I have tried two methods of extracting the dust from my bandsaw but neither are working very effectively and I thought maybe you guys might be able to help.
I've been cutting a plastic material and it's proving to be extremely messy with the plastic dust going everywhere including over my hands and clothes and I'm not sure why it's so much worse than wood dust....
Using the twin motor on my camvac extractor isn't making much difference despite the massive increase in suck.
This is what I have tried:
Pushing the 2.5" pipe up the dust extraction port so it is sucking near the wheel - see outside port and interior photos:
But I'm still getting a build up of dust so I tried this from an idea I saw on here a while ago. I've removed the pipe for clarity but it pushes into the round adapter:
I was hoping that it would suck the dust off the blade before it got circulated but it's not working, even with twin motors going on my camvac.
Do I need to enclose the adapter from the 3rd & 4th photos to improve suction or is it fundamentally a flawed concept?
I did see another idea on here making a plastic box to sit under the table which the blade runs through but does it work?
I'm getting piles of dust both on the wheels and on the base of the bandsaw as well as all over the surface of the table and I can see the stuff blowing everywhere. The plastic is really messy whereas wood seems much easier to control. I'm not sure what to do to resolve this.
Any ideas as to what I can do to improve the extraction?
Thanks,
Jennifer,
I've been cutting a plastic material and it's proving to be extremely messy with the plastic dust going everywhere including over my hands and clothes and I'm not sure why it's so much worse than wood dust....
Using the twin motor on my camvac extractor isn't making much difference despite the massive increase in suck.
This is what I have tried:
Pushing the 2.5" pipe up the dust extraction port so it is sucking near the wheel - see outside port and interior photos:

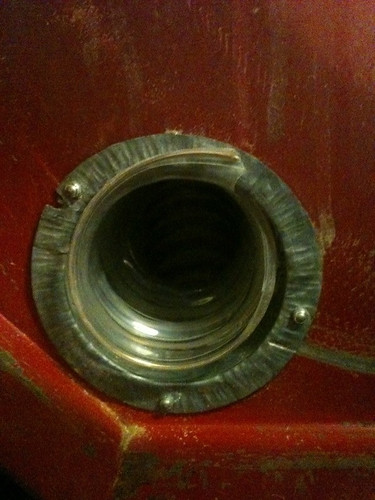
But I'm still getting a build up of dust so I tried this from an idea I saw on here a while ago. I've removed the pipe for clarity but it pushes into the round adapter:
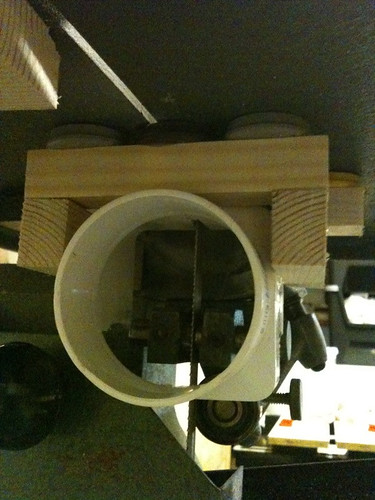

I was hoping that it would suck the dust off the blade before it got circulated but it's not working, even with twin motors going on my camvac.
Do I need to enclose the adapter from the 3rd & 4th photos to improve suction or is it fundamentally a flawed concept?
I did see another idea on here making a plastic box to sit under the table which the blade runs through but does it work?
I'm getting piles of dust both on the wheels and on the base of the bandsaw as well as all over the surface of the table and I can see the stuff blowing everywhere. The plastic is really messy whereas wood seems much easier to control. I'm not sure what to do to resolve this.
Any ideas as to what I can do to improve the extraction?
Thanks,
Jennifer,