TL;DR:
Has anyone got experience of extending one of the "Compton" type sectional concrete garages?
(i.e this type, although this isn't mine, just an example I found online)
Detailed explanatory aside:
I've recently acquired a house with a good sized (3.5m × 7.4m) concrete garage, with the plan of setting up my metal-bashing tools (Mill, Little Lathe, Big Lathe, Surface Plate, Drill, Grinders, Welder, Pipe Threader etc) in there.
However whilst i was preparing to insulate and board it, I realised that it also needed a new garage door to give me a cat in hell's chance of making it dry and warm enough to avoid serious rust issues once I clean the packing grease off my stored tools.
I used to make doors for a living once upon a time, so after a bit of research into bifold door mechanisms I drew some plans and bought 0.3m³ of unsorted redwood with the intention of making a bifold garage door, However upon taking delivery of the redwood I realised that all the rebates and tongue and groove profiles I had planned to plane by hand, mounted up to an awful lot of timber to remove...
To recuperate from this terrible realisation, I availed myself of a number of pear-derived refreshing beverages (actual Perry, not the alcopop in all but name stuff) which unaccountably turn out to be strongly alcoholic... With my judgement slightly impaired, I ended up idly browsing a well known internet auction site, and subsequently purchasing a nice little spindle moulder for a really very good price (so good in fact, that the spindle moulder and the wood are still less than buying the doors commercially).
There's not the space for seperate woodworking and metalworking workshops in the garage, and after spending nearly 2 years doing a nut and bolt rebuild of the mill (including a whole new spindle), I'm not willing to have wood dust in the same room as the machine tools. So, after making the doors, and before i finish setting up the workshop it would have to go, which seems silly as I'd never get another for that kind of price; and seen as I also have my little ELU Planer-Thicknesser on long term loan to someone whilst they refurbish a big Wadkin planer thicknesser, and a Radial Arm Saw which has found a temporary home (and occasional use) with another friend, it would be really nice to be able to get those back, and set up a decent woodworking shop too...
As it happens, there's an additional 4 to 4.5m (ish) of space to the rear of the garage which is basically dead space (and is full of dead and dying Leylandii) that could become garage, and an additional 2.5 × 2m area which is currently infested with bamboo and also wouldn't be missed; if I was to add these additional areas I'd have plenty of room for dedicated wood and metal workshops which were internally divided, could be absolutely sure about the slab-thickness and ground-loading capacity of the back section when I bring the big lathe in, and would have a little annex to do welding and grinding in, to protect the machines from abrasive dust and keep the sparks far from the woodworking area.
If I'm doing this, I'd be keen to save a bit of money on the paneling by only purchasing the cheaper half-height "window" panels, then re-using existing full-height panels I took out. Moreover, if I bulk buy the timber again, the frames will work out cheaper (excluding my labour) than the additional cost for full height panels, which would help to offset the cost of buying the sealed DG-units to go into said windows (which again if I'm ordering 8-10 in a basic spec, shouldn't be exorbitant).
Even better this is all well within my permitted development rights, as the land parcel associated with the house is substantial (even if a lot of it is not strictly my garden, but shared with my neighbours under an easement).
However there are three problems:
Edit:
Yes, I know it sounds kind of insane to commit to this style of building, but it is substantially cheaper and more convenient than rebuilding in brick; and the money saved there would help finance getting a 3-phase connection (conveniently, I have 3-phase to the meter, so forking that to add a connection on a separate meter in the workshop is actually pretty "cheap", at least in terms of 3-phase connection costs).
Has anyone got experience of extending one of the "Compton" type sectional concrete garages?
(i.e this type, although this isn't mine, just an example I found online)
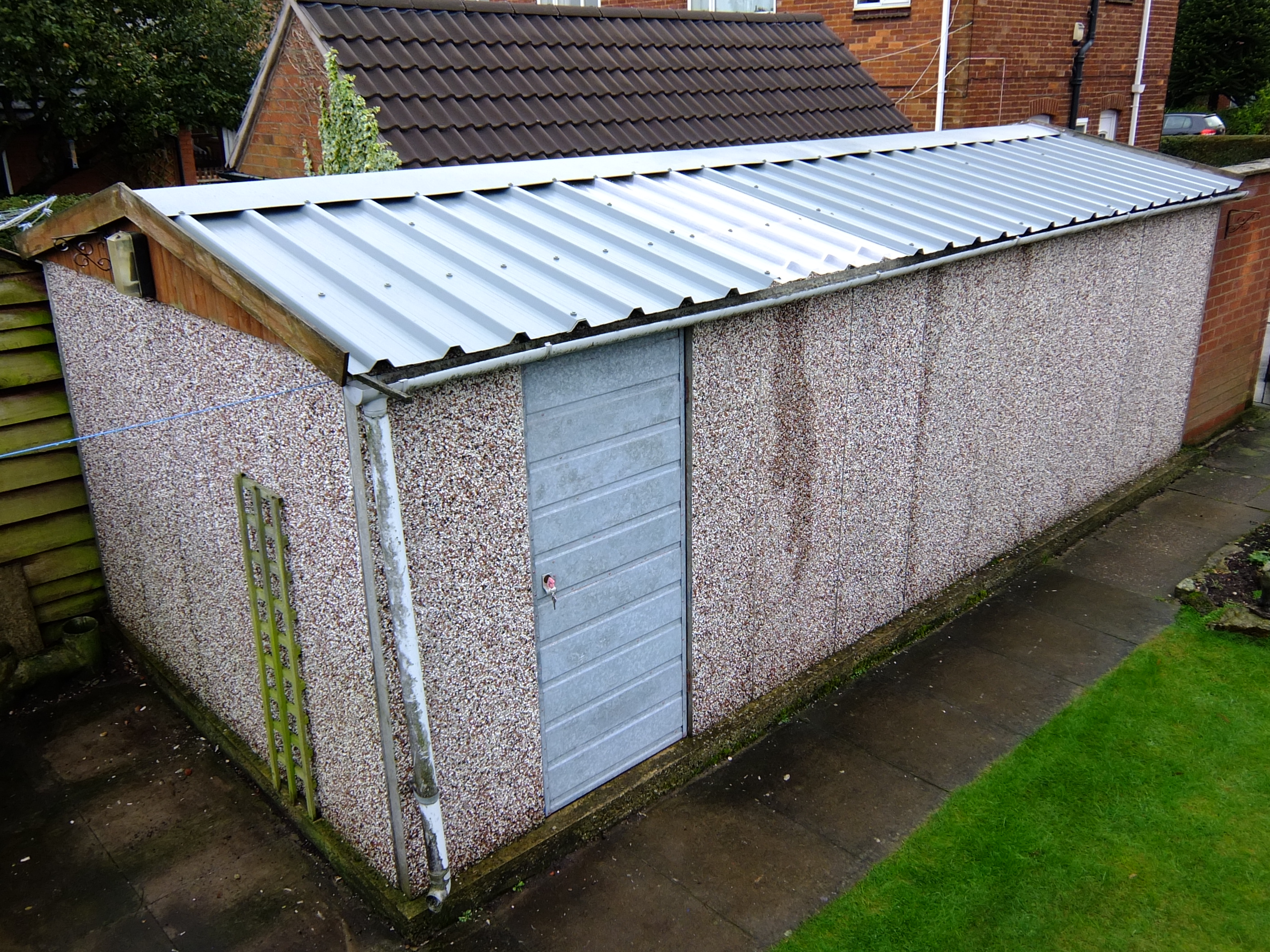
- Are they capable of meeting the building regs if they go over the "magic" 30m² exemption?
- Is it possible to make an exterior internal corner with the panels (see option 2 on diagram below)?
- I'm Quite concerned about the structural stability of the garage when taking out the eaves and rear panels out in order to add length; should I be?
- I'd like to fit "window" half panels to replace existing full height ones, and i'm very concerned about the structural stability of the garage whilst I'm doing this; again should I be?
Detailed explanatory aside:
I've recently acquired a house with a good sized (3.5m × 7.4m) concrete garage, with the plan of setting up my metal-bashing tools (Mill, Little Lathe, Big Lathe, Surface Plate, Drill, Grinders, Welder, Pipe Threader etc) in there.
However whilst i was preparing to insulate and board it, I realised that it also needed a new garage door to give me a cat in hell's chance of making it dry and warm enough to avoid serious rust issues once I clean the packing grease off my stored tools.
I used to make doors for a living once upon a time, so after a bit of research into bifold door mechanisms I drew some plans and bought 0.3m³ of unsorted redwood with the intention of making a bifold garage door, However upon taking delivery of the redwood I realised that all the rebates and tongue and groove profiles I had planned to plane by hand, mounted up to an awful lot of timber to remove...
To recuperate from this terrible realisation, I availed myself of a number of pear-derived refreshing beverages (actual Perry, not the alcopop in all but name stuff) which unaccountably turn out to be strongly alcoholic... With my judgement slightly impaired, I ended up idly browsing a well known internet auction site, and subsequently purchasing a nice little spindle moulder for a really very good price (so good in fact, that the spindle moulder and the wood are still less than buying the doors commercially).
There's not the space for seperate woodworking and metalworking workshops in the garage, and after spending nearly 2 years doing a nut and bolt rebuild of the mill (including a whole new spindle), I'm not willing to have wood dust in the same room as the machine tools. So, after making the doors, and before i finish setting up the workshop it would have to go, which seems silly as I'd never get another for that kind of price; and seen as I also have my little ELU Planer-Thicknesser on long term loan to someone whilst they refurbish a big Wadkin planer thicknesser, and a Radial Arm Saw which has found a temporary home (and occasional use) with another friend, it would be really nice to be able to get those back, and set up a decent woodworking shop too...
As it happens, there's an additional 4 to 4.5m (ish) of space to the rear of the garage which is basically dead space (and is full of dead and dying Leylandii) that could become garage, and an additional 2.5 × 2m area which is currently infested with bamboo and also wouldn't be missed; if I was to add these additional areas I'd have plenty of room for dedicated wood and metal workshops which were internally divided, could be absolutely sure about the slab-thickness and ground-loading capacity of the back section when I bring the big lathe in, and would have a little annex to do welding and grinding in, to protect the machines from abrasive dust and keep the sparks far from the woodworking area.
If I'm doing this, I'd be keen to save a bit of money on the paneling by only purchasing the cheaper half-height "window" panels, then re-using existing full-height panels I took out. Moreover, if I bulk buy the timber again, the frames will work out cheaper (excluding my labour) than the additional cost for full height panels, which would help to offset the cost of buying the sealed DG-units to go into said windows (which again if I'm ordering 8-10 in a basic spec, shouldn't be exorbitant).

Even better this is all well within my permitted development rights, as the land parcel associated with the house is substantial (even if a lot of it is not strictly my garden, but shared with my neighbours under an easement).
However there are three problems:
- Over 30m² of floor-space (I already have 26m² in the garage, and another 3.5m² of other outbuildings, so I can't avoid going over) I would no longer be exempt from building control, and I'm:
- Not at all sure that a sectional garage can meet the building regs.
- Really struggling to find out which parts would apply, so I can research to understand the answer to question 1
- If the area of the other outbuildings is considered, I will start to run quite close to the 50m² limit at which the energy efficiency requirements of the building regs will also kick in.
- The way these compton garage shells are constructed seems a bit sketchy at best, and I'm not clear if it will respond well to me:
- Removing the back wall and eaves in order to add additional length
- Removing full height panels mid-way along existing walls, to replace them with half-height panels (which are cheaper) to fit additional windows, which is a prefered option to add more natural light.
- I'm not sure you can have exterior internal corners using the compton-type panels, which might rule out my most prefered option (2, which is L-shaped to give sufficient separation from a mature tree I don't want to fell).
Edit:
Yes, I know it sounds kind of insane to commit to this style of building, but it is substantially cheaper and more convenient than rebuilding in brick; and the money saved there would help finance getting a 3-phase connection (conveniently, I have 3-phase to the meter, so forking that to add a connection on a separate meter in the workshop is actually pretty "cheap", at least in terms of 3-phase connection costs).
Last edited: