delaney001
Established Member
Any advise on how to get rid of these marks when finishing a bowl.
They only really visibly appear when I get to about 320 grit (I usually go to 600)
Would going back to 120 and starting the whole process again solve it?
https://imgur.com/gallery/28nKZ
Hopefully the link works above. If you look about 1cm from the rim of the bowl, there is a tool mark running around it.
Any suggestions appreciated.
mod edit to add pic
They only really visibly appear when I get to about 320 grit (I usually go to 600)
Would going back to 120 and starting the whole process again solve it?
https://imgur.com/gallery/28nKZ
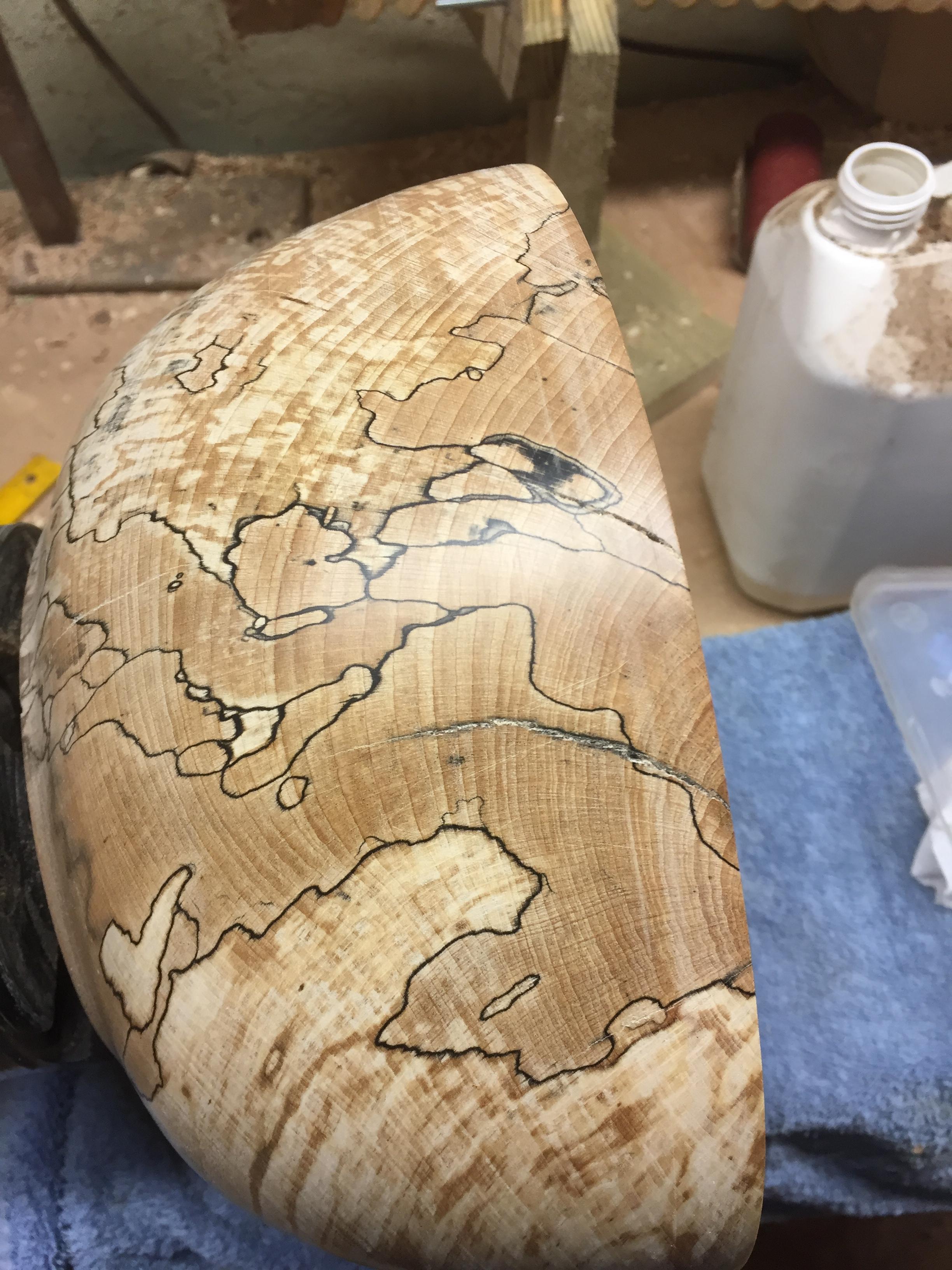
Hopefully the link works above. If you look about 1cm from the rim of the bowl, there is a tool mark running around it.
Any suggestions appreciated.
mod edit to add pic