Richard T
Established Member
erm.. yerss.. for once it's a relief to have a little one.
Anyway, here's the thing that the thing goes through with the thing that goes through it, through it.
Yes! It's half a G cramp with holes drilled in it.
The side plates need to have another plate fixed on to them so as the rivet heads don't interfere with the vertical sliding; I think I will use pretty brass sheet for that.
The hooked piece is about to get two holes drilled through it to take different dog tools - straight spike for bigger, lumpy, bark-still-on stuff and gentler, more padded feet for stock I don't want to put spike holes in.
Also I will draw out the back end of the bar into a thin tang to put a wooden handle on.
Anyway, here's the thing that the thing goes through with the thing that goes through it, through it.
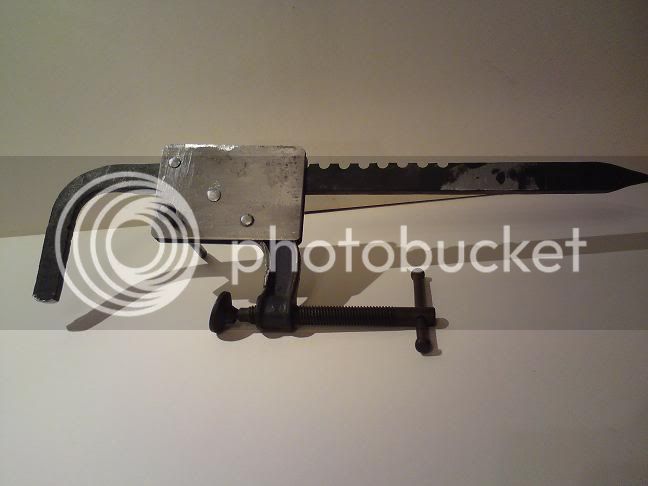
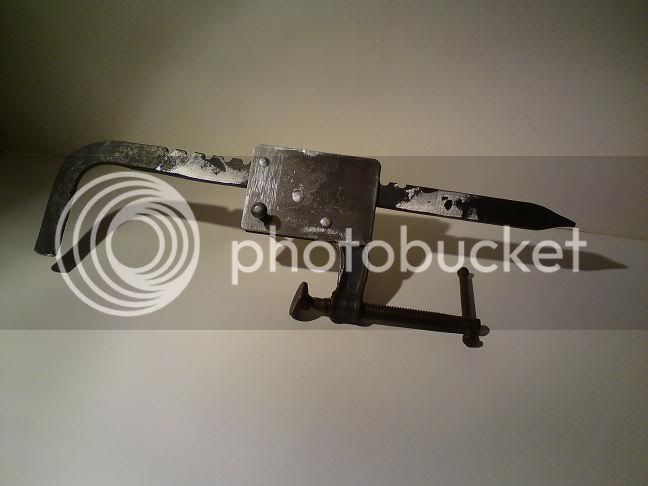
Yes! It's half a G cramp with holes drilled in it.
The side plates need to have another plate fixed on to them so as the rivet heads don't interfere with the vertical sliding; I think I will use pretty brass sheet for that.
The hooked piece is about to get two holes drilled through it to take different dog tools - straight spike for bigger, lumpy, bark-still-on stuff and gentler, more padded feet for stock I don't want to put spike holes in.
Also I will draw out the back end of the bar into a thin tang to put a wooden handle on.