NickN
Established Member
Rather a strange question but I'm needing a bit of advice.
I have a large cast iron wheel of around 800mm diameter (yes, 80cm) in which I need putting a plain central hole of 23.5 or perhaps 24mm diameter for an axle (and it needs to be exactly central), plus two tapped M10 10mm holes at 12.00 and 3.00 in the collar for securing bolts, and finally another plain 10mm hole in a section of one of the spokes that is made to accommodate this. I am not entirely sure what I need to be asking for, firstly for the central hole, is it drilling or milling, and would a lathe ideally be needed to skim the rim for any discrepancy in circular shape, and finally what exactly do I need to ask for in regards to the tapped holes, is 'tapped hole' the correct terminology?
If my digital caliper shows 23.57mm on the axle, should the hole be made 23.5 or 24mm, in your opinions?
Any recommendations as to who or what type of company I might approach to do this small job in the West Midlands / Worcestershire area, too?
I attach photos of an existing wheel and the axle in question to give you an idea what I'm jabbering on about!
Thanks in anticipation!
I have a large cast iron wheel of around 800mm diameter (yes, 80cm) in which I need putting a plain central hole of 23.5 or perhaps 24mm diameter for an axle (and it needs to be exactly central), plus two tapped M10 10mm holes at 12.00 and 3.00 in the collar for securing bolts, and finally another plain 10mm hole in a section of one of the spokes that is made to accommodate this. I am not entirely sure what I need to be asking for, firstly for the central hole, is it drilling or milling, and would a lathe ideally be needed to skim the rim for any discrepancy in circular shape, and finally what exactly do I need to ask for in regards to the tapped holes, is 'tapped hole' the correct terminology?
If my digital caliper shows 23.57mm on the axle, should the hole be made 23.5 or 24mm, in your opinions?
Any recommendations as to who or what type of company I might approach to do this small job in the West Midlands / Worcestershire area, too?
I attach photos of an existing wheel and the axle in question to give you an idea what I'm jabbering on about!
Thanks in anticipation!
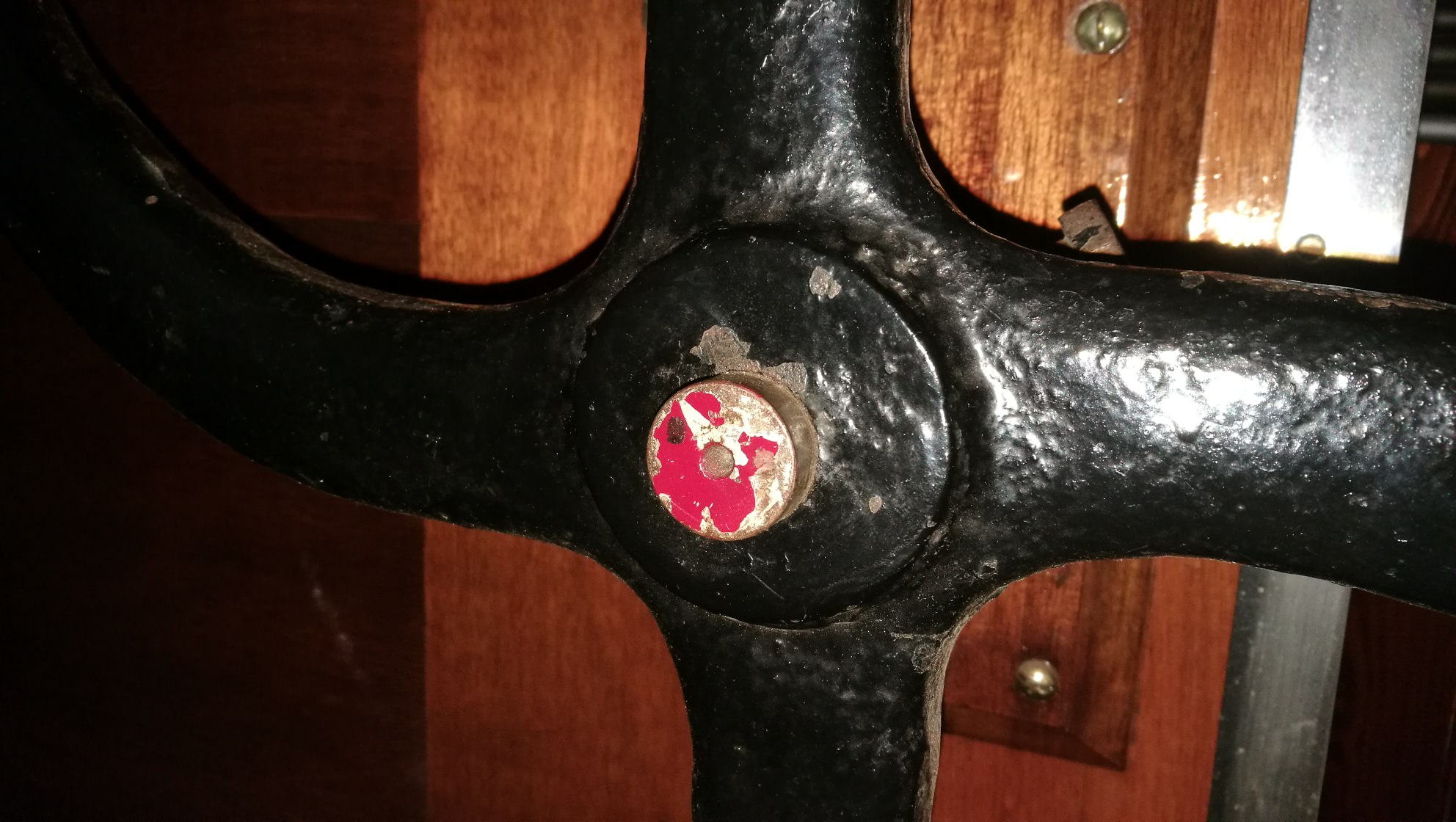
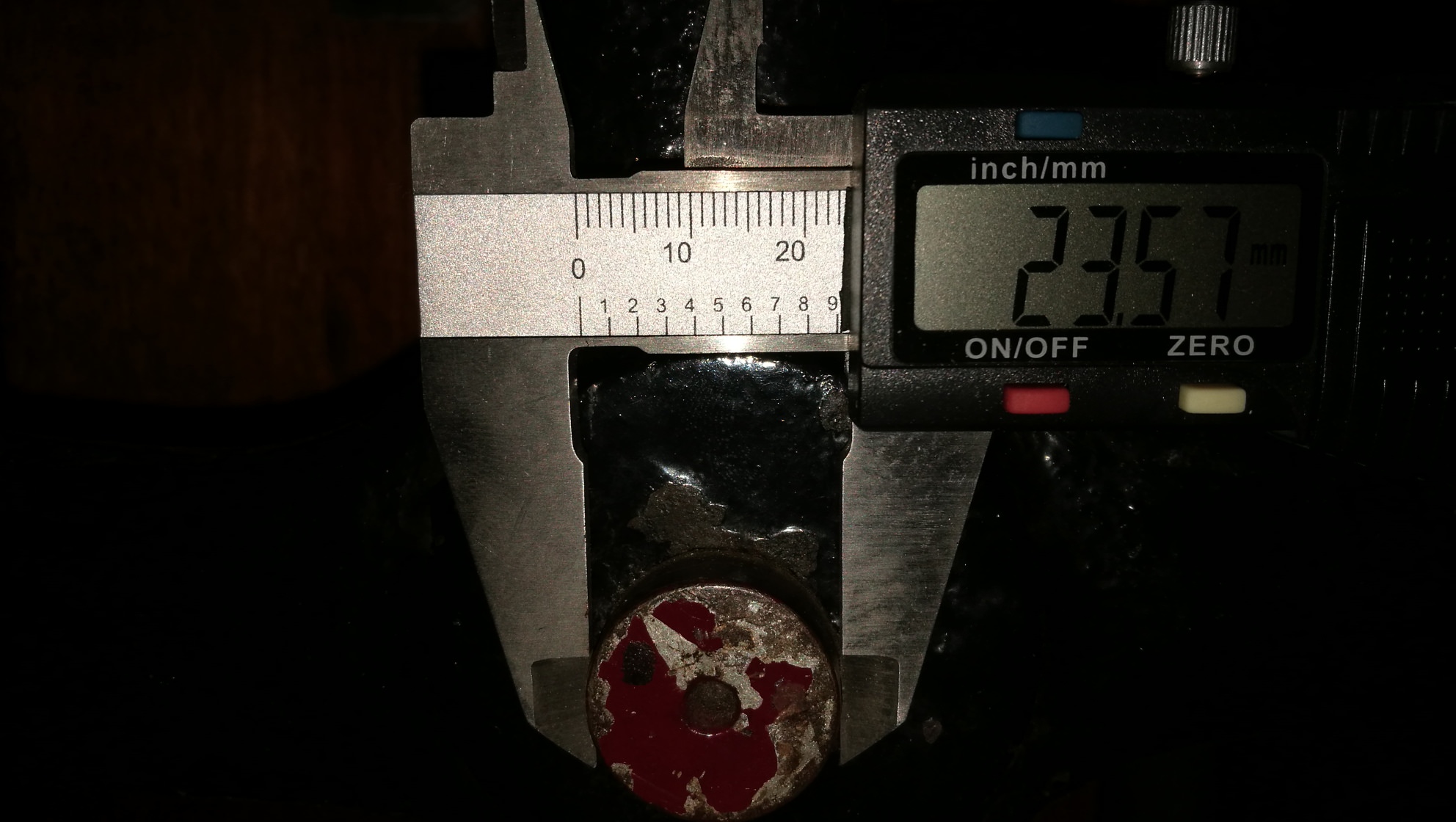
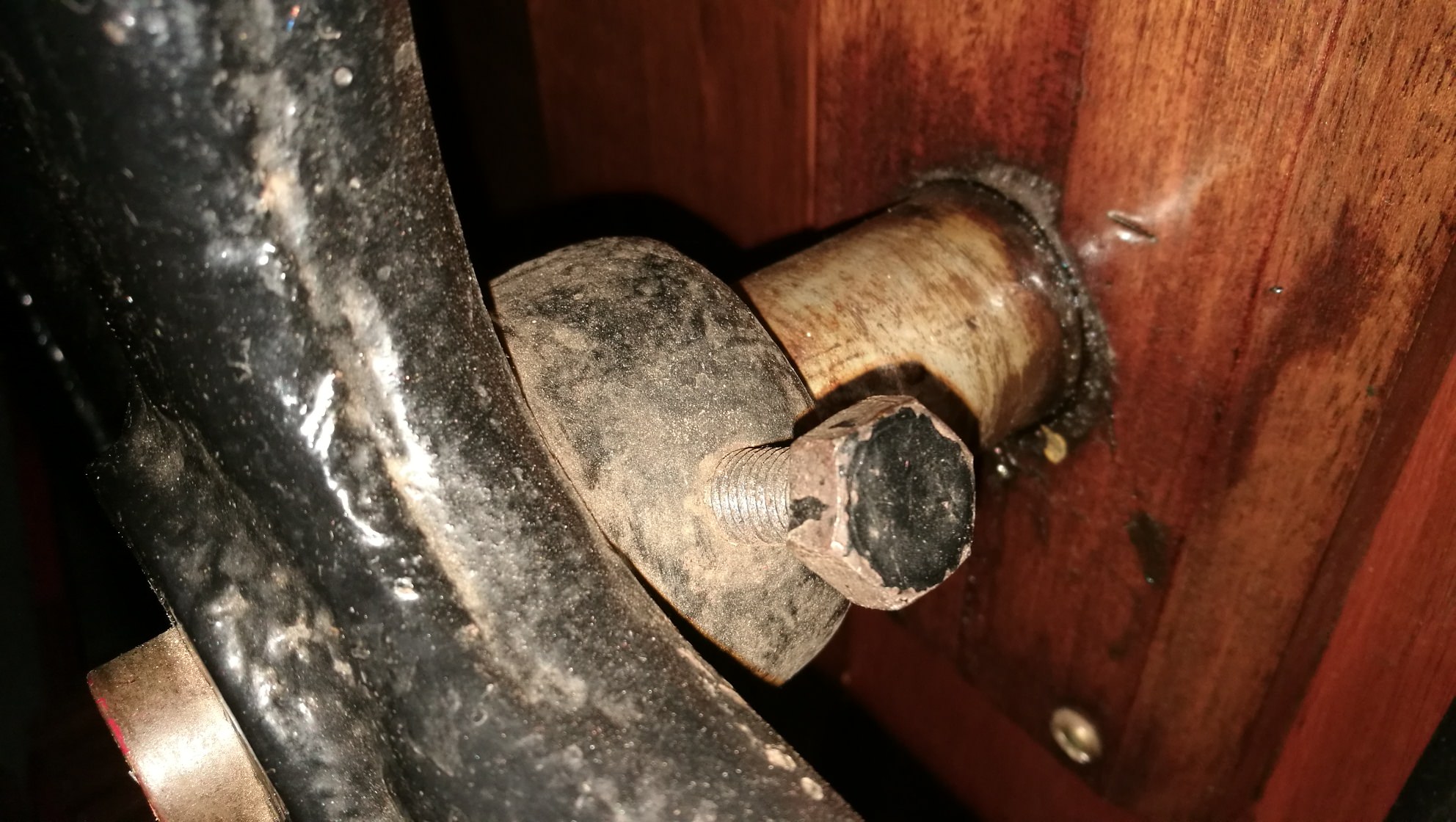
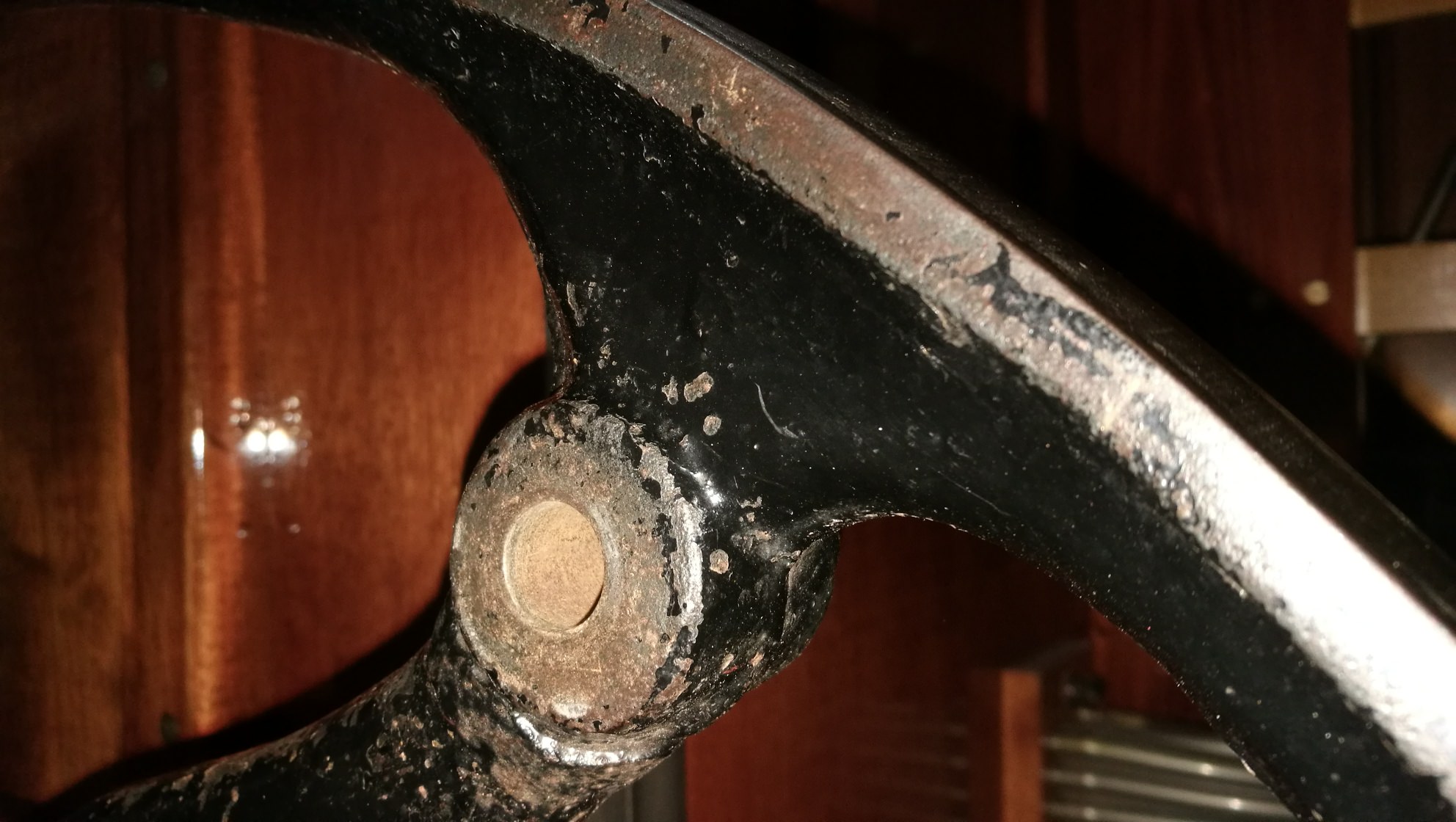