curtisrider
Established Member
I have been slowly building this disc sander up from bits and bobs that have been cluttering my shed, just fitting it in between jobs.
I used a 3/4hp motor that came with a lathe I was given (motor is great, lathe is rubbish!), some steel recycled from old tables, left over ply from a project, some spare waste pipe from doing up my house and a mitre gauge from a cheap router table. I bought 2x m6 quick release clamps from a scooter to make the bed quick and easy to adjust, some spray paint, sanding discs, rubber feet and a switch.
It's a simple welded construction for the main body, the motor is bolted down and its position can be adjusted to true it to the mitre gauge slot. The motor cover is friction fit and lifts off for adjustment if needed. The extraction box underneath does a pretty good job of catching most of the dust, some fine stuff does still manage to escape though but I am only using my henry hoover right now, my Nilfisk should make a better job of it. The wires are routed inside of the frame to keep it neat and for them to be less likely to be hit.
I didn't design it, I just used whatever I had and hoped for the best:
It does a really good job of removing material, the motor is hard to stall unless you abuse it. overall I'm quite chuffed with how little it cost and useful it is going to be! As you can see the disc guard is not on yet, I have curved the steel but I need to get round to mounting it onto the the body, after that it's ready for work
I used a 3/4hp motor that came with a lathe I was given (motor is great, lathe is rubbish!), some steel recycled from old tables, left over ply from a project, some spare waste pipe from doing up my house and a mitre gauge from a cheap router table. I bought 2x m6 quick release clamps from a scooter to make the bed quick and easy to adjust, some spray paint, sanding discs, rubber feet and a switch.
It's a simple welded construction for the main body, the motor is bolted down and its position can be adjusted to true it to the mitre gauge slot. The motor cover is friction fit and lifts off for adjustment if needed. The extraction box underneath does a pretty good job of catching most of the dust, some fine stuff does still manage to escape though but I am only using my henry hoover right now, my Nilfisk should make a better job of it. The wires are routed inside of the frame to keep it neat and for them to be less likely to be hit.
I didn't design it, I just used whatever I had and hoped for the best:

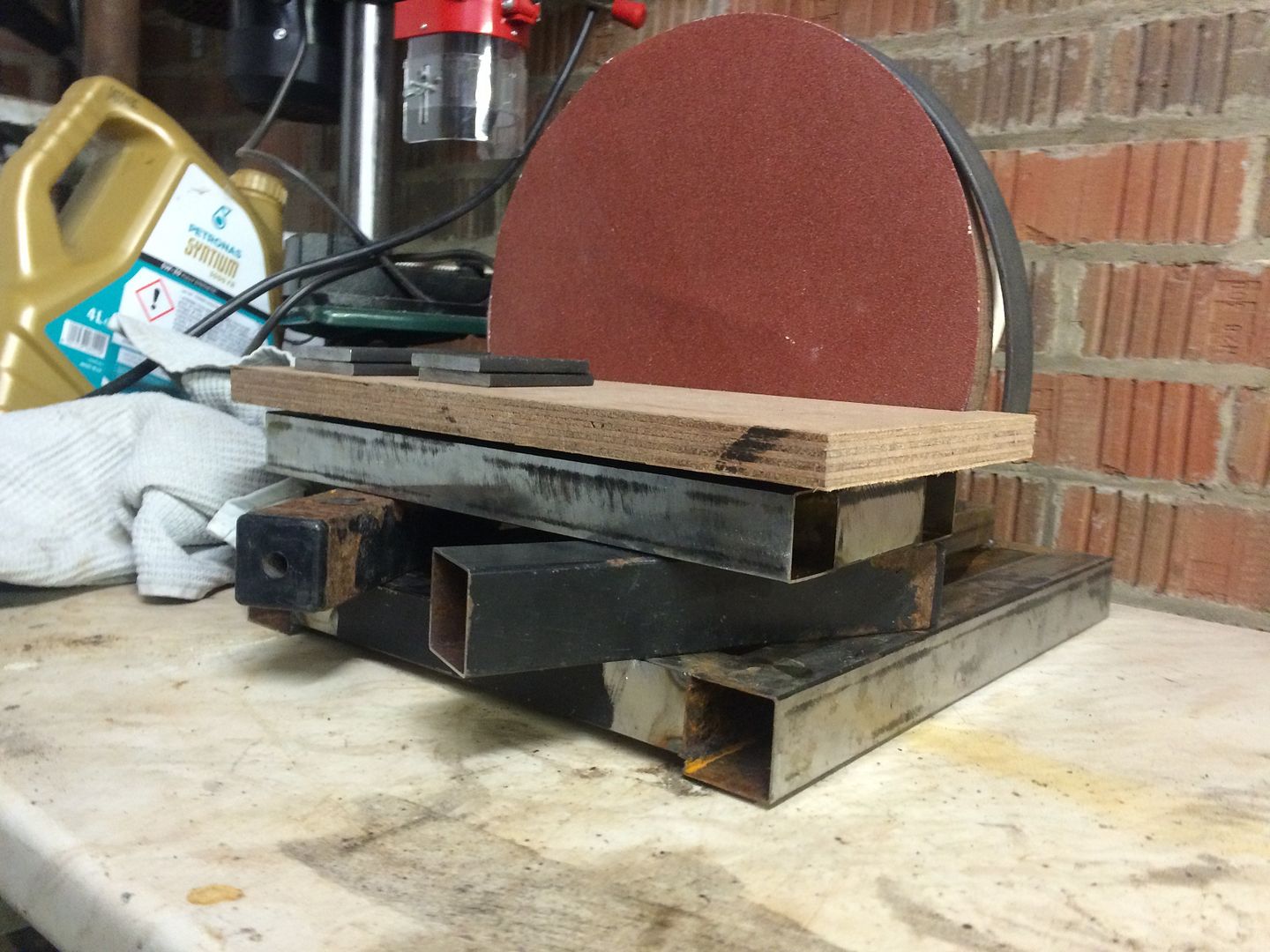



It does a really good job of removing material, the motor is hard to stall unless you abuse it. overall I'm quite chuffed with how little it cost and useful it is going to be! As you can see the disc guard is not on yet, I have curved the steel but I need to get round to mounting it onto the the body, after that it's ready for work