Hi. More daft questions!
I recently bought a Record Power 8" dry Grinder from another forum member who was selling a fair amount of nice tools due to a mountain biking injury. It's the one with the 40mm white wheel.
Included in the (fair) price was a Veritas jig and a dressing stone for the grey wheel.
I'm in the middle of a self imposed few month long shed ban while I complete a loft extension so it's sat down the shed for a few weeks all on it's lonesome.
I took a look at it the other day and realised the jig was missing the angle setter. Did a bit of research and found it seemed to be held in fairly low regard anyway perhaps unusually for Veritas gear.
Its the separate bit in the photo here:
I gave the fella a bell and he said he thinks he might know where it is but I've not heard back. Some older threads I looked at concerning the veritas jig mostly suggested the Tormek angle setting jig is far superior anyway.
I hedged my bets, bit my tongue and got it from axminster.
https://www.axminster.co.uk/tormek-wm-2 ... ter-368028
Clever bit of kit I suppose but bit lumpy for a bit of plastic maybe.
I know there's methods of establishing angles/bevels etc without using such stuff but I get so little time I'd rather spend it actually working on something I find enjoyable. Maths is not really my strong point.
Being a bank holiday Sunday I thought I'd take a break from DIWhydideverstartthispoxyextension before I went full blown Ives
and take a veeeeeery casual early morning walk down the shed with a coffee in my hand and a ciggy in my gob, casually dispersing trouserfuls of dirt, timing the patrols of the Kommandant and her two little Goons ( :| ) . Maybe sort the grinder out and get a few irons sorted so they are ready and waiting, knock a few German Civilian Wartime sets of Papers out... Sort through the wood store.... You know the score.
Soon as I'd dodged the searchlights, bribed the guards with some Red Cross Ciggies and made it to the shed I saw my mistake.
The tormek guide won't fit on the wheel with the guards in place. Not the German ones but the Record ones. Can I safely remove the side panels so the jig will fit on the wheel?
I need to alter/hacksaw the jig so I can use it on the white wheel anyway. I'm happy to play about with it within reason but I'd rather ask wise heads before I start messing about in case there is summat I have missed. Fairly certain I'm ok to remove them but I'd like to be sure.
Cheers chaps. Any advice or help appreciated as always.
Just don't say good luck for Christ Sake. :shock:
Thanks as always,
Chris
I recently bought a Record Power 8" dry Grinder from another forum member who was selling a fair amount of nice tools due to a mountain biking injury. It's the one with the 40mm white wheel.
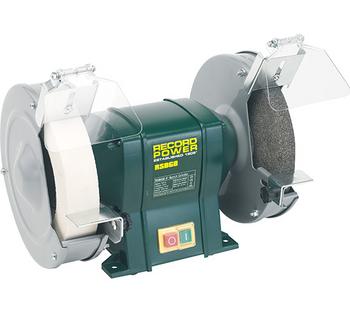
Included in the (fair) price was a Veritas jig and a dressing stone for the grey wheel.
I'm in the middle of a self imposed few month long shed ban while I complete a loft extension so it's sat down the shed for a few weeks all on it's lonesome.
I took a look at it the other day and realised the jig was missing the angle setter. Did a bit of research and found it seemed to be held in fairly low regard anyway perhaps unusually for Veritas gear.
Its the separate bit in the photo here:
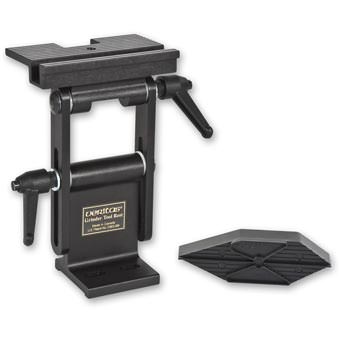
I gave the fella a bell and he said he thinks he might know where it is but I've not heard back. Some older threads I looked at concerning the veritas jig mostly suggested the Tormek angle setting jig is far superior anyway.
I hedged my bets, bit my tongue and got it from axminster.
https://www.axminster.co.uk/tormek-wm-2 ... ter-368028
Clever bit of kit I suppose but bit lumpy for a bit of plastic maybe.
I know there's methods of establishing angles/bevels etc without using such stuff but I get so little time I'd rather spend it actually working on something I find enjoyable. Maths is not really my strong point.
Being a bank holiday Sunday I thought I'd take a break from DIWhydideverstartthispoxyextension before I went full blown Ives
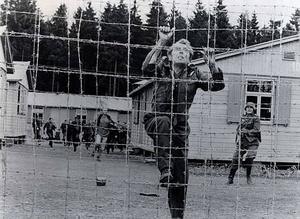
and take a veeeeeery casual early morning walk down the shed with a coffee in my hand and a ciggy in my gob, casually dispersing trouserfuls of dirt, timing the patrols of the Kommandant and her two little Goons ( :| ) . Maybe sort the grinder out and get a few irons sorted so they are ready and waiting, knock a few German Civilian Wartime sets of Papers out... Sort through the wood store.... You know the score.
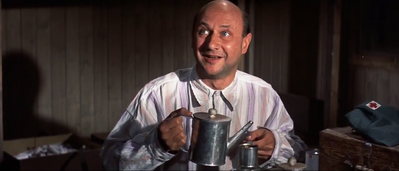
Soon as I'd dodged the searchlights, bribed the guards with some Red Cross Ciggies and made it to the shed I saw my mistake.
The tormek guide won't fit on the wheel with the guards in place. Not the German ones but the Record ones. Can I safely remove the side panels so the jig will fit on the wheel?
I need to alter/hacksaw the jig so I can use it on the white wheel anyway. I'm happy to play about with it within reason but I'd rather ask wise heads before I start messing about in case there is summat I have missed. Fairly certain I'm ok to remove them but I'd like to be sure.
Cheers chaps. Any advice or help appreciated as always.
Just don't say good luck for Christ Sake. :shock:
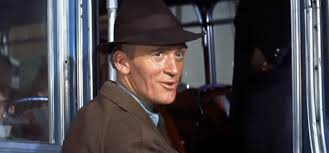
Thanks as always,
Chris