Aragorn
Established Member
Ooo. Am I inaugerating this new section??
As a finishing touch to the kitchen project I have recently been working on, I am making a free-standing butcher’s block on a mobile trolley in oak and black walnut.
The piece is to have a variety of functions: general purpose chopping board; nice looking piece of furniture; additional storage space; mobile trolley for outdoor/BBQ use.
Since there’s been a thread recently about plans, I’ve included what I tend to do.
(click thumbnails for larger images)
I make up drawings like this in CorelDRAW, but they tend to change during the construction. I don’t put every little detail on the drawing as I use the computer and a cut-list as well for exact sizes.
This post is the construction of the chopping block, and the next post will be the rest of the trolley (when I finish it!)
Due to the desired size and footprint of the trolley, I wanted to make up a prototype to get an idea of how top-heavy it would be. For this, I used the actual oak legs and clamped them together with pine cut to the size of the rails.
I had ideas for incorporating hidden “outriggers” if it wasn’t very stable, but after crashing myself into the prototype a few times, I realised this wasn’t going to be necessary. This was going to be a heavy stable piece!
Here’s the timber for the chopping block: American black walnut, bought PAR from British Hardwoods.
I’ve cut it to rough length, then I need to surface plane it, and thickness it to an exact rectangle of 41x43mm. It is vital to make sure the surfaces are 90º to each other, so that the final block has an even look to the endgrain checks. The measurement of 41mm means that I end up with my desired dimensions with all the squares the same size. The dimension of 43mm allows me some lee-way for planing after the glue-up.
I’m gluing the lengths together in two batches. This is so that I can put each half through the thicknesser and dimension down to just over 41mm. At this point the endgrain blocks are nearly square. I carefully glued my two halves together, making sure they meet really well.
When the glue’s gone off, I make a final sand of the board, levelling off any high-points, and bringing the dimension down to 41mm. This gives me a board made up of 41x41mm lengths, flat and even.
Next, I need to crosscut the board into slices 53mm thick. This is going to be the height of the chopping block. I really want to get this accurate, as I don’t much fancy having to level off a 700x450mm block of endgrain that’s all higgledy-piggledy.
The easiest way to do this would be to set the rip fence on the table saw to 53mm and cut away, but I felt I would get burn marks and sawtooth marks, so I opted for using the Festool plunge saw.
I made a simple jig that holds the wood, and guides the saw.
Here I’ve trimmed the end of the board square to the sides. Next I attach the guide rail:
The length of pine nearest us is the end stop. The other pine lengths are exactly 90º to it and are snug to the width of the board, so that they hold it firmly. They are also the same height as the board.
The Festool guide rail is screwed into the pine batons at the right distance from the endstop so that when I push the walnut up to the stop and make a cut with the saw, the offcut is exactly 53mm wide.
So, I slide the walnut up to the stop and make a cut, put the offcut aside and repeat this process over and over again.
Here’s the first few slices straight out of the jig. I’m really pleased with the finish, and am just keeping everything crossed that this works!
And all cut up:
Thankfully it did work, I didn’t run out of walnut before completing the cuts and each slice is within a good tolerance. Turned on end, I get my first glimpse of how this is going to look, and get a feel for the size of the chopping block. I hope my customers like cooking!
I could just glue this up now and I’d have a nice butcher’s block, but I want to insert some non-endgrain blocks into the board to use as fixing points to the trolley that is to come. If I screwed the trolley directly into the walnut it might just rip off if it’s lifted by the board, and it would not allow for any expansion and contraction of the chopping board.
I used the Leigh FMT to cut some mortices into the relevant endgrain slices to co-ordinate with where the trolley will attach, two through each side rail and one through the rail at the back of the trolley.
Next I made up some small blocks of oak which are free to float about in the mortices. When the trolley base is screwed up into these blocks, they will allow the butcher’s block to move with the climate in all directions, and give a firm fixing for the screws. (Hopefully!)
Everything’s in place to start the glue up. I use the cutting jig again to provide a good 90º guide. When I butt the endgrain slices up to the jig I will get good alignment between the squares (I want chessboard here, not brick wall!) Can you believe I stopped halfway through to take a photo!
Here it is in the clamps. Thank heavens for Bessey’s! Here they really helped keep everything aligned.
The block came off the clamps quite well.
Sorry about the bad photo - not sure what happened here. Some sort of interference?
I spent some time with the plane taking out the high points and then sanded it smooth.
Here’s a close-up at 180 grit.
By the way, when planing an endgrain chopping block, don’t forget about tearout! The first plane swipe went straight off the edge of the board and knocked off a bit of the side. I glued it back on and it doesn’t show a bit. I was a little more careful after that!
With everything sanded back to 600 grit on all sides, it’s ready for some oil.
And here’s the finished block after 8 coats of finishing oil. (This is the underside. Do you think I’ve got Shaker blood in me?)
Some time quite soon, I’ll post the construction of the oak base.
As a finishing touch to the kitchen project I have recently been working on, I am making a free-standing butcher’s block on a mobile trolley in oak and black walnut.
The piece is to have a variety of functions: general purpose chopping board; nice looking piece of furniture; additional storage space; mobile trolley for outdoor/BBQ use.
Since there’s been a thread recently about plans, I’ve included what I tend to do.
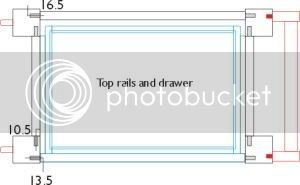
(click thumbnails for larger images)
I make up drawings like this in CorelDRAW, but they tend to change during the construction. I don’t put every little detail on the drawing as I use the computer and a cut-list as well for exact sizes.
This post is the construction of the chopping block, and the next post will be the rest of the trolley (when I finish it!)
Due to the desired size and footprint of the trolley, I wanted to make up a prototype to get an idea of how top-heavy it would be. For this, I used the actual oak legs and clamped them together with pine cut to the size of the rails.
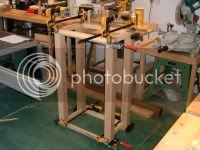
I had ideas for incorporating hidden “outriggers” if it wasn’t very stable, but after crashing myself into the prototype a few times, I realised this wasn’t going to be necessary. This was going to be a heavy stable piece!
Here’s the timber for the chopping block: American black walnut, bought PAR from British Hardwoods.
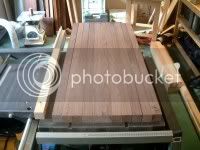
I’ve cut it to rough length, then I need to surface plane it, and thickness it to an exact rectangle of 41x43mm. It is vital to make sure the surfaces are 90º to each other, so that the final block has an even look to the endgrain checks. The measurement of 41mm means that I end up with my desired dimensions with all the squares the same size. The dimension of 43mm allows me some lee-way for planing after the glue-up.
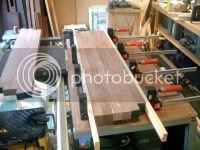
I’m gluing the lengths together in two batches. This is so that I can put each half through the thicknesser and dimension down to just over 41mm. At this point the endgrain blocks are nearly square. I carefully glued my two halves together, making sure they meet really well.
When the glue’s gone off, I make a final sand of the board, levelling off any high-points, and bringing the dimension down to 41mm. This gives me a board made up of 41x41mm lengths, flat and even.
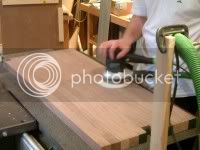
Next, I need to crosscut the board into slices 53mm thick. This is going to be the height of the chopping block. I really want to get this accurate, as I don’t much fancy having to level off a 700x450mm block of endgrain that’s all higgledy-piggledy.
The easiest way to do this would be to set the rip fence on the table saw to 53mm and cut away, but I felt I would get burn marks and sawtooth marks, so I opted for using the Festool plunge saw.
I made a simple jig that holds the wood, and guides the saw.
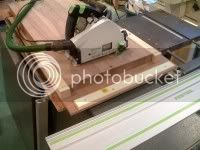
Here I’ve trimmed the end of the board square to the sides. Next I attach the guide rail:
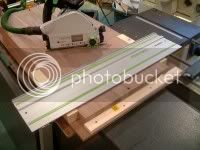
The length of pine nearest us is the end stop. The other pine lengths are exactly 90º to it and are snug to the width of the board, so that they hold it firmly. They are also the same height as the board.
The Festool guide rail is screwed into the pine batons at the right distance from the endstop so that when I push the walnut up to the stop and make a cut with the saw, the offcut is exactly 53mm wide.
So, I slide the walnut up to the stop and make a cut, put the offcut aside and repeat this process over and over again.
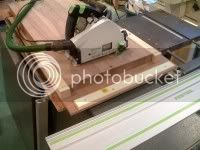
Here’s the first few slices straight out of the jig. I’m really pleased with the finish, and am just keeping everything crossed that this works!
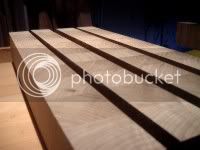
And all cut up:
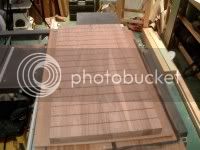
Thankfully it did work, I didn’t run out of walnut before completing the cuts and each slice is within a good tolerance. Turned on end, I get my first glimpse of how this is going to look, and get a feel for the size of the chopping block. I hope my customers like cooking!
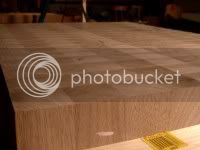
I could just glue this up now and I’d have a nice butcher’s block, but I want to insert some non-endgrain blocks into the board to use as fixing points to the trolley that is to come. If I screwed the trolley directly into the walnut it might just rip off if it’s lifted by the board, and it would not allow for any expansion and contraction of the chopping board.
I used the Leigh FMT to cut some mortices into the relevant endgrain slices to co-ordinate with where the trolley will attach, two through each side rail and one through the rail at the back of the trolley.
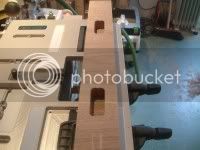
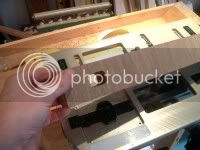
Next I made up some small blocks of oak which are free to float about in the mortices. When the trolley base is screwed up into these blocks, they will allow the butcher’s block to move with the climate in all directions, and give a firm fixing for the screws. (Hopefully!)
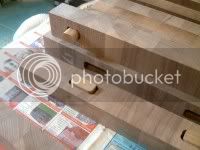
Everything’s in place to start the glue up. I use the cutting jig again to provide a good 90º guide. When I butt the endgrain slices up to the jig I will get good alignment between the squares (I want chessboard here, not brick wall!) Can you believe I stopped halfway through to take a photo!
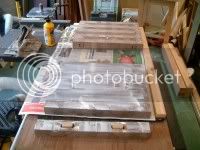
Here it is in the clamps. Thank heavens for Bessey’s! Here they really helped keep everything aligned.
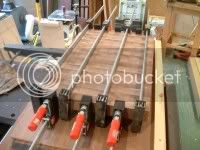
The block came off the clamps quite well.
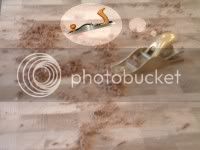
Sorry about the bad photo - not sure what happened here. Some sort of interference?
I spent some time with the plane taking out the high points and then sanded it smooth.
Here’s a close-up at 180 grit.
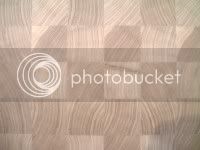
By the way, when planing an endgrain chopping block, don’t forget about tearout! The first plane swipe went straight off the edge of the board and knocked off a bit of the side. I glued it back on and it doesn’t show a bit. I was a little more careful after that!
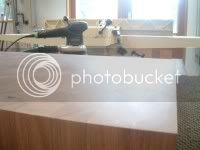
With everything sanded back to 600 grit on all sides, it’s ready for some oil.
And here’s the finished block after 8 coats of finishing oil. (This is the underside. Do you think I’ve got Shaker blood in me?)
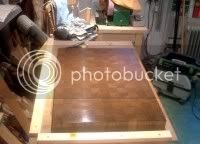
Some time quite soon, I’ll post the construction of the oak base.