sploo
Somewhat extinguished member
A few months ago I got a decent deal on an old Warco Mini Mill (one of the many SIEG SX2 clones). I say it was a decent deal... but on firing it up, the motor emitted plumes of smoke, and the machine itself made some fairly horrific noises. I'd planned to strip it down anyway, so...
First the motor was removed, and the head taken off the vertical column:
Looking inside the head it was clear the internal gearing was basically trash (apparently a common problem with this design):
I stripped more of the head:
And the gears at the top looked ok:
The motor was dismantled, and it turns out that a problem with the brush holders meant they'd damaged the commutator (smearing the metal and creating shorts). Fortunately I was able to clean it up:
Having looked into replacement gears I decided it would be better to attempt a belt drive conversion, so the shaft carrying the change gear had to be removed:
Finally, the spindle itself was pressed out:
And the last of the bearings removed:
Here you can see the spring loaded arm that balances the weight of the (now stripped) head. They're apparently not particularly even in the force they produce, so I planned to remove it and add a gas strut instead:
Many more images coming soon...
First the motor was removed, and the head taken off the vertical column:
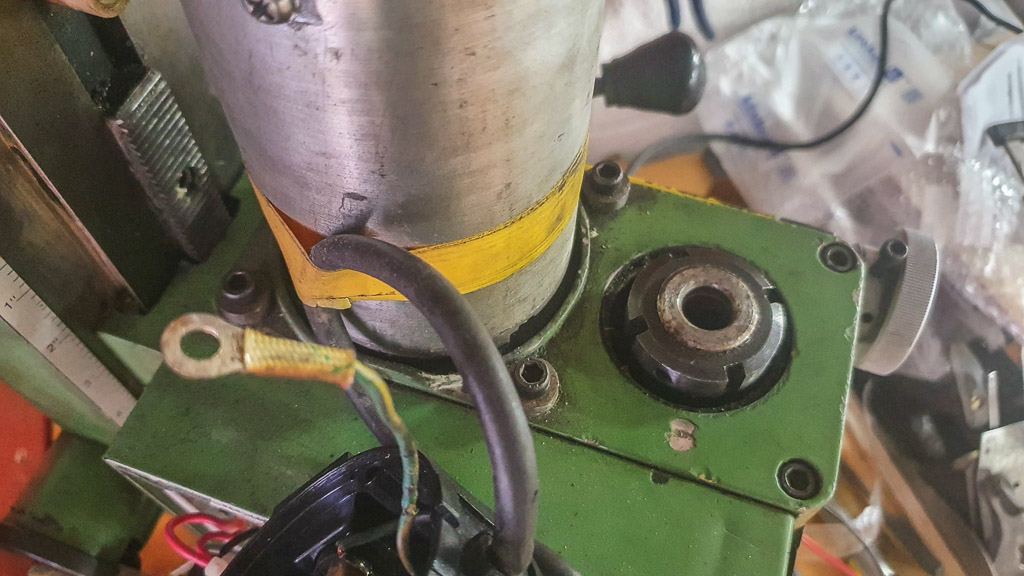
Looking inside the head it was clear the internal gearing was basically trash (apparently a common problem with this design):
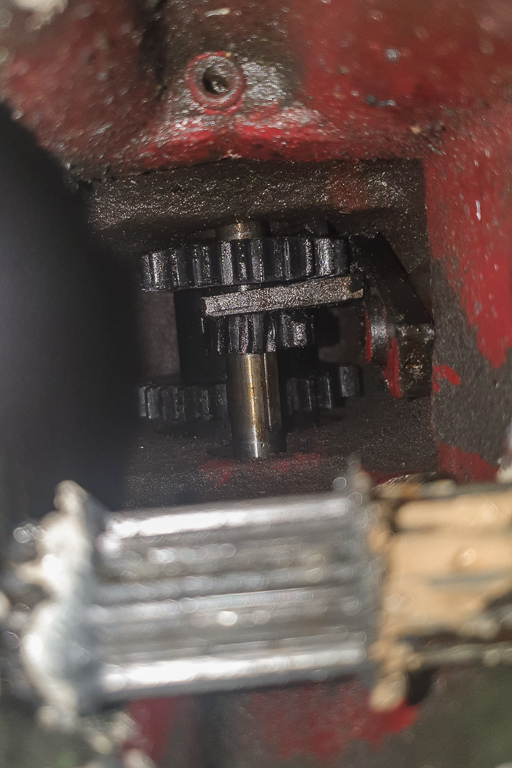
I stripped more of the head:
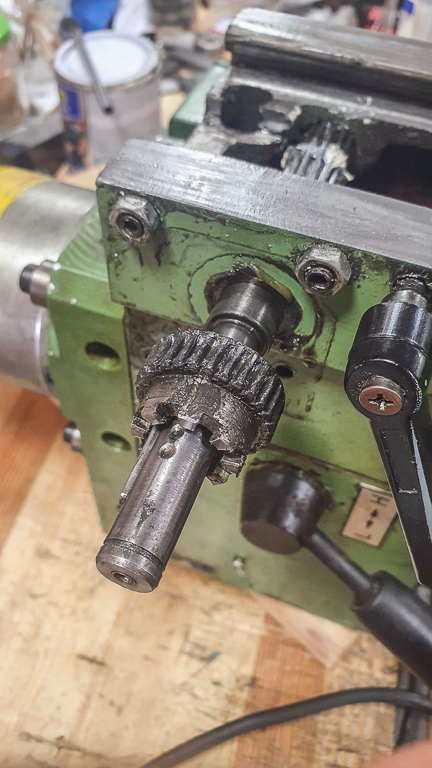
And the gears at the top looked ok:
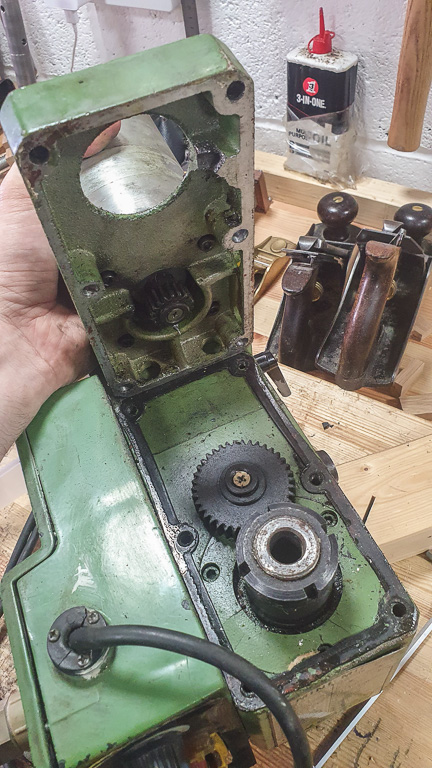
The motor was dismantled, and it turns out that a problem with the brush holders meant they'd damaged the commutator (smearing the metal and creating shorts). Fortunately I was able to clean it up:
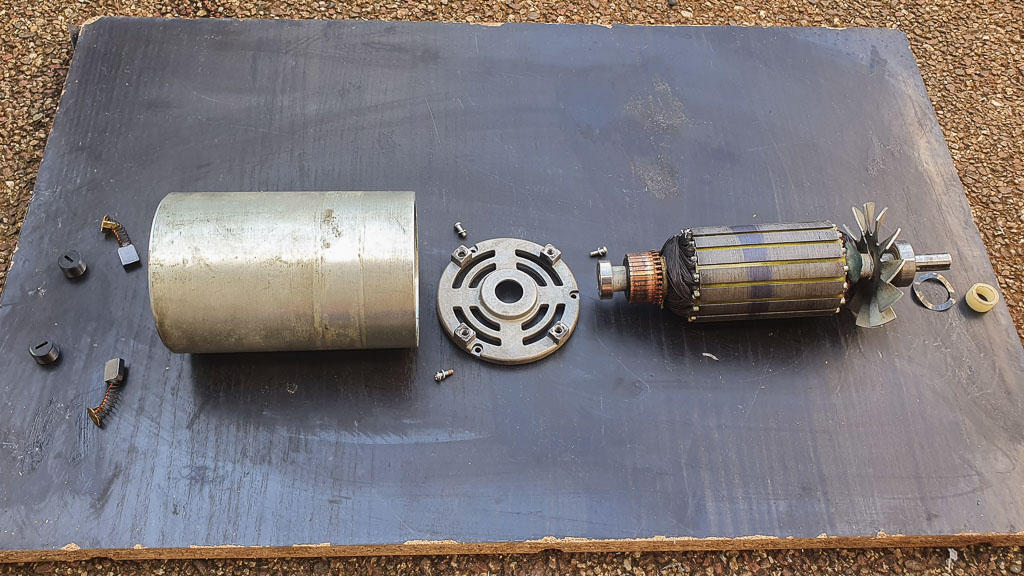
Having looked into replacement gears I decided it would be better to attempt a belt drive conversion, so the shaft carrying the change gear had to be removed:
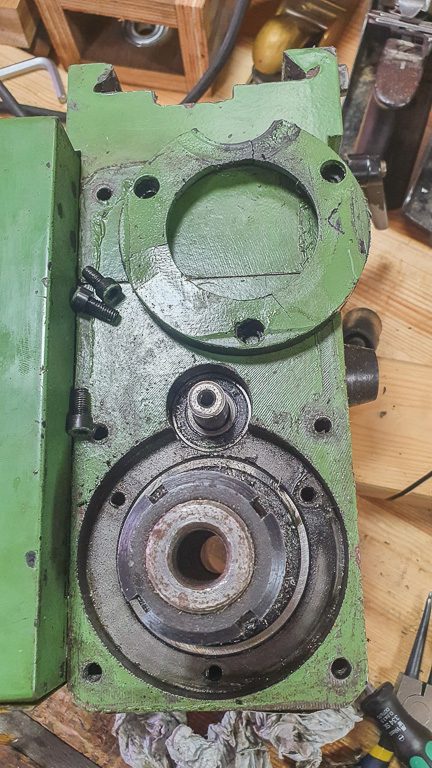
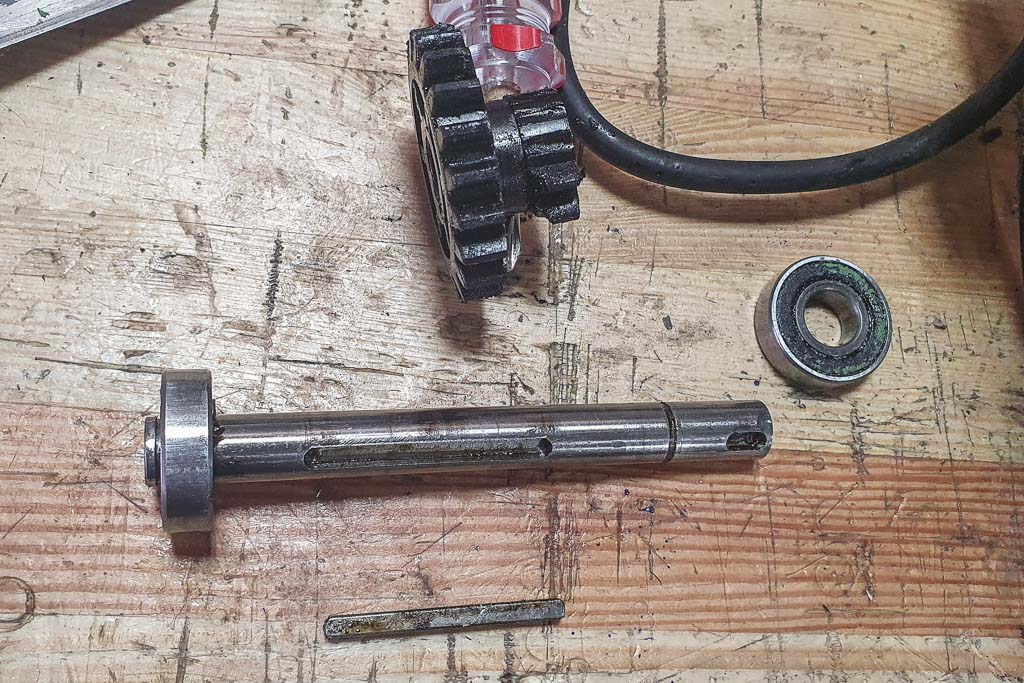
Finally, the spindle itself was pressed out:
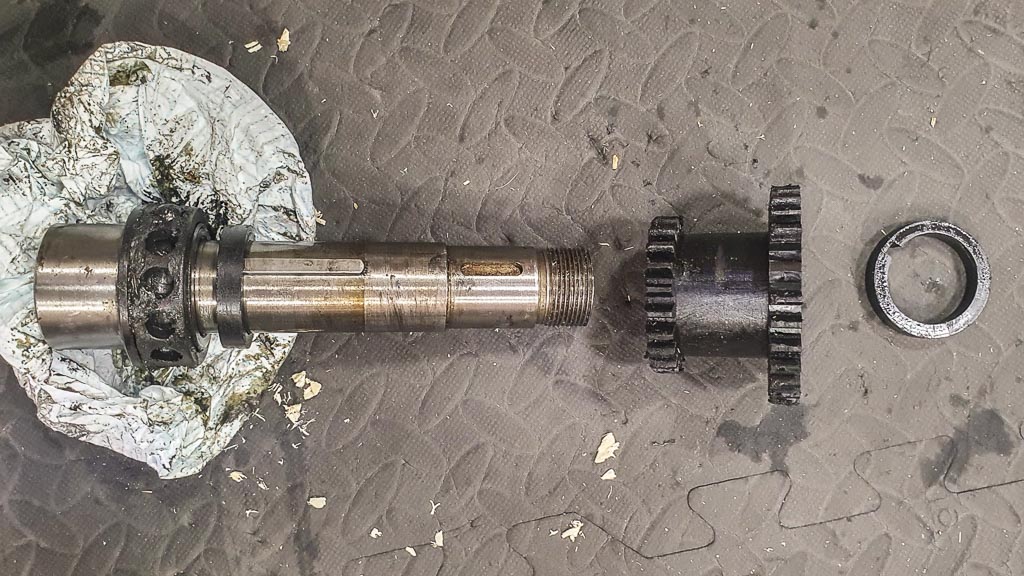
And the last of the bearings removed:
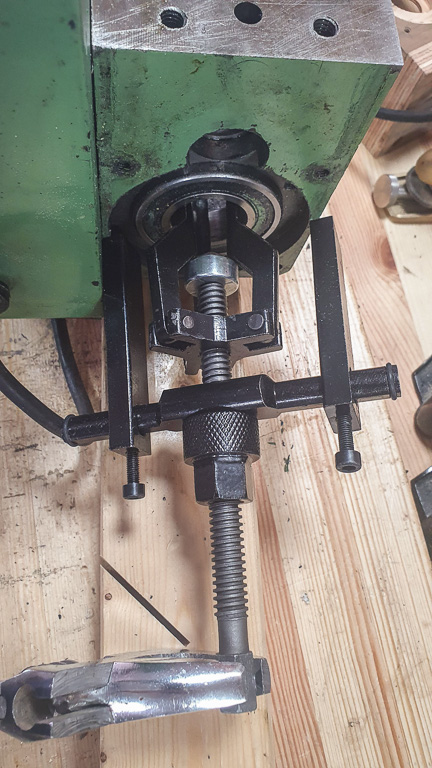
Here you can see the spring loaded arm that balances the weight of the (now stripped) head. They're apparently not particularly even in the force they produce, so I planned to remove it and add a gas strut instead:
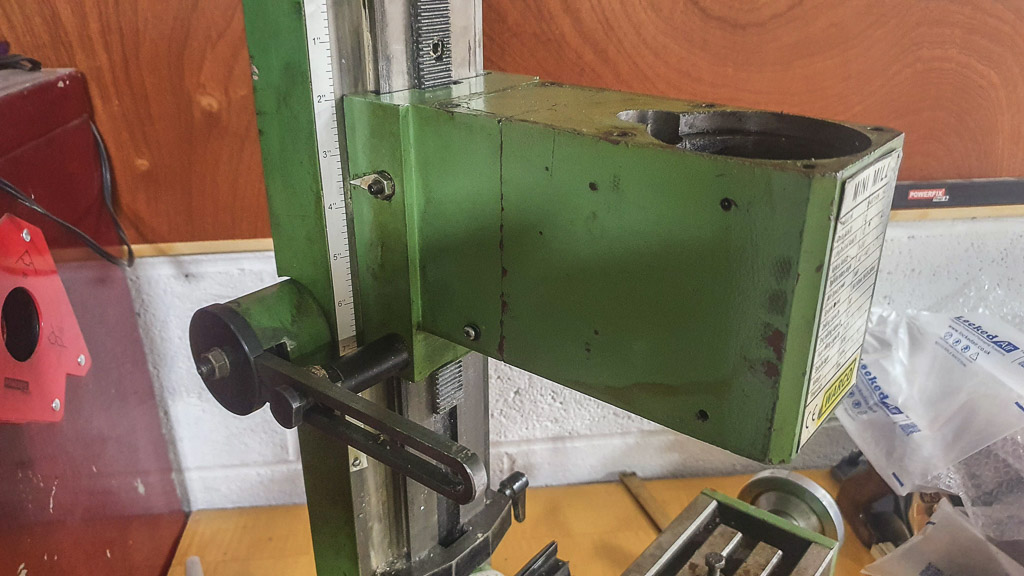
Many more images coming soon...