Yesterday I spent a fantastic day with Richard Findley having tuition in woodturning. It was for my birthday which was a couple of weeks ago.
Spent the morning practicing beads and coves on his big Wadkin. Being a lady I had to stand on a little platform so I could use it comfortably! Richard is well prepared
Started off with the basics, roughing gouge and planing cuts with the skew on round timber which indicated that I'd previously been using it slightly wrong having too much emphasis on the short point rather than cutting with the lower third of the skew. Then moved onto roughing a square block of timber and then started on beads using the spindle gouge. It is something I've previously struggled with so it was good to learn how to do beads and coves properly. I did take a few attempts to get the shape and movement of the tool right and tended to leave a bit of a point but with further practice I'll get it mastered now I know what to do. Beads with the skew I found slightly easier and my attempts were a bit better.
Moved onto coves with the spindle gouge where I had a habit of making a bit of a flat bottomed 'U' but again, with practice I'll get there and the last was much improved over the first!
Richard had a look at the tools I'd brought before lunch. I had mini turning tools and a roughing gouge but I also have a few full size tools inherited from my great uncle when he died. Unfortunately the two spindle gouges have bent shafts and there was a home made tool of unknown purpose which we left, but the skews and parting tool were ok and so Richard taught me how to sharpen all the different tools on the grinder which was invaluable and also showed me how to put a fingernail grind on the spindle gouge so the wings don't catch. My little mini tools needed a very light touch and have too short a shaft for the standard approach so Richard did those.
After a toastie at the cafe round the corner the next couple of hours were spent making my project of choice which was a small lidded box. Richard suggested a simple shape and went through the process and it turned something that seemed very complicated into a fairly straightforward process. Learnt a few tips and tricks along the way, like how to size the wood initially so you rough it down accurately and then using callipers and a parting tool to make the spigots for the chuck etc.
I finished it a bit early so had another go at hollowing with the spindle gouge in a bit of Oak to try and get a smoother action and also tried using a couple of different hollowing tools.
Lastly I asked about doing a shoulder on something like a bed post so had a go at a square and round one of those then by that point I'd reached information storage capacity for one day
Richard is a great teacher and after a quick demo of the tool and process I did everything else myself with his guidance. He watches so when you do make a mistake he knows why and can show you how to correct it and that's invaluable in the learning process. It's such a great feeling when you do get it right and you can tell by the sound and the finish that you've had good tool control.
If anyone is thinking about getting some tuition then I would fully recommend booking a day with Richard.
First photo shows (from bottom to top):
Initial beads with the spindle gouge - Richard's is on the far left and I started on the far right, narrow one done last.
Beads with the skew - again, Richard's is the one on the far left and mine are the rest - narrow one done last
Coves with the spindle gouge - Richard's on the left again.
My lidded box made from Sapele. Unfinished apart from sanding and nyweb pad at the end. It's about 3" high.
Shot to show the bottom of the box so shallow depth of field here...
Spent the morning practicing beads and coves on his big Wadkin. Being a lady I had to stand on a little platform so I could use it comfortably! Richard is well prepared
Started off with the basics, roughing gouge and planing cuts with the skew on round timber which indicated that I'd previously been using it slightly wrong having too much emphasis on the short point rather than cutting with the lower third of the skew. Then moved onto roughing a square block of timber and then started on beads using the spindle gouge. It is something I've previously struggled with so it was good to learn how to do beads and coves properly. I did take a few attempts to get the shape and movement of the tool right and tended to leave a bit of a point but with further practice I'll get it mastered now I know what to do. Beads with the skew I found slightly easier and my attempts were a bit better.
Moved onto coves with the spindle gouge where I had a habit of making a bit of a flat bottomed 'U' but again, with practice I'll get there and the last was much improved over the first!
Richard had a look at the tools I'd brought before lunch. I had mini turning tools and a roughing gouge but I also have a few full size tools inherited from my great uncle when he died. Unfortunately the two spindle gouges have bent shafts and there was a home made tool of unknown purpose which we left, but the skews and parting tool were ok and so Richard taught me how to sharpen all the different tools on the grinder which was invaluable and also showed me how to put a fingernail grind on the spindle gouge so the wings don't catch. My little mini tools needed a very light touch and have too short a shaft for the standard approach so Richard did those.
After a toastie at the cafe round the corner the next couple of hours were spent making my project of choice which was a small lidded box. Richard suggested a simple shape and went through the process and it turned something that seemed very complicated into a fairly straightforward process. Learnt a few tips and tricks along the way, like how to size the wood initially so you rough it down accurately and then using callipers and a parting tool to make the spigots for the chuck etc.
I finished it a bit early so had another go at hollowing with the spindle gouge in a bit of Oak to try and get a smoother action and also tried using a couple of different hollowing tools.
Lastly I asked about doing a shoulder on something like a bed post so had a go at a square and round one of those then by that point I'd reached information storage capacity for one day
Richard is a great teacher and after a quick demo of the tool and process I did everything else myself with his guidance. He watches so when you do make a mistake he knows why and can show you how to correct it and that's invaluable in the learning process. It's such a great feeling when you do get it right and you can tell by the sound and the finish that you've had good tool control.
If anyone is thinking about getting some tuition then I would fully recommend booking a day with Richard.
First photo shows (from bottom to top):
Initial beads with the spindle gouge - Richard's is on the far left and I started on the far right, narrow one done last.
Beads with the skew - again, Richard's is the one on the far left and mine are the rest - narrow one done last
Coves with the spindle gouge - Richard's on the left again.
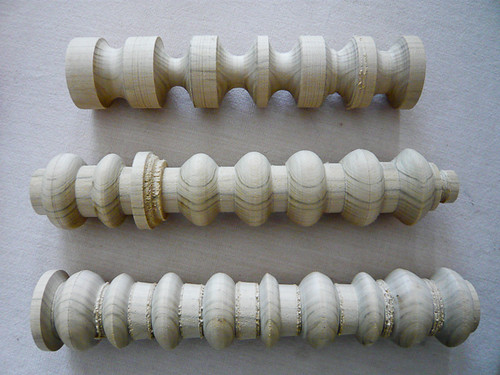
My lidded box made from Sapele. Unfinished apart from sanding and nyweb pad at the end. It's about 3" high.
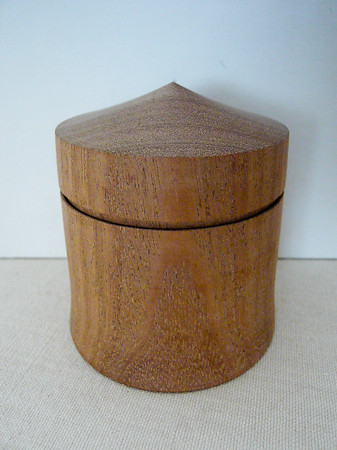
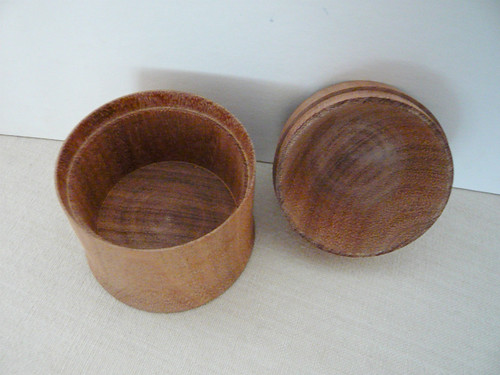
Shot to show the bottom of the box so shallow depth of field here...
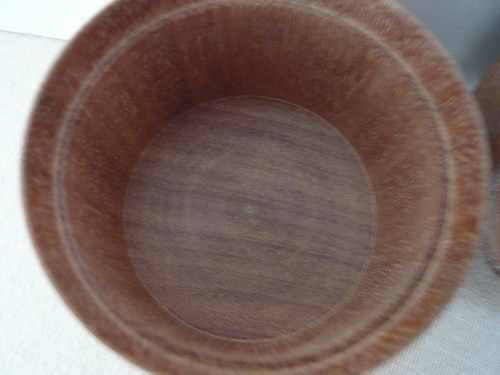