Myfordman
AKA 9Fingers
want to make a quantity of the part shown in the drawing from stock brass angle 10 x10 x1.5 or imperial equivalent.
Where suppliers state the type of brass angle they tend to quote CZ121 which looks to be formulated for best machining quality rather than bending.
I need to start from stock material as I don't have the equipment needed to form the angle from sheet stock which has optimum bending qualities.
My question is how readily can 1.5mm thick CZ121 be formed to a 5mm radius on a scale from "piece of cake why even ask" to " you have got to be joking mate"
Also will heat be needed - desirable - helpful - essential etc
This will affect how I design and build the bending tool.
n.b. The overall length will be about 300mm. The drawing just shows this particular formed feature.
TIA
Bob
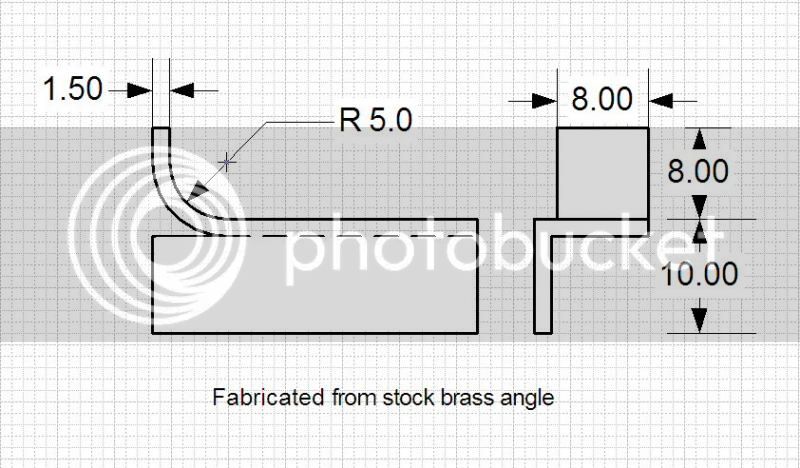
Where suppliers state the type of brass angle they tend to quote CZ121 which looks to be formulated for best machining quality rather than bending.
I need to start from stock material as I don't have the equipment needed to form the angle from sheet stock which has optimum bending qualities.
My question is how readily can 1.5mm thick CZ121 be formed to a 5mm radius on a scale from "piece of cake why even ask" to " you have got to be joking mate"
Also will heat be needed - desirable - helpful - essential etc
This will affect how I design and build the bending tool.
n.b. The overall length will be about 300mm. The drawing just shows this particular formed feature.
TIA
Bob