Aled Dafis
Established Member
I've bought the Leigh D4R D/T jig home from school over the holidays so that I could get used to using it before the mad rush that next term brings with it.
My first impressions of the jig are very impressive indeed, it's very well made and fairly straigtforward to set up. I have come up against one problem however, when cutting my first joint, I found that one side of the dovetails consistently had a gap of about 0.5mm on the left hand side of the pin, across the board.
The gap doesn't show up too well in this pic, but it's definately there.
So I went about checking the guide bush concentricity and set up. The guide bush seemed ok, so I tried another joint just to see whether it was down to user error. Much to my surprise, joint B also showed the same error, so I'm either consistently out, or it's the jig.
The gaps are a bit clearer here. But on the right this time as the joint was photographed the other way round.
And in close up...
So any guidance would be most appreciated.
Cheers
Aled
My first impressions of the jig are very impressive indeed, it's very well made and fairly straigtforward to set up. I have come up against one problem however, when cutting my first joint, I found that one side of the dovetails consistently had a gap of about 0.5mm on the left hand side of the pin, across the board.
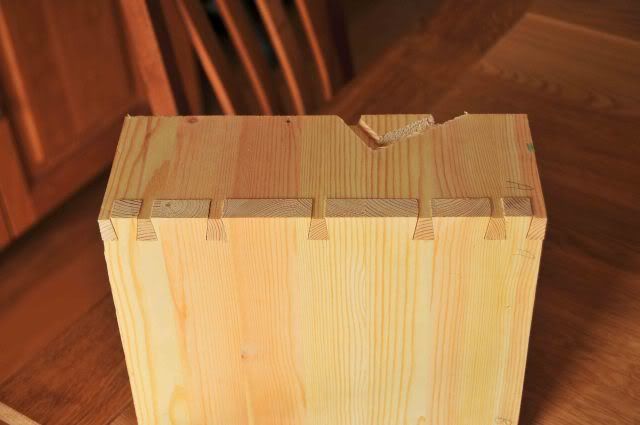
The gap doesn't show up too well in this pic, but it's definately there.
So I went about checking the guide bush concentricity and set up. The guide bush seemed ok, so I tried another joint just to see whether it was down to user error. Much to my surprise, joint B also showed the same error, so I'm either consistently out, or it's the jig.
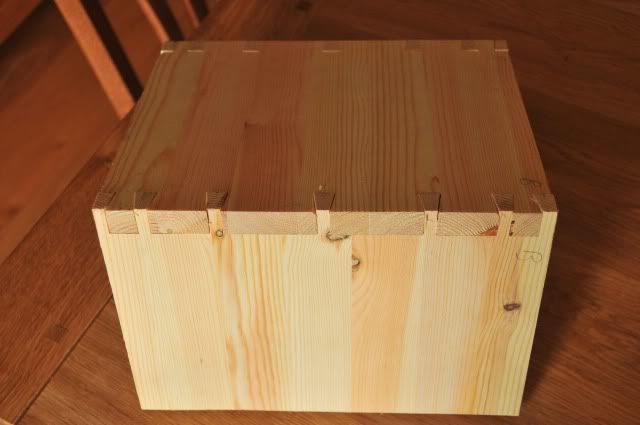
The gaps are a bit clearer here. But on the right this time as the joint was photographed the other way round.
And in close up...
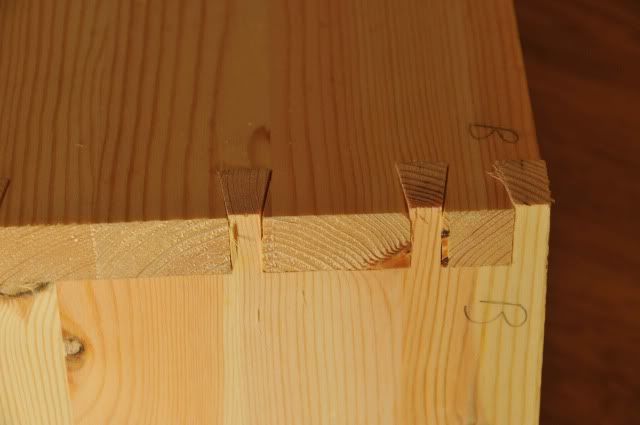
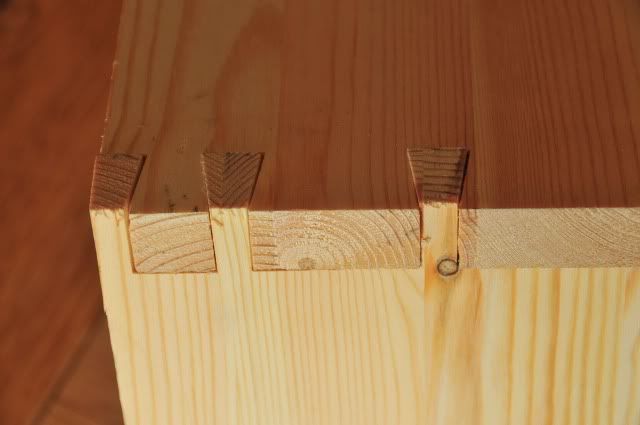
So any guidance would be most appreciated.
Cheers
Aled