OPJ
Established Member
Without counting, I know there aren't very many weeks left until the deadline and I do not honestly fancy my chances of finishing this table in time. I'm in the middle of doing two other jobs for two other people so, we'll see how far this one goes...
As it happens, one of the other pieces I'm making also happens to be a dining table. That extends on a 'drawer leaf' mechanism where as, the table in this thread (which is for my mother :roll
will operate one what's commonly know as a 'butterfly' mechanism (I'm sure you've all seen it - where two leaves unfold and swing out from underneath the centre). Progress on the drawer-leaf table was going very well indeed [there's some brief information in my UKW Blog :wink:], until yesterday when I was looking at preparing boards for the top... To cut a long story short, some of the boards I had weren't fit for purpose and I hadn't bought enough spare to get on with (very unlike me, as anyone from college will agree!
). This morning, I took a trip Interesting Timbers for some more 1in. oak and, while I was there, I decided I would fill my car with the remainder of beech I required.
Actually, this is a photo of my second load. :shock: Believe it or not, I bought enough of enough of both timbers to overload my car. Earlier this year, I pushed my car's suspension to the limits with a load of 3in. beech for my workbench. Miraculously, it just keeps on going but, I decided it would be sensible to get the wood for this dining table in two trips.
Back to my old ways, I spent almost double what I had anticipated! :shock: I usually blame the wastage factor involved with waney-edged timbers but, as this is a regular occurrence, could it actually be me? :? Three cubic feet of oak for one table top (1000mm x 760mm) - I'm not saying any more!! [-(
Some of these 2in. thick boards were phenomenally wide - I ripped the bark from one edge, cut the other parallel and still had 21in.-worth of usable timber!! 8)
I'm still hanging on to this Makita saw, despite owning a larger Hitachi. I find this one more convenient for sheet materials (at least until I can afford a plunge saw!
). It did struggle a bit but, I'd put that down to the 40t blade. Previously, I was set on a 32mm thick top. After studying my SketchUp drawing, I've now decided on 38mm finished thickness. It is a shame no-one stocks 1¾in. sawn timber (they do 2½in. - and who the heck buys that, anyway?! :roll:
)
My approach to working waney-edged wood this time around is a little different... Normally, I'd remove the bark from both edges. This time, I intend to straight only one edge [yes, I'm aware of what I wrote earlier!! :wink:]. Once it's had some time to settle in the 'shop (a week or so), I'll reference off this edge to get my components out over-sized before sticking them indoors for a bit.
Speaking of bark and wastage, this is what I'll be throwing away initially. I'll normally give this away to someone else as firewood - I do wonder whether anyone would actually pay for a 'good quality hardwood' though...? :-k :wink:
On to the design, at last...
My brief calls for a table roughly the same size as our existing pine piece, which will initially seat four people, extending to seat six on occasion. Mum did talk about an eight-seater at one point but I showed her (using the power of Google SketchUp!) how that isn't really feesable in our small kitchen. I'm aware that each seater (and seat, inside the frame) needs at least 500mm of arm room for comfort. So, as you can probably see in these images; I'm not far off but, there's still a little bit of playing around with dimensions to be done.
It's a bit 'touch-and-go', in the sense that I don't want the outer corners of the legs to be too close to to perimeter of the table top, for aesthetics, more-so than anything else.
In order to help such matters (I hope!), in my current leg design (see below), I will add a considerate radius to the outer arris, which I feel compliments the curve of the top (...speaking of which, that curve isn't yet concrete). I bought some 3x3in. pine a few weeks ago and will make a couple of mock-up legs soon.
Regardless of whether or not I actually finish, I would like to have this underframe construction finished by the end of October. After which, the top should be fairly straight forward. I'm fully aware that beech isn't the most stable of timbers, which is why I'll be adding a central runner to this construction, which should help to keep the top flat.
Thinking back to the sawn timber, which currently rests at approximately 54mm thick, that's an awful lot of waste to achieve a 38mm thickness. I don't fancy mountains of wood shavings and several trips to the Recycling Centre so, I may have to cut and store nineteen beech veneers, 100mm wide! No, I don't like to waste wood, which is partly why I often end up taking home the boards in a stack which several other people have already turned over...! :roll:
There's still a little more ripping to be done tomorrow, as the heavens halted proceedings for today. :x I've hand some 3in. beech on stand-by since my 'bench build during the summer. This length was the only one not to have split severely. Damien's [Ironballs] thread appears to have sprung his competition entry in to life. While I appreciate that I have minimal progress to show so far, I'm hoping this entry will have a similar effect on my project. :wink:
See you in twenty-four hours!
As it happens, one of the other pieces I'm making also happens to be a dining table. That extends on a 'drawer leaf' mechanism where as, the table in this thread (which is for my mother :roll
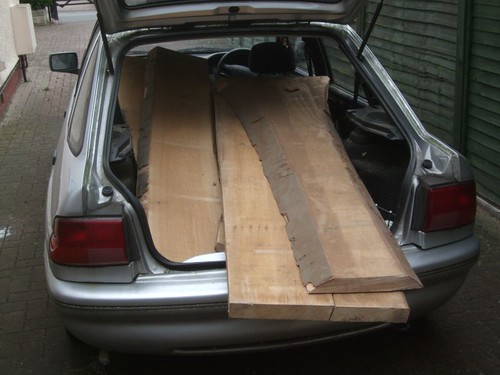
Actually, this is a photo of my second load. :shock: Believe it or not, I bought enough of enough of both timbers to overload my car. Earlier this year, I pushed my car's suspension to the limits with a load of 3in. beech for my workbench. Miraculously, it just keeps on going but, I decided it would be sensible to get the wood for this dining table in two trips.
Back to my old ways, I spent almost double what I had anticipated! :shock: I usually blame the wastage factor involved with waney-edged timbers but, as this is a regular occurrence, could it actually be me? :? Three cubic feet of oak for one table top (1000mm x 760mm) - I'm not saying any more!! [-(
Some of these 2in. thick boards were phenomenally wide - I ripped the bark from one edge, cut the other parallel and still had 21in.-worth of usable timber!! 8)

I'm still hanging on to this Makita saw, despite owning a larger Hitachi. I find this one more convenient for sheet materials (at least until I can afford a plunge saw!
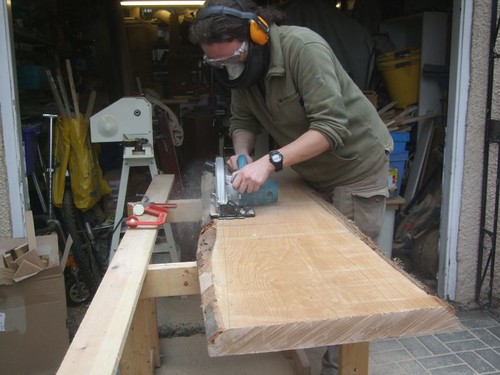
My approach to working waney-edged wood this time around is a little different... Normally, I'd remove the bark from both edges. This time, I intend to straight only one edge [yes, I'm aware of what I wrote earlier!! :wink:]. Once it's had some time to settle in the 'shop (a week or so), I'll reference off this edge to get my components out over-sized before sticking them indoors for a bit.
Speaking of bark and wastage, this is what I'll be throwing away initially. I'll normally give this away to someone else as firewood - I do wonder whether anyone would actually pay for a 'good quality hardwood' though...? :-k :wink:
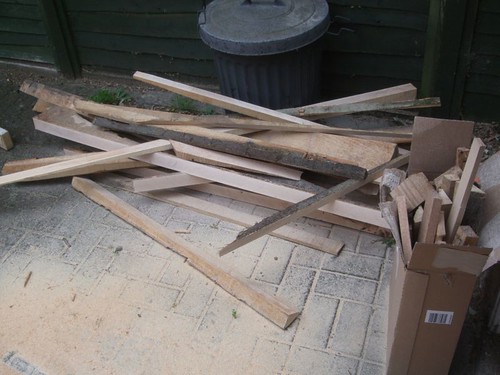
On to the design, at last...
My brief calls for a table roughly the same size as our existing pine piece, which will initially seat four people, extending to seat six on occasion. Mum did talk about an eight-seater at one point but I showed her (using the power of Google SketchUp!) how that isn't really feesable in our small kitchen. I'm aware that each seater (and seat, inside the frame) needs at least 500mm of arm room for comfort. So, as you can probably see in these images; I'm not far off but, there's still a little bit of playing around with dimensions to be done.
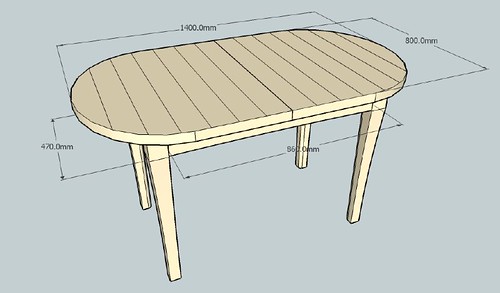
It's a bit 'touch-and-go', in the sense that I don't want the outer corners of the legs to be too close to to perimeter of the table top, for aesthetics, more-so than anything else.
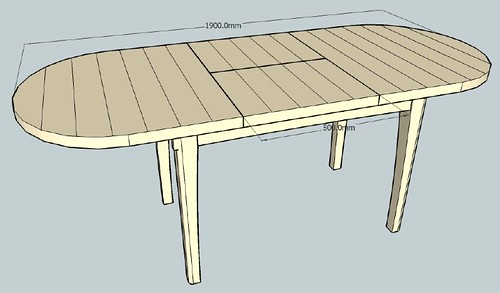
In order to help such matters (I hope!), in my current leg design (see below), I will add a considerate radius to the outer arris, which I feel compliments the curve of the top (...speaking of which, that curve isn't yet concrete). I bought some 3x3in. pine a few weeks ago and will make a couple of mock-up legs soon.
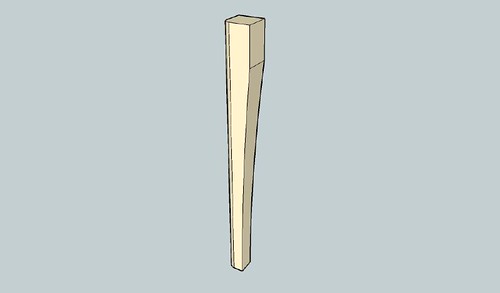
Regardless of whether or not I actually finish, I would like to have this underframe construction finished by the end of October. After which, the top should be fairly straight forward. I'm fully aware that beech isn't the most stable of timbers, which is why I'll be adding a central runner to this construction, which should help to keep the top flat.
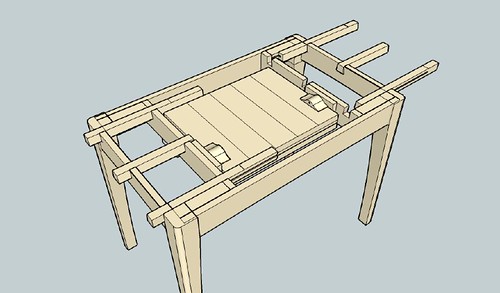
Thinking back to the sawn timber, which currently rests at approximately 54mm thick, that's an awful lot of waste to achieve a 38mm thickness. I don't fancy mountains of wood shavings and several trips to the Recycling Centre so, I may have to cut and store nineteen beech veneers, 100mm wide! No, I don't like to waste wood, which is partly why I often end up taking home the boards in a stack which several other people have already turned over...! :roll:
There's still a little more ripping to be done tomorrow, as the heavens halted proceedings for today. :x I've hand some 3in. beech on stand-by since my 'bench build during the summer. This length was the only one not to have split severely. Damien's [Ironballs] thread appears to have sprung his competition entry in to life. While I appreciate that I have minimal progress to show so far, I'm hoping this entry will have a similar effect on my project. :wink:
See you in twenty-four hours!