Neil Dyball
Established Member
Hi,
Saw a Simon hope demo a while back and was inspired to have a crack at casting pewter. I really liked the contrast between the dark natural wood (African Blackwood in his demo) and the 'silvery' polished pewter.
Finally got "a round tuit" this weekend, had a nice piece of elm burr that I'd been saving and SWMBO asked for a "simple bowl", so that's what I made.
The pewter casting actually took two goes, fortunately it's easy to melt down and re-try! I'm fairly happy with it although I did uncover a couple of small 'voids' in the casting when I turned it down to the final size. Lots of lessons learned for next time though!
All (constructive) criticism appreciated 8-[
Cheers,
Neil.
Saw a Simon hope demo a while back and was inspired to have a crack at casting pewter. I really liked the contrast between the dark natural wood (African Blackwood in his demo) and the 'silvery' polished pewter.
Finally got "a round tuit" this weekend, had a nice piece of elm burr that I'd been saving and SWMBO asked for a "simple bowl", so that's what I made.
The pewter casting actually took two goes, fortunately it's easy to melt down and re-try! I'm fairly happy with it although I did uncover a couple of small 'voids' in the casting when I turned it down to the final size. Lots of lessons learned for next time though!

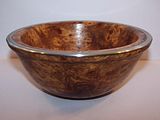
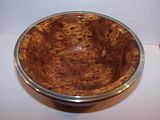

All (constructive) criticism appreciated 8-[
Cheers,
Neil.