marknotts
Established Member
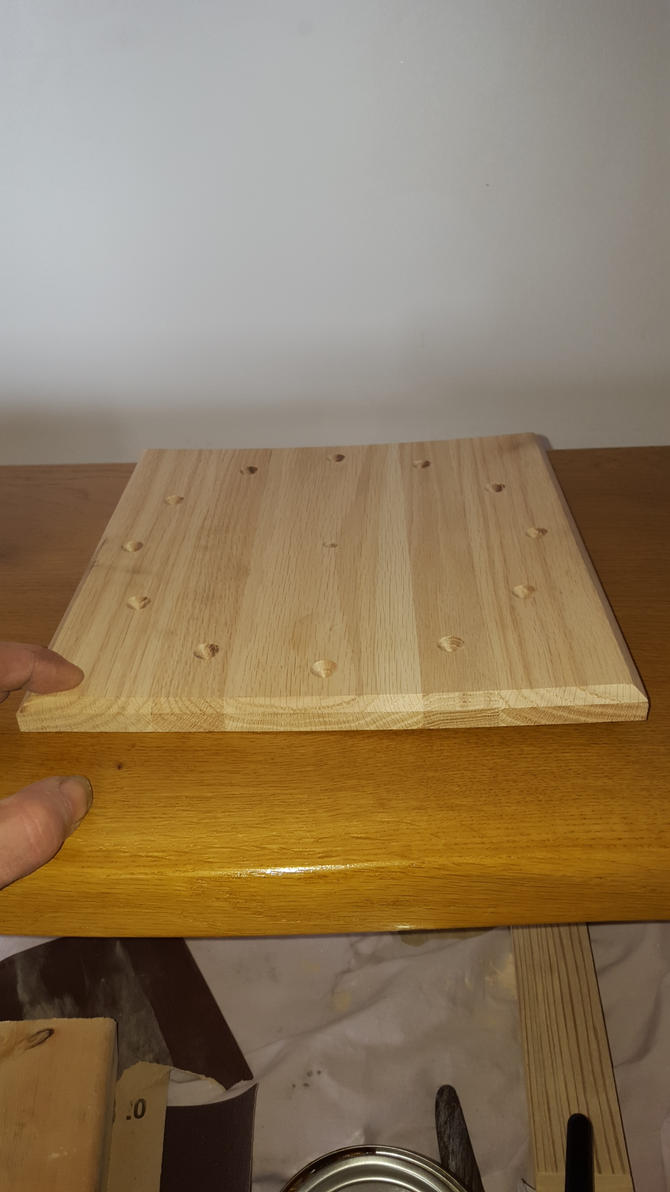
As you can see there is severe warp, this is a clock face which i was going to finish then fix the clock movement today ready for my mums birthday, now im going to have to remake the damn thing..
The process I followed was to cut down the oak offcuts which i aquired a while back into length and width, then shaved the bandsaw marks off 1 face on all lengths.
Then I edge amd face jointed on a router table and glued up the panel good faces down.
This panel was left for a day then clamps off and rested for a lot longer than planned, about a month!
Yesterday as i dont have a 12" jointer or even any jointer or thicknesser I jigged up my router with a wide 1/2" intumescent? Bit to skim the good face then flipped and skimmed the bad face, this took the thickness down from 23mm to 15mm.
After that i used the router table and a chissel to put the profile around the face and chisel out a rebate to the rear so the movement seats in deep enough for the hand spindle to poke out the front, plus routered the indents for the hour marks.
Then comes the problem, the face was dead flat and i moved it from the shed into the nice warm house overnight as i was danish oiling today, the pic is the result of only 12h indoors!
Now I know the heat and humidity change from the wood being in the shed for about 3 months over winter then having a shock of 22c indoors is enough to make millions of little wood fiber toes and fingers uncurl and relax!! , but wood has to come out of a workshop and indoors at some point so what do I have to do to stop this happening?
Sorry about the long winded post but I added the full process so anyone reading it can advise me at anypoint of the process instead of guessing what I did.
Mark.