Well here it is.
The plan
Having read an article recently on making a small jewelery box with a coopered lid made from mahogany I hope to replicate it with dovetails included somewhere (I can't find the original article). My box will either be used for storing candles or tea, I haven't quite decided yet.
I was intending to build this box even before the competition cam up so I thought about it a bit and decided I didn't really want to see the joints so came up with a a mitered blind dovetail joint as a solution.
Just like this
The Inspiration
The look I want is something like this but with out the dark wood sides:
Combined with this:
This is the rough plan I'm working to. I haven't quite decided whether it will have trays but If I do they will be walnut.
The problem is I didn't quite have all the tools I needed so went on a miniature spending spree.
The plan
Having read an article recently on making a small jewelery box with a coopered lid made from mahogany I hope to replicate it with dovetails included somewhere (I can't find the original article). My box will either be used for storing candles or tea, I haven't quite decided yet.
I was intending to build this box even before the competition cam up so I thought about it a bit and decided I didn't really want to see the joints so came up with a a mitered blind dovetail joint as a solution.
Just like this
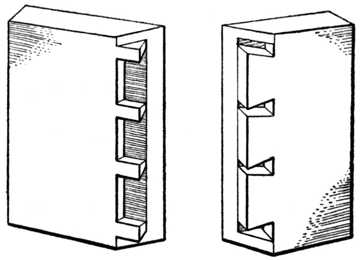
The Inspiration
The look I want is something like this but with out the dark wood sides:

Combined with this:

This is the rough plan I'm working to. I haven't quite decided whether it will have trays but If I do they will be walnut.
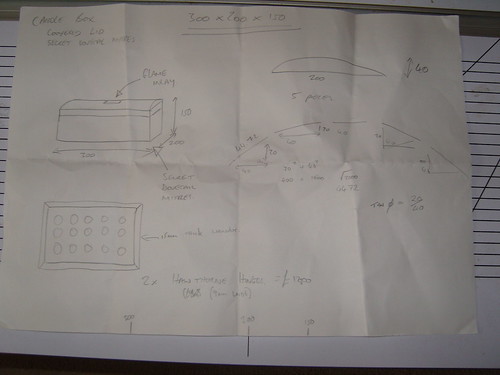
The problem is I didn't quite have all the tools I needed so went on a miniature spending spree.