If you liked "Project Noxom" and loved the sequel "Project Dogs of Wonderment" you will adore "Like a tail/inset vice thingamajig,,,,,,,,,,but not fitted into the tail of the bench, because there's a wall in the way". Good working title, no? :lol:
Yes folks the daft taff is back again, good things come in threes they say. Well I'm not so sure these are good things but this is the third WIP of the n0legs volumes of works 8)
Yup! We will once again be creating wonderful and exciting objet d'art, using what we have to hand, tools not designed for the use they've been given and a few far east imports. Danger, sex, drink and drugs, rock 'n' roll and hopefully a bunch of chuckles along the way.
Okay, we'll leave out the sex. I don't have any sheep in the garden and I can't find my wellies :wink:
Let's get to it.
A tail vice is a wonderful thing. Insert wood, wind up tight and go at it with imagination and tools. Simple as that.
NO! Can't fit a tail vice due to shed/bench layout.
So without making myself a load of work (yeah right :roll: ) I decided I needed a variation on the tail vice. I did look at the Veritas inset vice, but that also needs fitting on the end of a bench
So the brief was quite simple, right?
Yes of course it is :shock:
"You see n0legs what you need is a tail vice come inset vice that you can wind up from the top". Don't really have any other choice do I.
There's no sketch up, no blueprints and not even a *** packet diagram. Quick question, how are people managing with these brown labeled plain packets these days? You cant draw on them, despite lack of room you'd need a white pencil. Oh I know, you need one of those silver paint pens like people use on christmas cards.
Slipped there didn't I? Nearly went down the rabbit hole a bit too early in this project. Naughty naughty n0legs.
So what is it we're actually doing? Well dear reader with the use of some gears we're making an inset vice.
One, that with a removable handle, we can let into the bench and tighten and loosen to our hearts content.
With a quick think and a ponder, the idea was for a gear driven vice. Namely a pair of bevel gears to take the drive from vertical to horizontal. So with absolutely no haste spared it was off to the Far East, via the bay of plenty for a little shopping.
And what do you know? Disappointed I was not, there's loads of them. So I settled on these.
12mm bore and 20 teeth. All for £8ish. Well they arrived and fair play they are well made. The bore is accurate, well according to my verynear it's 12mm, concentric and the teeth are well formed and they mesh together very very well
Things are going right straight out of the gates.
A little more shopping/acquiring was carried out and a nice 1/2" BSF high tensile bolt was found, and a few other bits and bobs. This will be the drive shaft, just you wait and see :?
Next thing to source was a suitable screw/thread/leadscrew. A 16 x 4 acme was found online along with a matching nut.
Some Oilite bushes completes the required for the moment.
As I said earlier there's no drawings or sketch so you'll just have to trust me. You do though, don't you? :lol:
First thing is to get the gear to slide on it's drive shaft. Now you maybe asking why I used a 1/2" bolt and not 12mm. Well all the 12mm I could find caused a sloppy fit for the gear. The world wide conspiracy to save materials extends to bolts as well. I could have used a shoulder bolt, these are accurately ground to a given diameter, but all the ones I found had a small socket head, not what I wanted. Here's a shoulder bolt compared to the 1/2"
So to the lathe with some wet and dry in hand, to gently persuade our bolt to loose a few thou' so our gear fits nice and snug.
Didn't take long, cool
This little bit of work also allowed the two Oilite bushes to slide onto the shaft, they wanted just under 12mm to play nicely ](*,)
I know,I missed a pic :roll:
Anyway this is as near as don't matter done.
Another quick question. If you saw Phil Collins drowning, would you save him??
I've been wondering and thinking on this myself,,,,, jury's still out I'm afraid Phil.
Anyway that's all for now. Bits and bobs are coming in fast, so we won't be waiting long for some more.
Much love.
Yes folks the daft taff is back again, good things come in threes they say. Well I'm not so sure these are good things but this is the third WIP of the n0legs volumes of works 8)
Yup! We will once again be creating wonderful and exciting objet d'art, using what we have to hand, tools not designed for the use they've been given and a few far east imports. Danger, sex, drink and drugs, rock 'n' roll and hopefully a bunch of chuckles along the way.
Okay, we'll leave out the sex. I don't have any sheep in the garden and I can't find my wellies :wink:
Let's get to it.
A tail vice is a wonderful thing. Insert wood, wind up tight and go at it with imagination and tools. Simple as that.
NO! Can't fit a tail vice due to shed/bench layout.
So without making myself a load of work (yeah right :roll: ) I decided I needed a variation on the tail vice. I did look at the Veritas inset vice, but that also needs fitting on the end of a bench
So the brief was quite simple, right?
Yes of course it is :shock:
"You see n0legs what you need is a tail vice come inset vice that you can wind up from the top". Don't really have any other choice do I.
There's no sketch up, no blueprints and not even a *** packet diagram. Quick question, how are people managing with these brown labeled plain packets these days? You cant draw on them, despite lack of room you'd need a white pencil. Oh I know, you need one of those silver paint pens like people use on christmas cards.
Slipped there didn't I? Nearly went down the rabbit hole a bit too early in this project. Naughty naughty n0legs.
So what is it we're actually doing? Well dear reader with the use of some gears we're making an inset vice.
One, that with a removable handle, we can let into the bench and tighten and loosen to our hearts content.
With a quick think and a ponder, the idea was for a gear driven vice. Namely a pair of bevel gears to take the drive from vertical to horizontal. So with absolutely no haste spared it was off to the Far East, via the bay of plenty for a little shopping.
And what do you know? Disappointed I was not, there's loads of them. So I settled on these.
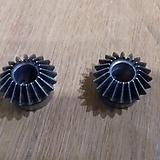
12mm bore and 20 teeth. All for £8ish. Well they arrived and fair play they are well made. The bore is accurate, well according to my verynear it's 12mm, concentric and the teeth are well formed and they mesh together very very well
Things are going right straight out of the gates.
A little more shopping/acquiring was carried out and a nice 1/2" BSF high tensile bolt was found, and a few other bits and bobs. This will be the drive shaft, just you wait and see :?
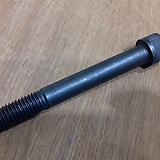
Next thing to source was a suitable screw/thread/leadscrew. A 16 x 4 acme was found online along with a matching nut.
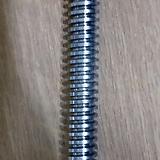
Some Oilite bushes completes the required for the moment.
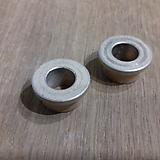
As I said earlier there's no drawings or sketch so you'll just have to trust me. You do though, don't you? :lol:
First thing is to get the gear to slide on it's drive shaft. Now you maybe asking why I used a 1/2" bolt and not 12mm. Well all the 12mm I could find caused a sloppy fit for the gear. The world wide conspiracy to save materials extends to bolts as well. I could have used a shoulder bolt, these are accurately ground to a given diameter, but all the ones I found had a small socket head, not what I wanted. Here's a shoulder bolt compared to the 1/2"
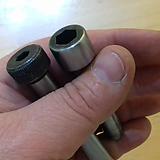
So to the lathe with some wet and dry in hand, to gently persuade our bolt to loose a few thou' so our gear fits nice and snug.
Didn't take long, cool
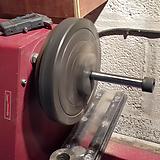
This little bit of work also allowed the two Oilite bushes to slide onto the shaft, they wanted just under 12mm to play nicely ](*,)
I know,I missed a pic :roll:
Anyway this is as near as don't matter done.
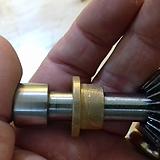
Another quick question. If you saw Phil Collins drowning, would you save him??
I've been wondering and thinking on this myself,,,,, jury's still out I'm afraid Phil.
Anyway that's all for now. Bits and bobs are coming in fast, so we won't be waiting long for some more.
Much love.