Steve Jones
Established Member
Hi,
Not been around much on here over the last few months mainly due to designing and building my 'new toy' :lol:
The machine size is 1550mm long by 950mm wide giving a cutting area of 1270mm x 630mm, I decided on these sizes so I could get a quarter sheet size on the cutting area.
The 1550 axis is running on 20mm supported precision rail, the 950 axis and Z axis are both on unsupported rail. I used trapezoidal thread on all axis' which are tr16x4 on the X & Y and tr12x3 on the Z. I made all the bearing blocks which sit at each end of the trapezoidal thread and turned the threads down to fit, this was all a first for me after buying a Chester DB7 lathe as I'd never done any metalworking before.
Running all axis' are Nema 23 439oz stepper motors which also have M542h Steeper Drivers on them as well, power for all this is supplied by a 48V 10A power supply.
I couldn't have built it without the help of a very good mate who's an engineer but during the build there have been many 'tearing the hair out moments' and once or twice I've nearly scrapped the build but now it's up and running I'm so glad I didn't :mrgreen:
I use Vcarve pro for designing anything I cut and Mach3 for running the cnc.
Having done quite a bit of testing over the last few weeks the only things I would changes are the TR threads on the X&Y and use 16x8 instead of 16x4 and in the future I'd also like to use a Kress 1050 spindle instead of the old Bosch router that's in there now.
Anyway on with the pics, hope you like them.
Not been around much on here over the last few months mainly due to designing and building my 'new toy' :lol:
The machine size is 1550mm long by 950mm wide giving a cutting area of 1270mm x 630mm, I decided on these sizes so I could get a quarter sheet size on the cutting area.
The 1550 axis is running on 20mm supported precision rail, the 950 axis and Z axis are both on unsupported rail. I used trapezoidal thread on all axis' which are tr16x4 on the X & Y and tr12x3 on the Z. I made all the bearing blocks which sit at each end of the trapezoidal thread and turned the threads down to fit, this was all a first for me after buying a Chester DB7 lathe as I'd never done any metalworking before.
Running all axis' are Nema 23 439oz stepper motors which also have M542h Steeper Drivers on them as well, power for all this is supplied by a 48V 10A power supply.
I couldn't have built it without the help of a very good mate who's an engineer but during the build there have been many 'tearing the hair out moments' and once or twice I've nearly scrapped the build but now it's up and running I'm so glad I didn't :mrgreen:
I use Vcarve pro for designing anything I cut and Mach3 for running the cnc.
Having done quite a bit of testing over the last few weeks the only things I would changes are the TR threads on the X&Y and use 16x8 instead of 16x4 and in the future I'd also like to use a Kress 1050 spindle instead of the old Bosch router that's in there now.
Anyway on with the pics, hope you like them.
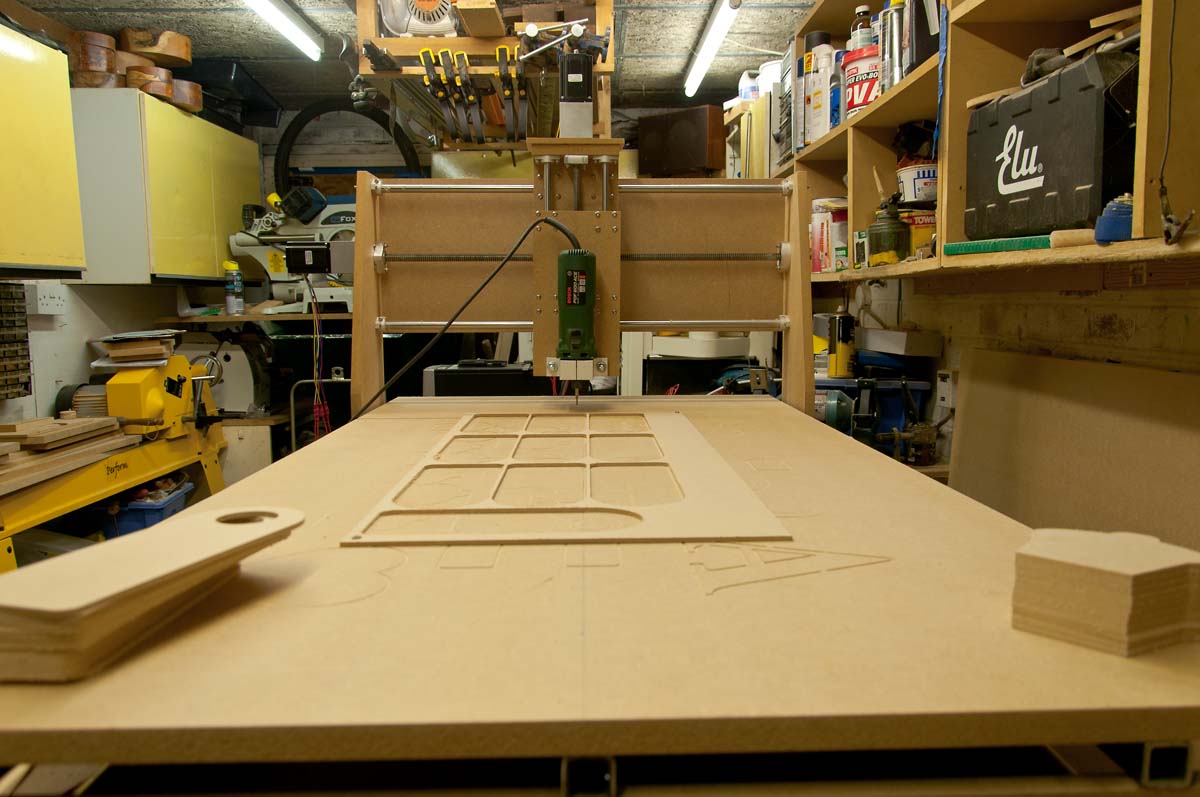
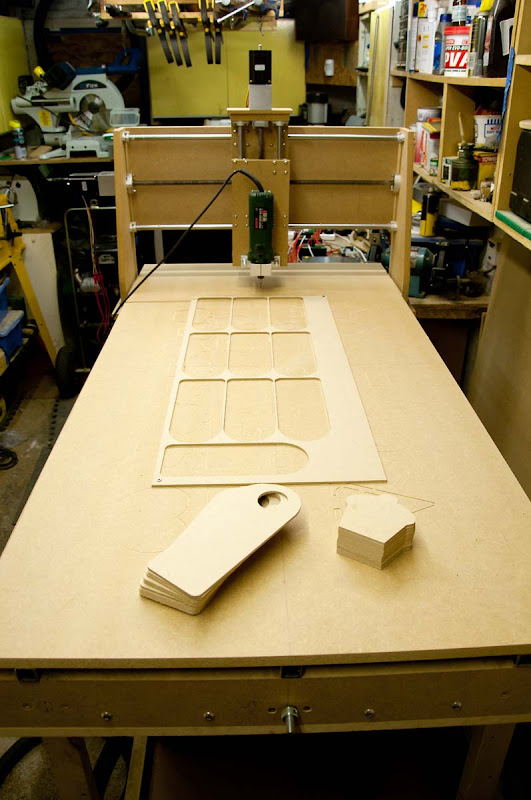
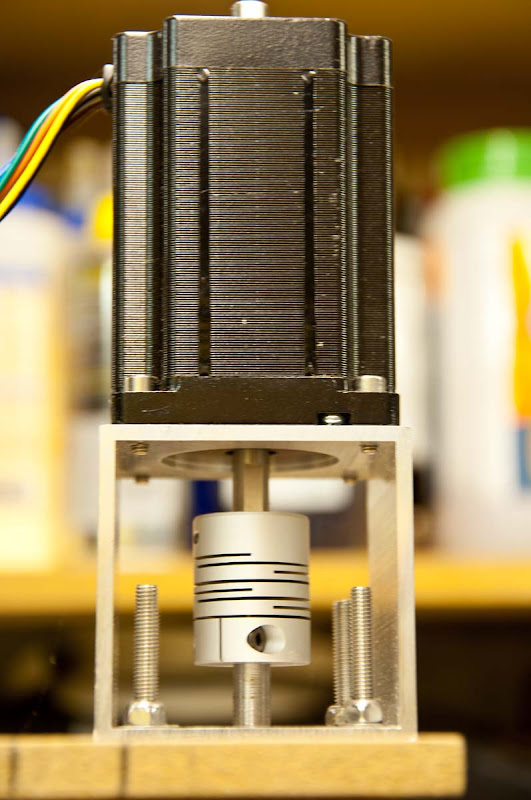
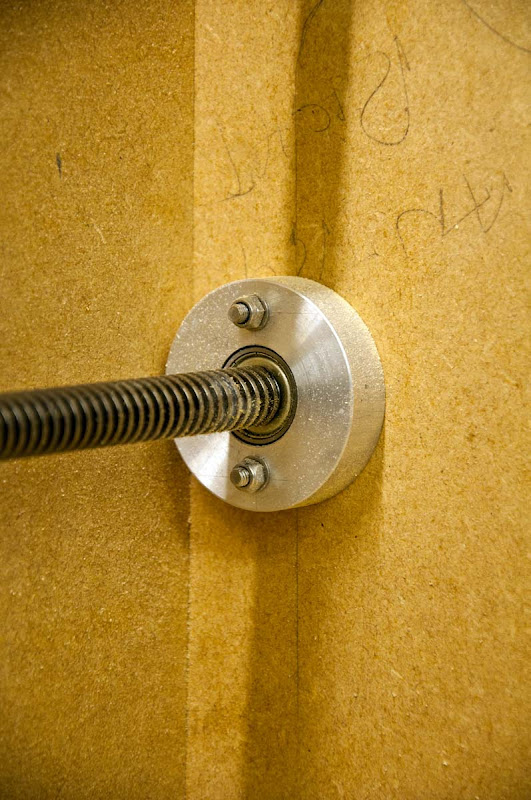
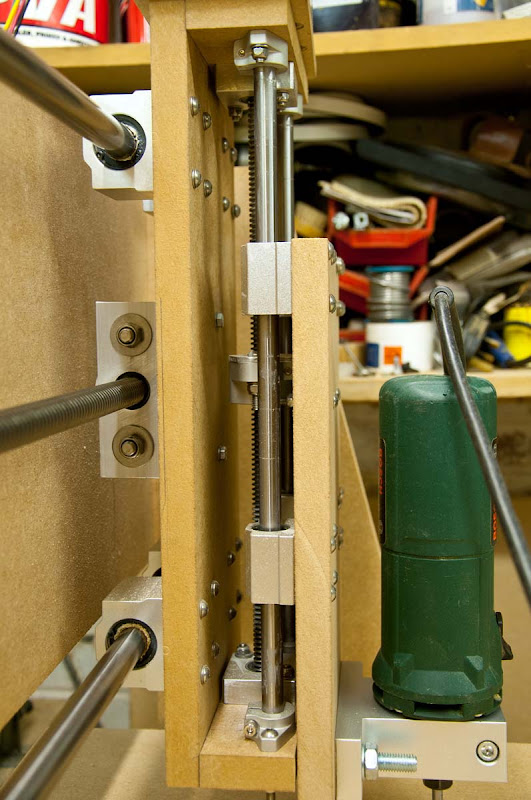