MikeG.
Established Member
I have a big Denbigh pillar drill, the K1 Series 2:
I have just broken the depth stop:
It's obviously not an original part, and it has never worked properly, but nonetheless it is a bit frustrating that I have just over-tightened it and broken the aluminium casting. That casting and the packers fitted around this threaded area:
Does anyone have an illustration of what the original looked like? Did it used to screw onto the thread in the last photo?
-
That's the important stuff. Next, whilst we're talking about this machine, it has a non-original casting on the top which fouls the pulleys, so I have a little spacer or two to hold it out of harms way. Any advice on that would be useful:
And finally, the handles look like this:
They look like they were made by a farmer, and annoyingly, just slightly foul the handle which raises and lowers the table. Again, suggestions of what to do are most welcome.
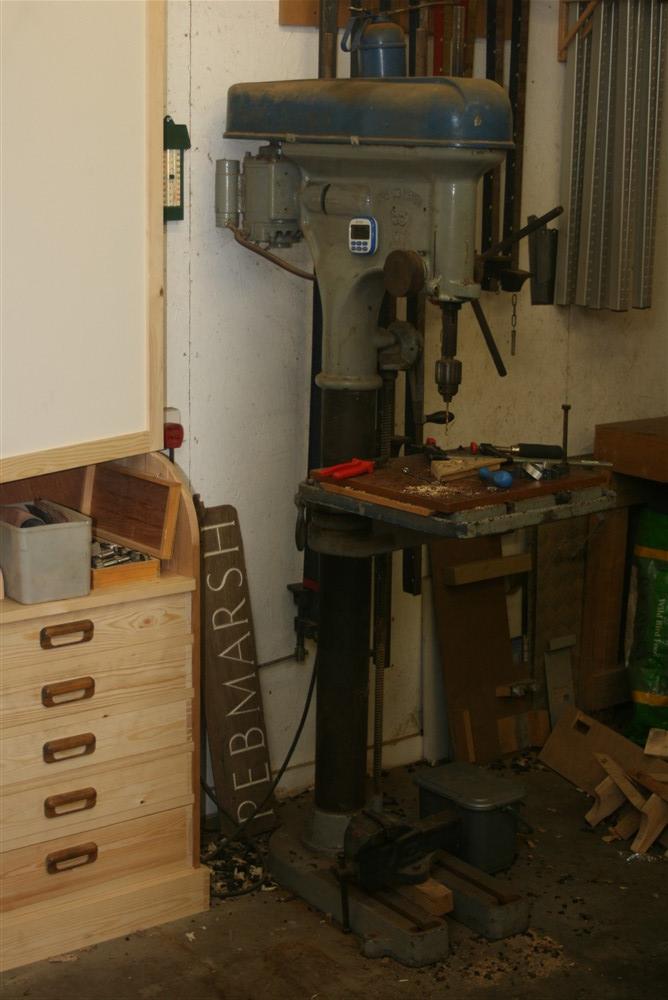
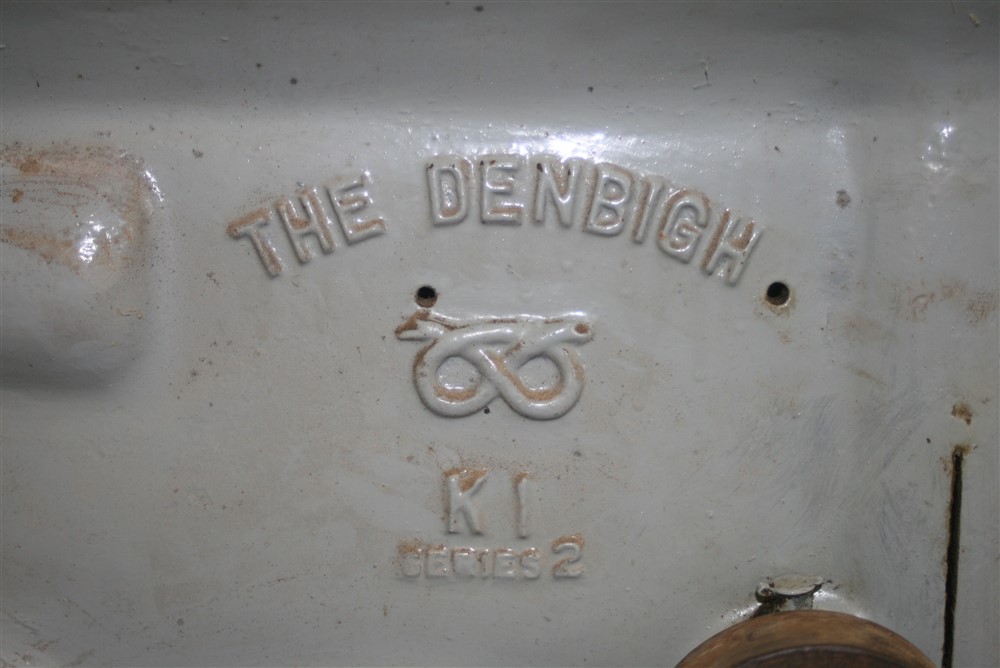
I have just broken the depth stop:
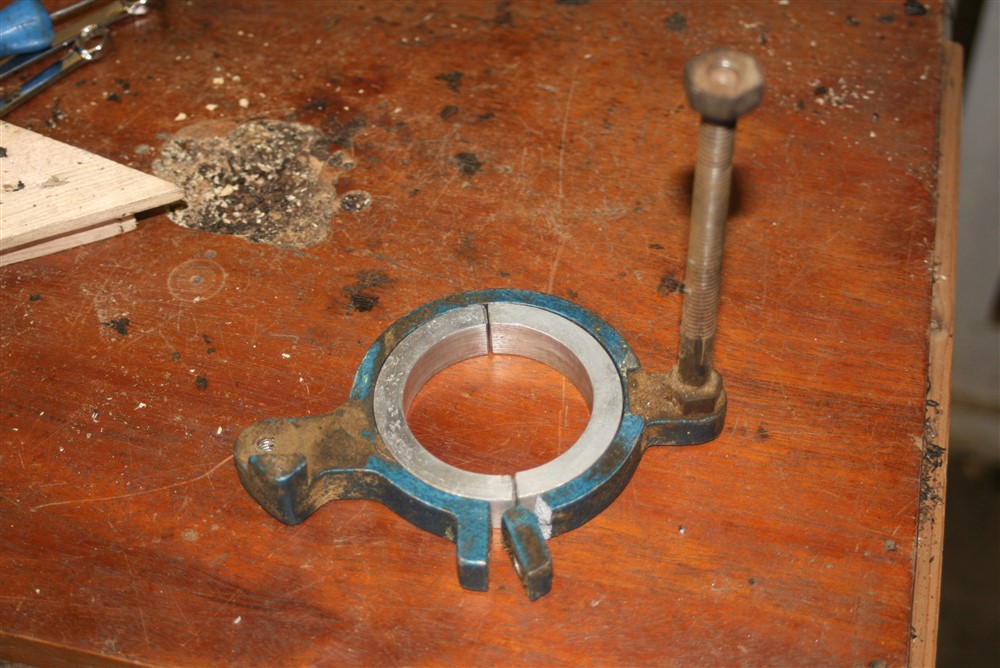
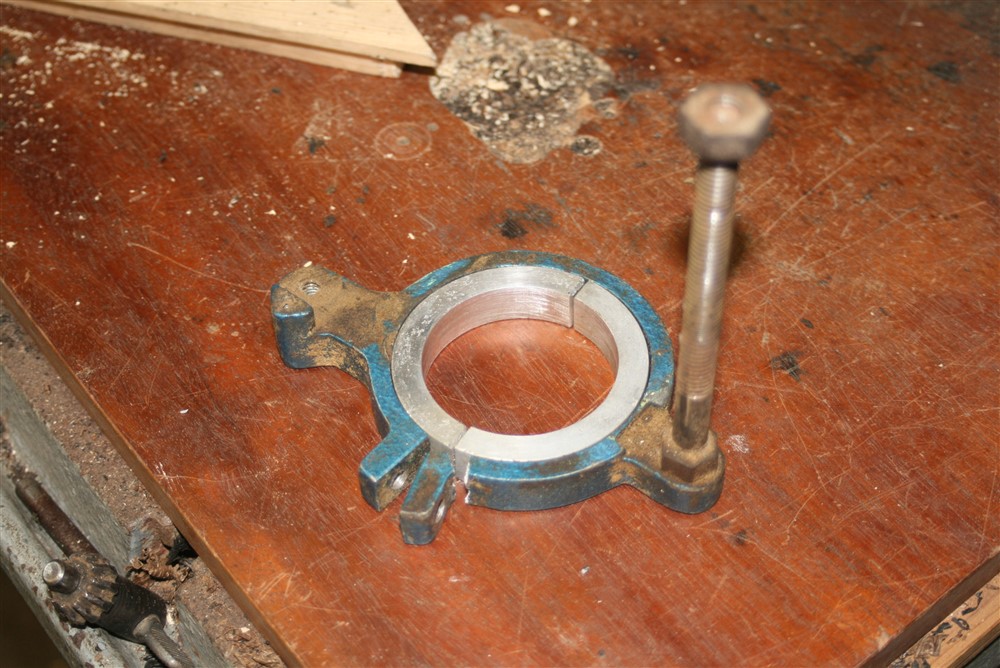
It's obviously not an original part, and it has never worked properly, but nonetheless it is a bit frustrating that I have just over-tightened it and broken the aluminium casting. That casting and the packers fitted around this threaded area:
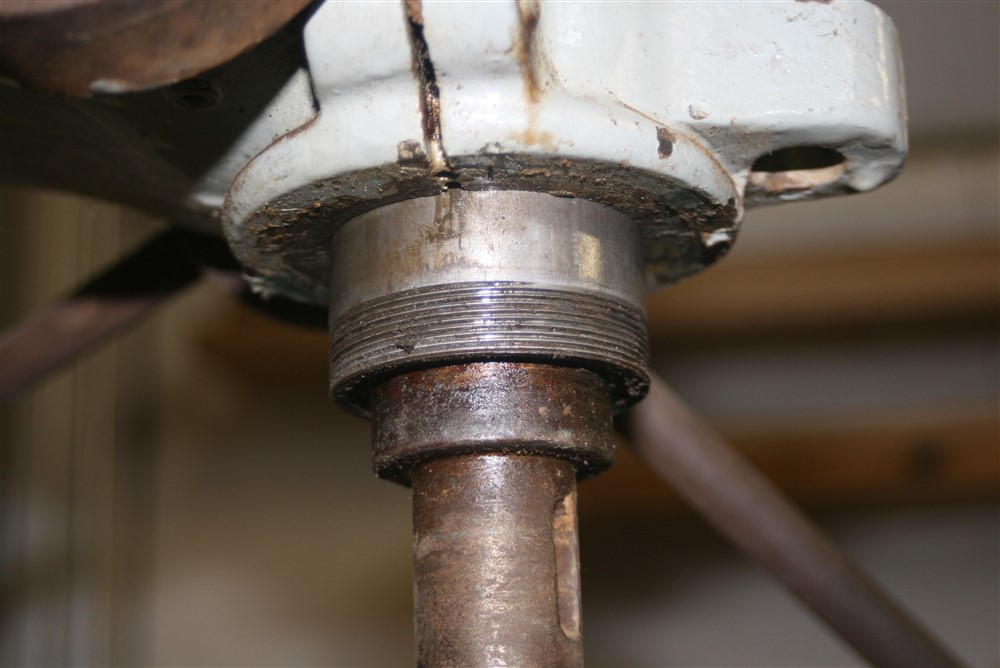
Does anyone have an illustration of what the original looked like? Did it used to screw onto the thread in the last photo?
-
That's the important stuff. Next, whilst we're talking about this machine, it has a non-original casting on the top which fouls the pulleys, so I have a little spacer or two to hold it out of harms way. Any advice on that would be useful:
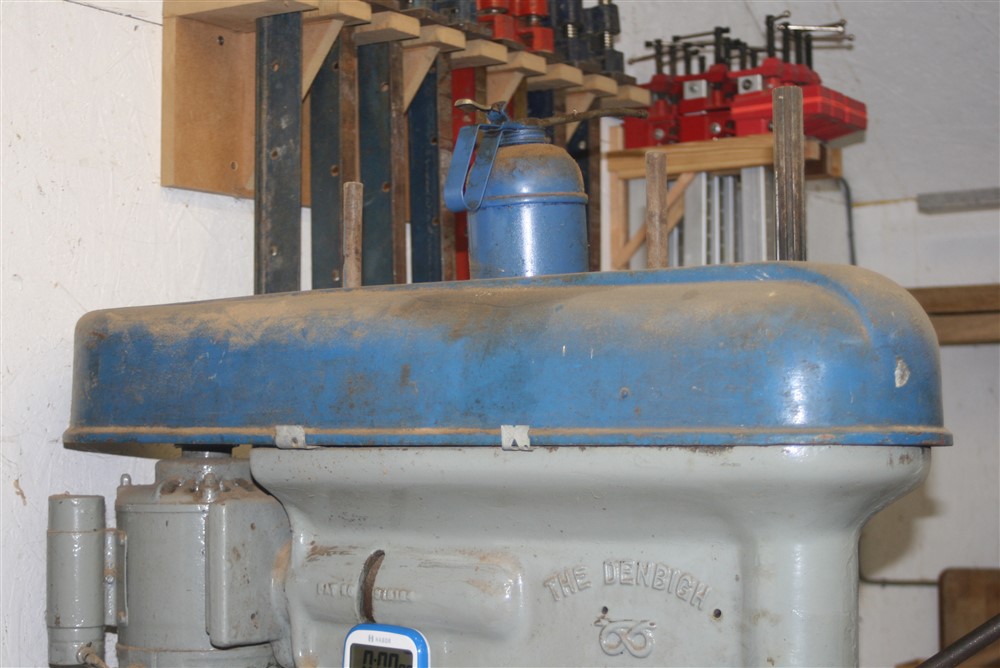
And finally, the handles look like this:
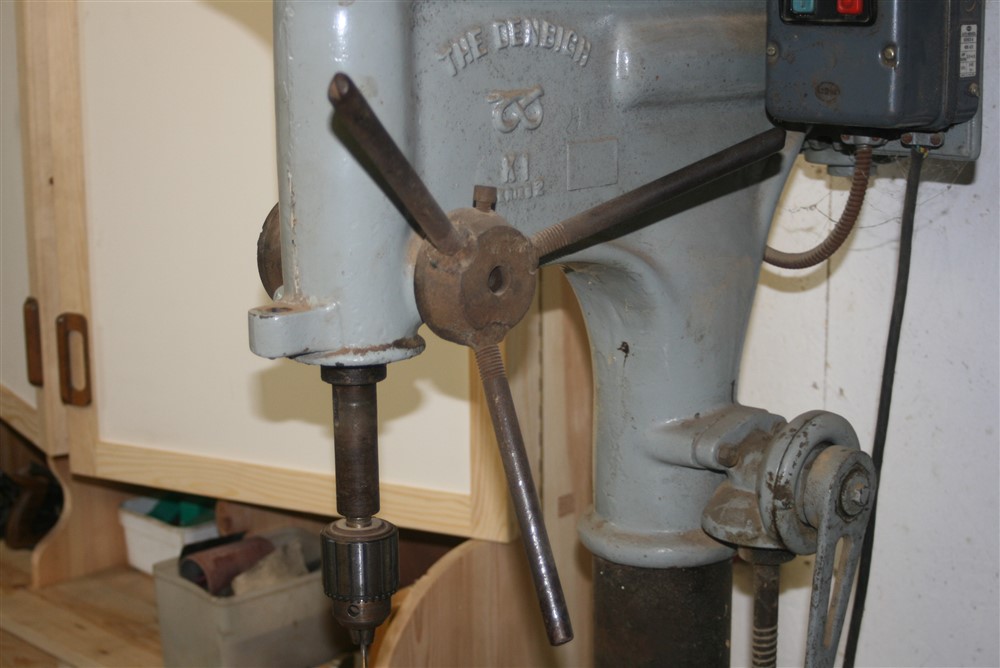
They look like they were made by a farmer, and annoyingly, just slightly foul the handle which raises and lowers the table. Again, suggestions of what to do are most welcome.