Derek Cohen (Perth Oz)
Established Member
I have had a Stanley #112 scraper plane for about 10 years. It came with a thin blade, the standard Stanley fare. I used it for a while, never really made it work very well, and eventually bought the Lie-Nielsen “Stanley Replacement” blade for the plane. I had read on forums, such as Badger Pond, that this was the way to go, in the same manner that thick plane blades were an upgrade on the thin original Stanley bench plane blades.
Blades for the #112 are ground in the same way as bench plane blades. LN suggests that their model, which is the same design as the vintage Stanley, be used sans hook. The hook is only recommended for advanced users.
I have a memory that the LN blade originally came with a 60-degree bevel. At any rate, I reground it to 45 degrees in line with the blade in my Stanley #80 scraper plane. In recent years I have been grinding the primary bevel at 30 degrees. This creates an edge with greater penetration (i.e. “sharper”) and I believe that the steel (probably 01) would not be compromised compared to a 45-degree primary bevel.
I have not used the Lee Valley/Veritas #112, which has the capacity for a thick and a thin blade. I would be interested to hear the opinion of those that have used both blades.
My interest in a thin blade was re-kindled recently by the writings of [Paul Hamler, who probably knows more about scraper plane design that anyone else. If Paul says that he prefers a thin blade to a thick one, then they must be better …
http://hamlertools.blogspot.com/
So still struggling with ‘flu and lacking the concentration for a long project (such as the Tallboy that is now languishing in the corner), I decided to instead spend this afternoon answering this question for myself.
I needed a thin blade, so decided to make one out of a piece of saw blade that was the right size and hardness. The big belt sander is a great tool – hardly ever been touched by wood, I use it for grinding metal. The steel was flattened, and both blades were honed up to 8000 on a Shapton waterstone. The thin blade was given a primary bevel of 35 degrees while the LN continued with its 30 degrees. Both blades were given a fine hook with a thin carbide rod I use as a burnisher.
The thin blade:
Behind the blade is my carbide burnisher. In front of this is the glass setting plate I use for woodies and scraper planes.
Here are the two blades alongside one another:
The thin blade measured 1.25mm or 3/64” thick. The LN measured 2.6mm or 7/64” thick.
Shavings
I started with the thin blade in the #112. This was a surprise on two scores: firstly, I was not prepared for the high-pitched screeeeeech it made as it moved across the wood. Good grief! Secondly, the thin blade worked exceptionally well.
Here is a picture of it scraping a board of Tasmanian Oak…
… and another on Jarrah …
The thin blade had a “soft” feel – as if it was flexing as it scraped. It also appeared to feel twitchy, that is, it required more effort to keep it straight. It seemed to want to move around the board.
By contrast, the thicker LN blade required a little more force to push, but it was silent (!) and it had a firm, purposeful feel to it.
Here is the LN blade scraping the same Tasmanian Oak board. The shavings are near identical to the previous effort …
Both blades left the wood smooth as a baby’s watsit.
By now I was having fun with the LN blade. Here is a long shaving …
…and a shaving from hard Rock Maple …
Summing up
Both thin and thick blades worked well. The thin blade surprised me just how well it produced shavings and the great finish it left. But I could not live with the sound it made – worse than a power router! Happily, the thick LN blade performed as well, or better, and did so effortlessly. I think that I will stay with it.
Regards from Perth
Derek
Blades for the #112 are ground in the same way as bench plane blades. LN suggests that their model, which is the same design as the vintage Stanley, be used sans hook. The hook is only recommended for advanced users.
I have a memory that the LN blade originally came with a 60-degree bevel. At any rate, I reground it to 45 degrees in line with the blade in my Stanley #80 scraper plane. In recent years I have been grinding the primary bevel at 30 degrees. This creates an edge with greater penetration (i.e. “sharper”) and I believe that the steel (probably 01) would not be compromised compared to a 45-degree primary bevel.
I have not used the Lee Valley/Veritas #112, which has the capacity for a thick and a thin blade. I would be interested to hear the opinion of those that have used both blades.
My interest in a thin blade was re-kindled recently by the writings of [Paul Hamler, who probably knows more about scraper plane design that anyone else. If Paul says that he prefers a thin blade to a thick one, then they must be better …
http://hamlertools.blogspot.com/
So still struggling with ‘flu and lacking the concentration for a long project (such as the Tallboy that is now languishing in the corner), I decided to instead spend this afternoon answering this question for myself.
I needed a thin blade, so decided to make one out of a piece of saw blade that was the right size and hardness. The big belt sander is a great tool – hardly ever been touched by wood, I use it for grinding metal. The steel was flattened, and both blades were honed up to 8000 on a Shapton waterstone. The thin blade was given a primary bevel of 35 degrees while the LN continued with its 30 degrees. Both blades were given a fine hook with a thin carbide rod I use as a burnisher.
The thin blade:
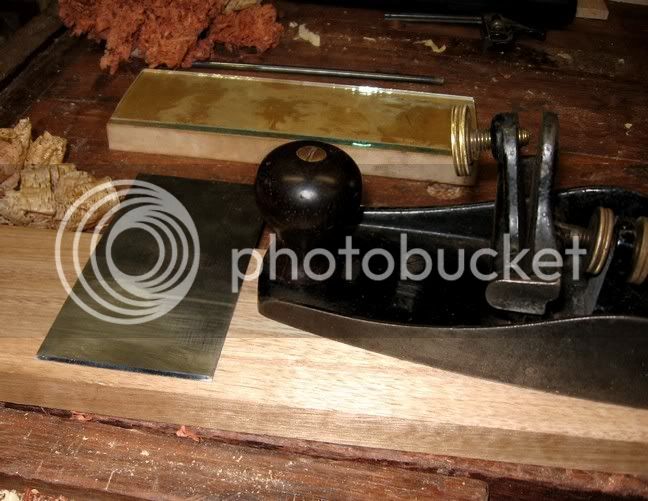
Behind the blade is my carbide burnisher. In front of this is the glass setting plate I use for woodies and scraper planes.
Here are the two blades alongside one another:
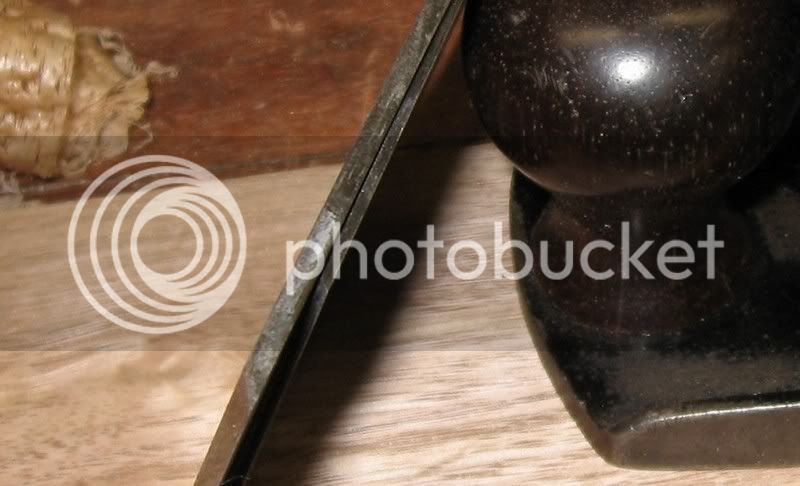
The thin blade measured 1.25mm or 3/64” thick. The LN measured 2.6mm or 7/64” thick.
Shavings
I started with the thin blade in the #112. This was a surprise on two scores: firstly, I was not prepared for the high-pitched screeeeeech it made as it moved across the wood. Good grief! Secondly, the thin blade worked exceptionally well.
Here is a picture of it scraping a board of Tasmanian Oak…
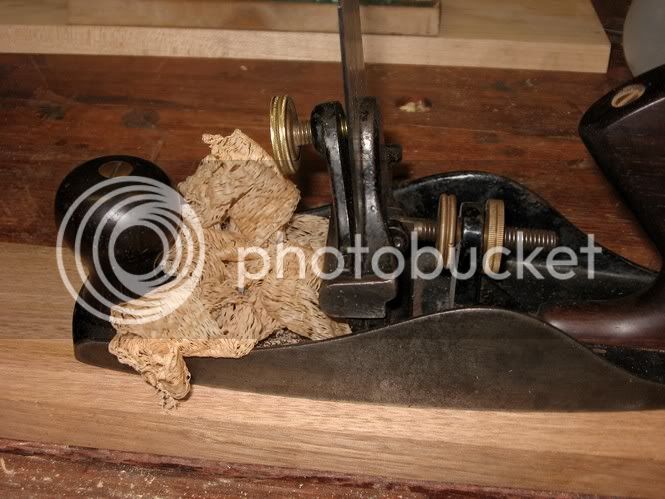
… and another on Jarrah …
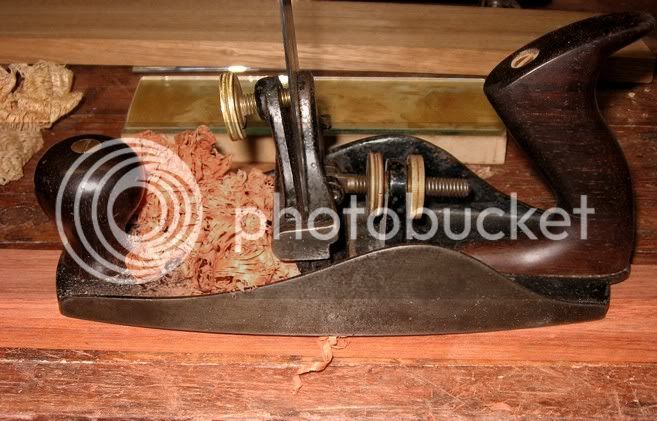
The thin blade had a “soft” feel – as if it was flexing as it scraped. It also appeared to feel twitchy, that is, it required more effort to keep it straight. It seemed to want to move around the board.
By contrast, the thicker LN blade required a little more force to push, but it was silent (!) and it had a firm, purposeful feel to it.
Here is the LN blade scraping the same Tasmanian Oak board. The shavings are near identical to the previous effort …

Both blades left the wood smooth as a baby’s watsit.
By now I was having fun with the LN blade. Here is a long shaving …
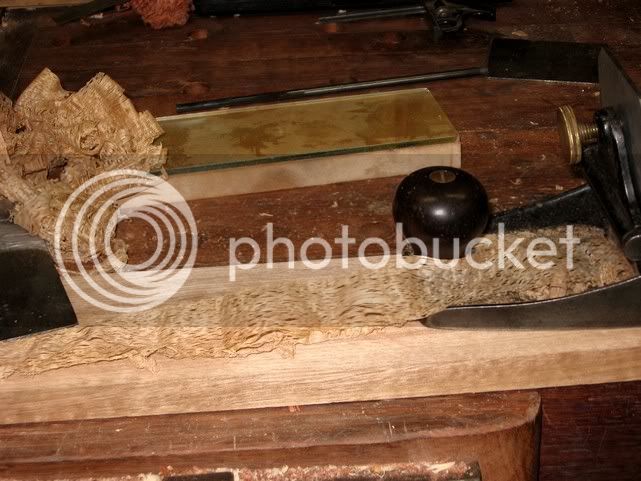
…and a shaving from hard Rock Maple …
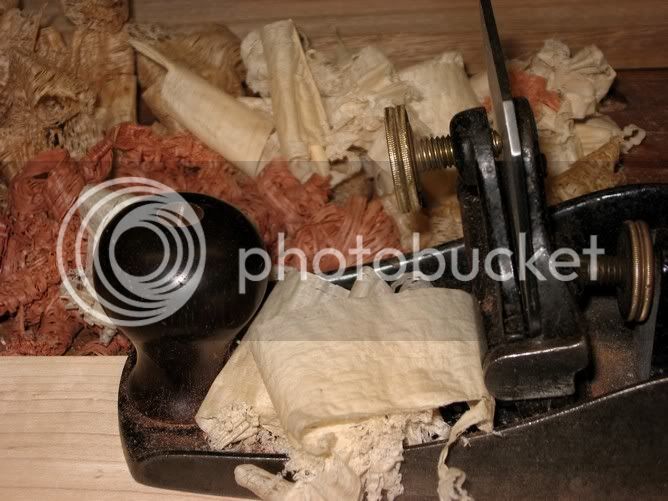
Summing up
Both thin and thick blades worked well. The thin blade surprised me just how well it produced shavings and the great finish it left. But I could not live with the sound it made – worse than a power router! Happily, the thick LN blade performed as well, or better, and did so effortlessly. I think that I will stay with it.
Regards from Perth
Derek