9fingers
Established Member
Having persuaded Father Christmas to deliver a MIG welder, it seemed to be a 'good idea' to make the first project to be one for SWMBO.
The idea was to support 10 troughs of spring bulbs at first floor level across the front of the house which is about 7 metres wide.
Firstly weld up some brackets from 30 x 30 x 3mm steel angle having cut all the parts on the bandsaw and drilled all the holes for screws.
.
A total of 12 were made and sent off to the galvanisers to be baptised by total immersion in molten zinc. I was determined that they would not rust for a long time hence drilling all the holes before the treatment.
Each bracket is bolted into the house wall with M10 bolts and a stainless steel screw towards the lower end to hold the bracket away from the brickwork so rainwater is not retained by capilliary action.
All fitted to the wall. The black tube that is just visible is an extension to the automatic irrigation system that we use elsewhere for hanging baskets. this is on timeswitch and pressurised to 1 bar. Each trough will have its own metering nozzle matched to the size of the planter.
Now to fit the wood. 50 x 30 mm sawn iroko. A total of 6 lengths 6.6m long. The joints made with galvanised joining plates and stainless steel screws.
Two length on the horizontal parts of the brackets to carry the planters and four lengths to keep them in place and distract the eye from the bracketry.
The planters were planted with about 120 daffodil bulbs last November.
The overall view
Now all we need is the blooming flowers
:wink: :lol: :lol:
Not much woodwork but a fun project nevertheless.
Bob
The idea was to support 10 troughs of spring bulbs at first floor level across the front of the house which is about 7 metres wide.
Firstly weld up some brackets from 30 x 30 x 3mm steel angle having cut all the parts on the bandsaw and drilled all the holes for screws.
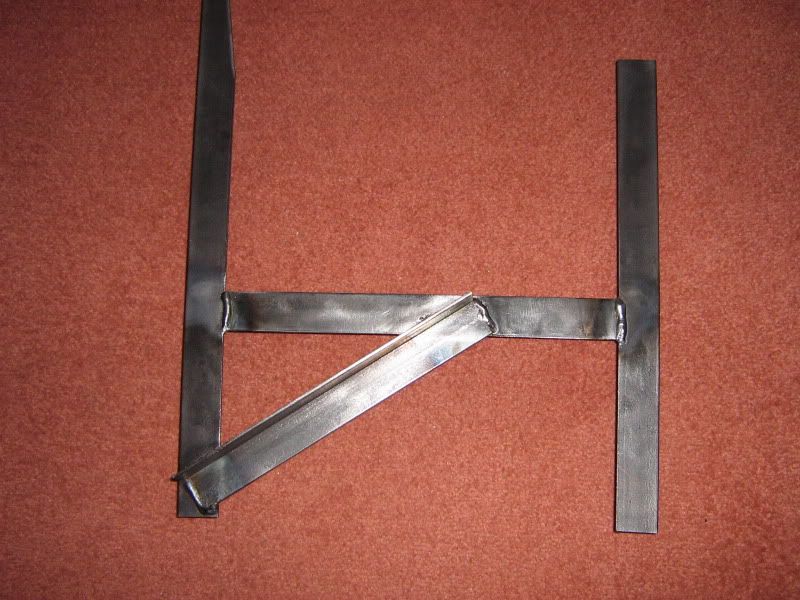
A total of 12 were made and sent off to the galvanisers to be baptised by total immersion in molten zinc. I was determined that they would not rust for a long time hence drilling all the holes before the treatment.
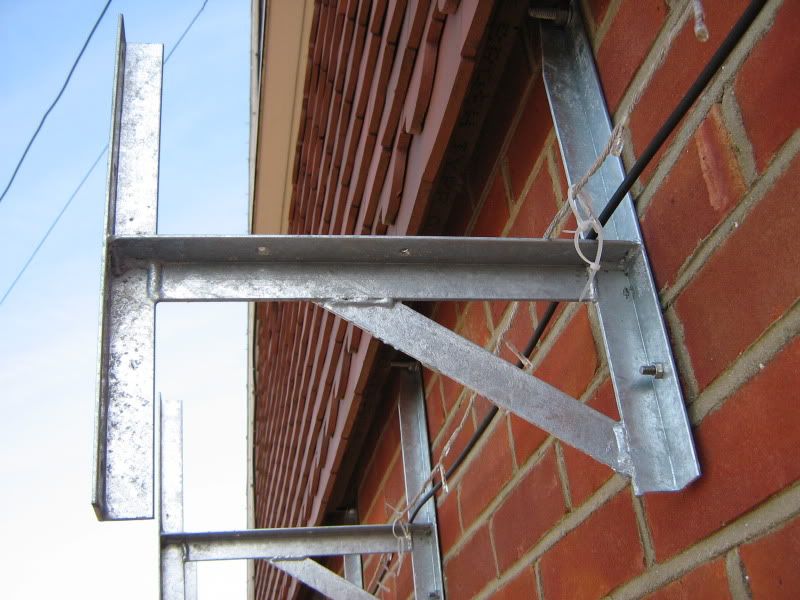
Each bracket is bolted into the house wall with M10 bolts and a stainless steel screw towards the lower end to hold the bracket away from the brickwork so rainwater is not retained by capilliary action.
All fitted to the wall. The black tube that is just visible is an extension to the automatic irrigation system that we use elsewhere for hanging baskets. this is on timeswitch and pressurised to 1 bar. Each trough will have its own metering nozzle matched to the size of the planter.
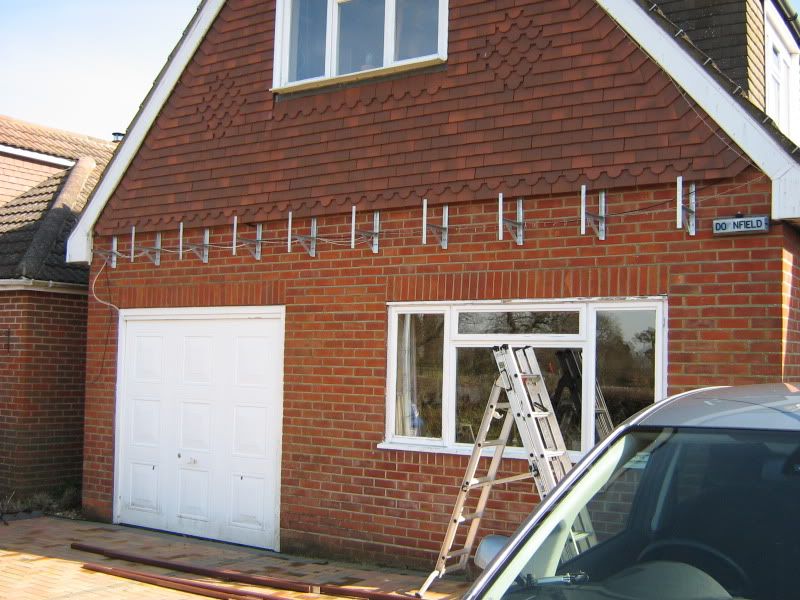
Now to fit the wood. 50 x 30 mm sawn iroko. A total of 6 lengths 6.6m long. The joints made with galvanised joining plates and stainless steel screws.
Two length on the horizontal parts of the brackets to carry the planters and four lengths to keep them in place and distract the eye from the bracketry.
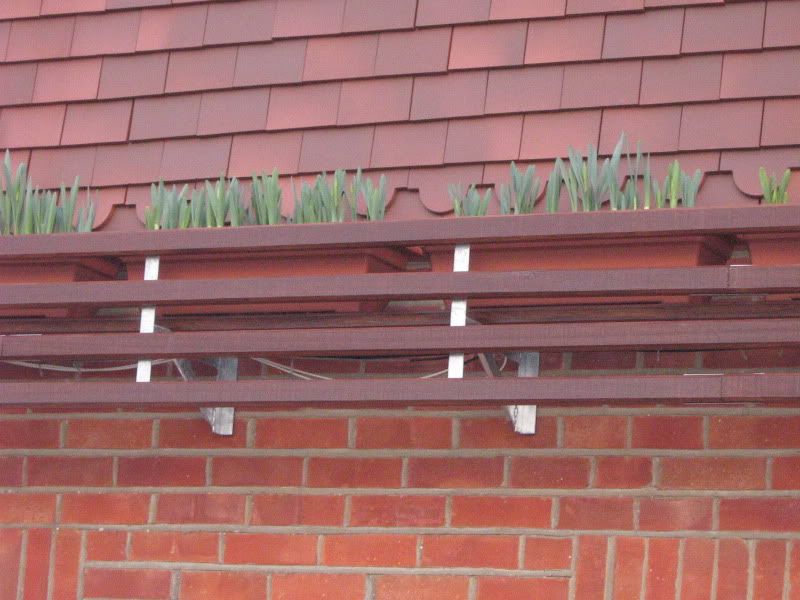
The planters were planted with about 120 daffodil bulbs last November.
The overall view
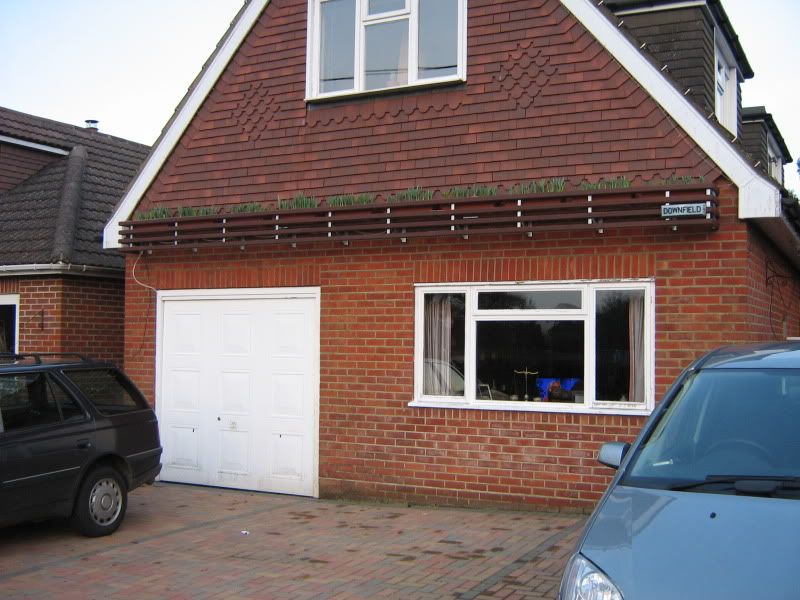
Now all we need is the blooming flowers
:wink: :lol: :lol:
Not much woodwork but a fun project nevertheless.
Bob