adzeman
Established Member
This is a WIP of three parts running concurrently.
Firstly. In September last year purchased a thicknesser/planer where does it go in a small crowded workshop?
Second It requires a stand.
Third. I need to improve my door making skills.
Part of my negotiations with SWMBO I agreed for our dryer and spare washing machine to be kept in the workshop along with my beer fridge. as luck would have it some of our white goods went belly up and a visit to the fire sale at Comet resulted in all our kitchen white goods being replaced. This resulted in a re-negotiation with floor space resulting in just the dryer staying along with my fridge.
So this is the canvas.
Further to the three parts I need to improve my skill set in making doors. I am happy making them out of timber wether hardwood or softwood but I would like to tru other materials such as MDF and some of the modern paints which most kitchen units are decorated.
So this is the plan
There’s a lot to work out from this plan so the first item is to build the first cupboard keeping it as small or narrow as possible. The minimum width being the width of the wash basket it has to hold.
Having established this position the next point will be the tool stand/shelves or is it the planer/thicknesser base? I need both, I have the dimensions of the planer but it has a number of protrusions, knobs and the like and it may have to spin to come out of the gap so the planer base is favourite. I used the top rail of the cupboard as a rod to calculate the height as I want the planer plate to be just 6mm above my bench heights.
I purchased the casters and used them to calculate the height off the floor.
Firstly. In September last year purchased a thicknesser/planer where does it go in a small crowded workshop?
Second It requires a stand.
Third. I need to improve my door making skills.
Part of my negotiations with SWMBO I agreed for our dryer and spare washing machine to be kept in the workshop along with my beer fridge. as luck would have it some of our white goods went belly up and a visit to the fire sale at Comet resulted in all our kitchen white goods being replaced. This resulted in a re-negotiation with floor space resulting in just the dryer staying along with my fridge.
So this is the canvas.
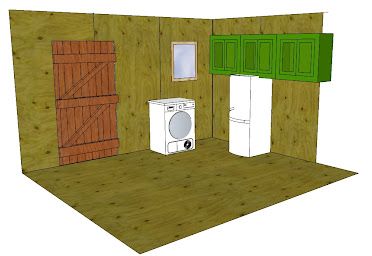
Further to the three parts I need to improve my skill set in making doors. I am happy making them out of timber wether hardwood or softwood but I would like to tru other materials such as MDF and some of the modern paints which most kitchen units are decorated.
So this is the plan
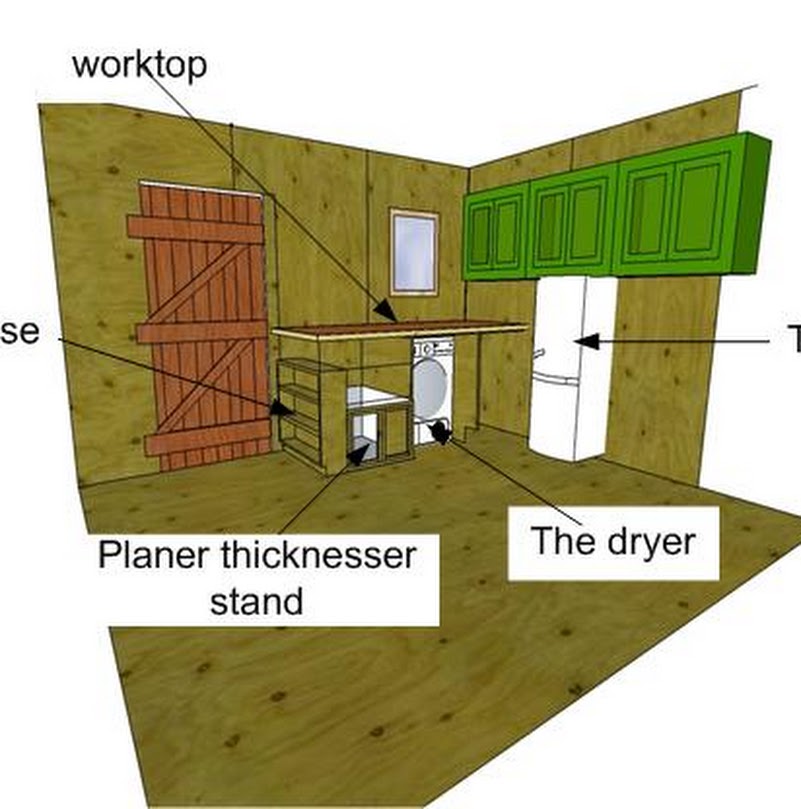
There’s a lot to work out from this plan so the first item is to build the first cupboard keeping it as small or narrow as possible. The minimum width being the width of the wash basket it has to hold.
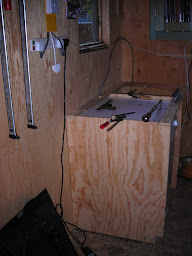
Having established this position the next point will be the tool stand/shelves or is it the planer/thicknesser base? I need both, I have the dimensions of the planer but it has a number of protrusions, knobs and the like and it may have to spin to come out of the gap so the planer base is favourite. I used the top rail of the cupboard as a rod to calculate the height as I want the planer plate to be just 6mm above my bench heights.
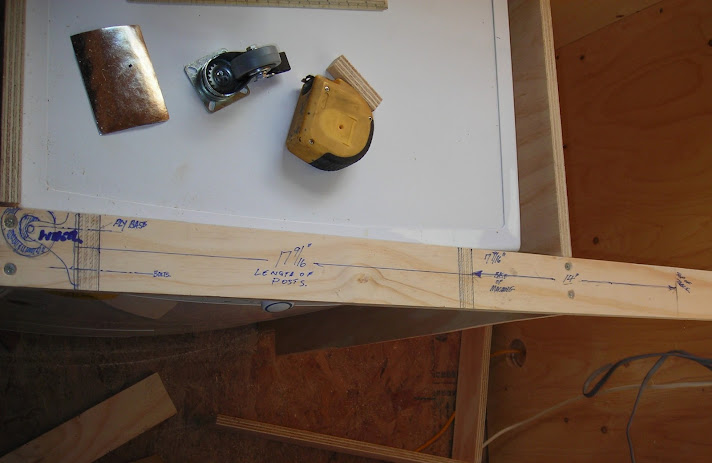
I purchased the casters and used them to calculate the height off the floor.