I thought I'd share the process I go through of making a casement window. It's a fairly straightforward design, but might be of interest to someone who hasn't made one before.
I've tried to make the process seem as logical as possible, so hopefully might be easy to follow- fingers crossed !
I wouldn't necessarily do the stages in this order, but this, I think, should be the easier way for somebody considering making there first window.
This is the windows I'm making
The joy of this job, is all the frame timbers are exactly the same size - 94x57mm.
First thing to do is make a cutting list so you can order timber and then cut out your pieces. These are the names of the window parts.
I usually allow around 100mm extra for length, so with this in mind, make a list of each part you require. As an example I've made a cutting list for the top window in the pic.
The windows only having single glazing, so only needs to be ex 2 inch thick.
Cut out and label the parts for your windows.
Top and tail, and thickness the pieces to size.
I've put the frame parts on the left pile to make finding them for machining easier.
Coley
I've tried to make the process seem as logical as possible, so hopefully might be easy to follow- fingers crossed !
I wouldn't necessarily do the stages in this order, but this, I think, should be the easier way for somebody considering making there first window.
This is the windows I'm making

The joy of this job, is all the frame timbers are exactly the same size - 94x57mm.
First thing to do is make a cutting list so you can order timber and then cut out your pieces. These are the names of the window parts.
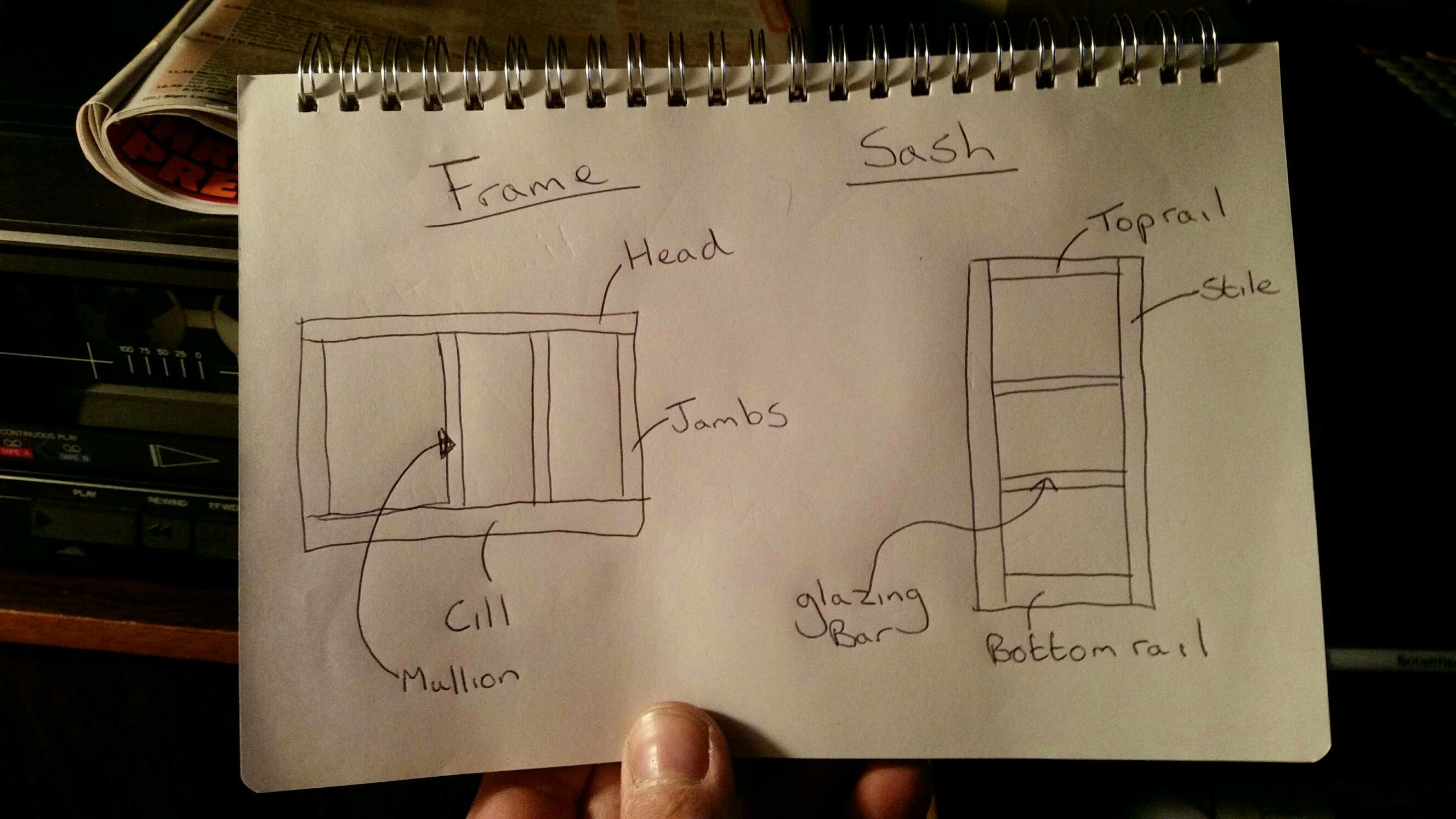
I usually allow around 100mm extra for length, so with this in mind, make a list of each part you require. As an example I've made a cutting list for the top window in the pic.
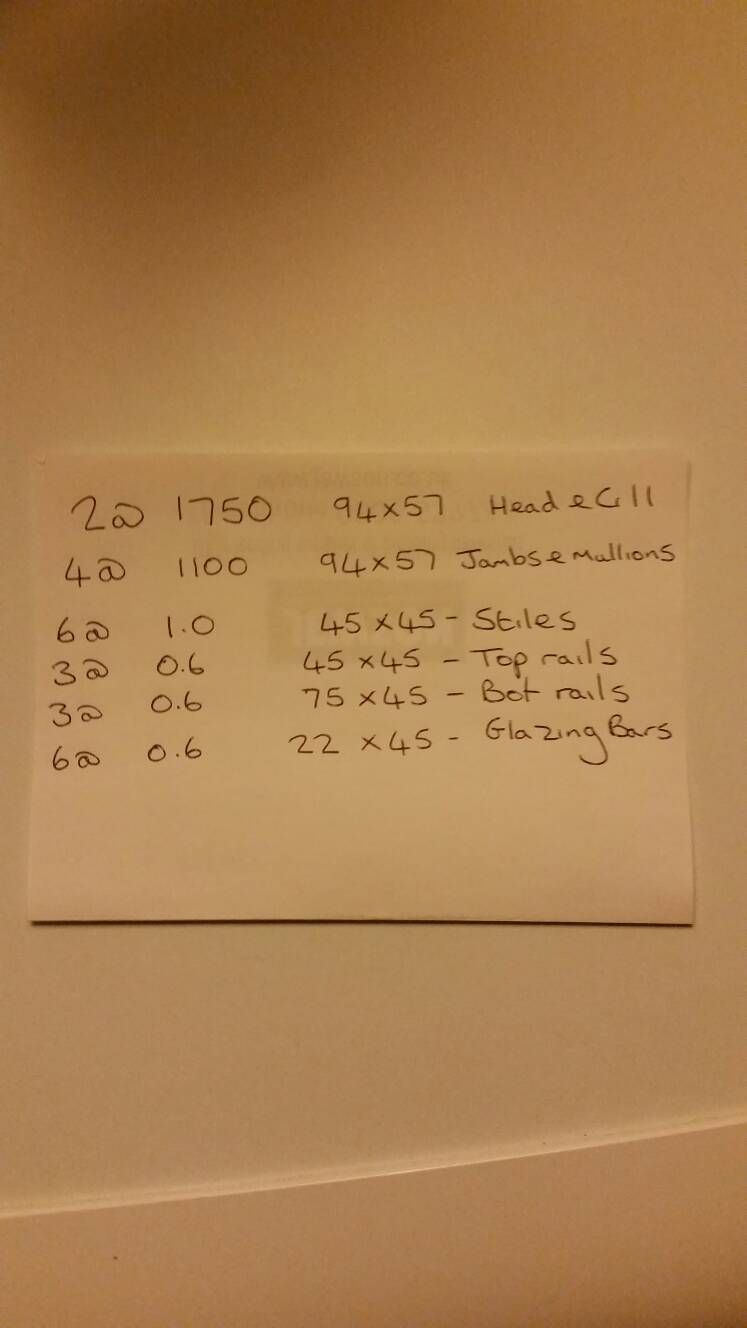
The windows only having single glazing, so only needs to be ex 2 inch thick.
Cut out and label the parts for your windows.
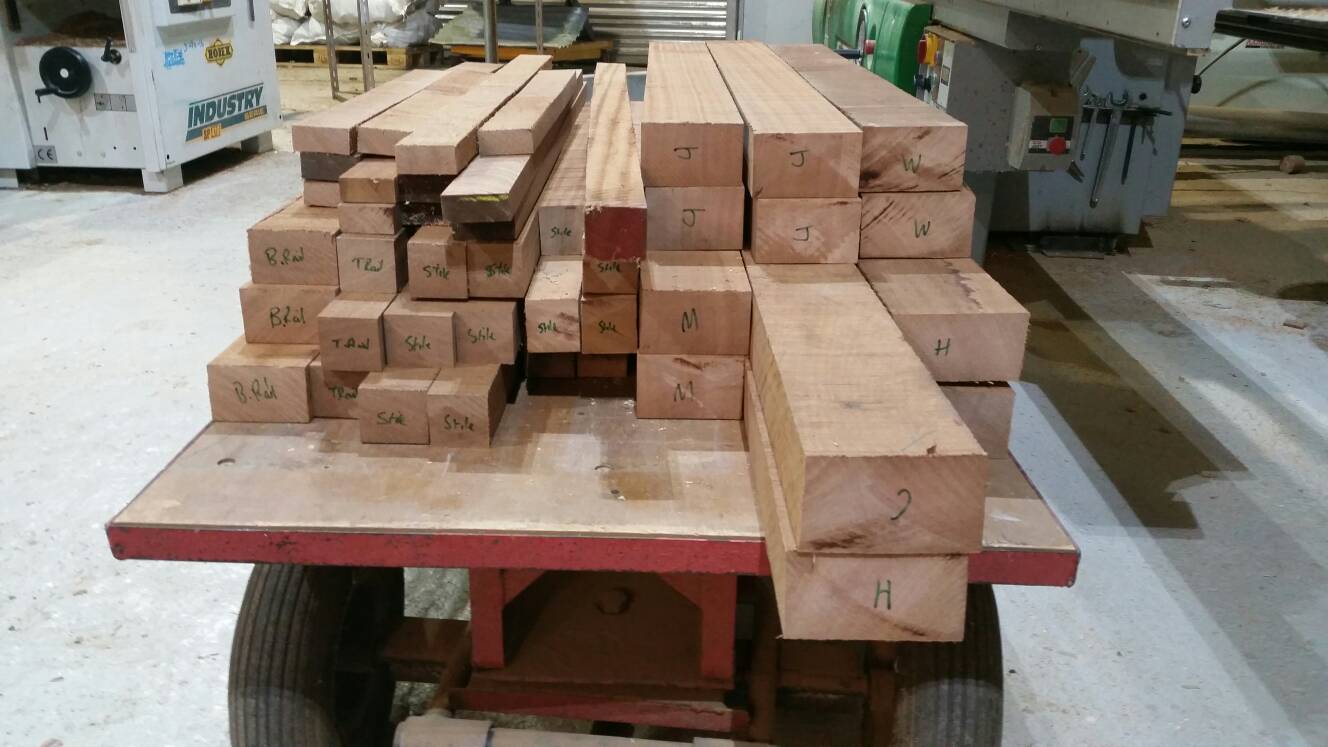
Top and tail, and thickness the pieces to size.
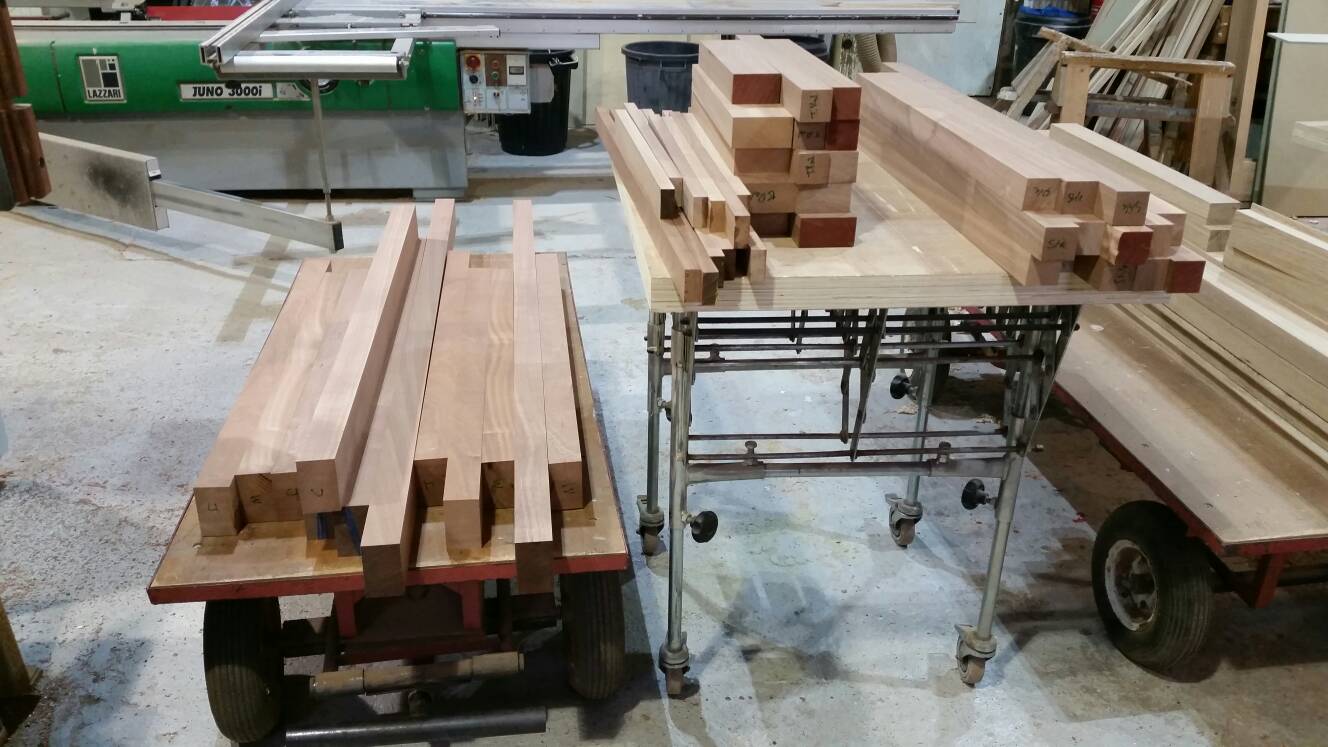
I've put the frame parts on the left pile to make finding them for machining easier.
Coley