OPJ
Established Member
Hi guys,
Anyone got any tips for removing bobbin sleeves from the Jet JBOS-5 spindles?
Bobbins larger than 16mm aren't a problem, where you remove a nut on top of the spindle and the sleeve slides off easily. On the smaller ones though (6mm, 12mm and 16mm), they're held in place with a small black clip:
Even with the screw removed, it's as if they've been glued on!! :x
Just to show that there's nothing holding them on at the other end:
I can't get them to budge.
What I'd really like to to is to remove them and flip them 180° to use the un-used upper portion of the sleeves. So, I'd rather not resort to using a knife, if I can help it! :wink: (Then, there would also be the risk of damaging the rubber bobbin...)
Axminster have e-mailed me back (with an admission that these have never been easy to remove) and have suggested the use of "rolling dough" to grip the abrasive, while using a twisting motion to gradually ease the sleeve away. I might give this a go, if I can steal some from the kitchen...!
Does anyone have any other suggestions?
There must be someone out there who's done this before???
Thanks,
Olly.
Anyone got any tips for removing bobbin sleeves from the Jet JBOS-5 spindles?
Bobbins larger than 16mm aren't a problem, where you remove a nut on top of the spindle and the sleeve slides off easily. On the smaller ones though (6mm, 12mm and 16mm), they're held in place with a small black clip:
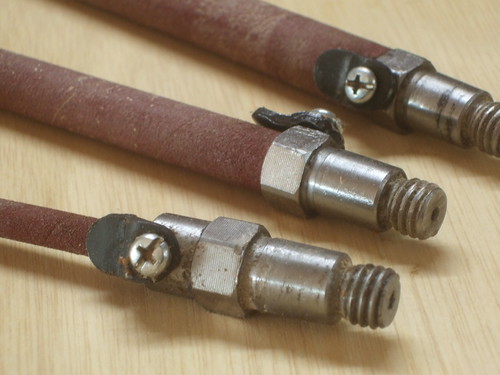
Even with the screw removed, it's as if they've been glued on!! :x
Just to show that there's nothing holding them on at the other end:
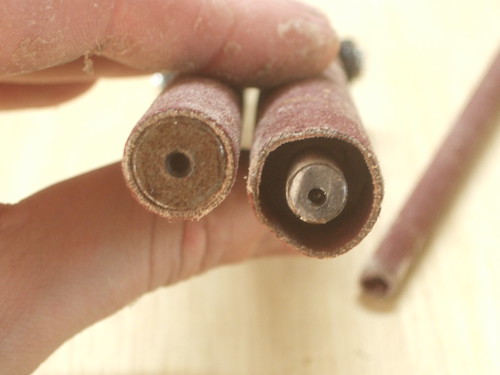
I can't get them to budge.
Axminster have e-mailed me back (with an admission that these have never been easy to remove) and have suggested the use of "rolling dough" to grip the abrasive, while using a twisting motion to gradually ease the sleeve away. I might give this a go, if I can steal some from the kitchen...!
Does anyone have any other suggestions?
There must be someone out there who's done this before???
Thanks,
Olly.