SPinonit
Established Member
Please be gentle - this is my first ever attempt at a proper bit of furniture (if you call storage units furniture..?). I made it for my youngest son's bedroom, which badly needed some good strong (he's a 6yr old bruiser! :roll: ) storage that actually fits his toy and books etc.
The tat you buy from the warehouses either seems to cost the earth, or is made from paper and just not worth the money. They are also fixed sizes, so making my own was a breath of fresh air and a bit of a baptism at the same time.
I got the desgn from a free template somwehere on the interweb, but I adapted the sizes to better suit my son's room and toys. I also added a couple of bits to strengthen it from the original design, but in doing so I appear to have complicated it slightly above my rather amateurish woodworking skill levels. Hopefully, what I've learnt from making this will benefit the next project.
Anyway, it got a thumbs up from the customer so here's a few pics from start to finish:
This is a layout of all the base pieces of the unit, which has kickboards set back from the front to allow feet under. I used biscuits as that was supposed to be the easiest way to do the joints, however, as I have a pretty cheap jointer and my jointing experience was low-to-nil, it was perhaps not as simple as it should have been. Leesons learned and next time should be better.
This shows the base built up and primed. on the corner at the bottom of the photo, you can just about see the cut-out (rebate?) that I made so the unit sits over the carpet gripper rods, which allows it to be square with the wall. Furniture always seems to have be be packed at the front with cardboard just to make it stand upright.
Now the base is painted:
You can see the biscuits that I use to [try] to align the three vertical dividers. In theory it should have been easy enough - that was another lesson learned - make sure the jointer cuts the biscuit slot halfway through the board thickness. The sigh-line on my jointer is supposed to show [i Would have thought] a line where you could expect the slot to be cut. Fail - it appears to be factory graffitti and nothing to do with slots, as it is nowhere near the right location.
There's a bit of a gap in photos, but this is the fiished article, along with that thumbs up from its new owner:
My son wanted blue, so he got blue. He wanted this shade of blue, so he got that too. He didn't get whatever colour the unit was sold in, which is obviously the other great advantage of building these yourself. As you can see from the top photo, his room is blue too, so this unit's colour fits in well. I had grand designitis and was planning to paint it in Arsenal colours, with the gunners logo airbrushed, but it's been a good few years since I airbrushed anything, so that can wait for another project (maybe the one in my other son's room).
I hope it's not a too bad first attempt....
The tat you buy from the warehouses either seems to cost the earth, or is made from paper and just not worth the money. They are also fixed sizes, so making my own was a breath of fresh air and a bit of a baptism at the same time.
I got the desgn from a free template somwehere on the interweb, but I adapted the sizes to better suit my son's room and toys. I also added a couple of bits to strengthen it from the original design, but in doing so I appear to have complicated it slightly above my rather amateurish woodworking skill levels. Hopefully, what I've learnt from making this will benefit the next project.
Anyway, it got a thumbs up from the customer so here's a few pics from start to finish:

This is a layout of all the base pieces of the unit, which has kickboards set back from the front to allow feet under. I used biscuits as that was supposed to be the easiest way to do the joints, however, as I have a pretty cheap jointer and my jointing experience was low-to-nil, it was perhaps not as simple as it should have been. Leesons learned and next time should be better.

This shows the base built up and primed. on the corner at the bottom of the photo, you can just about see the cut-out (rebate?) that I made so the unit sits over the carpet gripper rods, which allows it to be square with the wall. Furniture always seems to have be be packed at the front with cardboard just to make it stand upright.
Now the base is painted:

You can see the biscuits that I use to [try] to align the three vertical dividers. In theory it should have been easy enough - that was another lesson learned - make sure the jointer cuts the biscuit slot halfway through the board thickness. The sigh-line on my jointer is supposed to show [i Would have thought] a line where you could expect the slot to be cut. Fail - it appears to be factory graffitti and nothing to do with slots, as it is nowhere near the right location.
There's a bit of a gap in photos, but this is the fiished article, along with that thumbs up from its new owner:

My son wanted blue, so he got blue. He wanted this shade of blue, so he got that too. He didn't get whatever colour the unit was sold in, which is obviously the other great advantage of building these yourself. As you can see from the top photo, his room is blue too, so this unit's colour fits in well. I had grand designitis and was planning to paint it in Arsenal colours, with the gunners logo airbrushed, but it's been a good few years since I airbrushed anything, so that can wait for another project (maybe the one in my other son's room).


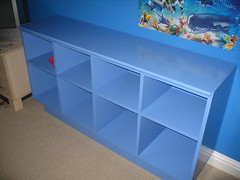

I hope it's not a too bad first attempt....