tool613
Established Member
Merry Xmas boys hope ya got what you want from Santa.
with my time off until after new years i thought i would pull the head out of the Wadkin RM and work the cutter block.
There was a stud and plate bolt missing in the head and i did not like the looks of the others. The thing that got me the most was I needed a 48"cheater pipe to brake the nut free of the head,so they were way to tight.
there is an old saying about moulding knife bolts::::
if you turn nut over and it wont thread on the threads are stretched. Most are that way and so here is were i need help.
the forged steel plate type cutterblock is really a great head with its skewed knifes and is also able to take moulding knifes. I did get the tool(spanner) for the head bolts that has short handle ,so i would think 60 to 100lbs is all that is need on the nuts.
any care to comment?
question
is there a source for the studs and nuts, and what is the grade of metal/thread etc?
the ones in there now appear to be mild steel.
The plates are tapered and so the studs lengths are long on one side and get shorter as you go across.
any old wadkin x staff around that can enlighten on how the head was balanced?
I hope this to be a discussion on the old plate type cutterblock and do not want it to turn into the safety of these old heads. I restore old wadkin kit and use it .
some pics
here is the block with the missing bolt as i got the machine
these nut does not look wadkin
this is a Wadkin nut with the rounded top.
the spanner
wadkin RM 26" over under
head removal
nice bearing on this one
2 RM 12 self aliening double rowed brass cage on the drive side with a 2308 SKF to the out board
hand scraped bearing retainer cap.
the head capless
jack
with my time off until after new years i thought i would pull the head out of the Wadkin RM and work the cutter block.
There was a stud and plate bolt missing in the head and i did not like the looks of the others. The thing that got me the most was I needed a 48"cheater pipe to brake the nut free of the head,so they were way to tight.
there is an old saying about moulding knife bolts::::
if you turn nut over and it wont thread on the threads are stretched. Most are that way and so here is were i need help.
the forged steel plate type cutterblock is really a great head with its skewed knifes and is also able to take moulding knifes. I did get the tool(spanner) for the head bolts that has short handle ,so i would think 60 to 100lbs is all that is need on the nuts.
any care to comment?
question
is there a source for the studs and nuts, and what is the grade of metal/thread etc?
the ones in there now appear to be mild steel.
The plates are tapered and so the studs lengths are long on one side and get shorter as you go across.
any old wadkin x staff around that can enlighten on how the head was balanced?
I hope this to be a discussion on the old plate type cutterblock and do not want it to turn into the safety of these old heads. I restore old wadkin kit and use it .
some pics
here is the block with the missing bolt as i got the machine
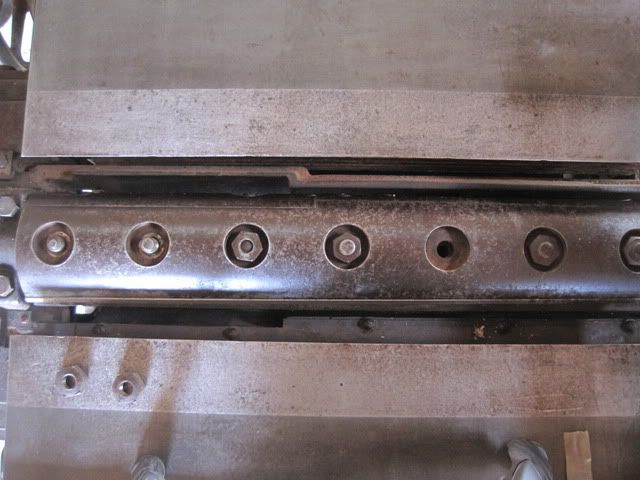
these nut does not look wadkin
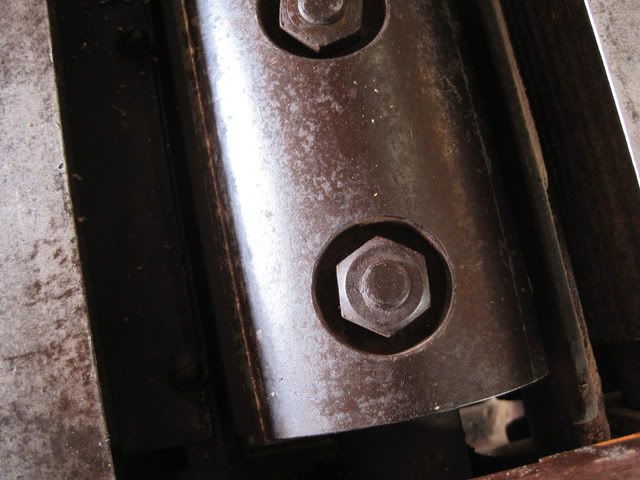
this is a Wadkin nut with the rounded top.
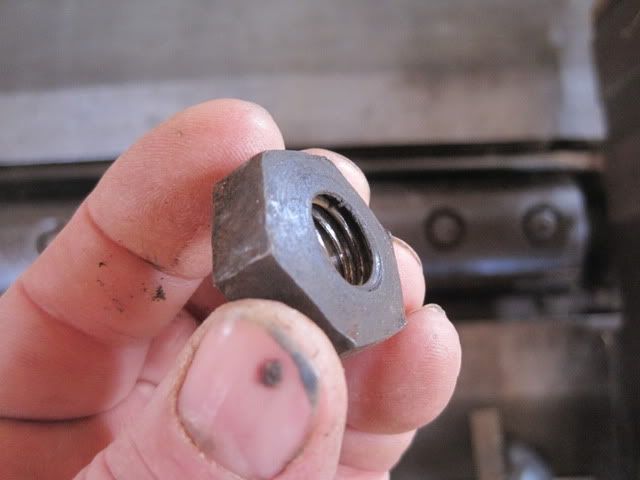
the spanner
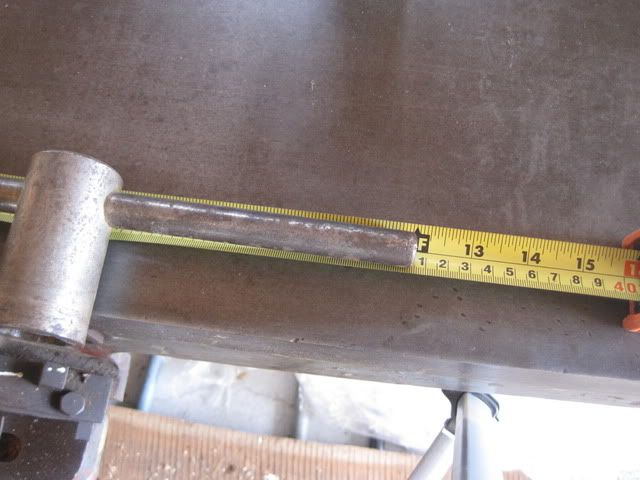
wadkin RM 26" over under
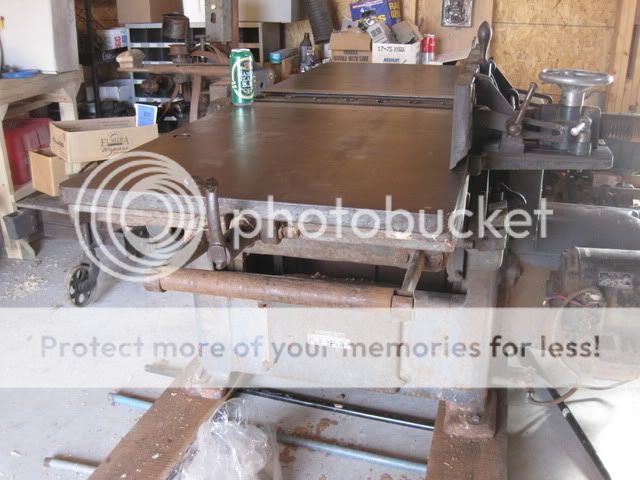
head removal
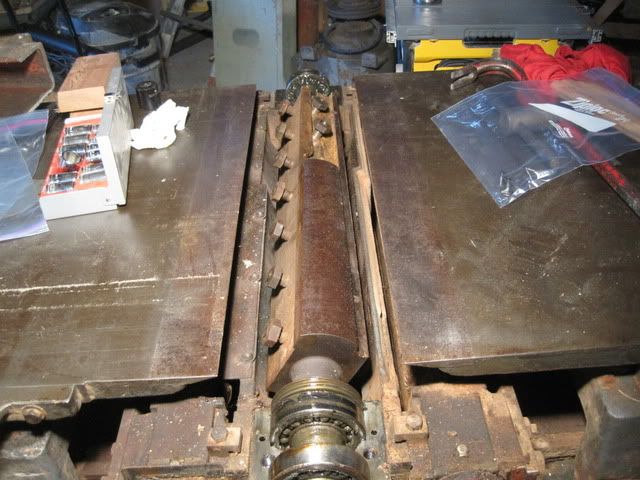

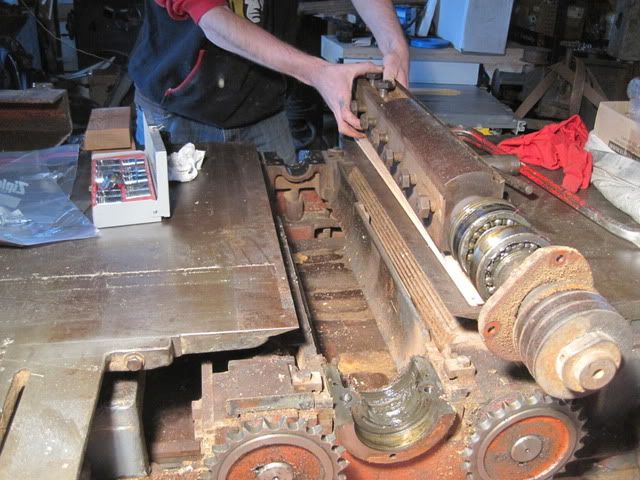
nice bearing on this one
2 RM 12 self aliening double rowed brass cage on the drive side with a 2308 SKF to the out board
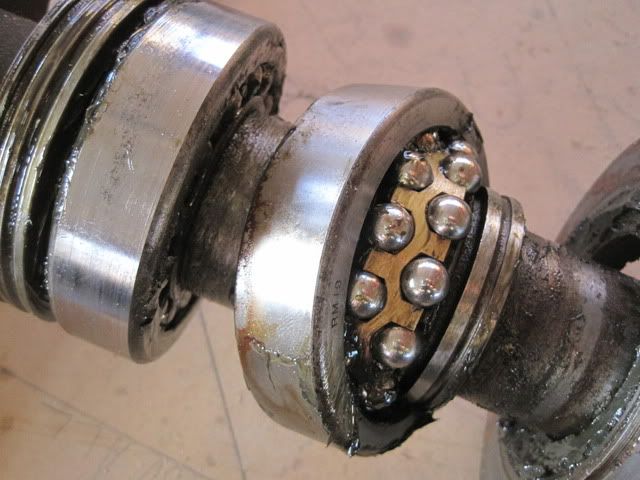
hand scraped bearing retainer cap.
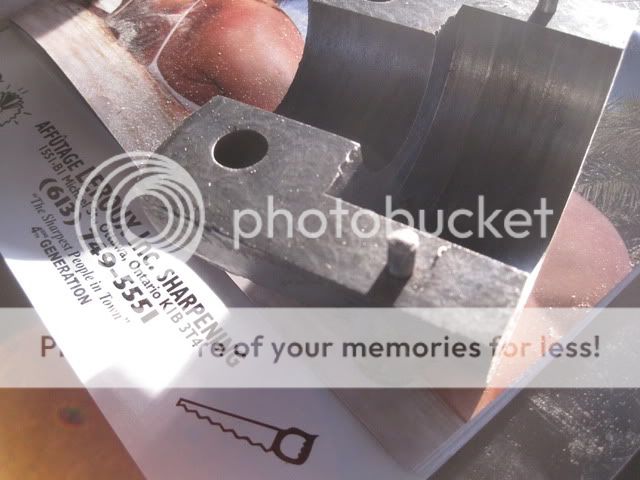
the head capless
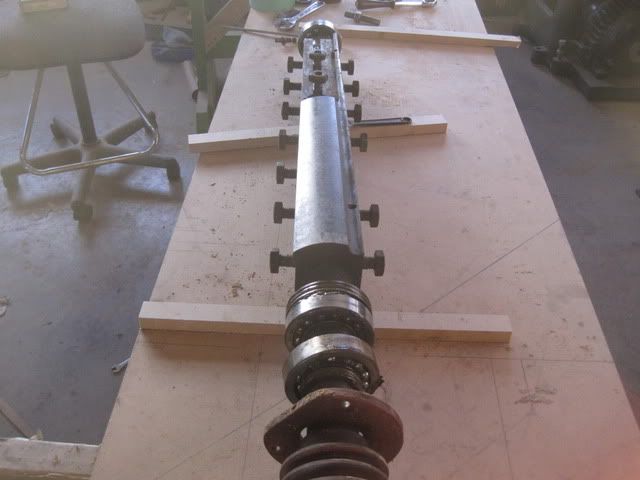
jack