RobertMP
Established Member
Should have a mitre gauge with luck. Seller seems diabolical with emails but i phoned and agreed to send them some postage money by paypal so they could send the mitre gauge on to me. So if they ever check their emails for paypal it should turn up next week some time.
Still playing with the design....
It occurred to me that the bench will be along a wall most of the time and would need pulling out to use it - which is fine for sawing but seems more effort than need be when doing a small routing job.
On my current B+Q el cheapo router table I threw the plastic fence away and just clamp a batten across as a fence..... so I've changed the table top edges to have overhangs suitable for clamping to - which would mean i could clamp a fence 90deg to the one in the drawing and run the workpiece along the bench instead of across it if that makes sense
I've 'hidden' the nearest aluminium extrusion saw fence mounting rail to make it clearer..
Still playing with the design....
It occurred to me that the bench will be along a wall most of the time and would need pulling out to use it - which is fine for sawing but seems more effort than need be when doing a small routing job.
On my current B+Q el cheapo router table I threw the plastic fence away and just clamp a batten across as a fence..... so I've changed the table top edges to have overhangs suitable for clamping to - which would mean i could clamp a fence 90deg to the one in the drawing and run the workpiece along the bench instead of across it if that makes sense
I've 'hidden' the nearest aluminium extrusion saw fence mounting rail to make it clearer..
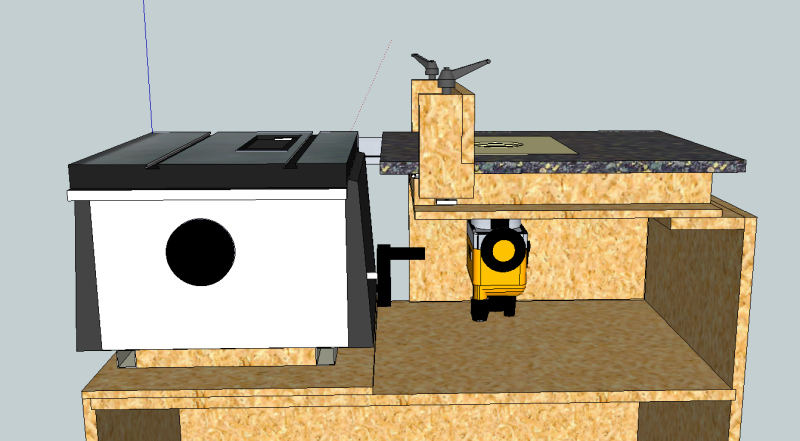