Dibs-h
Established Member
Update: Borrowed some aluminium ladders and fitted the roof hooks and then got going. Rolled out the ridge roll that comes with the Marley dry ridge kit, with a nail every 1m or so into the pieces of timber that were fitted onto the ridge.
With only one roof ladder - it was a right faff. Start at one end - roll it out, come down, move ladder, go back up, roll it some more, come down... you get the picture. Then the same shenanigans for nailing it, and sticking it down. Then onto getting the ridges up the. All I can say is thank God for Snickers work pants with knee pads!!
As you can appreciate WIP piccies are a bit hard work up a roof ladder. Sorry. Anyway here's one with all the ridges fitted,
And here's a gratuitous shot in better light,
That took a fair part of Sat. On Sunday my attention turned to the rear wall and where water had penetrated from the other side horizontally on and under the DPC. Cut the overhanging DPC back and then cut the mortar out (and the DPC) to a depth of around 20mm and more or less the full height of the mortar bed.
I'd got some Feb Waterstop
http://www.feb.uk.com/products/waterproofing/waterplug
and as per instructions, filled this cutout leaving.
I'd also got some of their FebTank Super,
http://www.feb.uk.com/products/waterpro ... tank-super
(a cementious slurry type product for negative and positive water pressure). In all honesty, since the guttering has been on the back - there has been no more seepage. But before fitting the DPM - I'd just like that extra bit of peace of mind.
Unfortunately on Sunday the temp dropped to around 5, and the datasheet for this product stated that it should only be applied in temps exceeding 5 degrees. So just had a day off! So hopefully will be giving it 2 coats of this stuff this week, some Synthaprufe and then down with the DPM, bearers and then the flooring and stud walls.
Found a supplier of 4" kingspan type stuff for a ridiculously low price, so will be grabbing a mate with a very large van and getting as many as we can can get into it. Will report back on that if anyone else is interested.
I was going to lay 2" Kingspan down - 3"x2" bearers down sideways, infill with 2" Kingspan and then 1" ply flooring. Now I'm just thinking that's a faff - and I'm inclined to use 4"x2" joists sat directly on the DPM and infill with 4" kingspan, with the 1" ply screwed on top. Any suggestions?
With only one roof ladder - it was a right faff. Start at one end - roll it out, come down, move ladder, go back up, roll it some more, come down... you get the picture. Then the same shenanigans for nailing it, and sticking it down. Then onto getting the ridges up the. All I can say is thank God for Snickers work pants with knee pads!!
As you can appreciate WIP piccies are a bit hard work up a roof ladder. Sorry. Anyway here's one with all the ridges fitted,
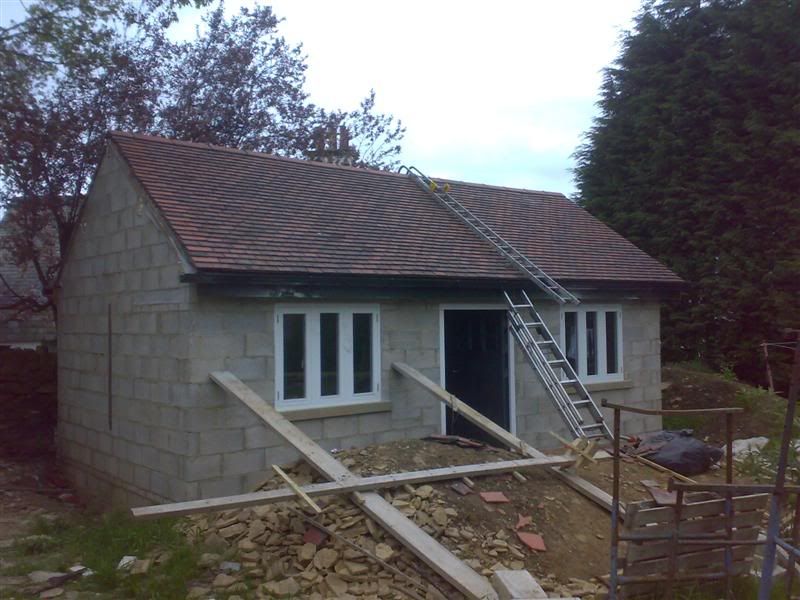
And here's a gratuitous shot in better light,
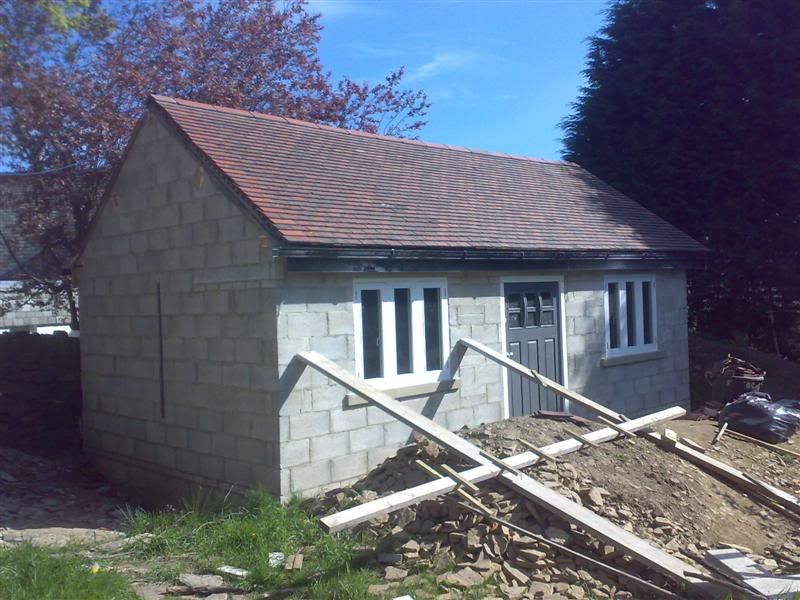
That took a fair part of Sat. On Sunday my attention turned to the rear wall and where water had penetrated from the other side horizontally on and under the DPC. Cut the overhanging DPC back and then cut the mortar out (and the DPC) to a depth of around 20mm and more or less the full height of the mortar bed.
I'd got some Feb Waterstop
http://www.feb.uk.com/products/waterproofing/waterplug
and as per instructions, filled this cutout leaving.

I'd also got some of their FebTank Super,
http://www.feb.uk.com/products/waterpro ... tank-super
(a cementious slurry type product for negative and positive water pressure). In all honesty, since the guttering has been on the back - there has been no more seepage. But before fitting the DPM - I'd just like that extra bit of peace of mind.
Unfortunately on Sunday the temp dropped to around 5, and the datasheet for this product stated that it should only be applied in temps exceeding 5 degrees. So just had a day off! So hopefully will be giving it 2 coats of this stuff this week, some Synthaprufe and then down with the DPM, bearers and then the flooring and stud walls.
Found a supplier of 4" kingspan type stuff for a ridiculously low price, so will be grabbing a mate with a very large van and getting as many as we can can get into it. Will report back on that if anyone else is interested.
I was going to lay 2" Kingspan down - 3"x2" bearers down sideways, infill with 2" Kingspan and then 1" ply flooring. Now I'm just thinking that's a faff - and I'm inclined to use 4"x2" joists sat directly on the DPM and infill with 4" kingspan, with the 1" ply screwed on top. Any suggestions?