Back last winter I was fortunate enough to obtain a small amount of Olive Ash, some of it very highly figured, including the piece these two boxes came from.
Made in the style of George Watkins' boxes ("Cornucopia" of this forum), they are finished with Shellac sanding sealer and buffed with a three wheel buffing system to a high gloss, though the images do not capture this too well.
Churn style
A more Oval style.
All comments welcome!
Made in the style of George Watkins' boxes ("Cornucopia" of this forum), they are finished with Shellac sanding sealer and buffed with a three wheel buffing system to a high gloss, though the images do not capture this too well.
Churn style
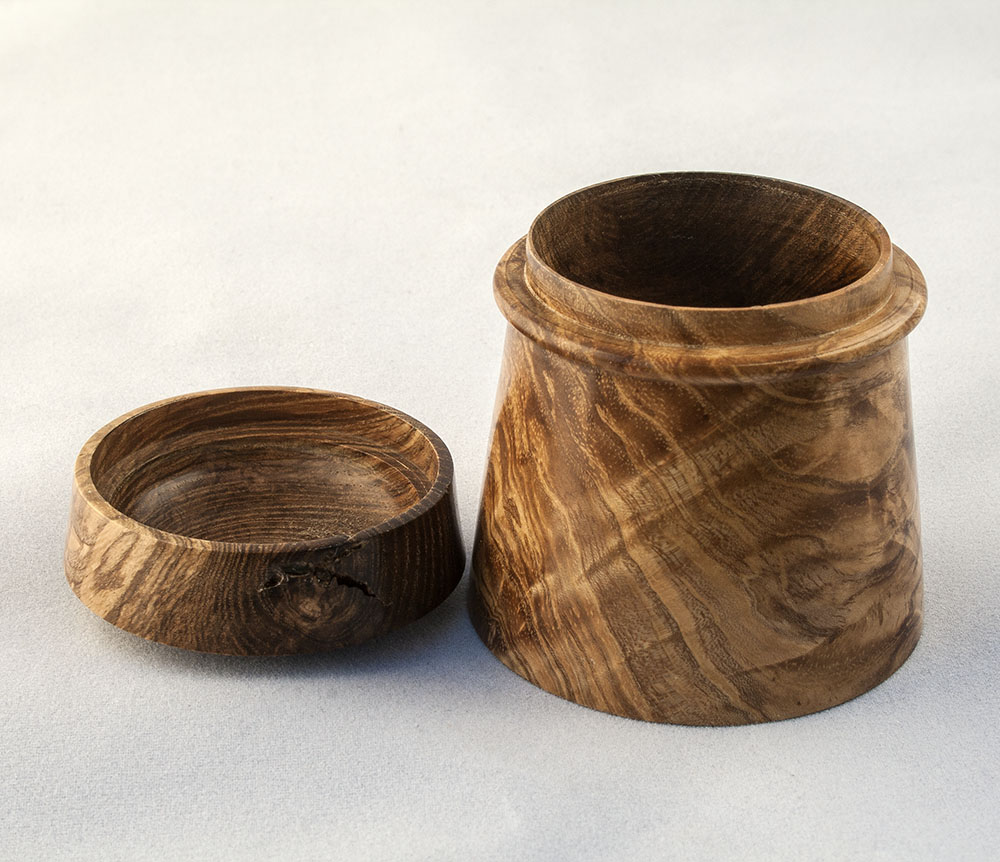
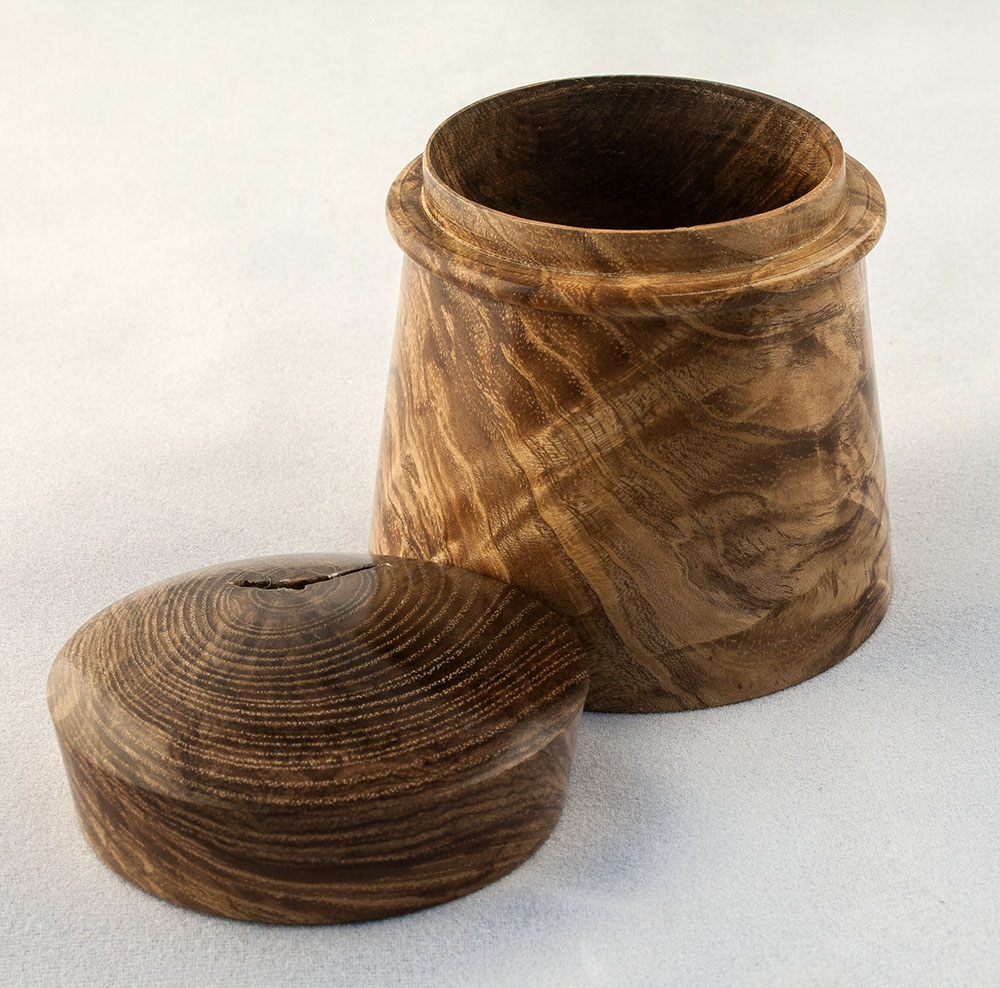
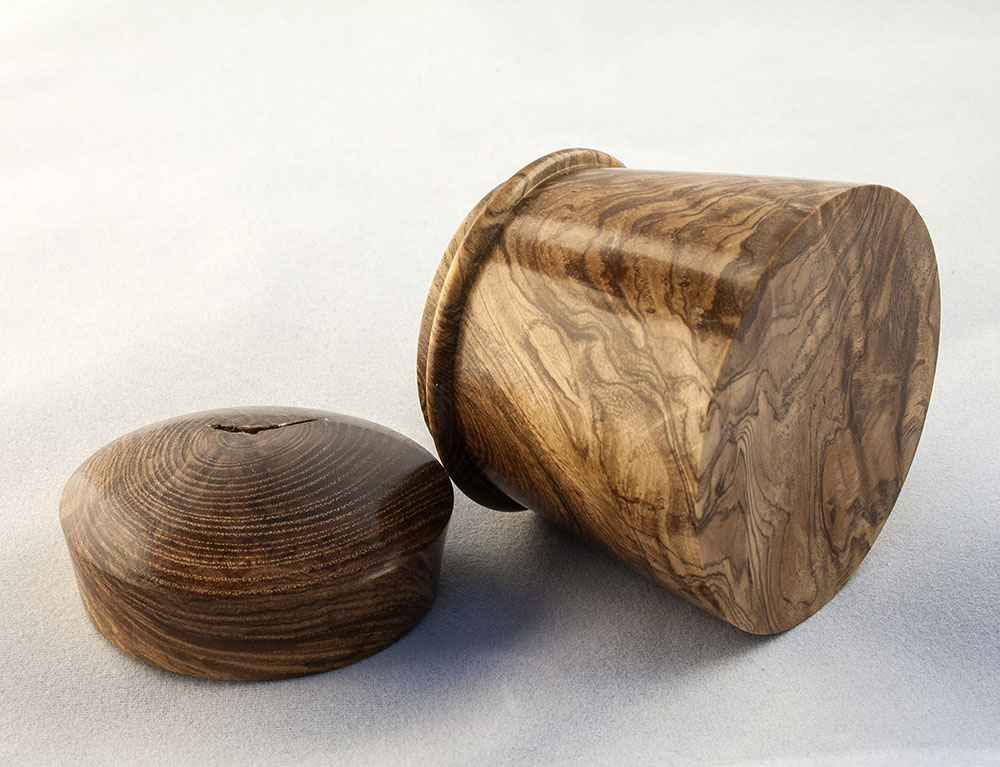
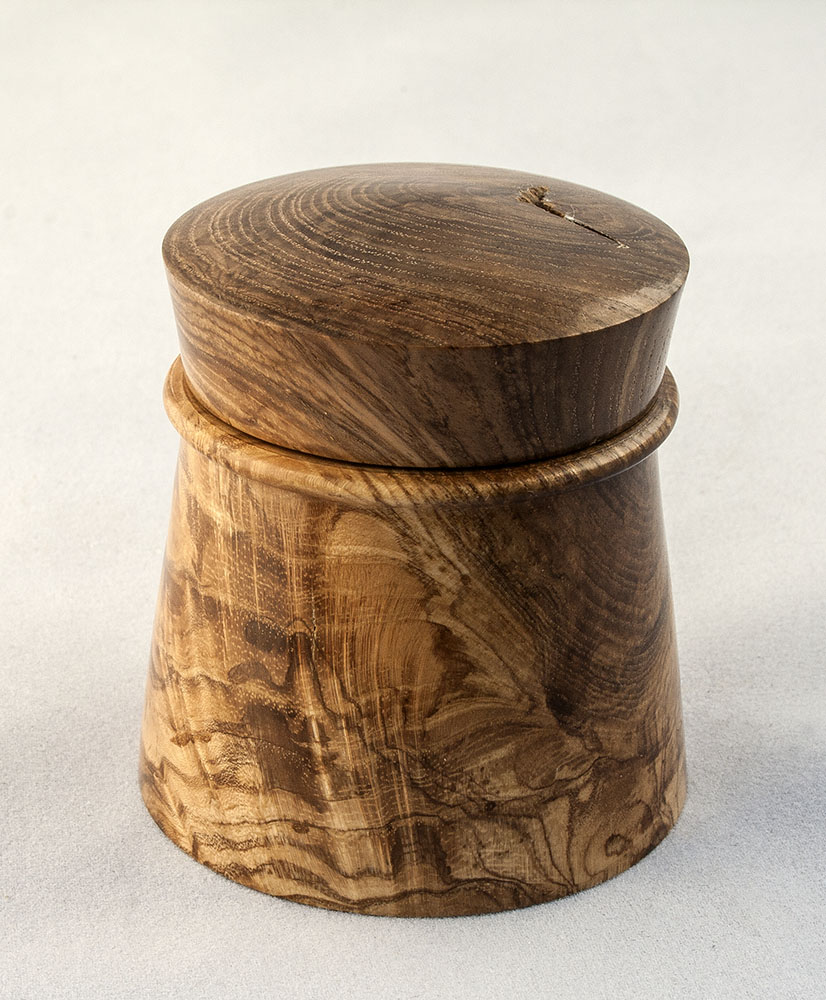
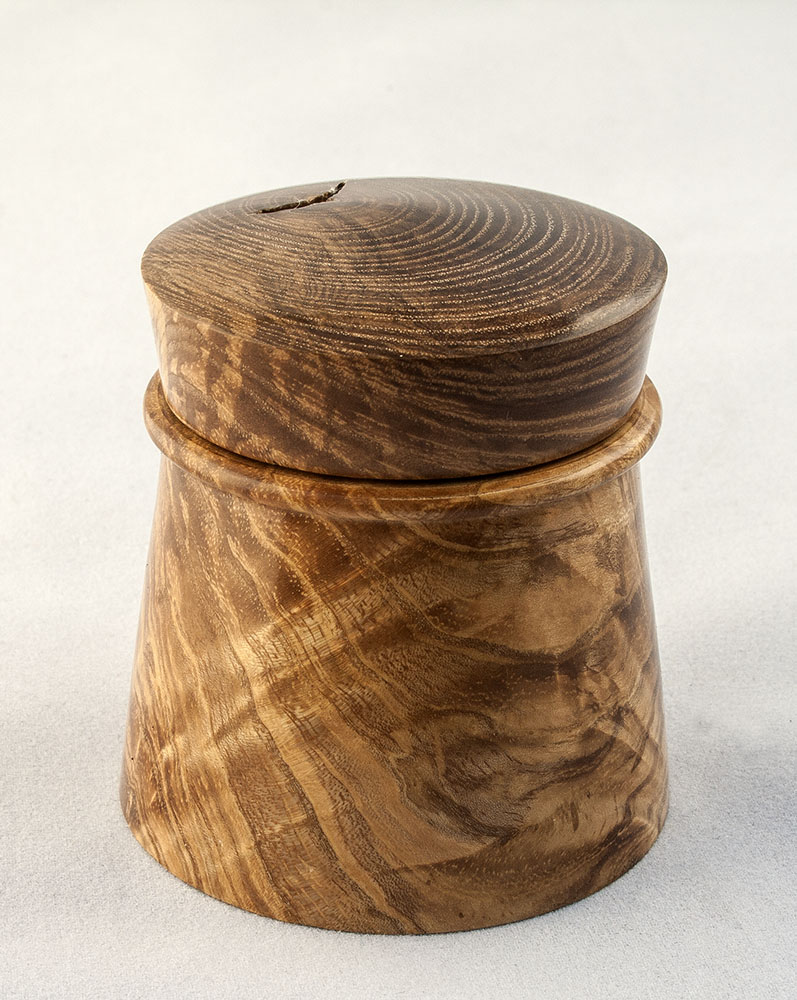
A more Oval style.
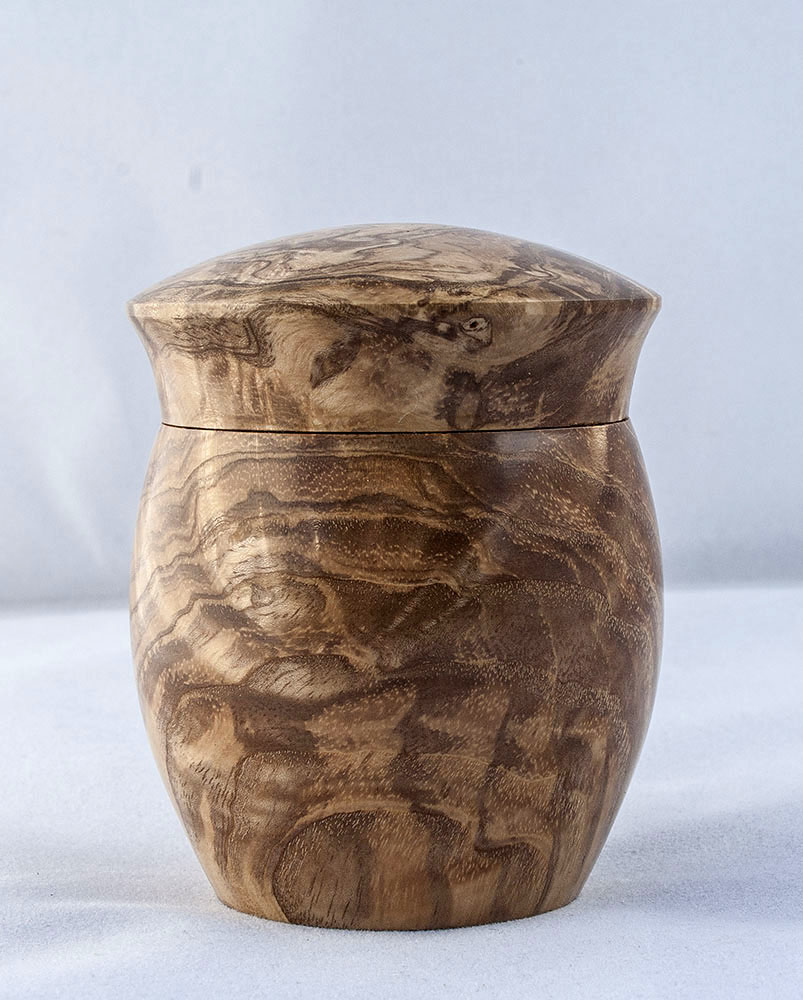

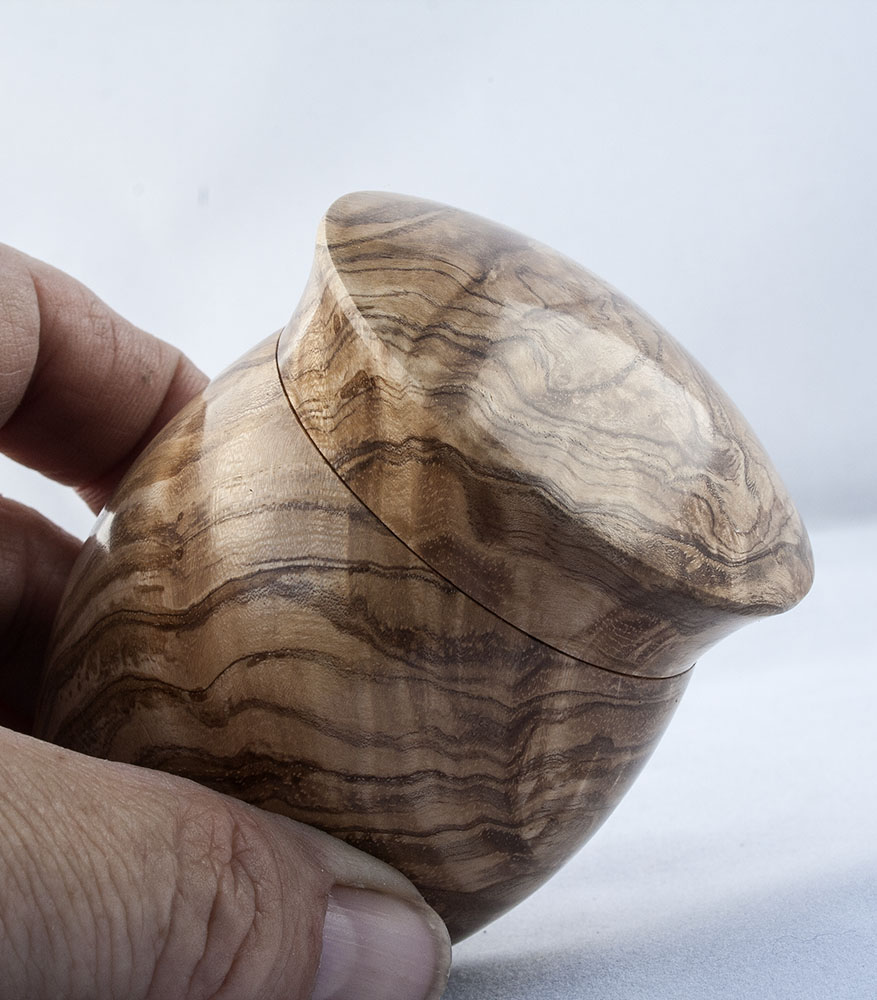
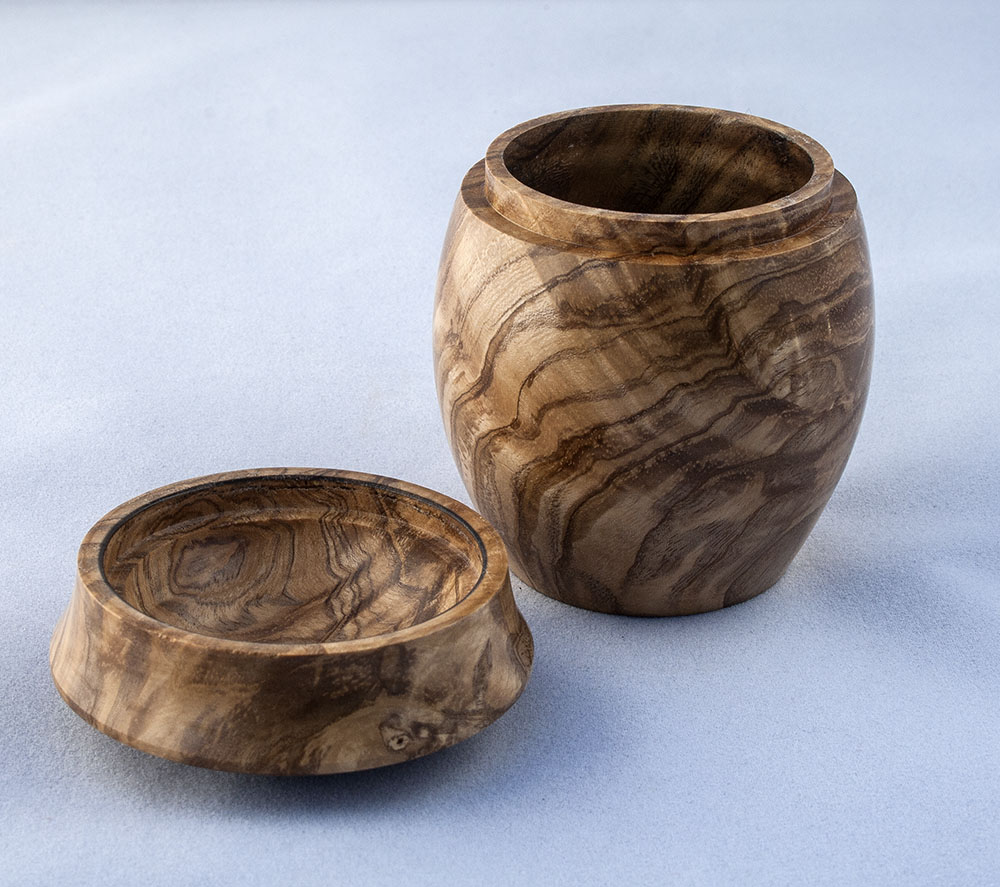
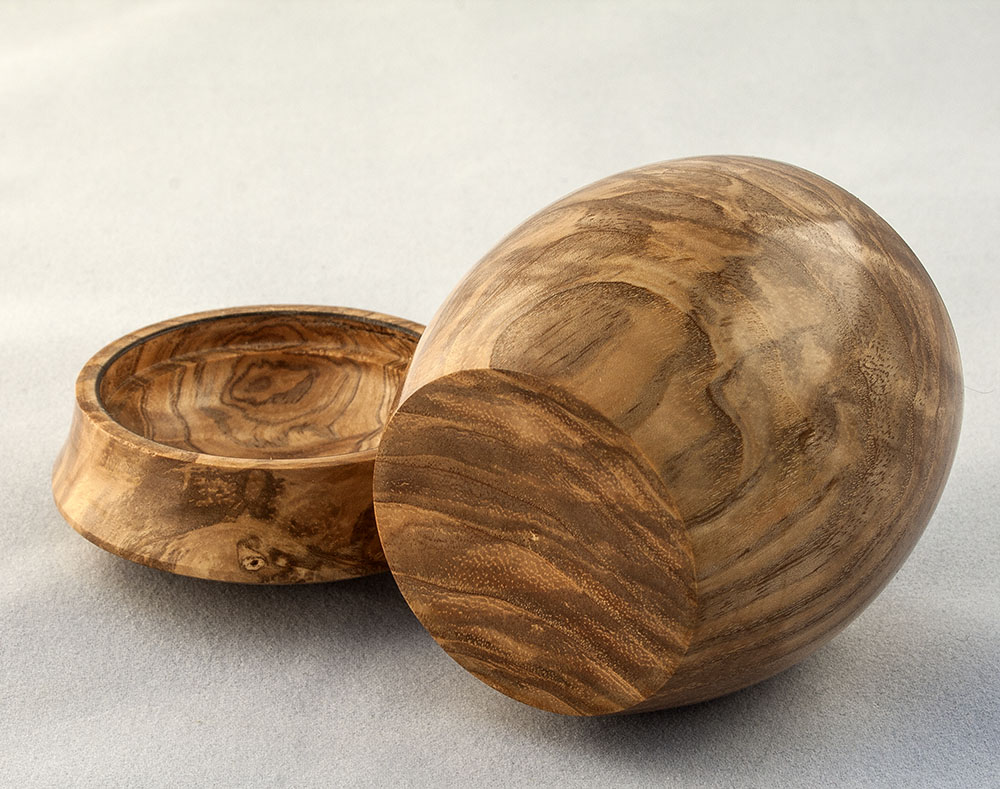
All comments welcome!