Please comment, helpful critism and advice is most welcome.
Just to give little background.Currently i do home refurbishments, anything from kitchens bathrooms to re-roofs but not a lot of it.(I work alone most the time.) On the carpentry side i generally only do the odd door or window, fitted cupboards etc. At the moment we moved in a new home so i'm temporily working out of a shed.
Now lets get on with it. First off the reclaimed pine i used came from a reclaim yard in Nottingham, 200 yr old Columbia redwood joists . I bought 3"x1" and 2"x1" PAR at the 30p a foot and that was the actual finished size, so nice and chunky. I also bought jointed 2' wide boards in 9mm and 20mm thickness for shelves and panels. The yard makes them up with RF glue and speed thickneser. Quality was better than expected.
Few pics of the Reclaim yard
Just to give little background.Currently i do home refurbishments, anything from kitchens bathrooms to re-roofs but not a lot of it.(I work alone most the time.) On the carpentry side i generally only do the odd door or window, fitted cupboards etc. At the moment we moved in a new home so i'm temporily working out of a shed.
Now lets get on with it. First off the reclaimed pine i used came from a reclaim yard in Nottingham, 200 yr old Columbia redwood joists . I bought 3"x1" and 2"x1" PAR at the 30p a foot and that was the actual finished size, so nice and chunky. I also bought jointed 2' wide boards in 9mm and 20mm thickness for shelves and panels. The yard makes them up with RF glue and speed thickneser. Quality was better than expected.
Few pics of the Reclaim yard
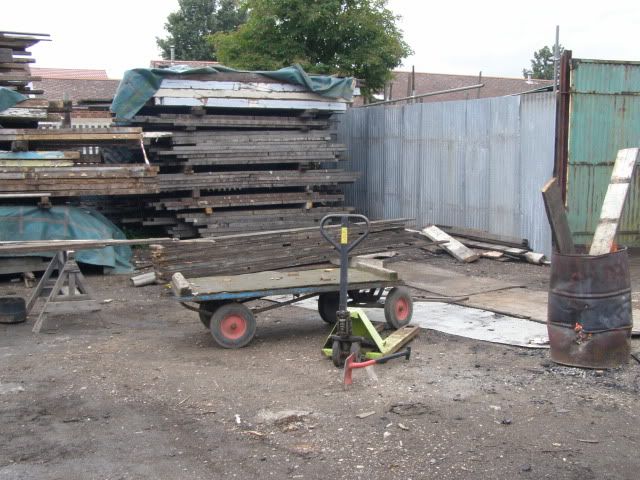
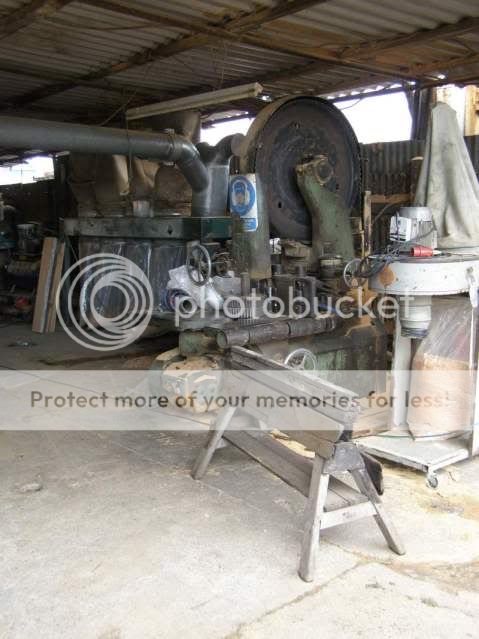
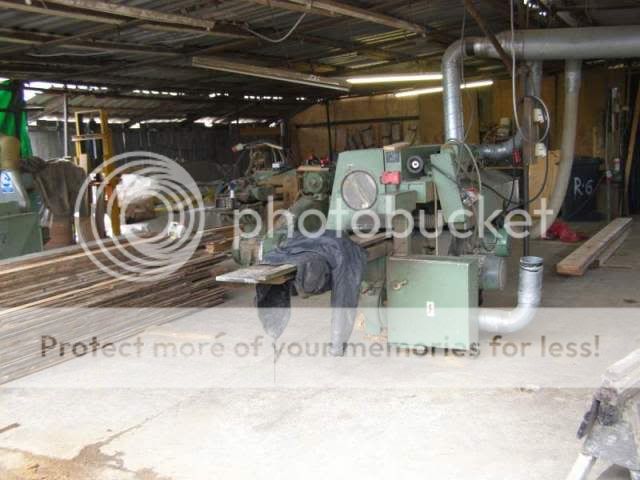