wallace
Established Member
I've been itching to start this since I got it a few weeks ago. I started takeing it to bits today. I always find it amazeing when dismantling wadkin stuff that its 60 year old been left outside and the nuts and bolts come undone as if they were new. Still with clean shiny threads.
One of the guides has a big chunk out of it
Its a pitty a new isolator had been installed
The original switch gear was missing
This is what it should look like
This is the first time I've been able to move a wadkin base by myself, its made from aluminium
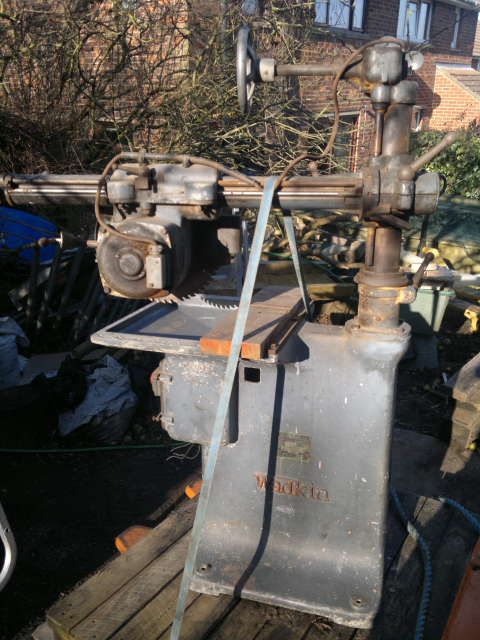



One of the guides has a big chunk out of it

Its a pitty a new isolator had been installed

The original switch gear was missing

This is what it should look like





This is the first time I've been able to move a wadkin base by myself, its made from aluminium
