Nigel Taylor
Established Member
The black paint needs a mention. I needed a paint that could work at a high temperature for the chimney and the firebox.
I found this coal black paint, initially I thought this description was really describing the colour. However, this paint is designed for painting your fake coal on the gas fire....really.
I had a quick search and saw that this paint is also used for stoves, so thought I would give it a go on the chimney and firebox. I've now fired the boiler a few times and this black finish is growing on me.
So, if you need a high temperature black paint then this paint from Rapide Products is rather good and cost me just £3.99 at a small hardware store.
I found this coal black paint, initially I thought this description was really describing the colour. However, this paint is designed for painting your fake coal on the gas fire....really.
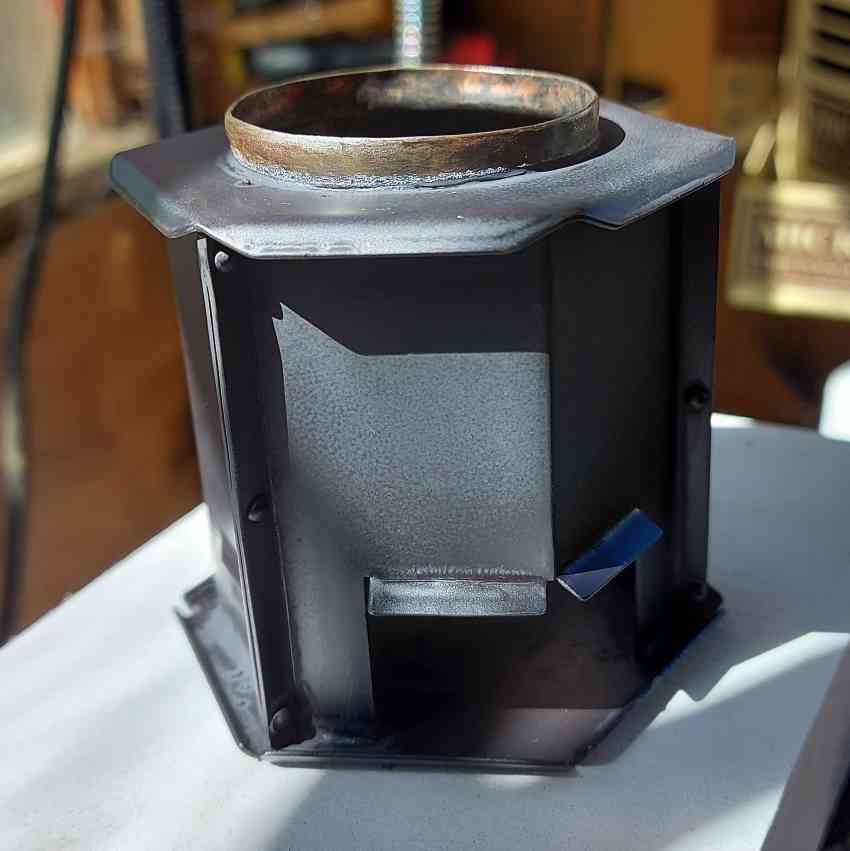
I had a quick search and saw that this paint is also used for stoves, so thought I would give it a go on the chimney and firebox. I've now fired the boiler a few times and this black finish is growing on me.
So, if you need a high temperature black paint then this paint from Rapide Products is rather good and cost me just £3.99 at a small hardware store.