Dissolve
Established Member
Hello,
I've decided it's worth my while making a decent auxilary table for my pillar drill. It's a fobco star bench drill, should be big enough for all I'll ever need, but I would use a fence quite a bit and it's much easier to do this with a table like this:
I have T-track, star knobs, M8 bolts and some spare formica laminate that will be the table face.
Would MDF be the best material for the job? I am currently thinking of using two 12mm sheets of MDF laminated together and countersink some drywall screws whilst sandwiched between two boards to hopefully obtain a flat surface after gluing!
I will be recessing M8 bolts through the table with wing nuts underneath and routing for T track to clamp a fence to.
Would I be better off laminating my MDF then applying the formica laminate before drilling/routing/recessing all my hardware? I suppose if I laminate the surface first then all my recessed bolts and t track channels can then be referenced from the finished surface?
Thanks!
I've decided it's worth my while making a decent auxilary table for my pillar drill. It's a fobco star bench drill, should be big enough for all I'll ever need, but I would use a fence quite a bit and it's much easier to do this with a table like this:
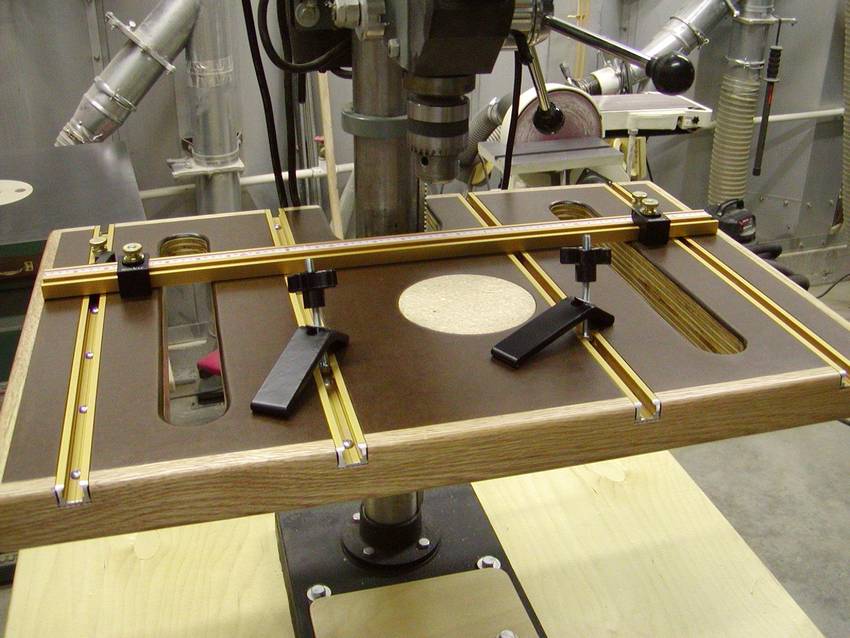
I have T-track, star knobs, M8 bolts and some spare formica laminate that will be the table face.
Would MDF be the best material for the job? I am currently thinking of using two 12mm sheets of MDF laminated together and countersink some drywall screws whilst sandwiched between two boards to hopefully obtain a flat surface after gluing!
I will be recessing M8 bolts through the table with wing nuts underneath and routing for T track to clamp a fence to.
Would I be better off laminating my MDF then applying the formica laminate before drilling/routing/recessing all my hardware? I suppose if I laminate the surface first then all my recessed bolts and t track channels can then be referenced from the finished surface?
Thanks!