wallace
Established Member
Hi all, the machine I'm working on at the moment has a cast cover with two damaged corners. I went to see my local fabricator who said it would be £30. I thought for that much I may as well have a go myself and maybe learn something. I thought brazing would be a good choice but I have no gear. I have a mig and a little stick welder that I got given (don't know if it works). I thought I would try the stick welder. Am I correct in thinking I need nickel rods?
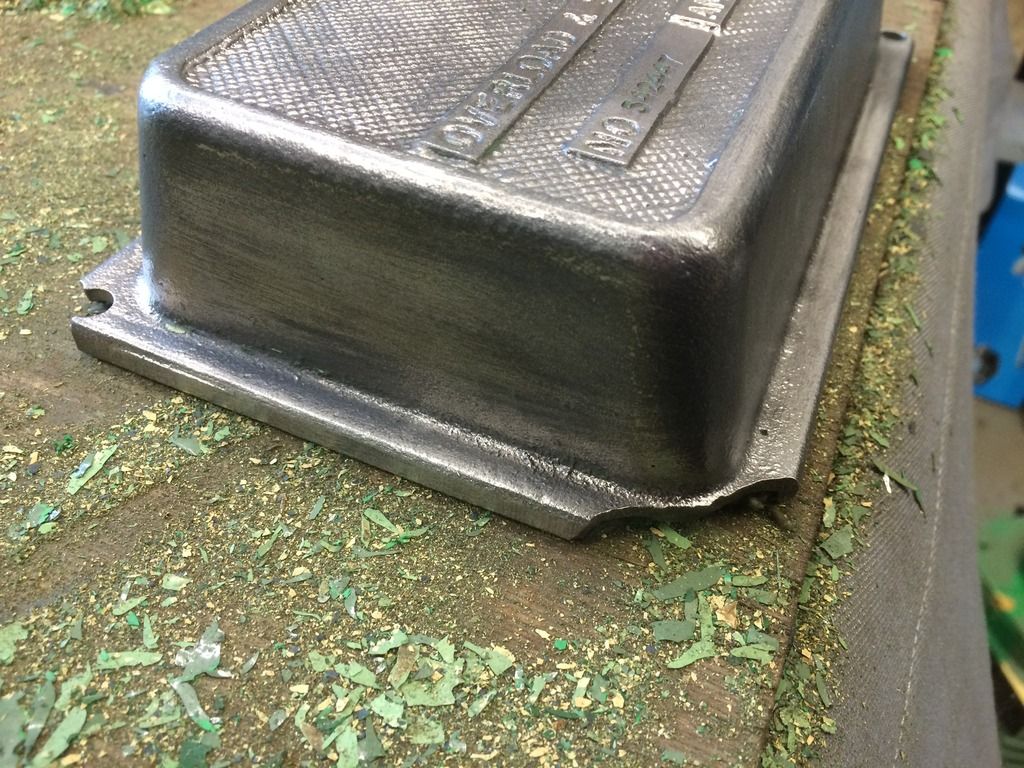