Well, kinda. I really liked the concept of the sorby pro edge sharpening system. But the price wasn't very agreeable and I like homemade tools. The design isn't mind but copied from John Heisz 's forums, by another user called Pekka.
Got some extra bolts, and replaced the tracking adjusting rod with a bolt and knob:
The tensioning mechanism works real nice and I calculated that I can take up to a 50x1000mm sanding belt. So this sander can take belts from 790mm (sorby belts) up to 1000mm long, a span of 210mm.
Because of this wide span of possible belt sizes, the upper and lower wheels will be in different positions depending on belt length. So I made the platen so it could be moved and adjusted for various belt lengths.
The platen is made from a piece of angle iron that I literally found rusting under my deck this summer (some of the house builders must've left it behind) and had forgotten about, just the right size too.
Next step is to paint it, I am thinking black and yellow. The belt speed is not very fast so the dust mainly falls straight down. Some more fiddling with the tool rest is needed too.
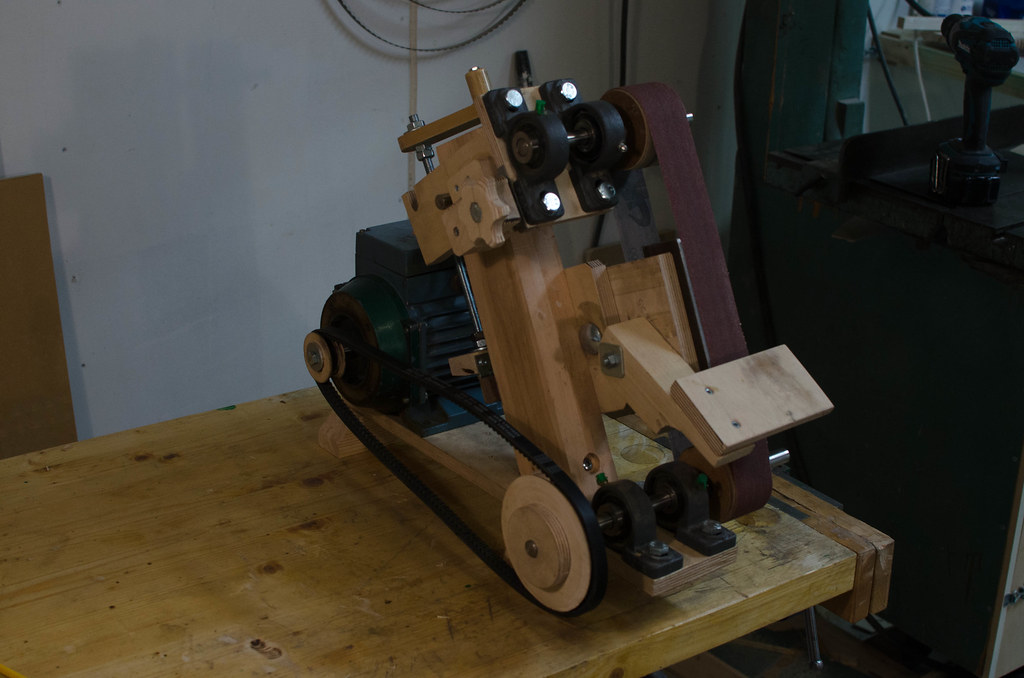
Got some extra bolts, and replaced the tracking adjusting rod with a bolt and knob:
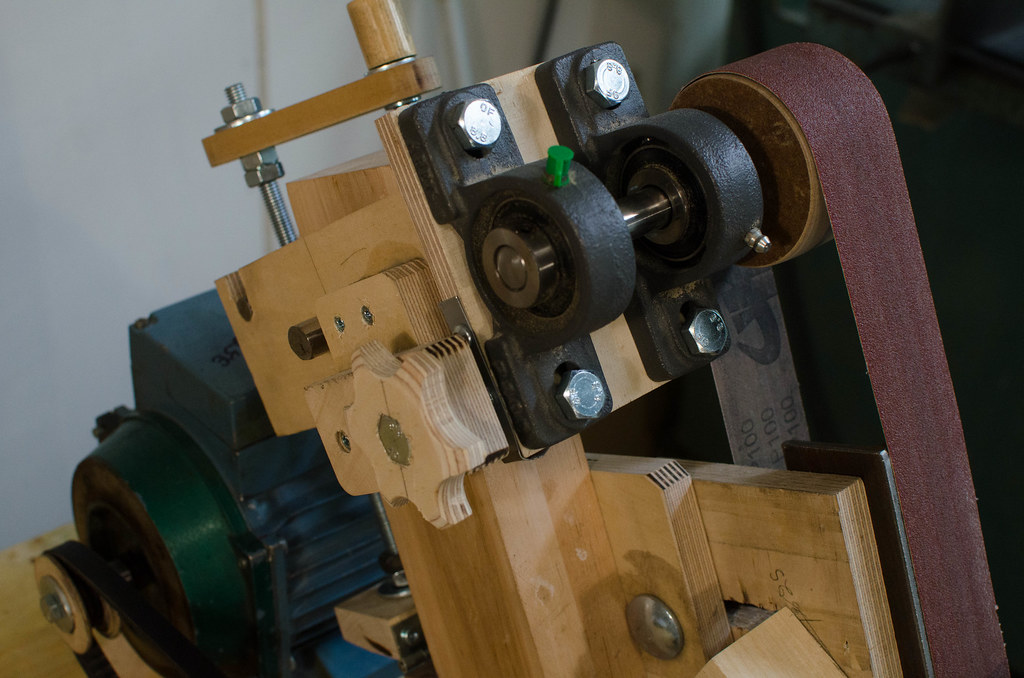
The tensioning mechanism works real nice and I calculated that I can take up to a 50x1000mm sanding belt. So this sander can take belts from 790mm (sorby belts) up to 1000mm long, a span of 210mm.
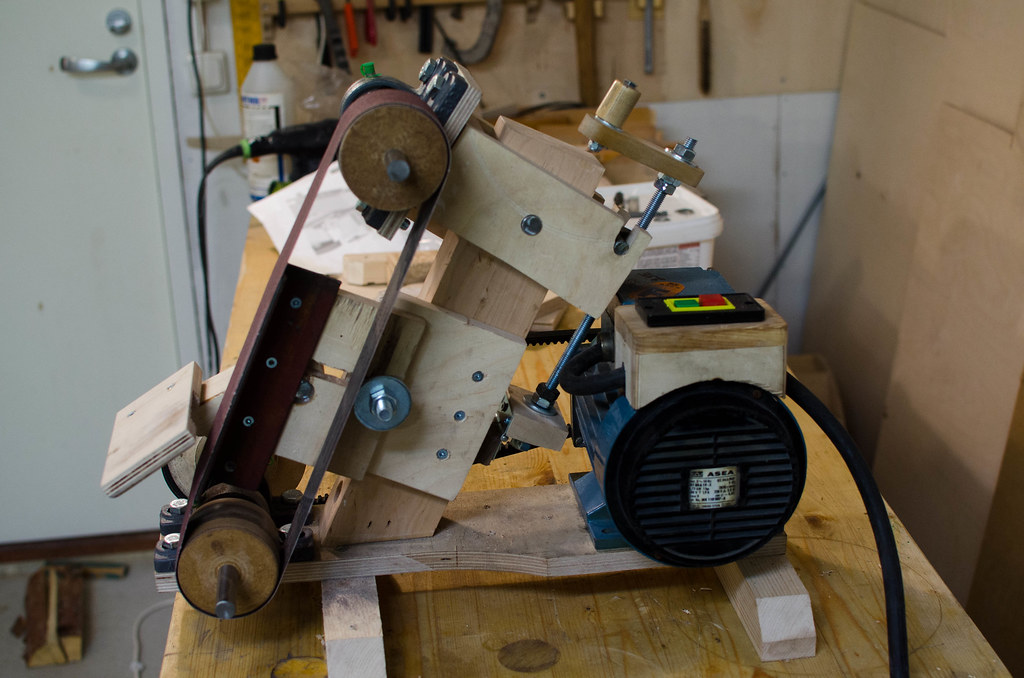
Because of this wide span of possible belt sizes, the upper and lower wheels will be in different positions depending on belt length. So I made the platen so it could be moved and adjusted for various belt lengths.
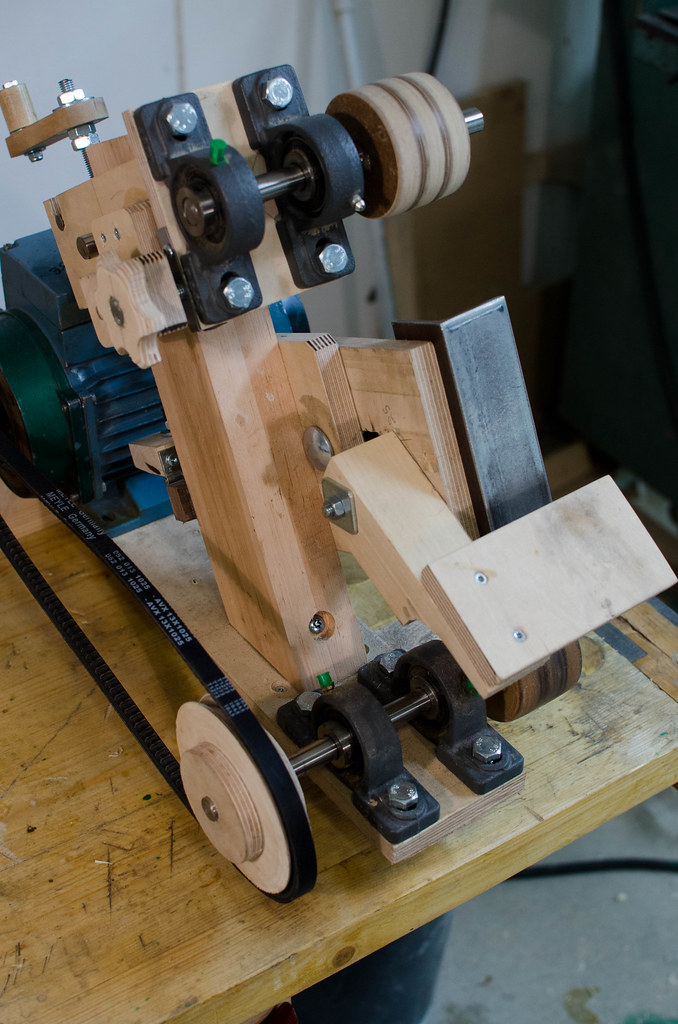
The platen is made from a piece of angle iron that I literally found rusting under my deck this summer (some of the house builders must've left it behind) and had forgotten about, just the right size too.
Next step is to paint it, I am thinking black and yellow. The belt speed is not very fast so the dust mainly falls straight down. Some more fiddling with the tool rest is needed too.