Good Surname or what ?
Established Member
After my earlier experience at the Windsor Workshop I've come back this week to make a Sack Back Chair - like this one.
Phil
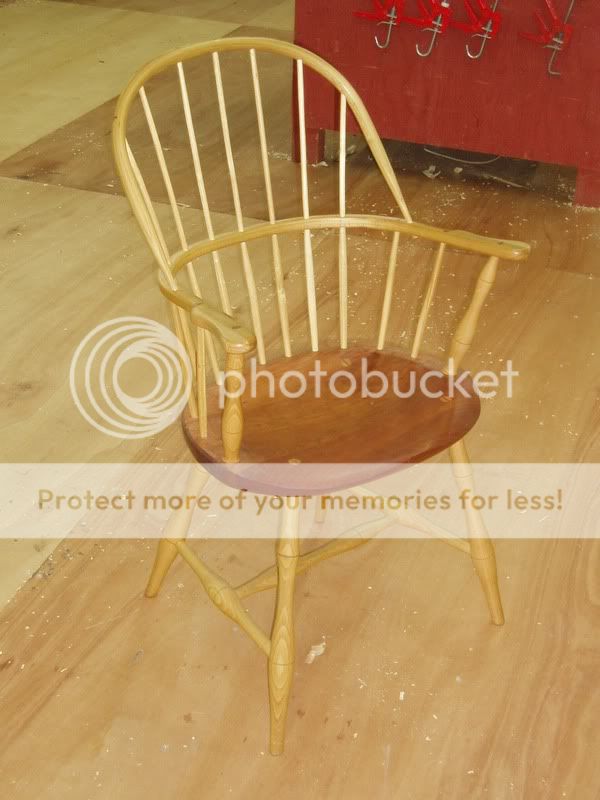
Phil
it's time for a well earned beer.
Good Surname or what ?":3iheuck1 said:Day 3.
... speaking of travishers. This one I bought from James earlier in the year is a wonderful tool.
Enter your email address to join: