So , my mate asked me to make some garage doors for him, as his were going rotten.
He just wanted pine and similar to what he already had. No talking to him about oak would make him change his mind .
So - anyone no where to get decent pine/redwood in the Coventry area ?????
I know where to get hardwoods !
so off I went to my local timber yard, to get some sawn timber.
I picked the best bits I could get at - they weren't happy mind
I took an inverter and my jigsaw along with my cutting list, and cut everything roughly to length so I could fit it in my van.
Sticked it up in the workshop for a couple of weeks to stabilize.
Now it was ready to start.
1st off, cross cutting on my TS with a sled. My mitre saw wont cut 7x2's, but I prefer the TS regardless !
nice and square
everything cut to length
now for a while on the thicknesser
and trued up the sides by ripping on the TS
all the rails and all the styles clamped together - I started marking out the M&T's
1st cuts of the tenons done on the band saw
Shoulders cut on the TS
I cut the center out of the mid rail double tenons with the morticer
nearly done -
cheeks next, with the router
all the tenons done
MISTAKE !!! I nearly cut one of the haunches off - wrong line
:roll:
so I repaired it with a slice to fill the kerf cut and a dowel to strengthen the haunch. theory was , its there to stop the rail twisting later on, so it should do the job
with a mortise gauge and a rod, I transfered the dimensions over to the styles.
and cut the mortises
I cut the last bit out of the end with a chisel to keep it neat
well that's all the joints done
a touch up with a block plane and chisel before the dry fit
All ready for clue up . I'm using PU, so need to work fast !
after the glue had set up, I routed out the rebates for the windows boards and panels
squaring up the window corners with a chisel
it started chucking down outside, so the dog decided to join me and Norm inside
I rounded over the top and bottom ship lap boards and fitted them with a dab of PU and panels pins each. Leaving a gap at each lap for them to move.
The inside of the door will have a ply panel PU'd in and to the middle baton, thus locking it all together front and back. I've left it off so I can treat and paint inside the cavity.
after some sanding, they are ready for the wood preservative . orrid stuff !
I dont take any risks with it.... door open with fan blowing clean air at my work area.... plenty of safety gear ... and when finished, straight inside for a shower and clothes in the washing machine. workshop cannot be entered again for 8 hrs !
It does show up the joints well tho
well thats it so far - the 8 hrs is just about up and I'm ka nak erred !
off to give them a coat of primer in a min before bed !
sorry for all the typo's at this late hour !
He just wanted pine and similar to what he already had. No talking to him about oak would make him change his mind .
So - anyone no where to get decent pine/redwood in the Coventry area ?????
I know where to get hardwoods !
so off I went to my local timber yard, to get some sawn timber.
I picked the best bits I could get at - they weren't happy mind
I took an inverter and my jigsaw along with my cutting list, and cut everything roughly to length so I could fit it in my van.
Sticked it up in the workshop for a couple of weeks to stabilize.
Now it was ready to start.
1st off, cross cutting on my TS with a sled. My mitre saw wont cut 7x2's, but I prefer the TS regardless !
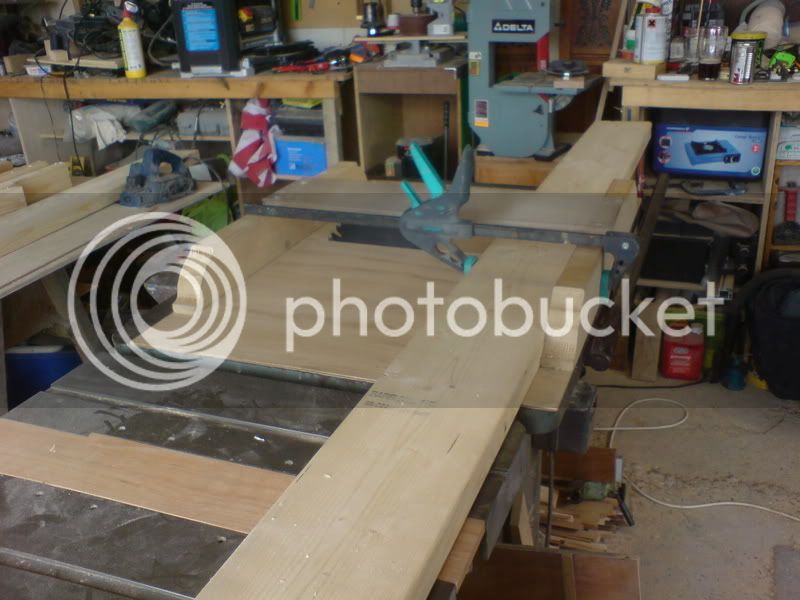
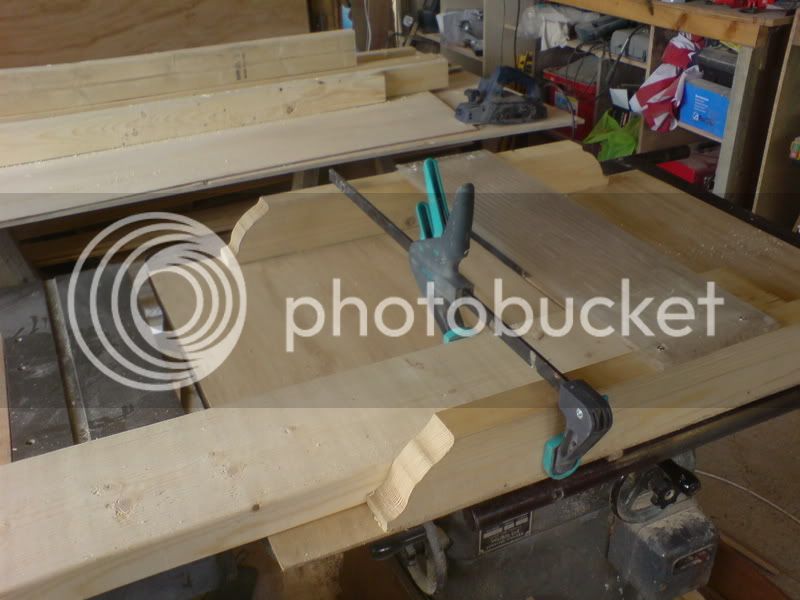
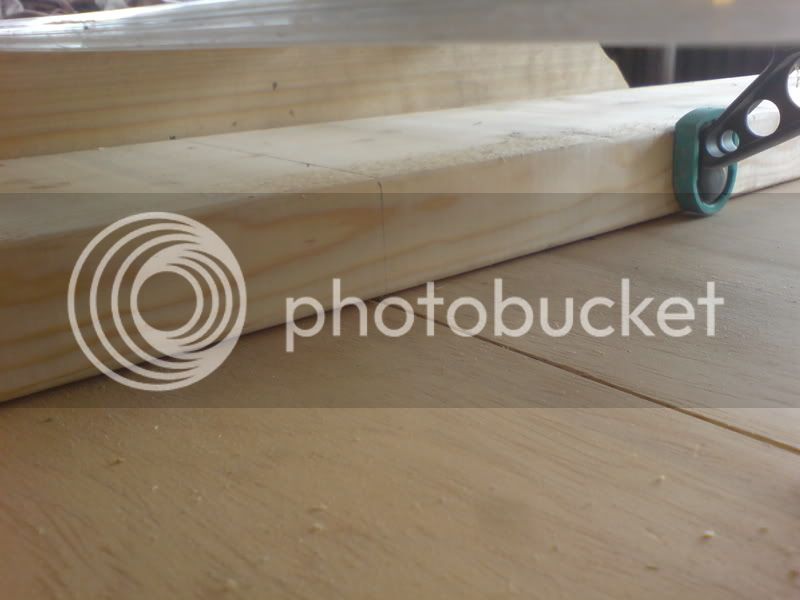
nice and square
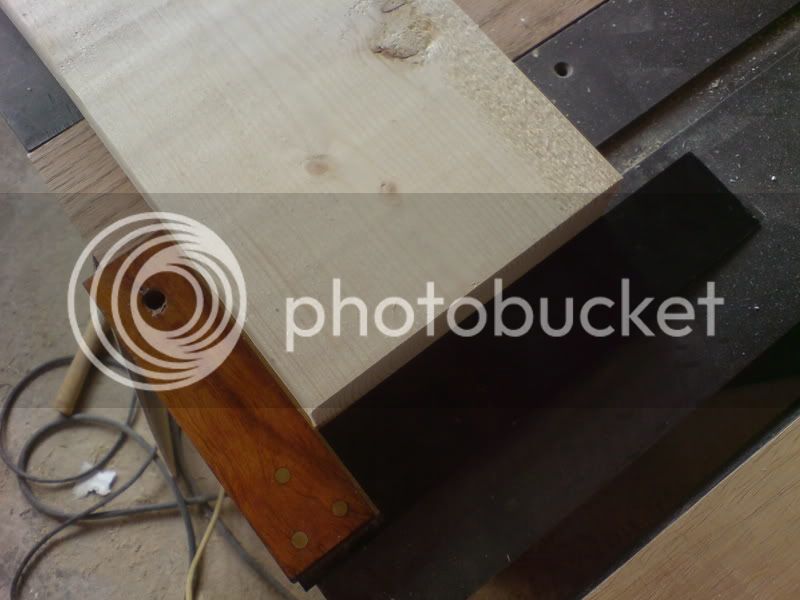
everything cut to length
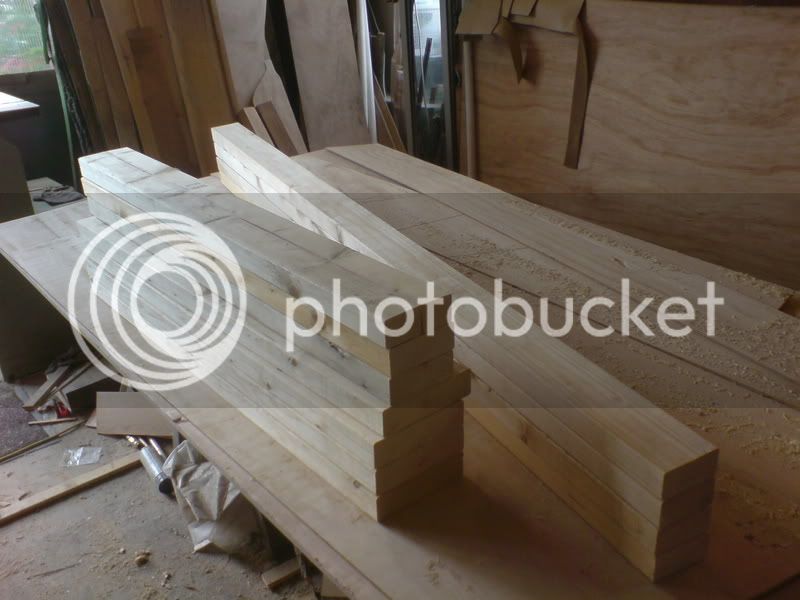
now for a while on the thicknesser
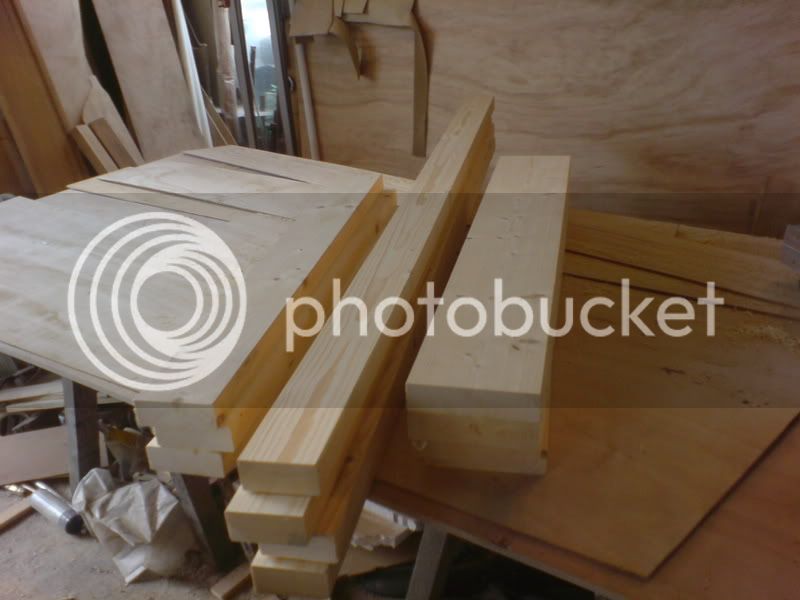
and trued up the sides by ripping on the TS
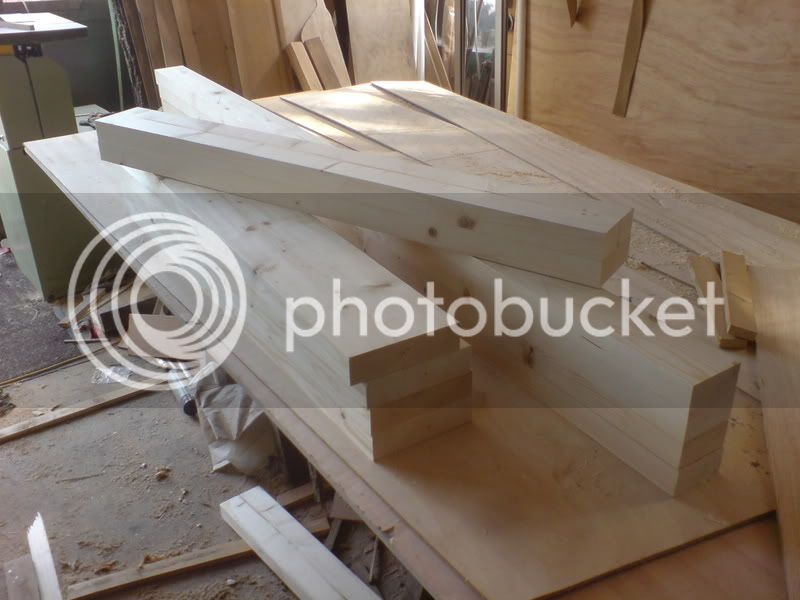
all the rails and all the styles clamped together - I started marking out the M&T's
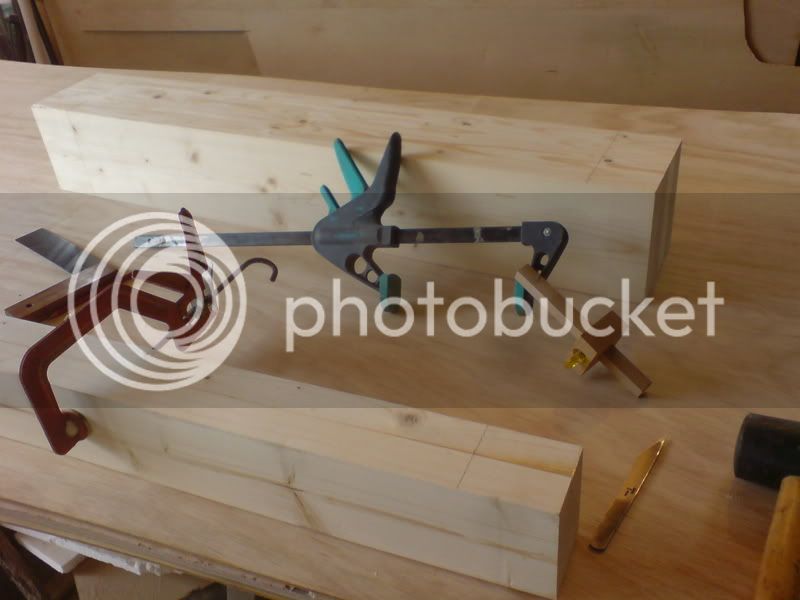
1st cuts of the tenons done on the band saw
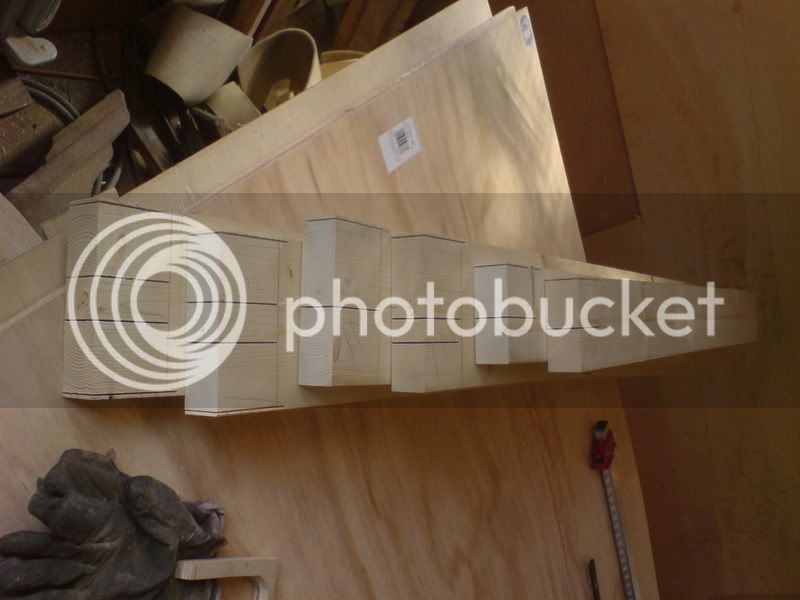
Shoulders cut on the TS
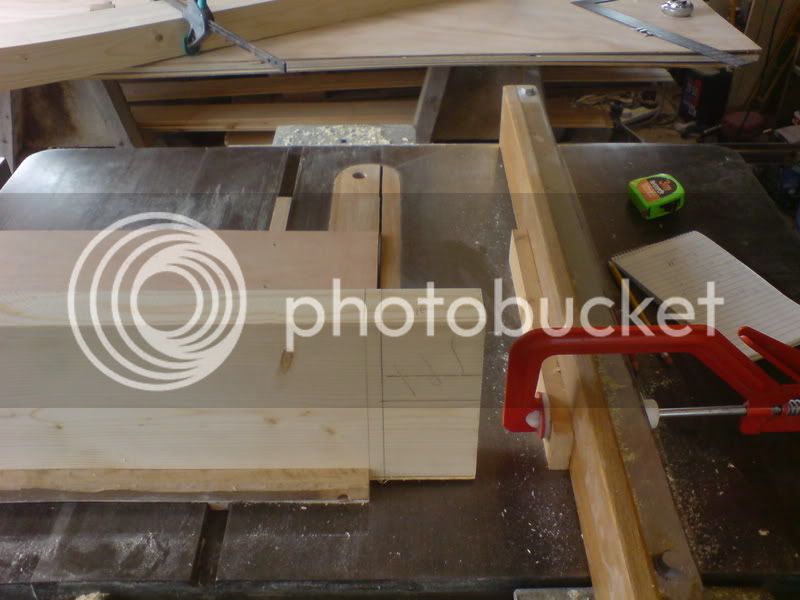
I cut the center out of the mid rail double tenons with the morticer

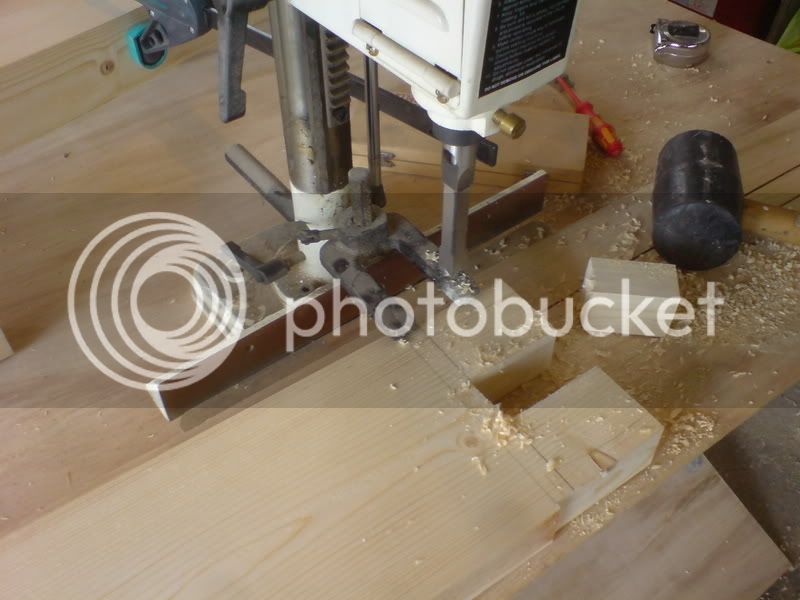
nearly done -
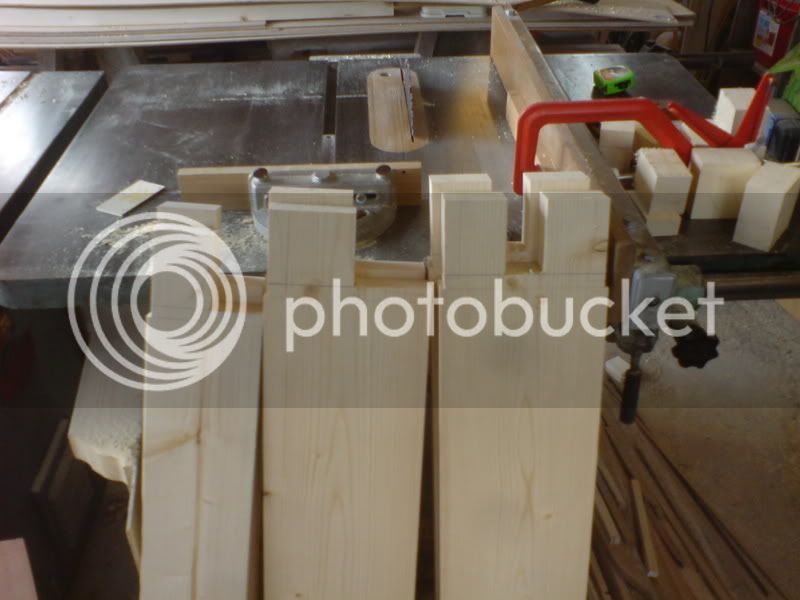
cheeks next, with the router
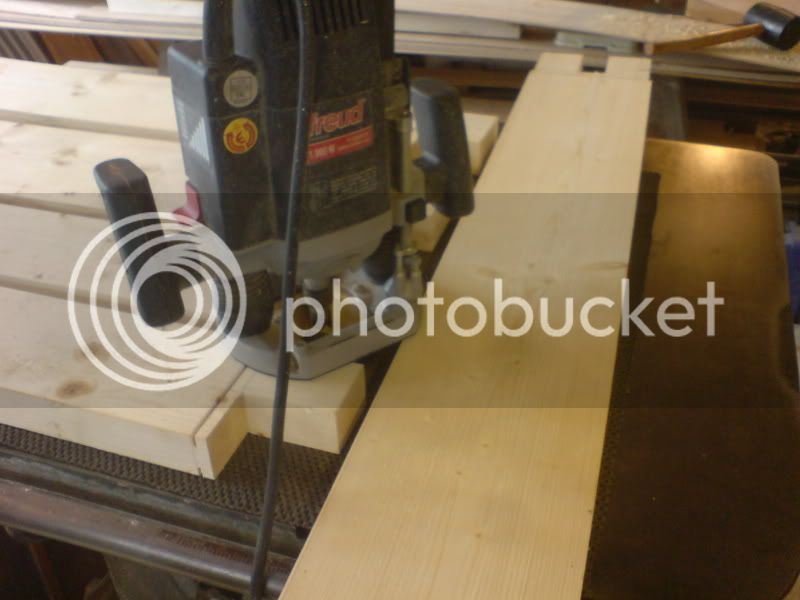
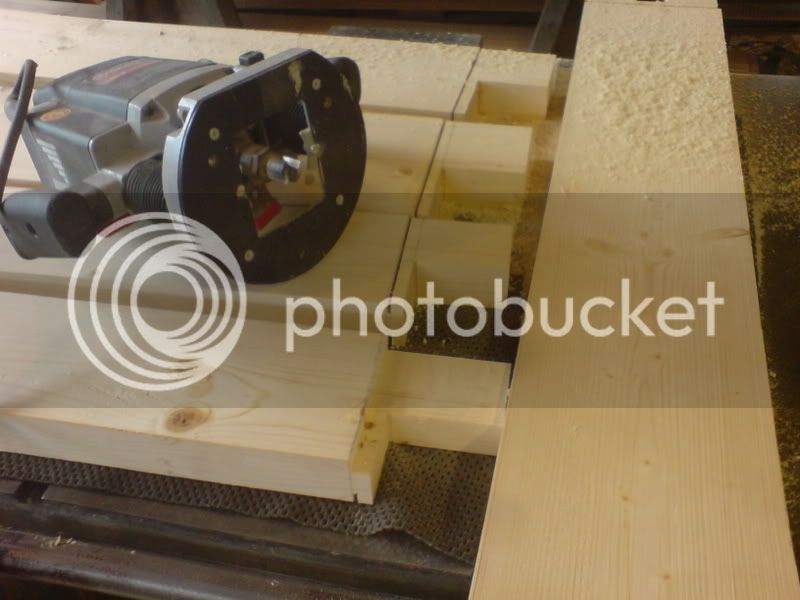
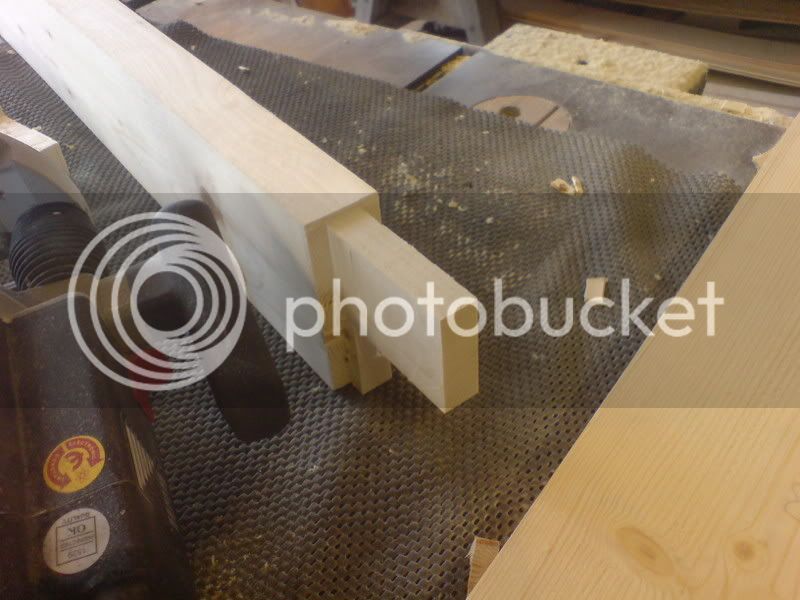
all the tenons done
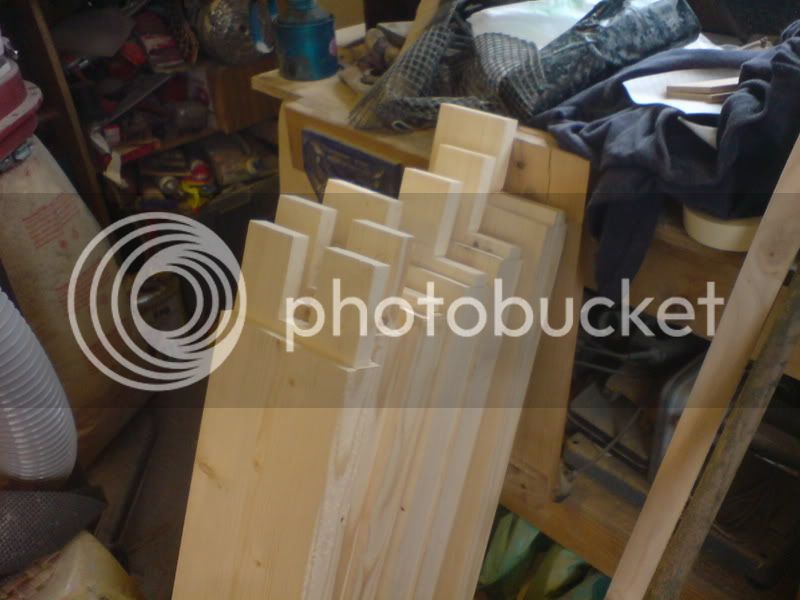
MISTAKE !!! I nearly cut one of the haunches off - wrong line
:roll:
so I repaired it with a slice to fill the kerf cut and a dowel to strengthen the haunch. theory was , its there to stop the rail twisting later on, so it should do the job
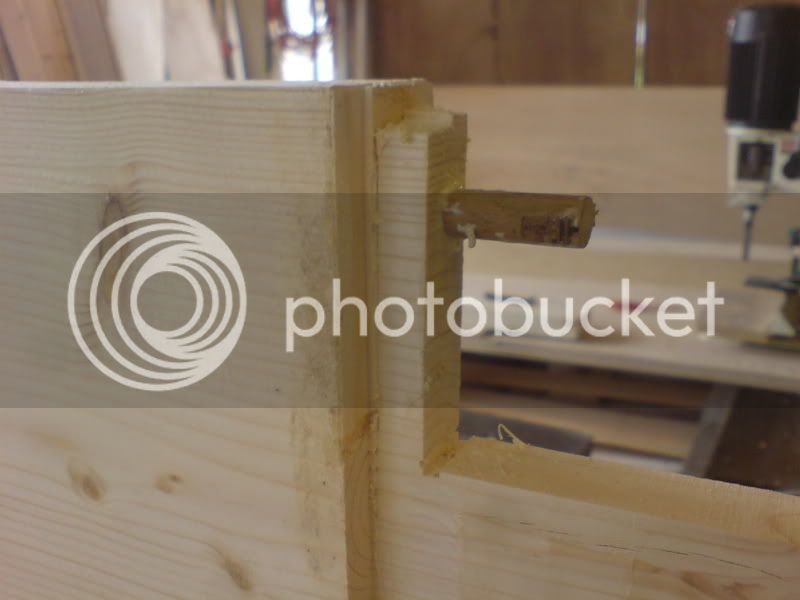
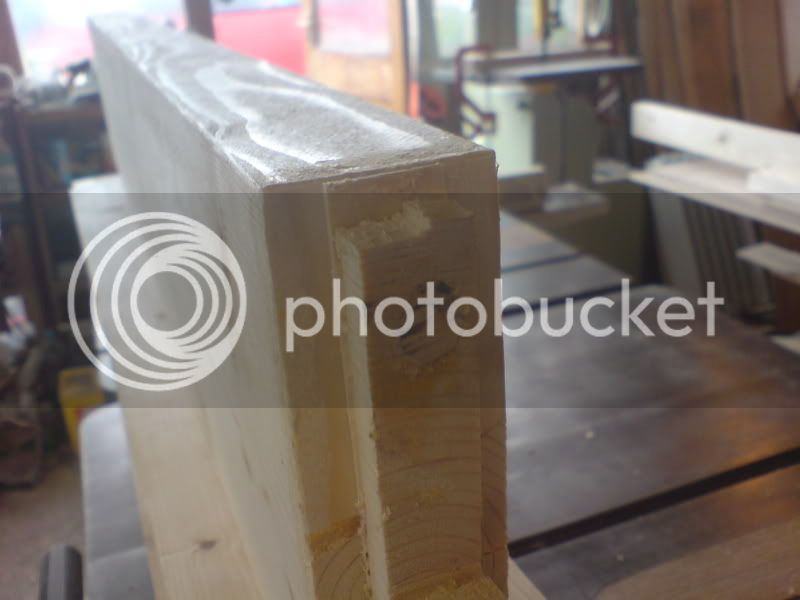
with a mortise gauge and a rod, I transfered the dimensions over to the styles.
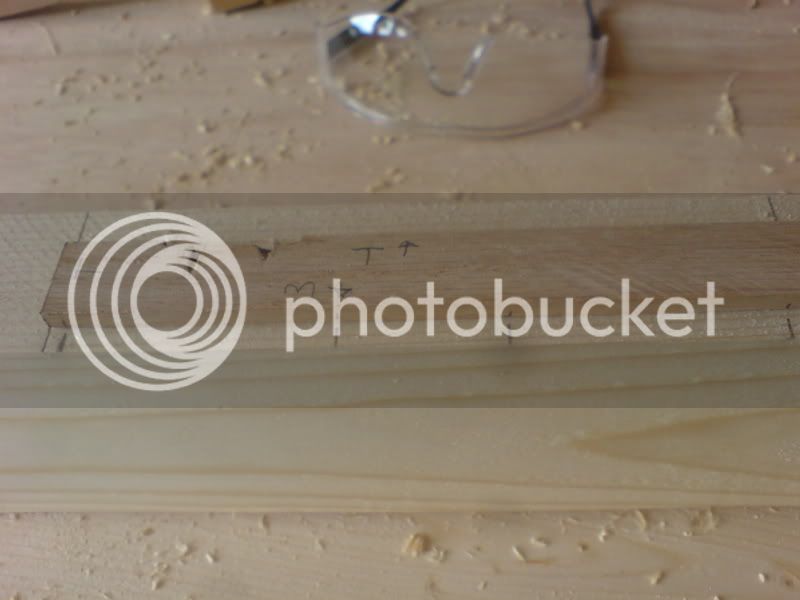
and cut the mortises
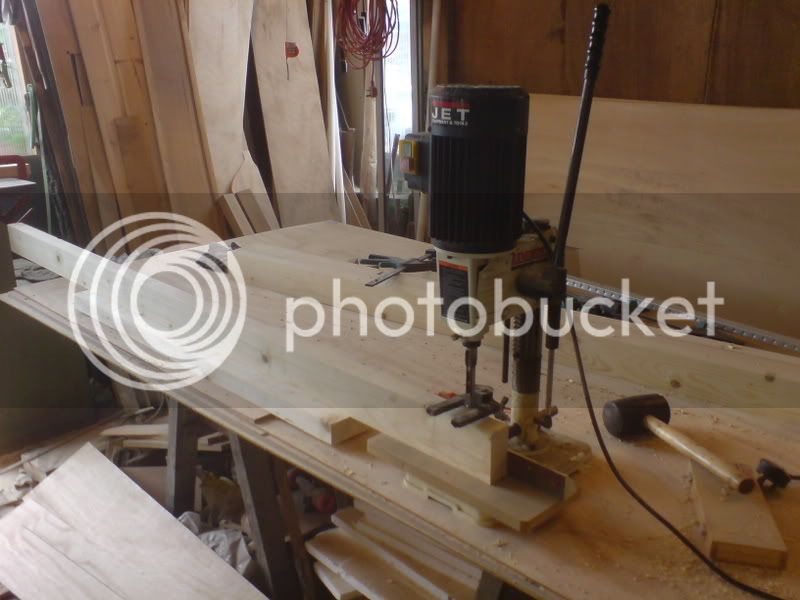
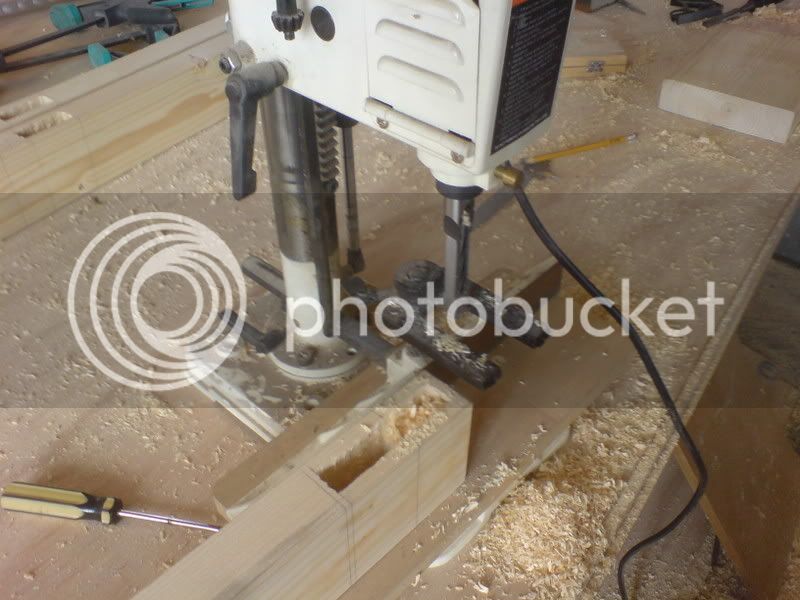
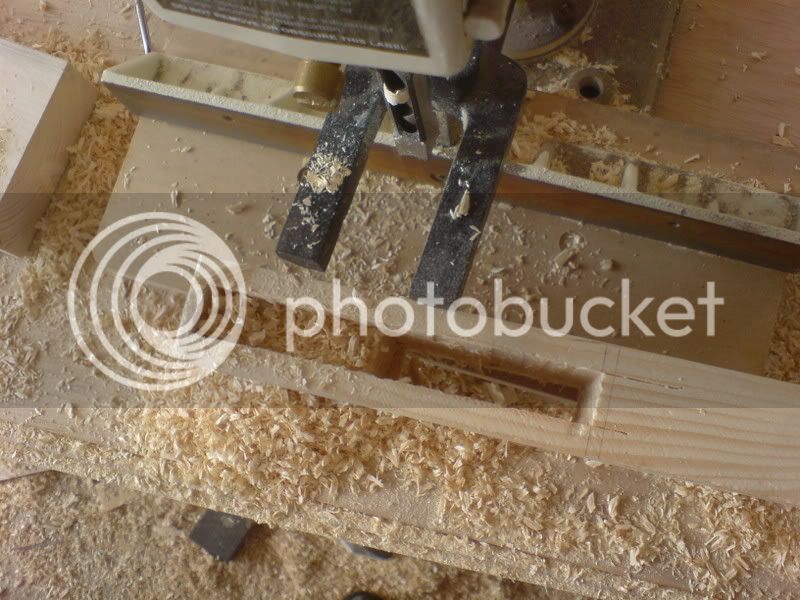
I cut the last bit out of the end with a chisel to keep it neat
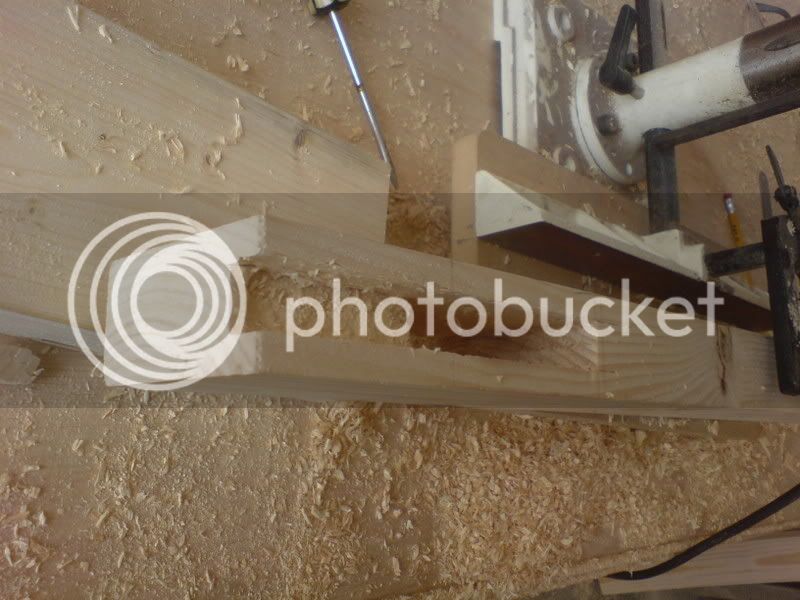
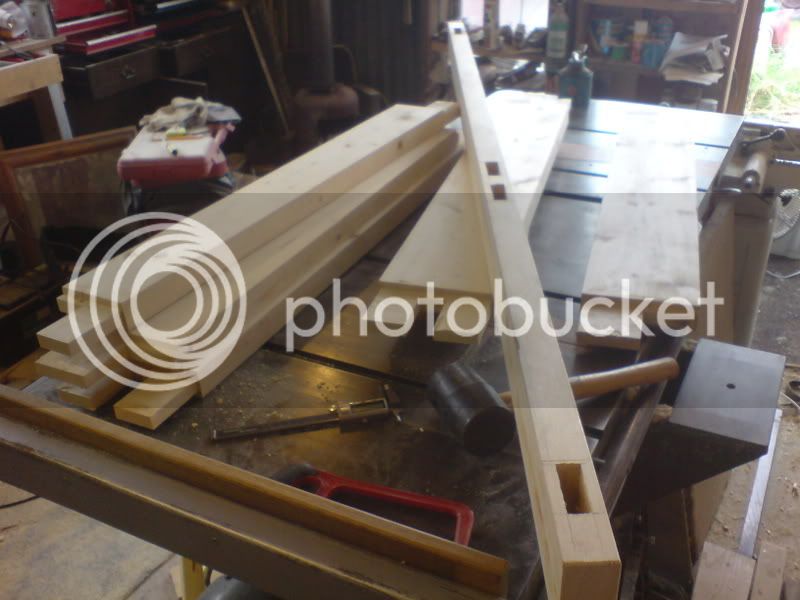
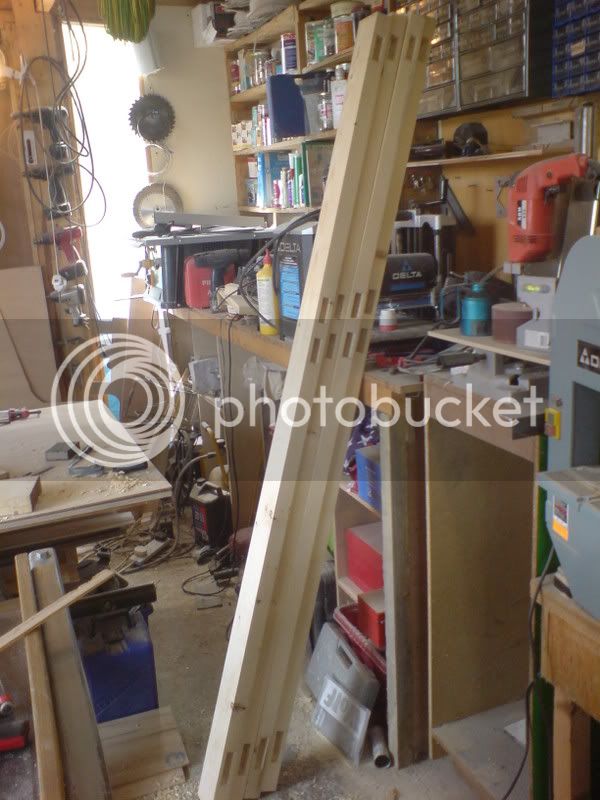
well that's all the joints done
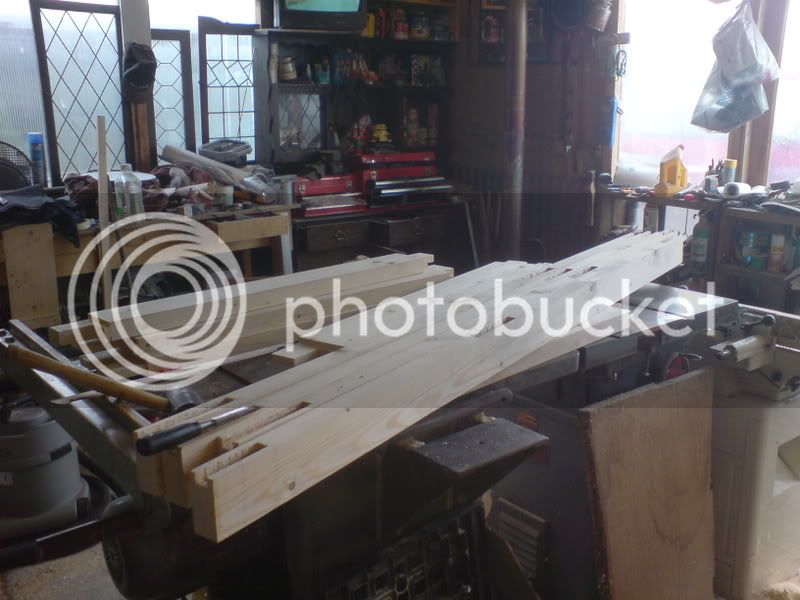
a touch up with a block plane and chisel before the dry fit
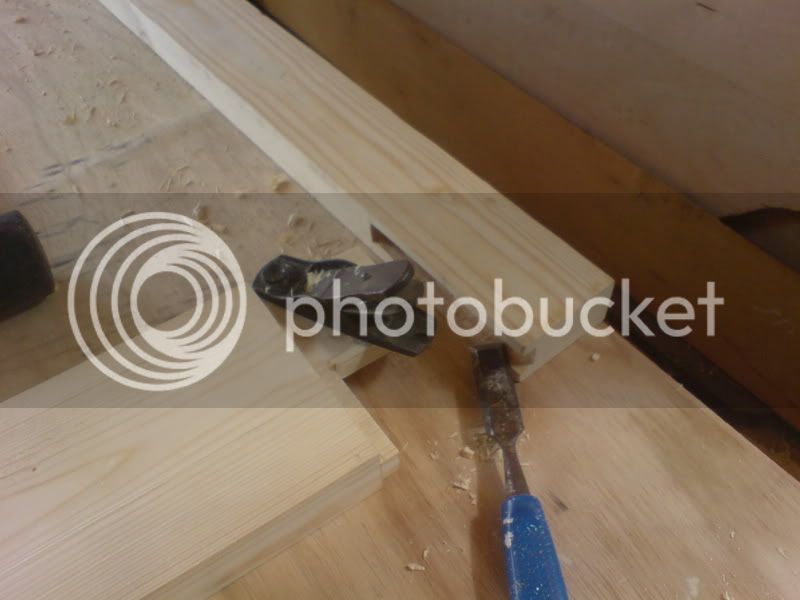
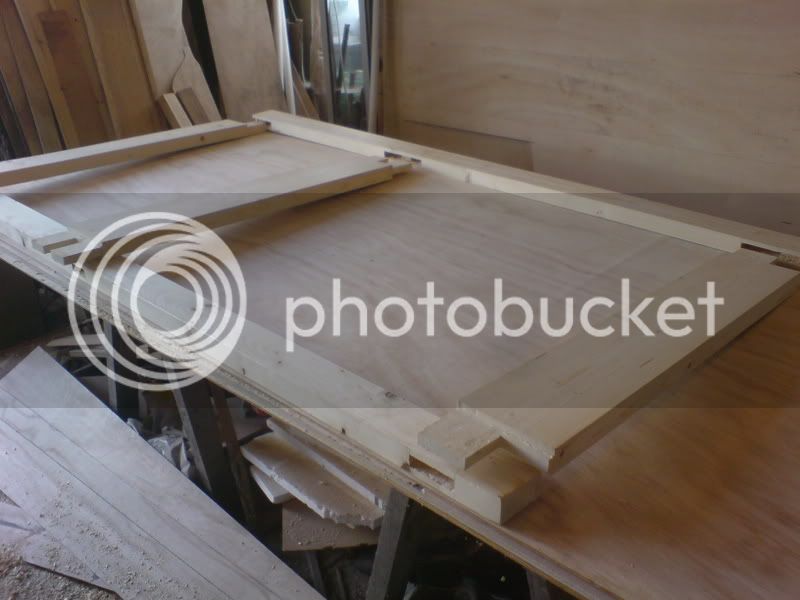
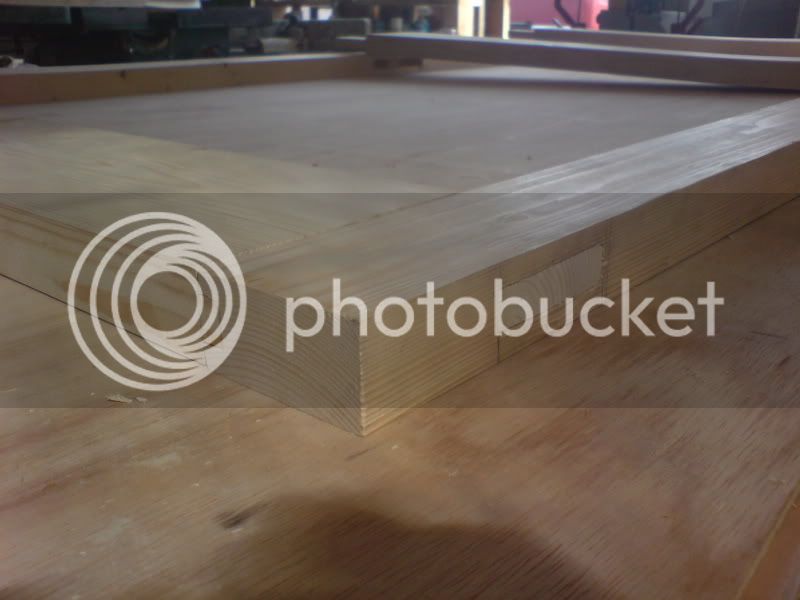
All ready for clue up . I'm using PU, so need to work fast !
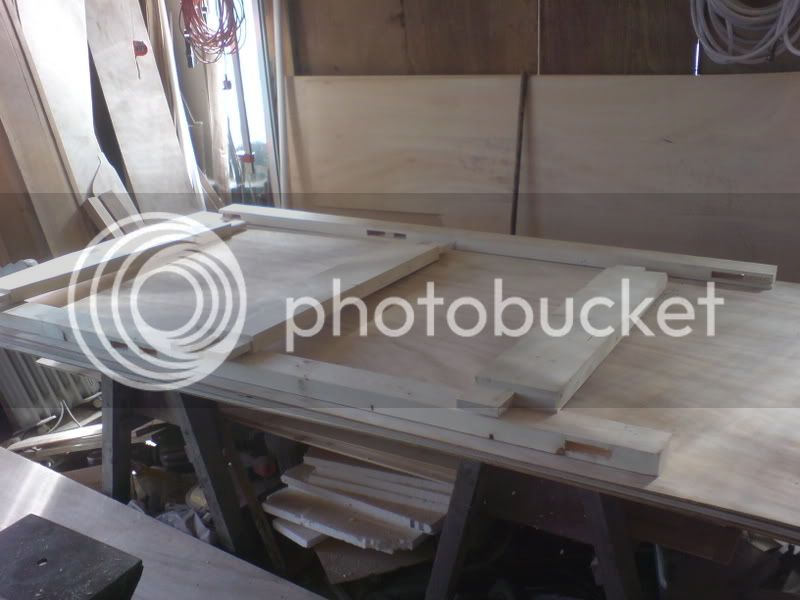
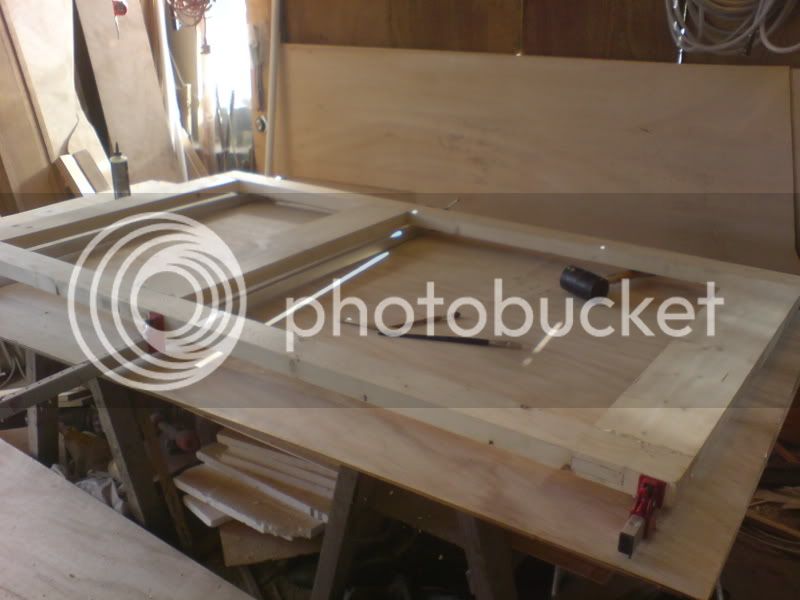
after the glue had set up, I routed out the rebates for the windows boards and panels
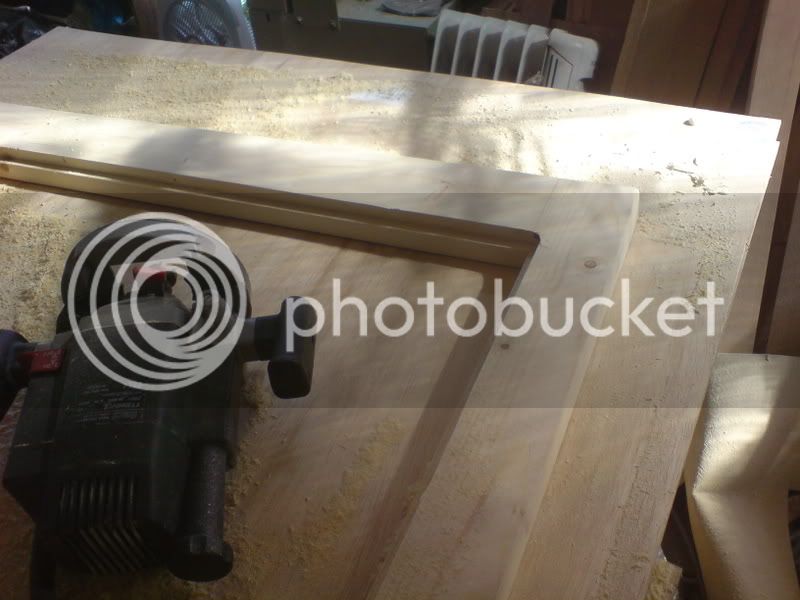
squaring up the window corners with a chisel
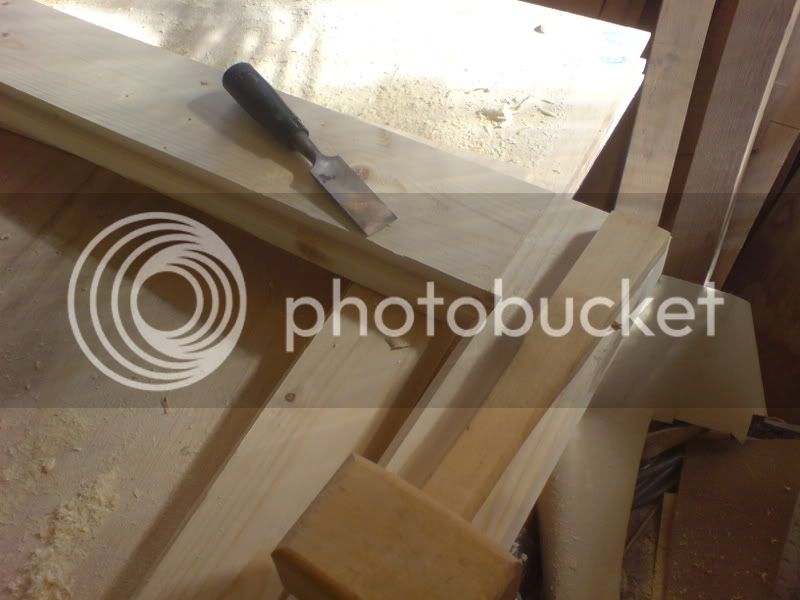
it started chucking down outside, so the dog decided to join me and Norm inside
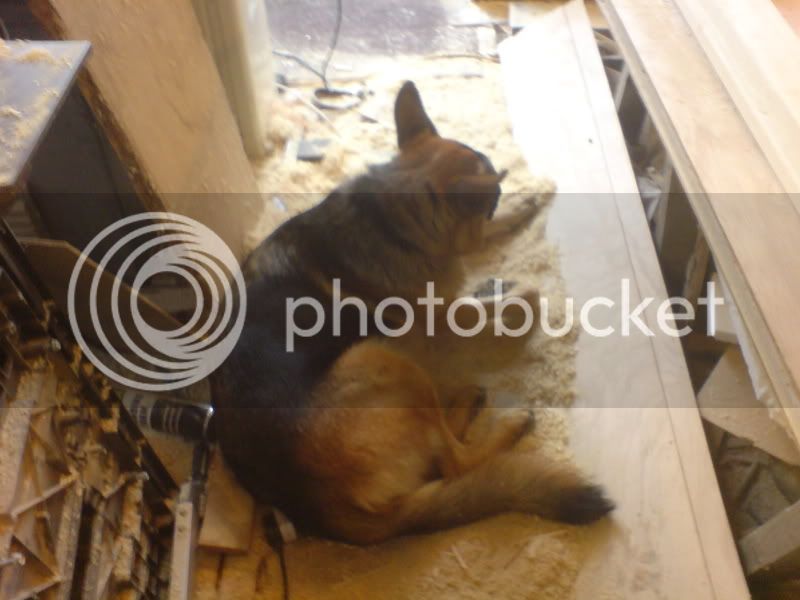
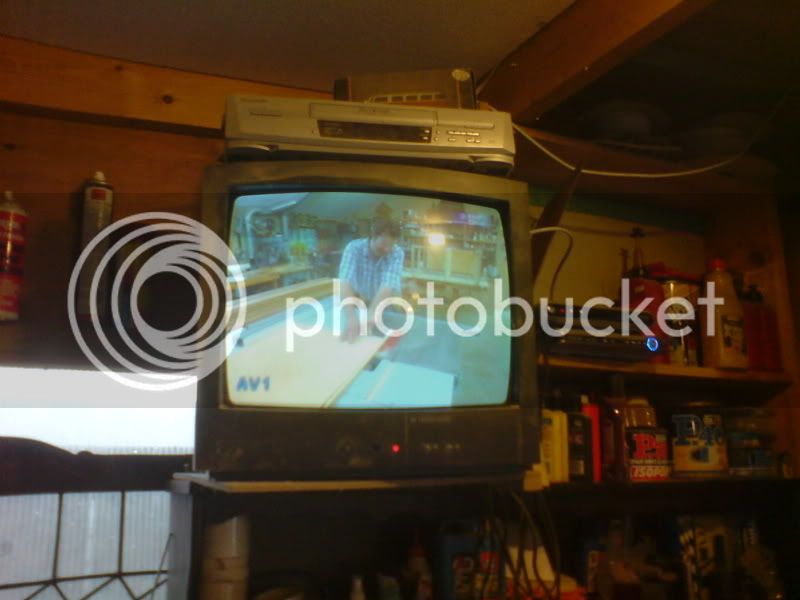
I rounded over the top and bottom ship lap boards and fitted them with a dab of PU and panels pins each. Leaving a gap at each lap for them to move.
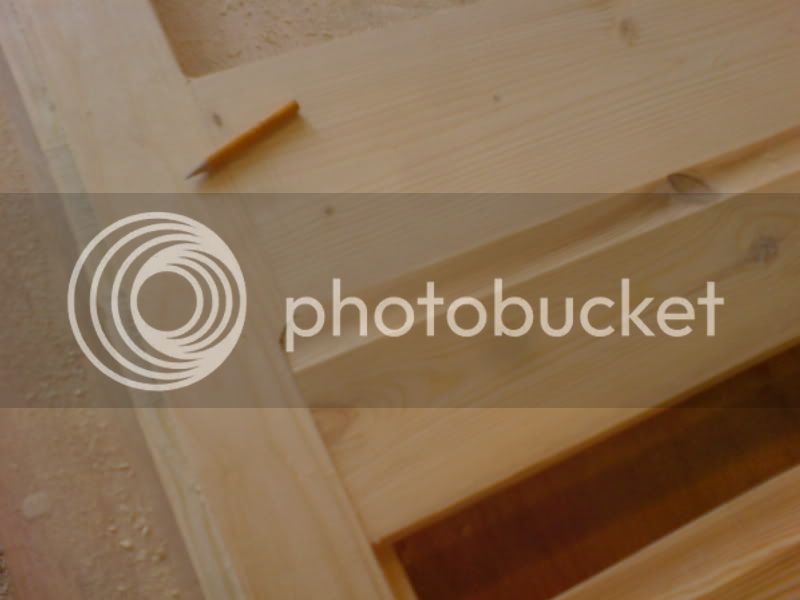
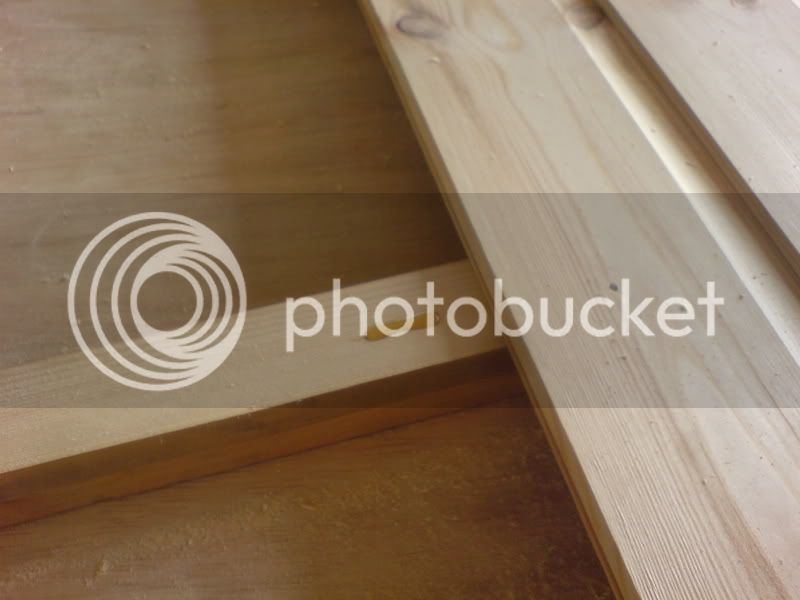
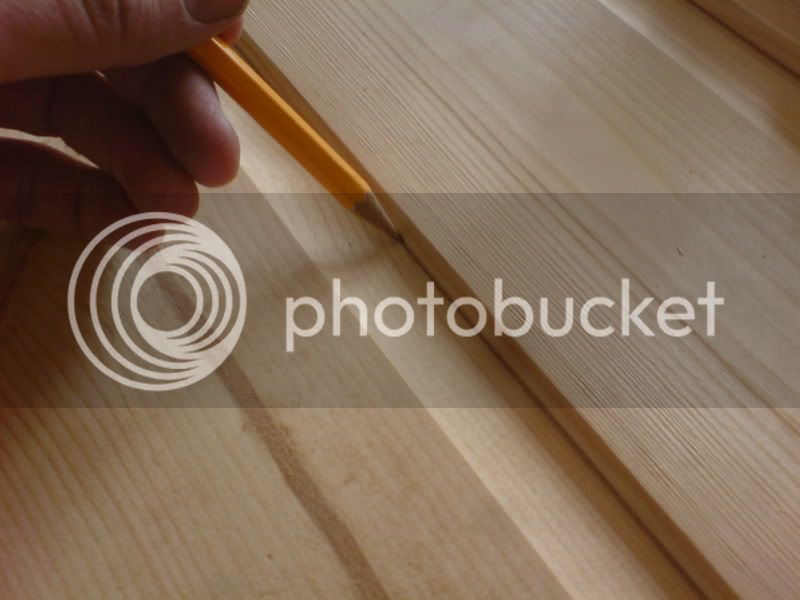
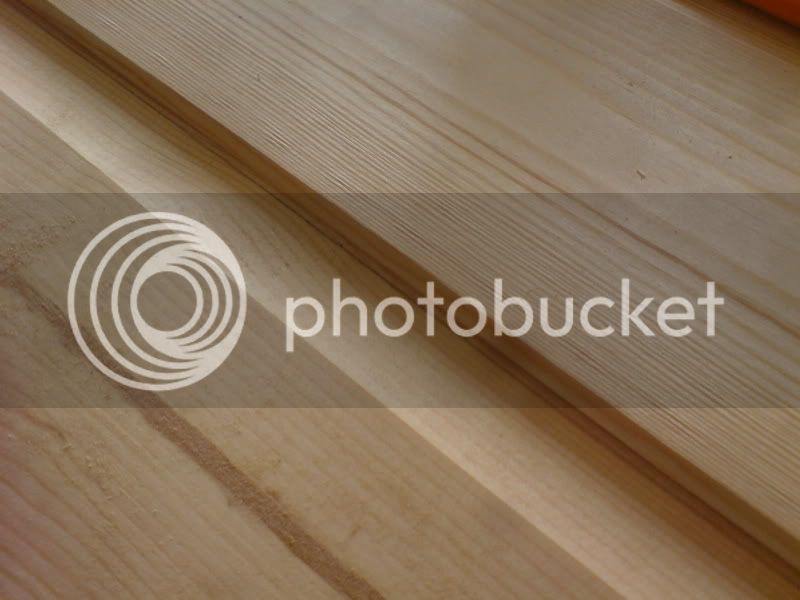
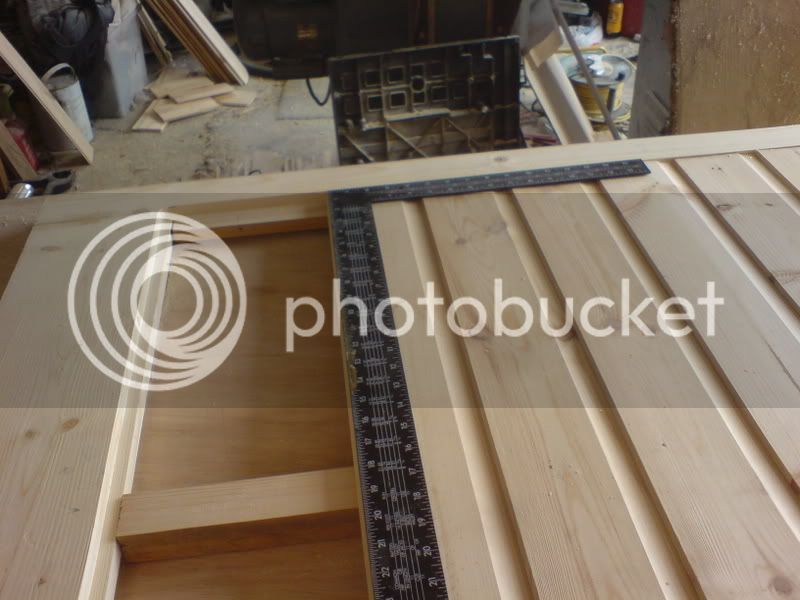
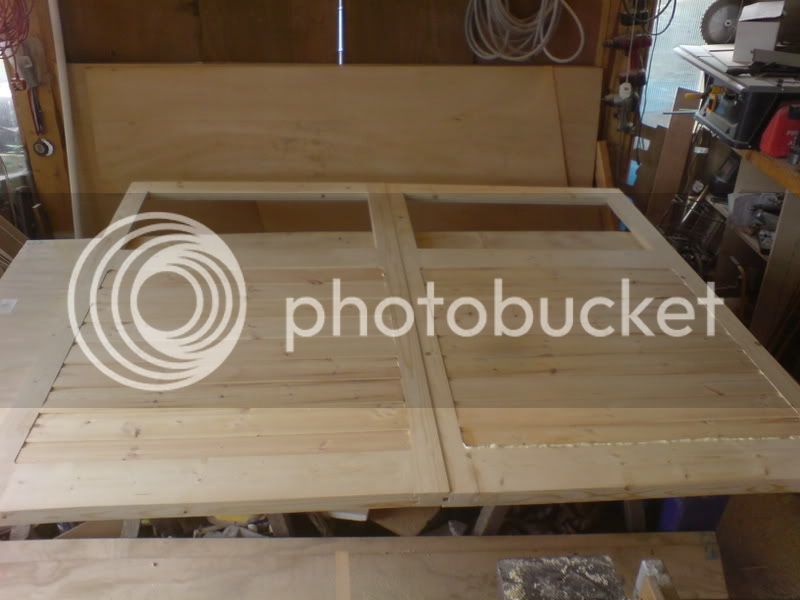
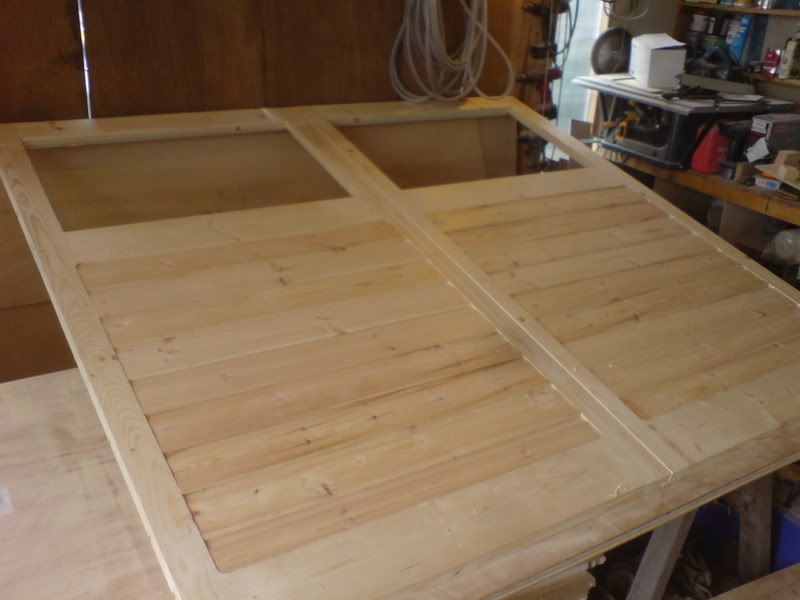
The inside of the door will have a ply panel PU'd in and to the middle baton, thus locking it all together front and back. I've left it off so I can treat and paint inside the cavity.
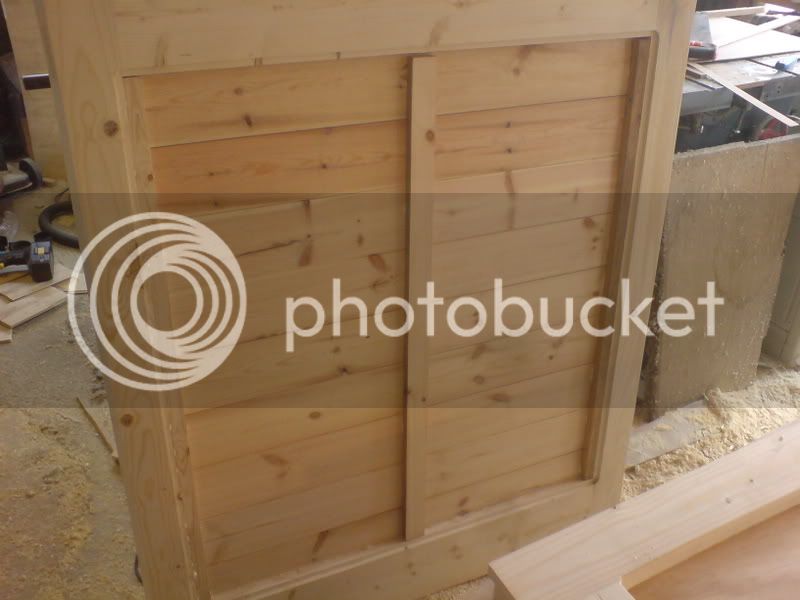
after some sanding, they are ready for the wood preservative . orrid stuff !
I dont take any risks with it.... door open with fan blowing clean air at my work area.... plenty of safety gear ... and when finished, straight inside for a shower and clothes in the washing machine. workshop cannot be entered again for 8 hrs !
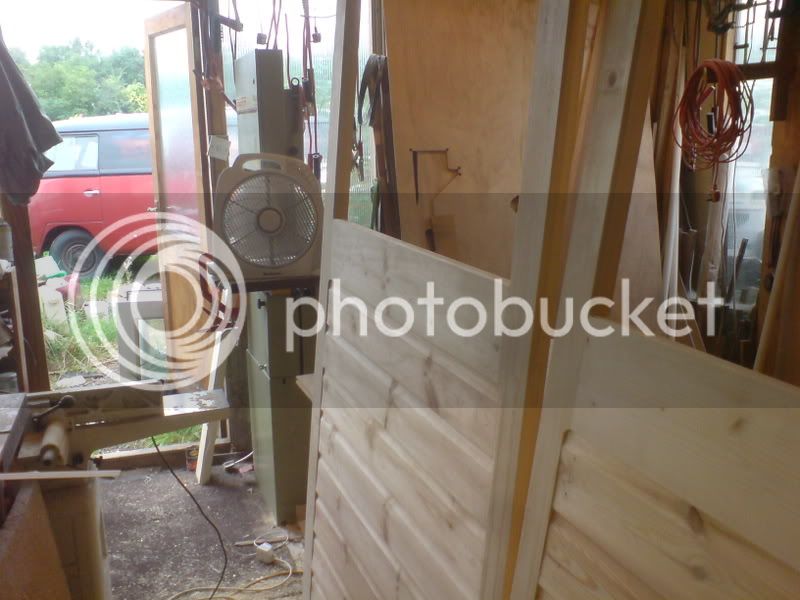
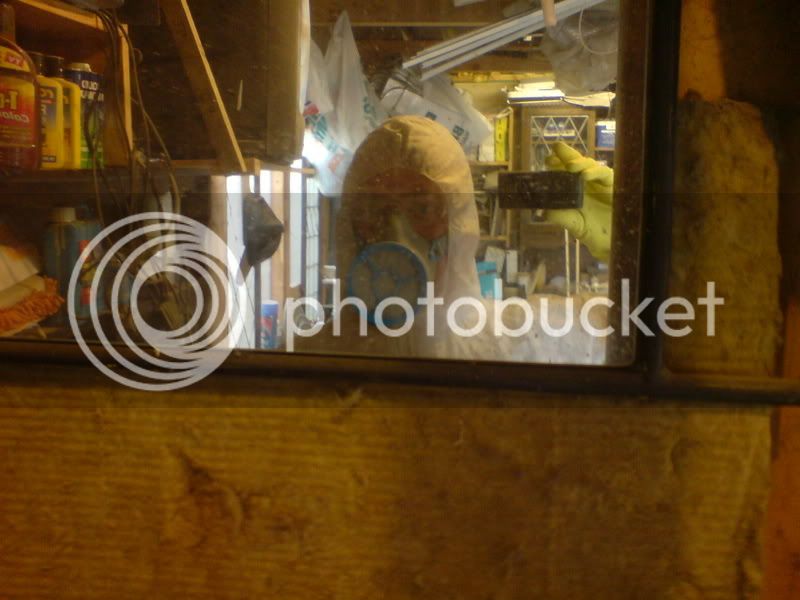
It does show up the joints well tho
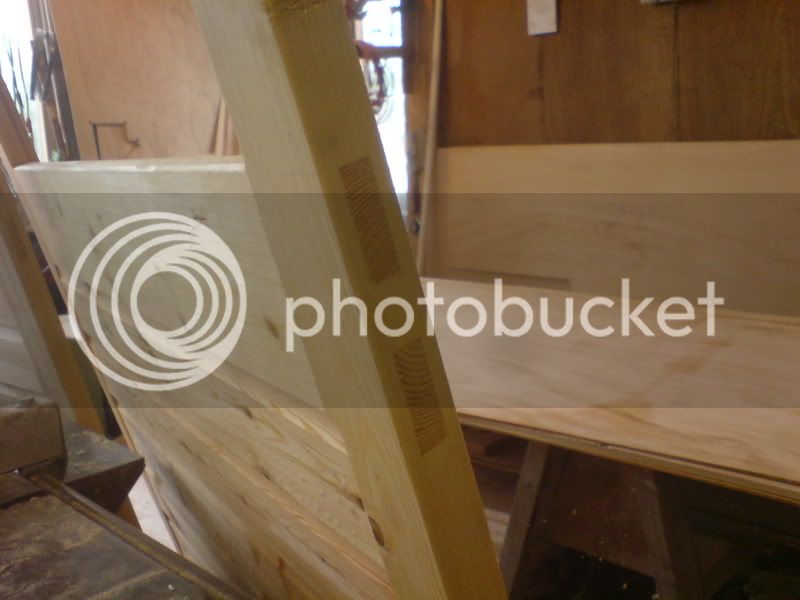
well thats it so far - the 8 hrs is just about up and I'm ka nak erred !
off to give them a coat of primer in a min before bed !
sorry for all the typo's at this late hour !