Mikey R
Established Member
Hi,
Ive recently moved into my new house, so Ive finally got my dedicated workshop space in the spare bedroom. So, Ive been working on a new workbench to replace the old workmate. I thought I'd share some progress shots.
I wanted to base the design around the Roubo / Holtzapffel designs published by Chris Schwarz. I like the idea of the twin screw vice for gripping tapered pieces, it will be very useful for holding a guitar neck whilst supporting it from below using dogs in the vice and bench top. I will also add a simple end vice for holding boards whilst I plane the faces.
Heres what the room looked like when I first moved in, before any work had been done:
You can even see the floor.
To make up the legs and stretchers, I based the design around the knock-down Holtzapffel Workbench from the woodworking magazin blog. I used cheap rough sawn B&Q 2x3s and 2x4s as I would be doing the surfacing by hand using my Stanley no 7.
As this is the first bit of joinery Ive done, and becuase those mortices are huge, I was worried that I would cut them out of square. As I was laminating the legs, I decided to be creative and cut the mortices before laminating the pieces together. I started by routing out a rebate accross the grain, using a simple jig:
Then, when they were glued up, the mortice was ready and perfectly square:
I then cut the stretchers, and was really pleased when my first mortice and tennon joint was perfectly square, if a little rough looking:
The joinery for the short stretchers is permanent, glued and pinned using 10mm ash pegs. The pegs are probably overkill but its good to overbuild a bench. Rather then offsetting the holes like you do when drawboring, I simply clamped the assembilies together then drilled right through the mortice wall and the tennon in one go.
To allow the bench to be knocked down, the long stretchers are bolted in using 200mm long 10M allthread (please ignore the glue squeeze out on this pic - I said the joinery was rough!):
Rather than expect the end grain of the pine to hold the nut in place, Ive used small blocks of rock maple which should last much longer.
And a very dull shot of the outside of the leg, showing the nut for the allthread holding the long stretcher, and the pegs holding the short stretcher:
So heres where we are this evening:
Now Ive got to decide how Im going to approach the top. I was going to use more softwood 2x4s laminated into a600mm wide top, but that would make a very soft bench. The vice jaws will certainly need to be hardwood.
I rather like how Boz did his bench top, so might look into that.
Ive recently moved into my new house, so Ive finally got my dedicated workshop space in the spare bedroom. So, Ive been working on a new workbench to replace the old workmate. I thought I'd share some progress shots.
I wanted to base the design around the Roubo / Holtzapffel designs published by Chris Schwarz. I like the idea of the twin screw vice for gripping tapered pieces, it will be very useful for holding a guitar neck whilst supporting it from below using dogs in the vice and bench top. I will also add a simple end vice for holding boards whilst I plane the faces.
Heres what the room looked like when I first moved in, before any work had been done:
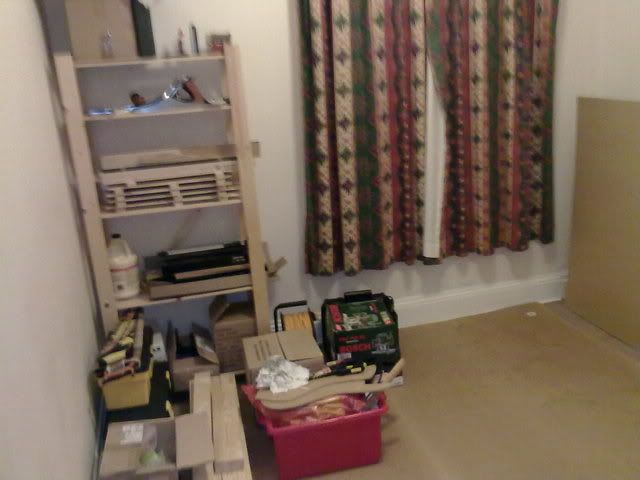
You can even see the floor.
To make up the legs and stretchers, I based the design around the knock-down Holtzapffel Workbench from the woodworking magazin blog. I used cheap rough sawn B&Q 2x3s and 2x4s as I would be doing the surfacing by hand using my Stanley no 7.
As this is the first bit of joinery Ive done, and becuase those mortices are huge, I was worried that I would cut them out of square. As I was laminating the legs, I decided to be creative and cut the mortices before laminating the pieces together. I started by routing out a rebate accross the grain, using a simple jig:
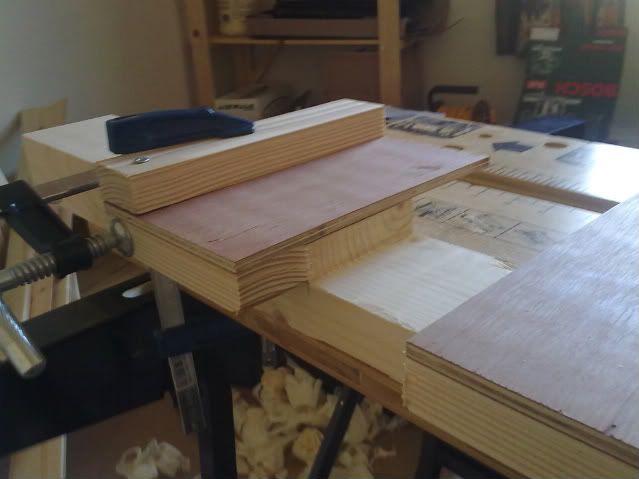
Then, when they were glued up, the mortice was ready and perfectly square:
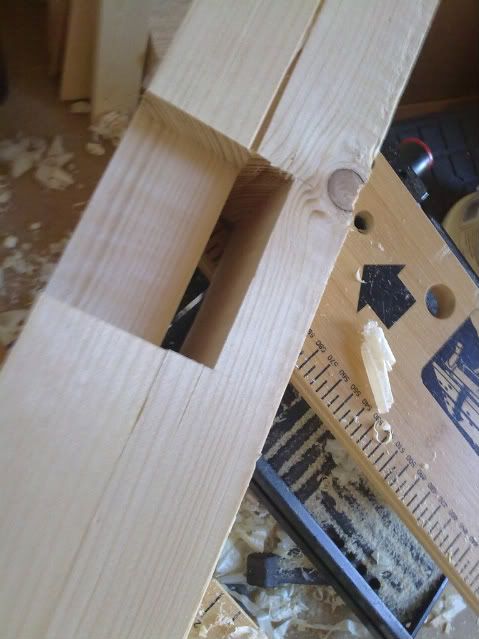
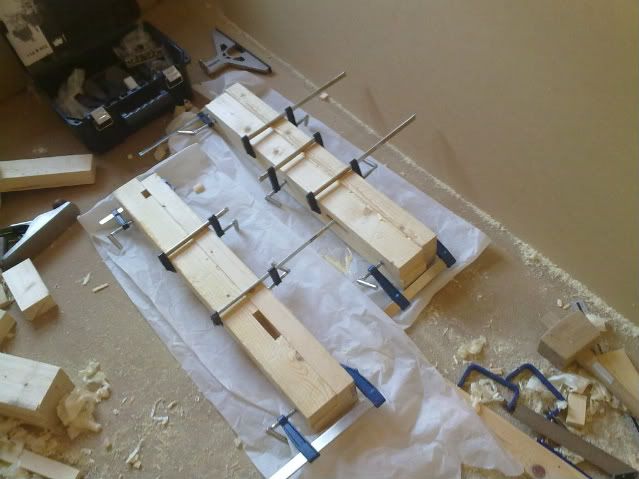
I then cut the stretchers, and was really pleased when my first mortice and tennon joint was perfectly square, if a little rough looking:
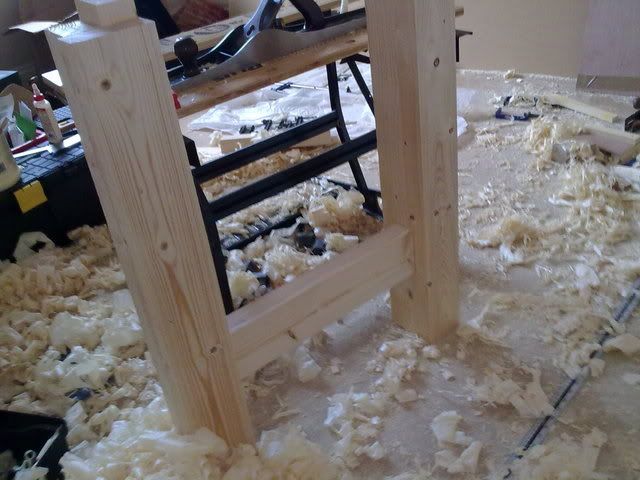
The joinery for the short stretchers is permanent, glued and pinned using 10mm ash pegs. The pegs are probably overkill but its good to overbuild a bench. Rather then offsetting the holes like you do when drawboring, I simply clamped the assembilies together then drilled right through the mortice wall and the tennon in one go.
To allow the bench to be knocked down, the long stretchers are bolted in using 200mm long 10M allthread (please ignore the glue squeeze out on this pic - I said the joinery was rough!):
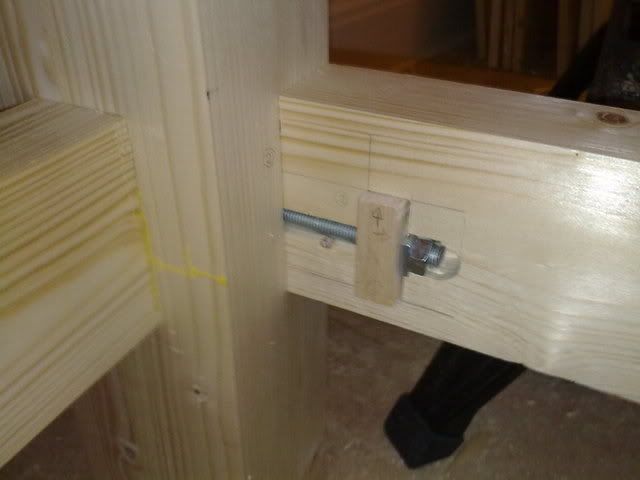
Rather than expect the end grain of the pine to hold the nut in place, Ive used small blocks of rock maple which should last much longer.
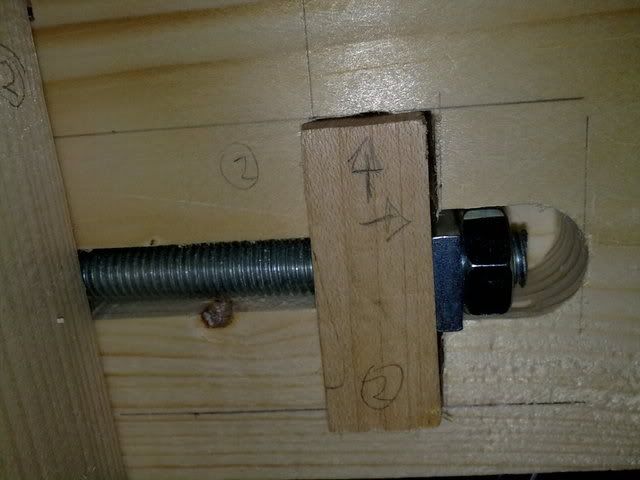
And a very dull shot of the outside of the leg, showing the nut for the allthread holding the long stretcher, and the pegs holding the short stretcher:
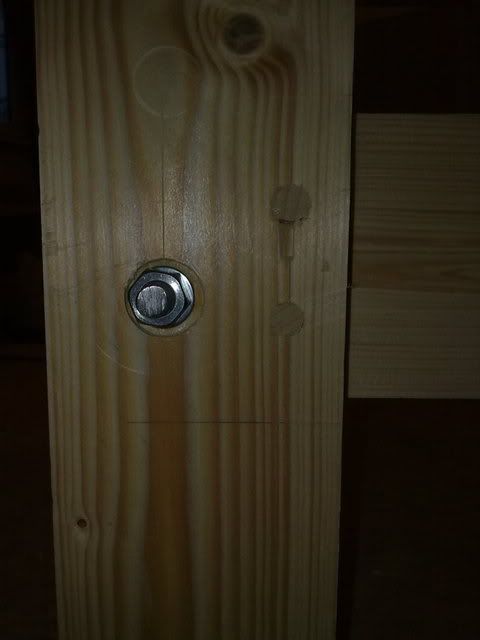
So heres where we are this evening:
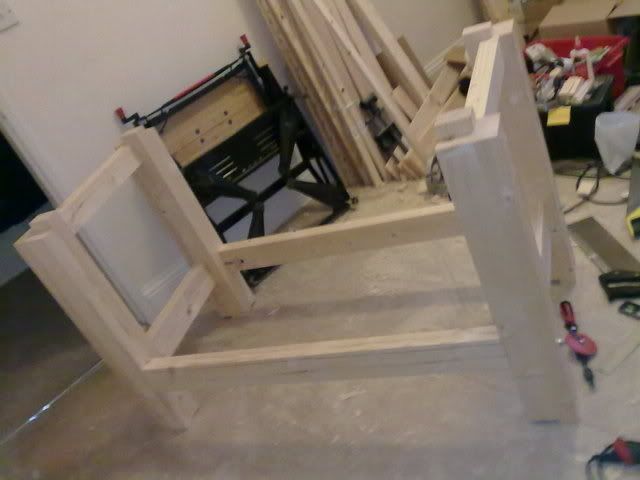
Now Ive got to decide how Im going to approach the top. I was going to use more softwood 2x4s laminated into a600mm wide top, but that would make a very soft bench. The vice jaws will certainly need to be hardwood.
I rather like how Boz did his bench top, so might look into that.