rhrwilliams
Established Member
So I had a long winded thread a while back about sash window research from 1720-1750 ish . Anyway I got round to making them finally this weekend. I've had so much help from various people I thought I better document what I have done in case someone else may find use for it .
I've used a drawing from Jacob as the rough basis , although I have changed a few dims to make similar to some windows I found locally . I've never made a sash window before and didn't know what that would look like on the house so made a mock up first out of scrap wood I had knocking about ... a few cock ups but got them out the way in the mock up.
Here is mock up
I ground two sets of profile cutters , one a for a 18mm glazing bar and one for 14mm. I'm using the 14mm one as I like it .
Simple Cutters like thes are actually much easier to grind than I thought. Took about 20 mins .
I then made a full size rod on plywood to match my drawing I made on CAD
Then spent what seemed like forever planing timber for cill and box . Then machined the parting Bead groove and tongues for linings . I used a single £10 Euro cutter for everything from forming rebated to cutting the tongue .
Then a big stack of wood appeared . Cut the housings in the cill and box frame head
I've used a drawing from Jacob as the rough basis , although I have changed a few dims to make similar to some windows I found locally . I've never made a sash window before and didn't know what that would look like on the house so made a mock up first out of scrap wood I had knocking about ... a few cock ups but got them out the way in the mock up.
Here is mock up
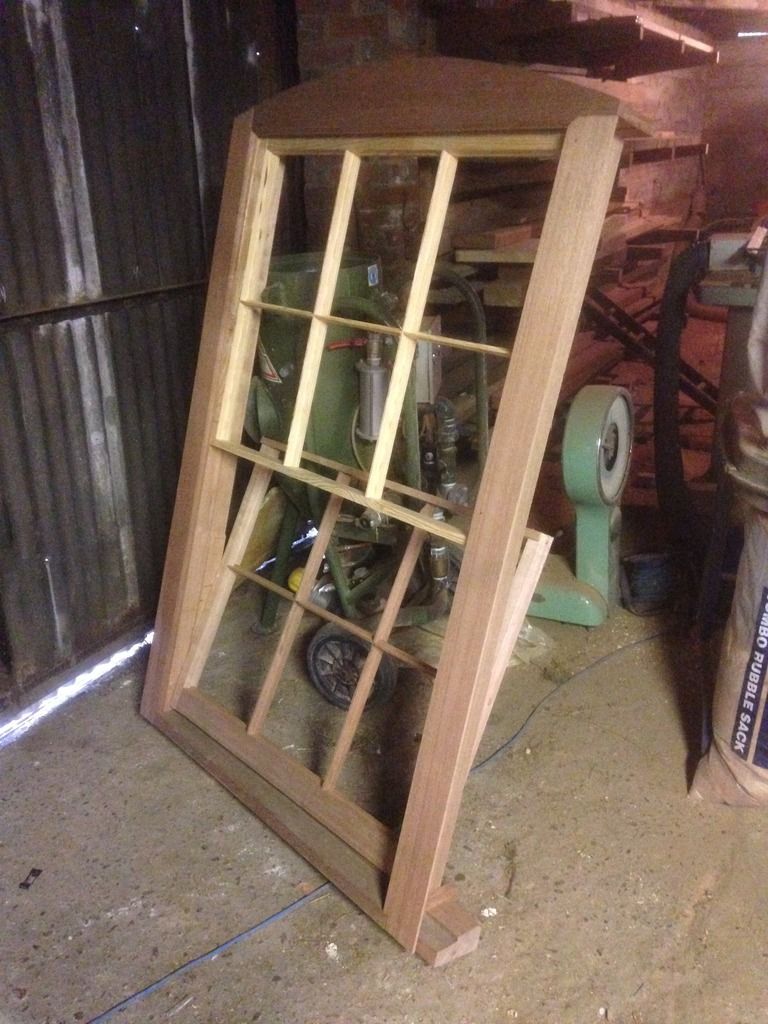
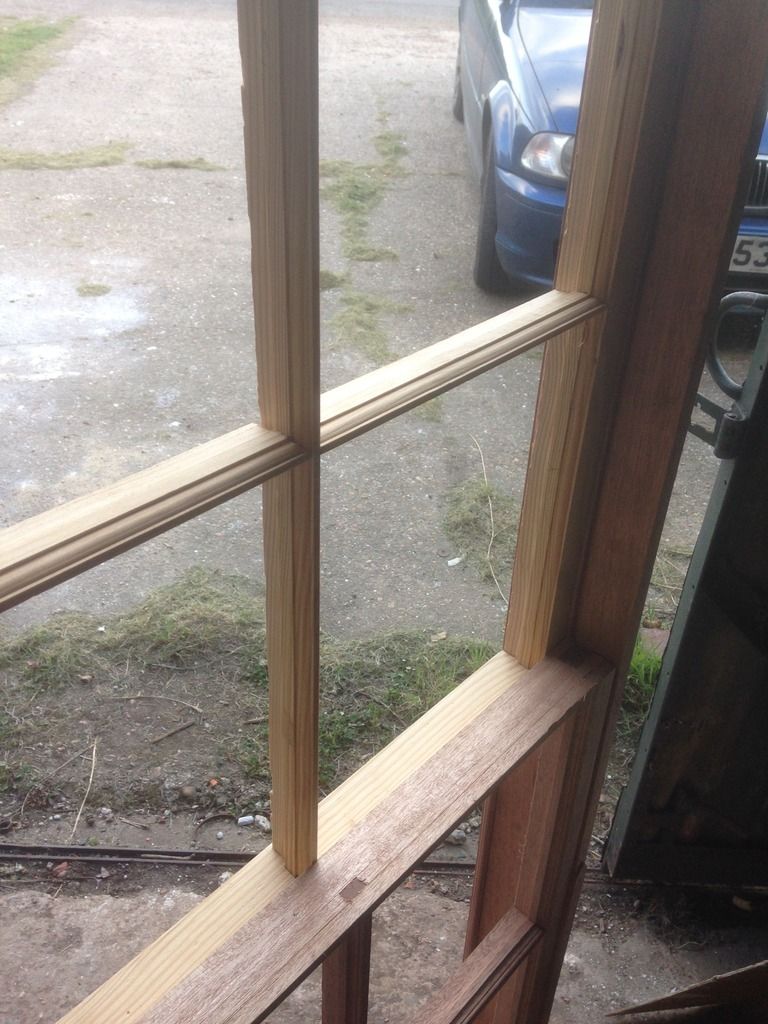
I ground two sets of profile cutters , one a for a 18mm glazing bar and one for 14mm. I'm using the 14mm one as I like it .
Simple Cutters like thes are actually much easier to grind than I thought. Took about 20 mins .
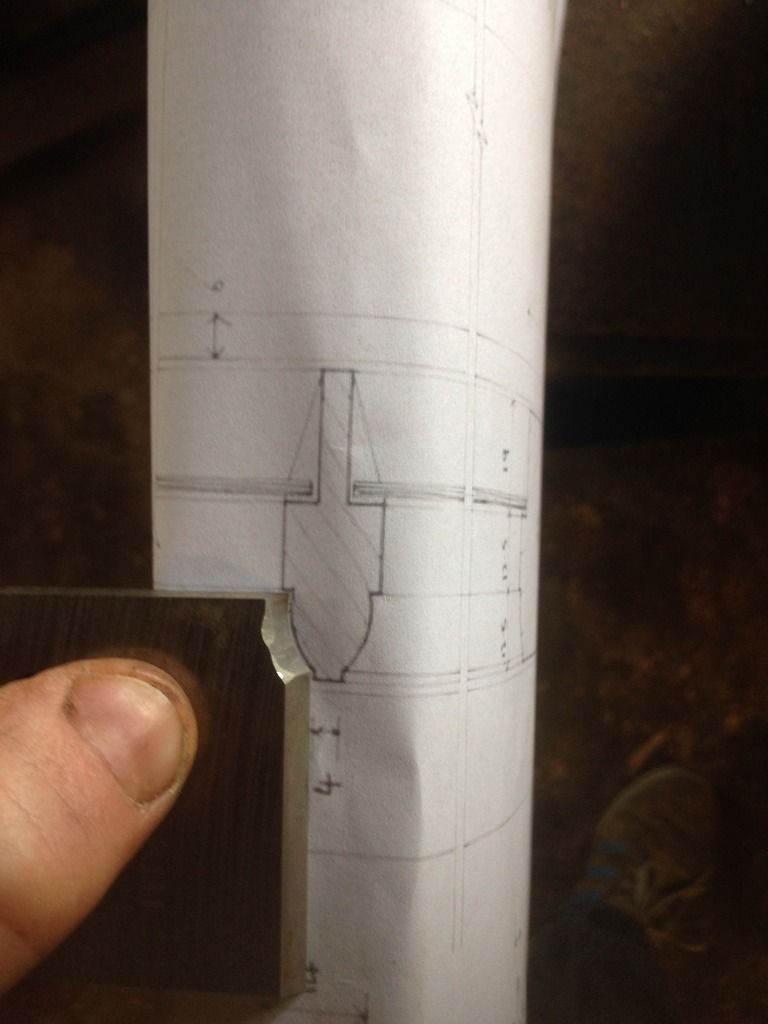
I then made a full size rod on plywood to match my drawing I made on CAD
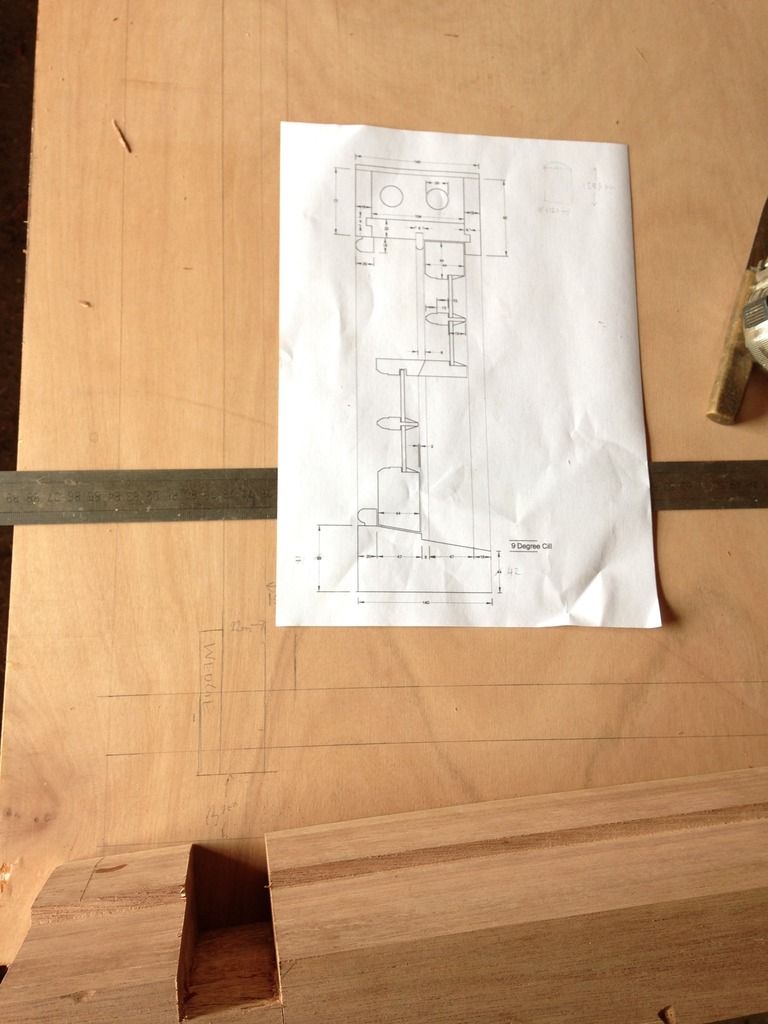
Then spent what seemed like forever planing timber for cill and box . Then machined the parting Bead groove and tongues for linings . I used a single £10 Euro cutter for everything from forming rebated to cutting the tongue .
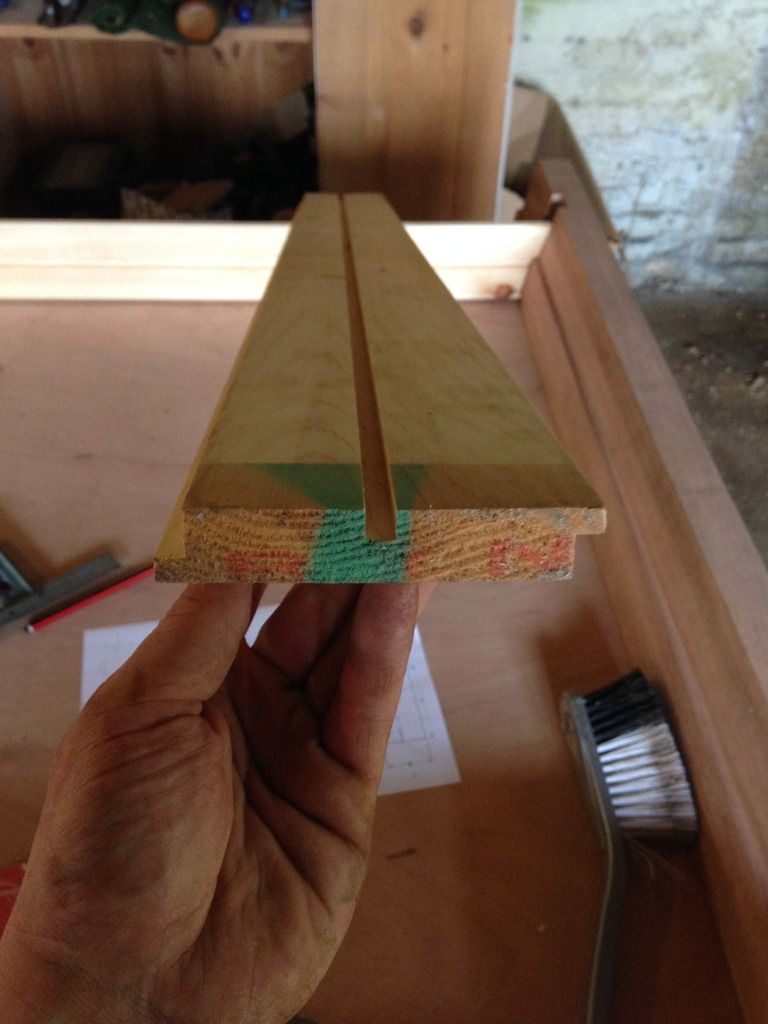
Then a big stack of wood appeared . Cut the housings in the cill and box frame head
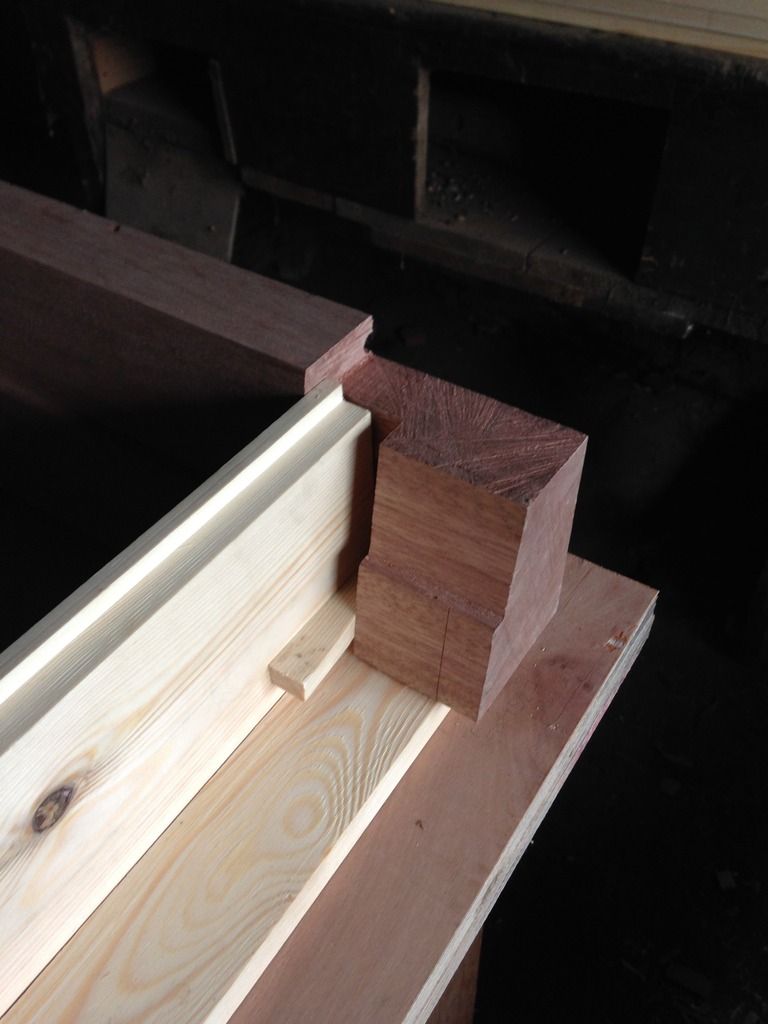