Mike Wingate
Established Member
Dozuki 240 mm saw from Rutlands (offer) with UHMWPE spine stiffener and depth stop. Ply and UHMWPE saw guide, Bakelite height shims. Lexan CAD CAM Laser cut slotting template, St.Steel locator pin (or Stanley blade in slot for copying precut f/b slots) and 15" Purpleheart Ukulele fingerboard blank. Worked well.
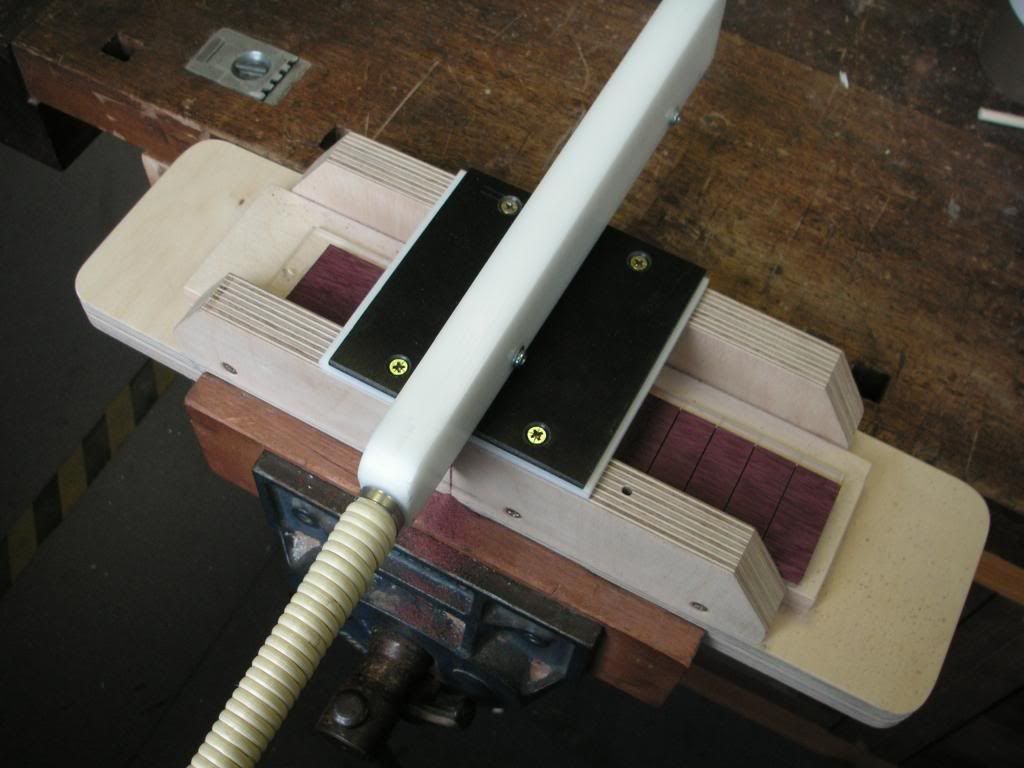
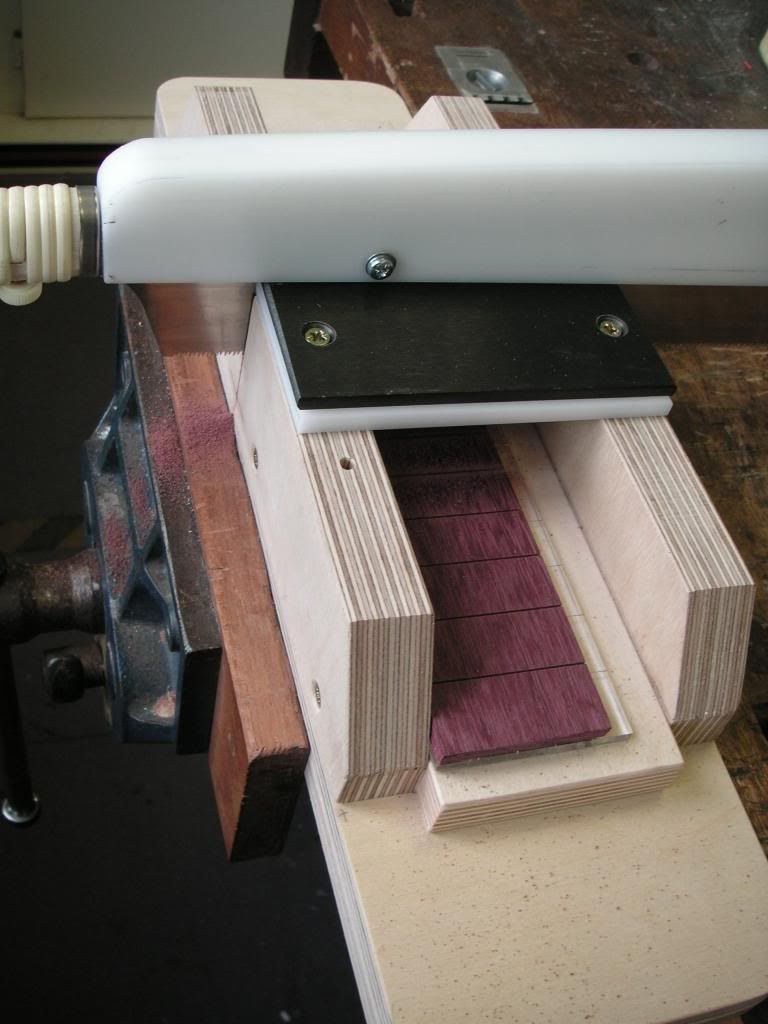