RossJarvis
Established Member
It’s approaching evening so I’ve downed tools ready for the weekend. Friday is steak chips and a glass of wine night. After this week’s work I think I’ll make that two glasses!
Where was we, oh yes, tenoning (is that a word?). My evening class teacher said “let the saw do the work, don’t force it”, so I sat there for ages, and the b****y saw did nowt, just like the apprentice. So I had to get up and do the work myself! I’ve got one side of my body like Popeye now and the other like Olive Oyle.
Meanwhile, back on topic I was going to start marking out the mortices for the joists and tie beams. So I lined the two frames up to see which way round they ought to be. The first shot shows where the feet are together but everything else is on the p*** (at an angle);
….the next shows both frames matching near perfick like;
…obviously that was all intended and “ahem!” we need not worry about the whole thing leaning slightly to one side. It’s well within spec! Once both frames were levelled and matched together, I marked out the positions of the mortices. These were set about an inch from nearby mortices or tenons, to leave some strength in the wood;
…and to make sure I didn’t b****r it up next time, I marked the rear frame to know which way round it ought to go;
I find writing instructions all over the wood is better than doing it on paper, it’s generally harder to lose the wood than paper! I also marked the side of the line I needed to mark the mortices and which side of the timber needed the hole cut in it;
This was ‘cos the faces for the mortices were the ones clamped together. I then marked the mortices out and found an old bit of tenon waste was handy to mark the width out with;
Although, this being carcassing, no two bits of wood are the same thickness! BRRR WHIZZ WOOF OUCH and here we are, one end of the wood fitted to the other bits of wood. There is an issue about the other ends but we’ll leave that for now shall we.;
I could now do the braces for the floor. These could have been done at 45 degrees like the others, but me back were killing me so I just bunged ‘em in any old how. No-one’s going to care, they’re going to be boarded over anyway!
I’m sure, as long as the joist is at 90(ish) degrees, we’ll all be happy. BANG, CHOP, WHIRR, TWEET, OUCH and;
…the pile of sticks is starting to look like something at last here’s it with the other frame dumped on top;
I’m quite pleased with that, particularly the floor;
…even though it’s pretending to be a stud wall at the mo. Mind you, last time I was pleased with something, it broke! We’ll have to see what the morrow brings.
TTFN
Where was we, oh yes, tenoning (is that a word?). My evening class teacher said “let the saw do the work, don’t force it”, so I sat there for ages, and the b****y saw did nowt, just like the apprentice. So I had to get up and do the work myself! I’ve got one side of my body like Popeye now and the other like Olive Oyle.
Meanwhile, back on topic I was going to start marking out the mortices for the joists and tie beams. So I lined the two frames up to see which way round they ought to be. The first shot shows where the feet are together but everything else is on the p*** (at an angle);
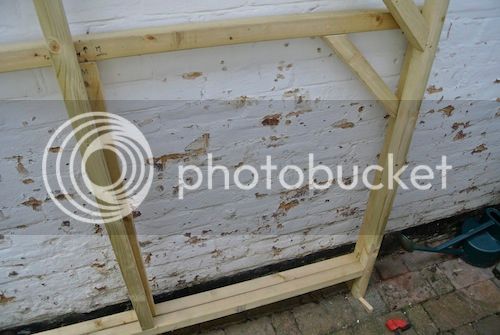
….the next shows both frames matching near perfick like;
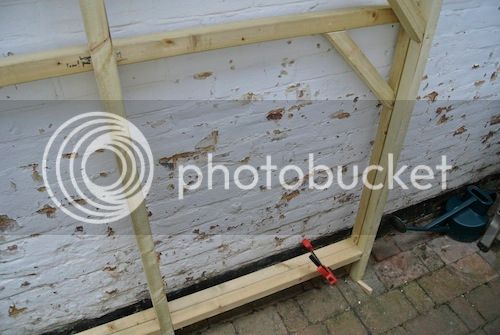
…obviously that was all intended and “ahem!” we need not worry about the whole thing leaning slightly to one side. It’s well within spec! Once both frames were levelled and matched together, I marked out the positions of the mortices. These were set about an inch from nearby mortices or tenons, to leave some strength in the wood;
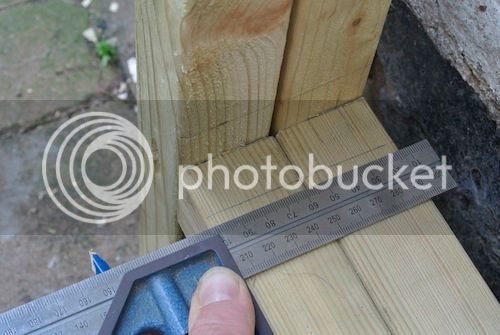
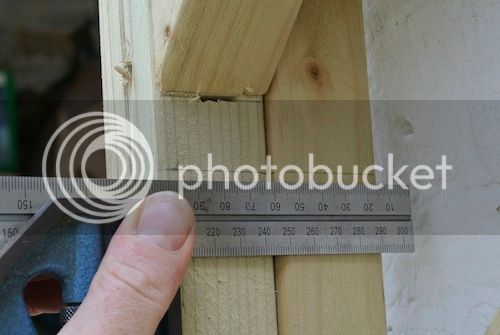
…and to make sure I didn’t b****r it up next time, I marked the rear frame to know which way round it ought to go;
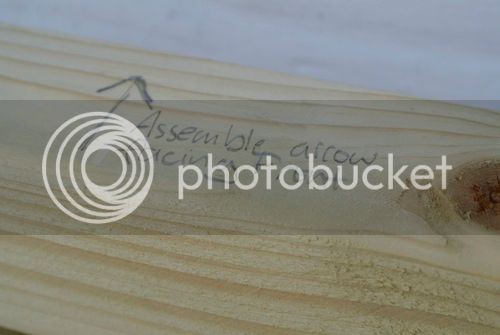
I find writing instructions all over the wood is better than doing it on paper, it’s generally harder to lose the wood than paper! I also marked the side of the line I needed to mark the mortices and which side of the timber needed the hole cut in it;
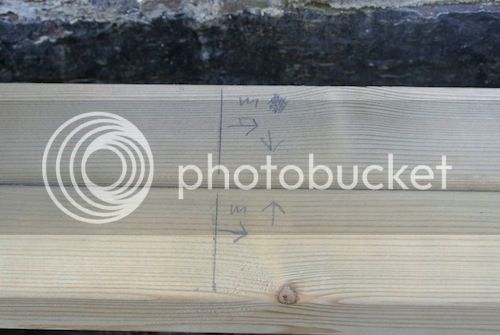
This was ‘cos the faces for the mortices were the ones clamped together. I then marked the mortices out and found an old bit of tenon waste was handy to mark the width out with;
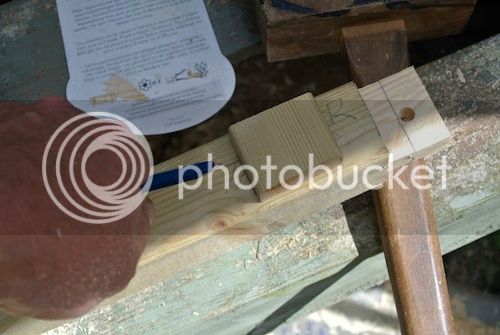
Although, this being carcassing, no two bits of wood are the same thickness! BRRR WHIZZ WOOF OUCH and here we are, one end of the wood fitted to the other bits of wood. There is an issue about the other ends but we’ll leave that for now shall we.;
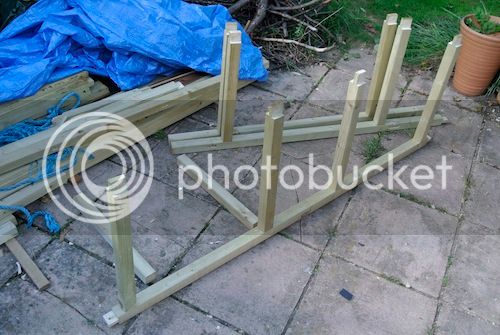
I could now do the braces for the floor. These could have been done at 45 degrees like the others, but me back were killing me so I just bunged ‘em in any old how. No-one’s going to care, they’re going to be boarded over anyway!
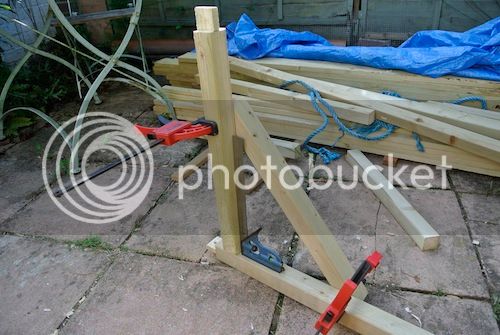
I’m sure, as long as the joist is at 90(ish) degrees, we’ll all be happy. BANG, CHOP, WHIRR, TWEET, OUCH and;

…the pile of sticks is starting to look like something at last here’s it with the other frame dumped on top;
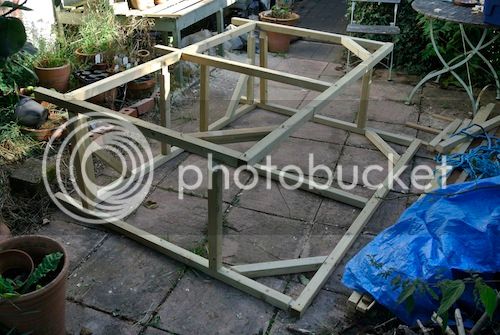
I’m quite pleased with that, particularly the floor;
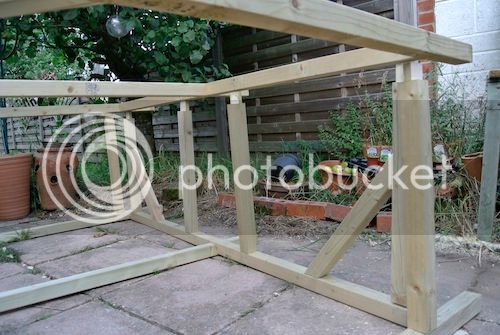
…even though it’s pretending to be a stud wall at the mo. Mind you, last time I was pleased with something, it broke! We’ll have to see what the morrow brings.
TTFN