aesmith
Established Member
Hi,
I haven't used my Elektra Beckum BAS316 bandsaw for a while, and when I came to try and use it today I found that the upper guide castings have distorted, apparently of their own accord, to the extent that the saw is unusable. Has anyone else found this sort of thing happening? The guides were always a bit squint and in fact I have photos from a few years back so can see the difference ...
Previously ..
Today ..
And the offending part ...
Any ideas? I'm really losing the will to persist with that bandsaw, it's never been a good machine even after Electra Beckum swapped the original for a brand new one. Trouble is that in the current state I can't really sell it, and not sure what I would buy as a replacement. To make matters worse that upper guide is apparently no longer available.
Tony S
I haven't used my Elektra Beckum BAS316 bandsaw for a while, and when I came to try and use it today I found that the upper guide castings have distorted, apparently of their own accord, to the extent that the saw is unusable. Has anyone else found this sort of thing happening? The guides were always a bit squint and in fact I have photos from a few years back so can see the difference ...
Previously ..

Today ..
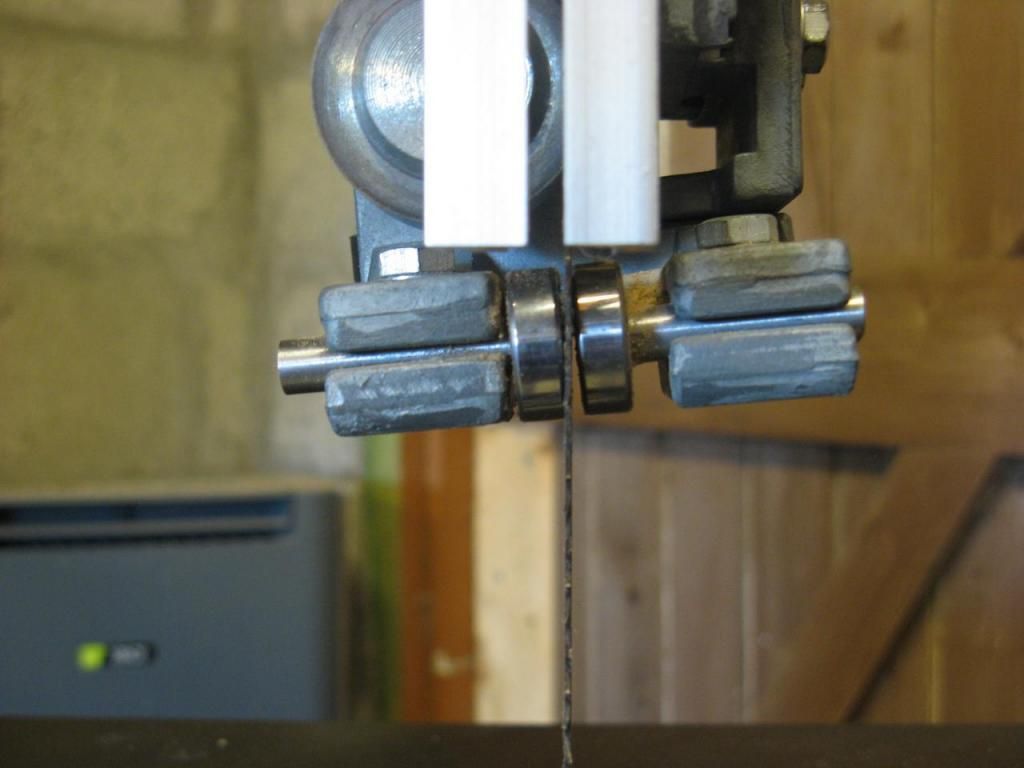
And the offending part ...
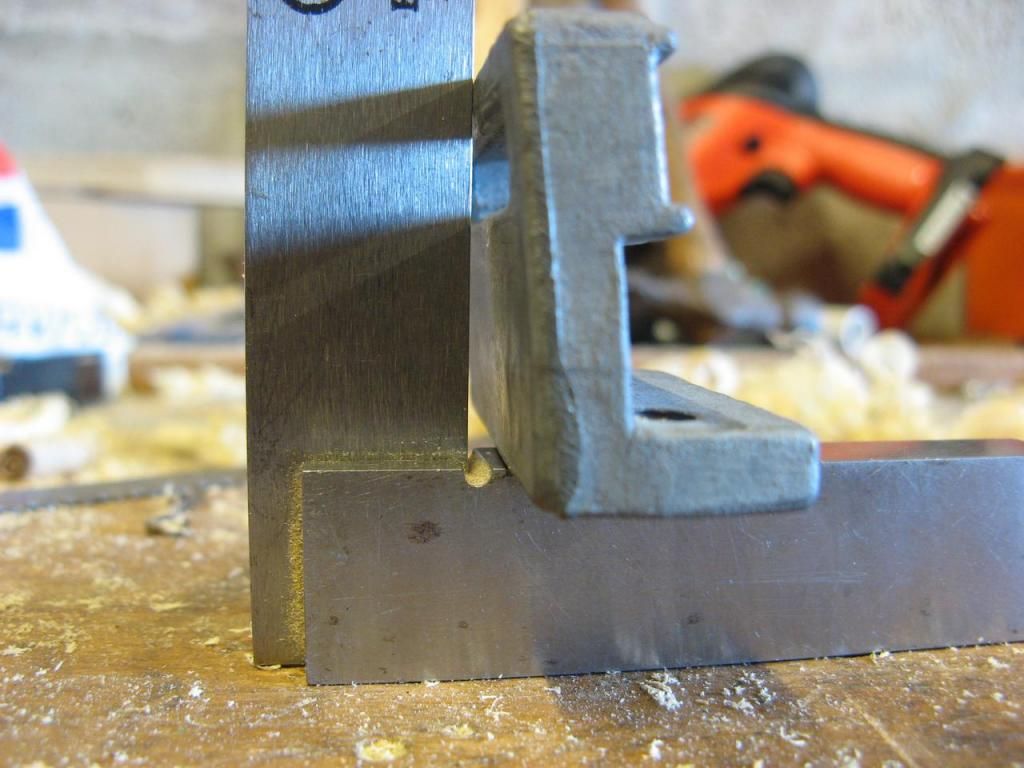
Any ideas? I'm really losing the will to persist with that bandsaw, it's never been a good machine even after Electra Beckum swapped the original for a brand new one. Trouble is that in the current state I can't really sell it, and not sure what I would buy as a replacement. To make matters worse that upper guide is apparently no longer available.
Tony S