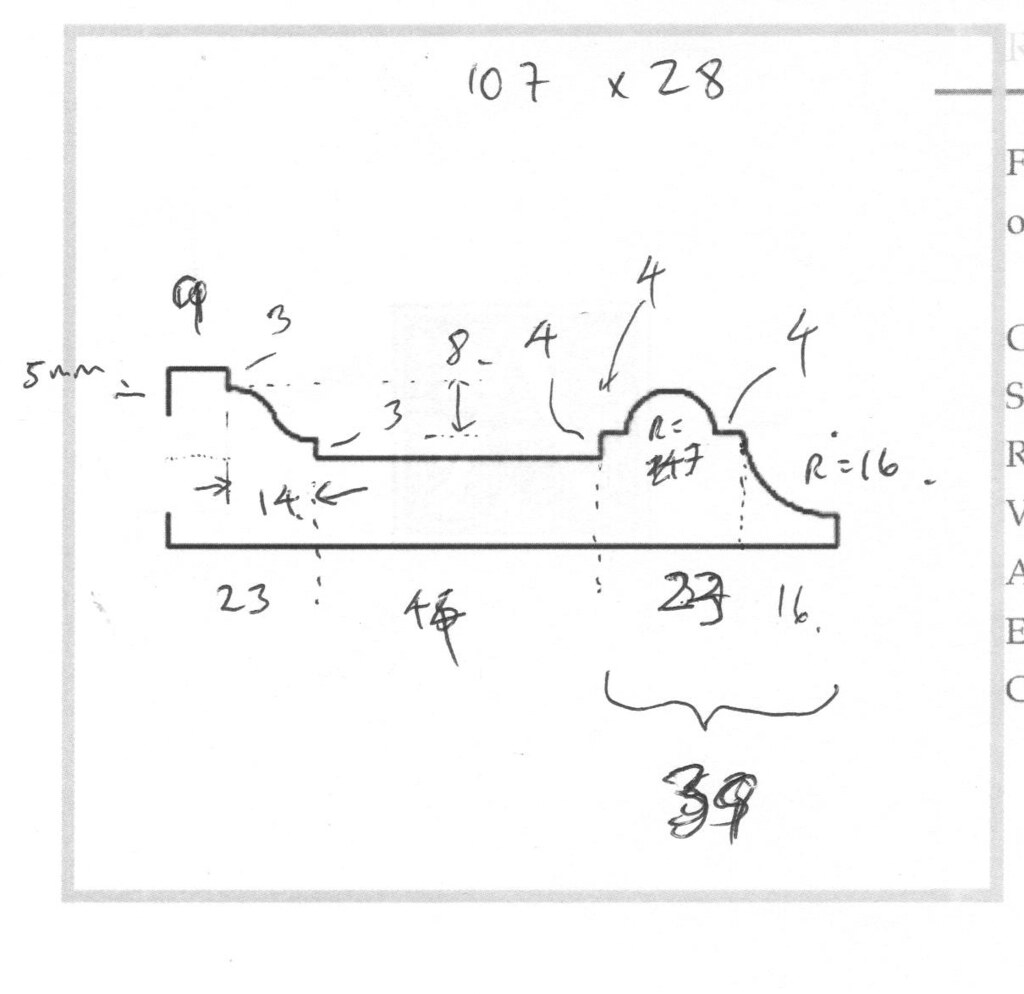
Tarted up and submitted to Whitehill
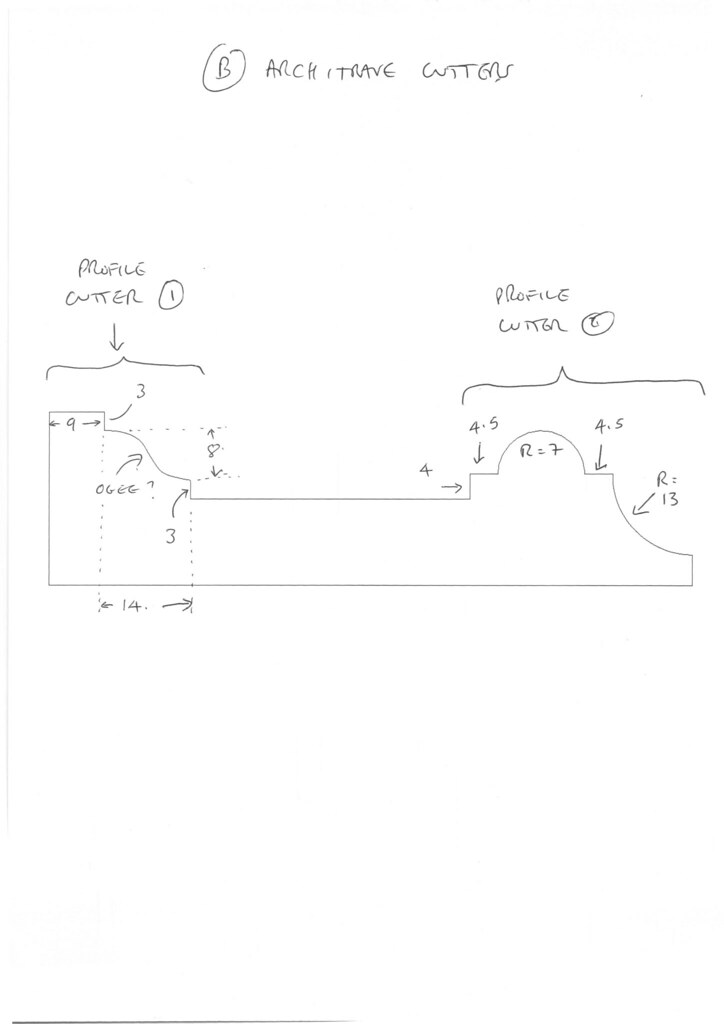
Draft cutter schematic from Whitehill
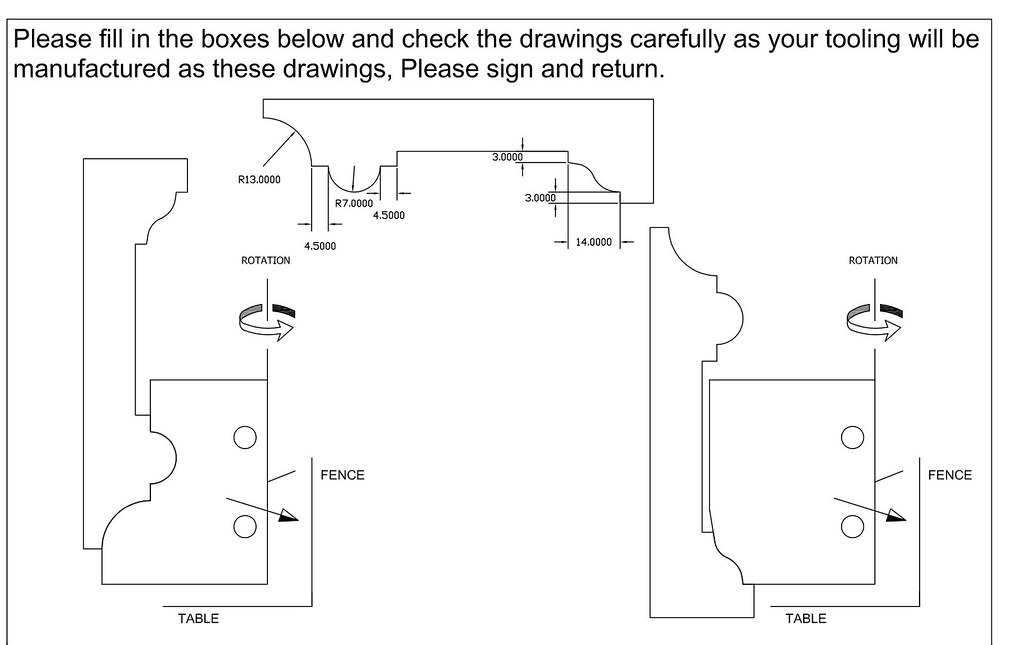
I then suggested that they could extend the cutters (shown shaded) to avoid me having to make a third pass with a rebate cutter
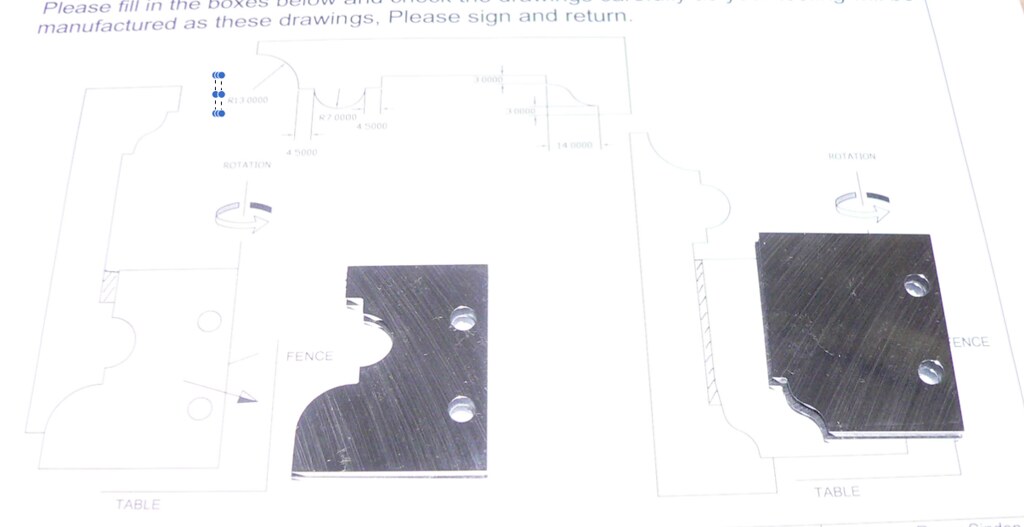
Second draft
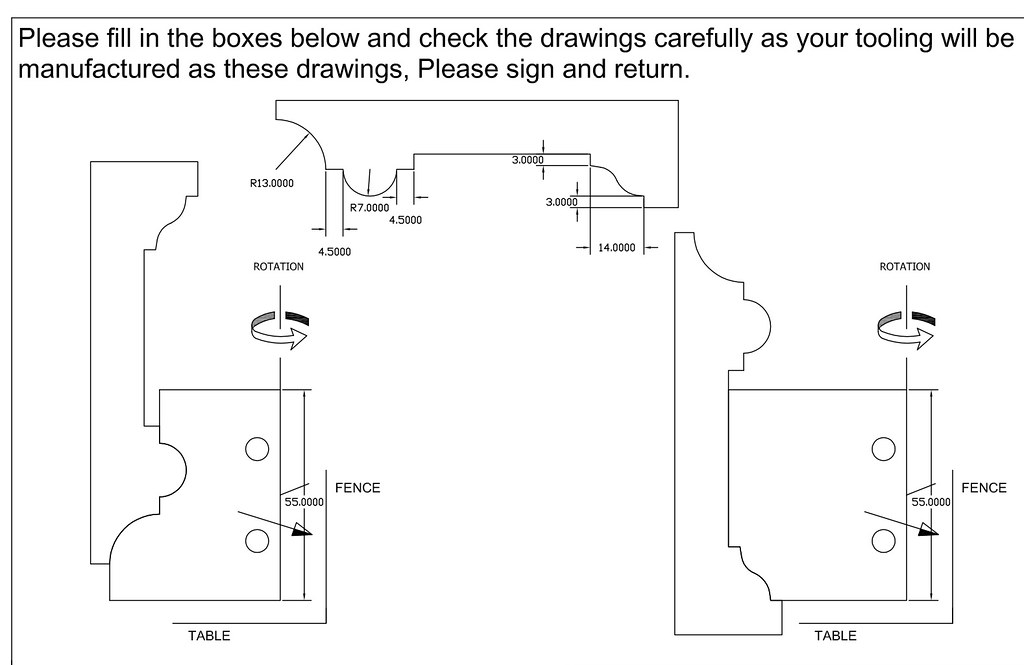
They missed one !
Final signed off cutter drawing
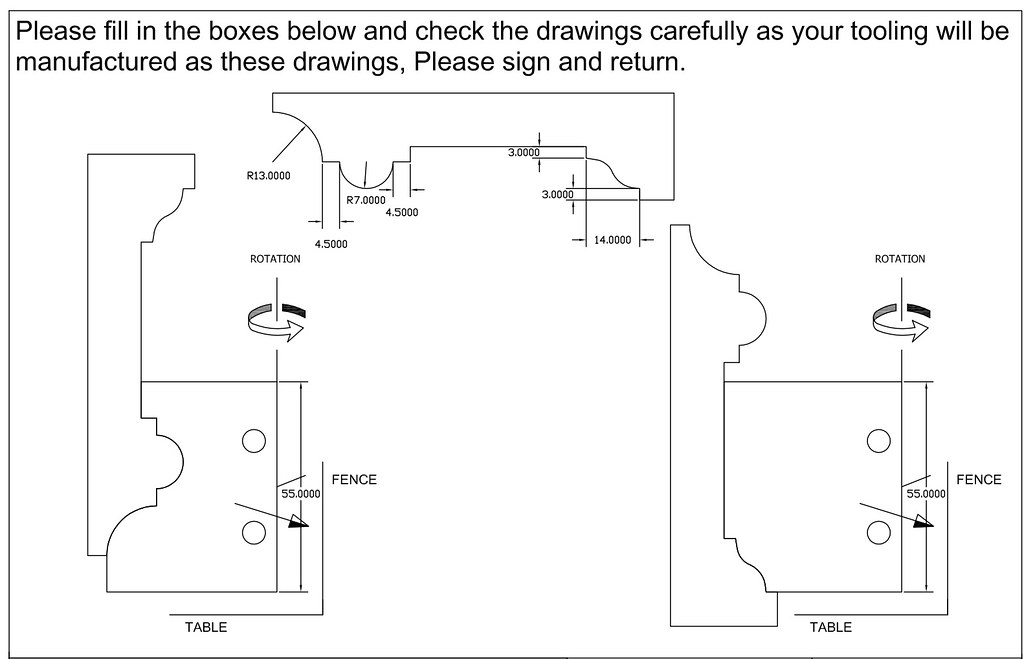
Neither they nor I spotted the oversight aka cock-up which didn't become apparent until I'd finished moulding two sets of architrave
Can you spot it ? As I said, PM me if you can.
Not a complete disaster and not that obvious on the finished product and I doubt that anyone would notice it. It's easily fixable for the remaining 12 sets.