Ironballs
Established Member
Okay chaps, finally taken the brave pills and have embarked on this years evening class project, a Les Paul copy, in no small part helped by the previous builds I've seen on here.
Over the summer I've been doing the research, read Melvyn Hiscock's book, bought the plans, bought some tools, bought some wood, trawled the net and stared longingly at Messrs Page, Perry and Slash in action.
So, you have to start somewhere and I started with with a length of mahogany that needed converting into a 2 piece body blank. First up I gave a good going over with a jack plane and a number 6 to remove the rough and have a look at the grain underneath. This was partly because I wanted to practice my hand planing and partly because I needed to cut the 5ft board up before introducing it to the P/T and wanted to see where best to make my cuts. See below
Tell you what, mahogany shavings are great for starting fires in the stove
Once I had the boards roughed out I laid over the cut outs from my template for no particular reason at all. Have created some plywood templates from these to use as references for doing the body carve.
Next step would have been glueing the body together but further research revealed that my titebond 3 was heavily frowned upon for instrument making but titebond 1 was perfect. Shame I didn't have any. Ebay solved that.
Whilst I was waiting I took my neck material and started preparing that. You may have seen in another thread that I got my hands on a large piece of 4" mahogany and I need to go about converting that. This is where having access to a college workshop really is a plus, first cut was on the bandsaw, this little fella stands about 8-9ft tall and takes no prisoners. After taking one length off planed up the end to square-ish and used the fence on their TS to cut the rest of the lengths.
Not sure what I'll do with the rest of the neck blanks but you can get 2 one-piece Les Paul necks per blank so might stick them on the bay. All nice and straight and a couple show a bit of quarter sawn flecking.
Took one of the blanks to college this week and set about it with the templates and the bandsaw, was quite pleasantly surprised to find that hidden in there was a neck shaped object and it didn't take too long to find it. A very rewarding evening
Last job was to take a paper template and create my very own plywood Les Paul. What an axe! Step aside Angus the real deal is here
This will be a slow burner and is likely to take me the full three terms but I'll post updates as I go along. I've already bought the wood for the top and I think you'll like it......
Over the summer I've been doing the research, read Melvyn Hiscock's book, bought the plans, bought some tools, bought some wood, trawled the net and stared longingly at Messrs Page, Perry and Slash in action.
So, you have to start somewhere and I started with with a length of mahogany that needed converting into a 2 piece body blank. First up I gave a good going over with a jack plane and a number 6 to remove the rough and have a look at the grain underneath. This was partly because I wanted to practice my hand planing and partly because I needed to cut the 5ft board up before introducing it to the P/T and wanted to see where best to make my cuts. See below
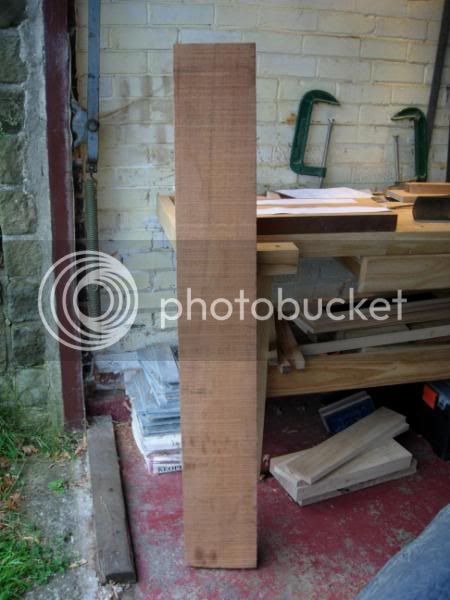

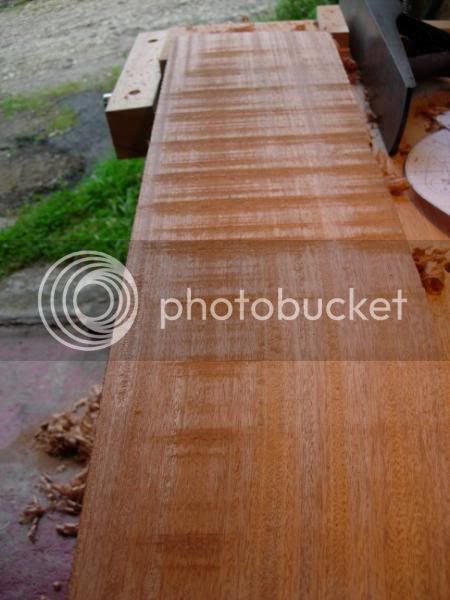
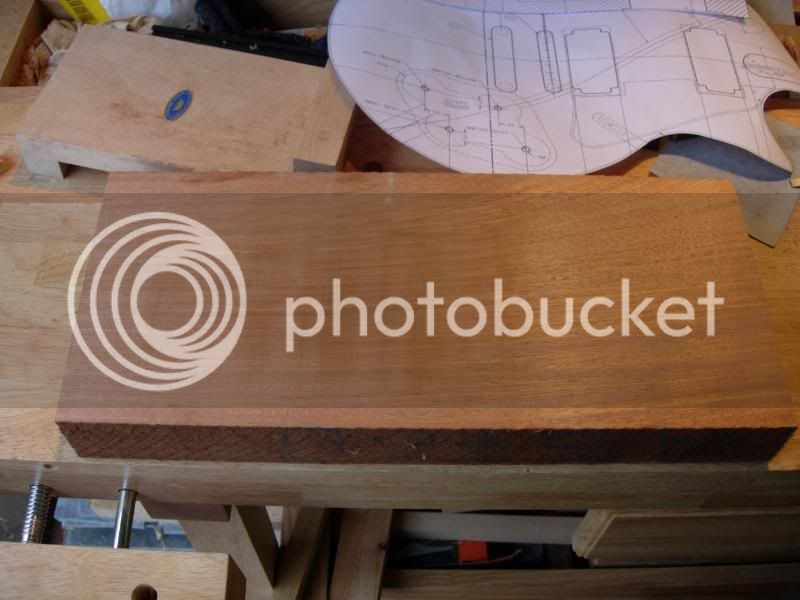
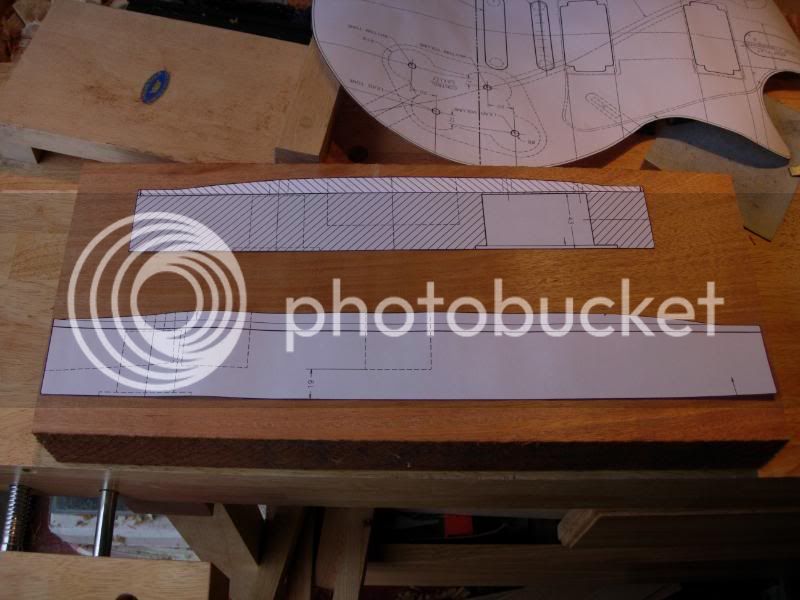
Tell you what, mahogany shavings are great for starting fires in the stove
Once I had the boards roughed out I laid over the cut outs from my template for no particular reason at all. Have created some plywood templates from these to use as references for doing the body carve.
Next step would have been glueing the body together but further research revealed that my titebond 3 was heavily frowned upon for instrument making but titebond 1 was perfect. Shame I didn't have any. Ebay solved that.
Whilst I was waiting I took my neck material and started preparing that. You may have seen in another thread that I got my hands on a large piece of 4" mahogany and I need to go about converting that. This is where having access to a college workshop really is a plus, first cut was on the bandsaw, this little fella stands about 8-9ft tall and takes no prisoners. After taking one length off planed up the end to square-ish and used the fence on their TS to cut the rest of the lengths.
Not sure what I'll do with the rest of the neck blanks but you can get 2 one-piece Les Paul necks per blank so might stick them on the bay. All nice and straight and a couple show a bit of quarter sawn flecking.

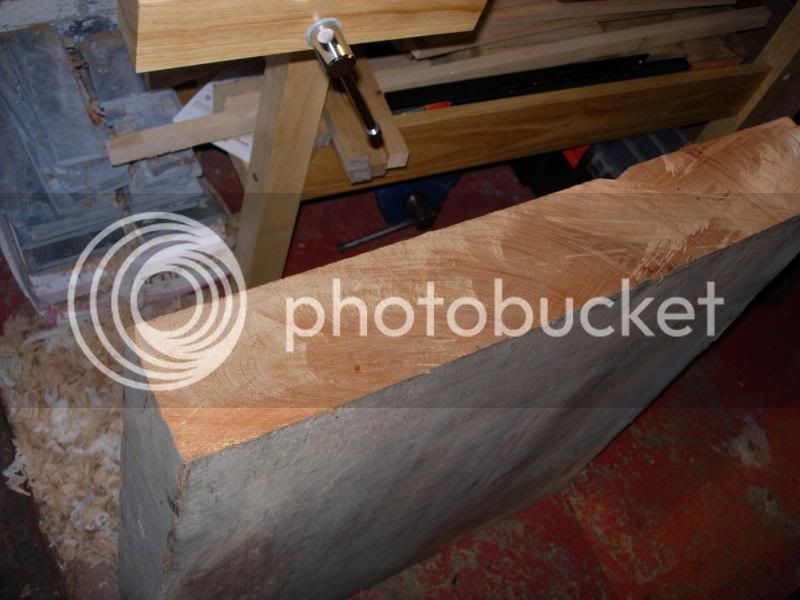
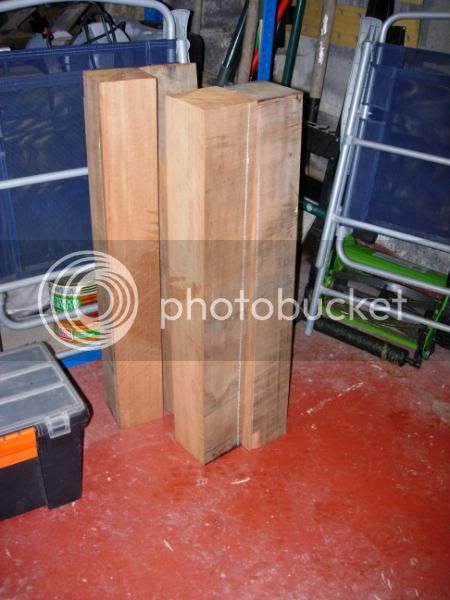

Took one of the blanks to college this week and set about it with the templates and the bandsaw, was quite pleasantly surprised to find that hidden in there was a neck shaped object and it didn't take too long to find it. A very rewarding evening


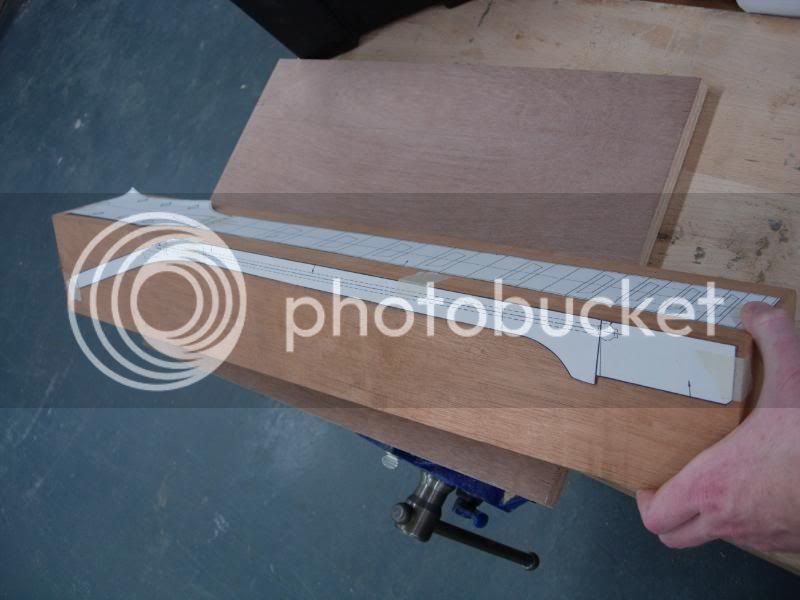
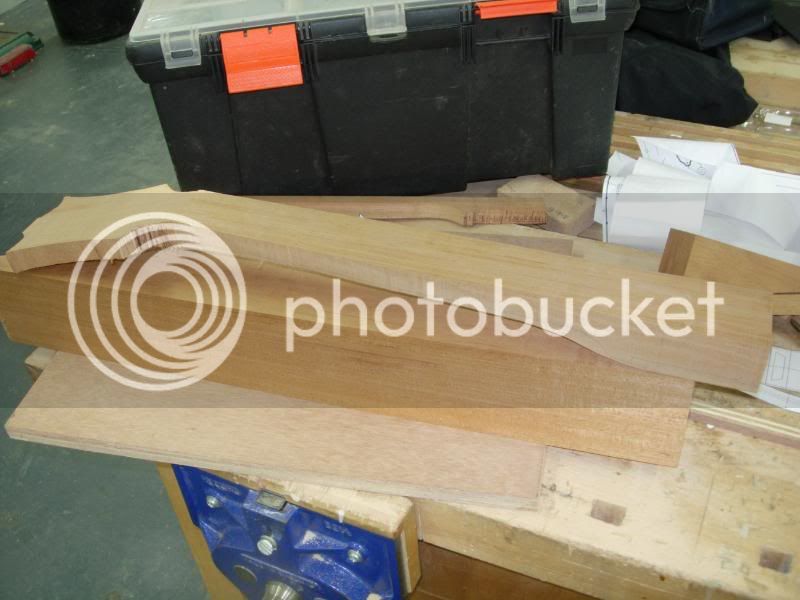
Last job was to take a paper template and create my very own plywood Les Paul. What an axe! Step aside Angus the real deal is here

This will be a slow burner and is likely to take me the full three terms but I'll post updates as I go along. I've already bought the wood for the top and I think you'll like it......