OPJ
Established Member
It's a new year, I've got a little bit of money to spare and I'm going to try and make several improvements to my workshop that I've been planning for the last three-years now. Namely, this involves fitting a suspended floor overheard, insulating the roof and then replacing the up-and-over garage doors with a pair of FLB timber doors. I owe many thanks to Mike Garnham in particular, among many others members who contributed with ideas and solutions in my posts on several UK forums.
Basically, this is a record of everything I should've done before buying any tools!!! ](*,)
On Tuesday, I officially made a start on the suspended floor. A week earlier, I ordered over £200-worth (free delivery!
) of treated sawn timber from BuildBase - I'd never used them before but, they have an online ordering system and I found several personal recommendations on this forum. I was amazed when they phoned me, five minutes after placing my order, with the offer of delivery for the very next-day! :shock: Are all builder's merchants like this?! I presume they just stockpile it at their yards and don't have any machining facilities, etc.
This is what arrived, conveniently loaded direct from the lorry by one of those mechanical arm/grab-things:
Those 7x2ins will be the joists. Where they didn't have the one 2.4m or nine 3.6m lengths that I'd ordered, they've given me ten lengths at 4.2m, with no extra charge!
Those 5x2ins will be used on the roof along with the 4x2ins - they couldn't offer any 2x2in so, I'll have to rip those down myself (just bought a brand-new saw blade, too! ;-)).
I was pleased to see that the folding sawhorses I made last year were capable of withholding all this weight:
A lot of the timber still feels quite damp and, for stress-graded wood (C24), there are some ruddy great knots - though, they are all live, rather than dead! What I haven't shown you yet are the seven sheets of 2400x600mm chipboard flooring on my workbench, which had to hand-balled off the lorry:
[Exotic turning blanks make for good bearers!! :twisted:]
As my order didn't arrive until just after 14.00, on day one, I only really had time to double-check my measurements and to start cutting the joists to length:
Of course; re-treating any cut ends is very important when working with tanalised timber:
Here are the offcuts I have so far, much of which will be used for noggings:
Had I known they were going to supply me with all this extra wood, I would never have ordered that extra 2.4m length, which was purely for blocking and additional noggings around the existing truss. Speaking of that lone truss in the centre of the roof, I've taken Mike's advice by fixing an extra 7x2in to one face. This new joist also had to be notched to fit over the pillars at either end. What you can't see is that I've managed to cut them about 10mm short but, once they're bolted in place, it shouldn't matter. I didn't appreciate how badly bowed the old 4x2in joist was until I sat this new one next to it... So, I've increased the floor level by about 5mm, to remove any further strain on that old bit of wood, which has already been riddled with woodworm in a past life.
Now, for the joist hangers (Simpson Strong-Tie JHA270). Here's a mock-up of what I wanted to achieve:
Basically, the new joists need to sit 32mm (1¼in) above the timber wall plates, so they're at the same level as the joist bolted to the truss. My problem was that the 'wraps' are about 20-25mm too long - rather than cutting them off, which would break the galvanising seal, I've bent them all back, as they won't tuck in behind the wall plates with the roof still on. I also had to bend the location tabs back as well, since I can't see them fitting in to a block wall with any ease!
What's worse than this though, was the state of my workshop at the end of the first day (an early finish, as well):

I still need to rip all these 4x2ins down to 2x2in. I was going hoping to do this today but, it's been raining all morning.
Thanks for looking so far. Coming up shortly is an update on yesterday's (Wednesday's) progress.
Basically, this is a record of everything I should've done before buying any tools!!! ](*,)
On Tuesday, I officially made a start on the suspended floor. A week earlier, I ordered over £200-worth (free delivery!
This is what arrived, conveniently loaded direct from the lorry by one of those mechanical arm/grab-things:
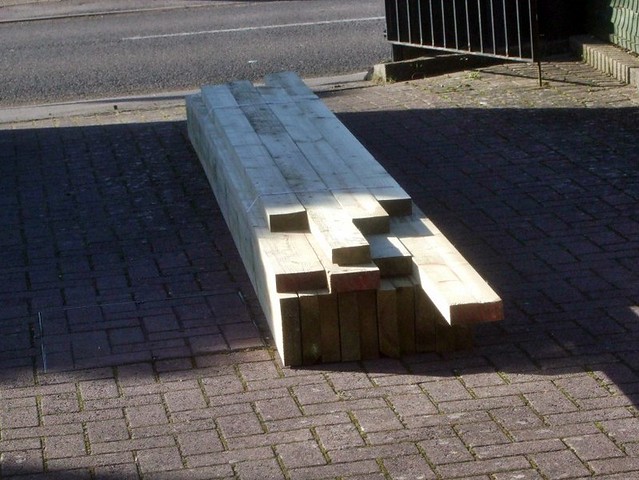
Those 7x2ins will be the joists. Where they didn't have the one 2.4m or nine 3.6m lengths that I'd ordered, they've given me ten lengths at 4.2m, with no extra charge!
I was pleased to see that the folding sawhorses I made last year were capable of withholding all this weight:
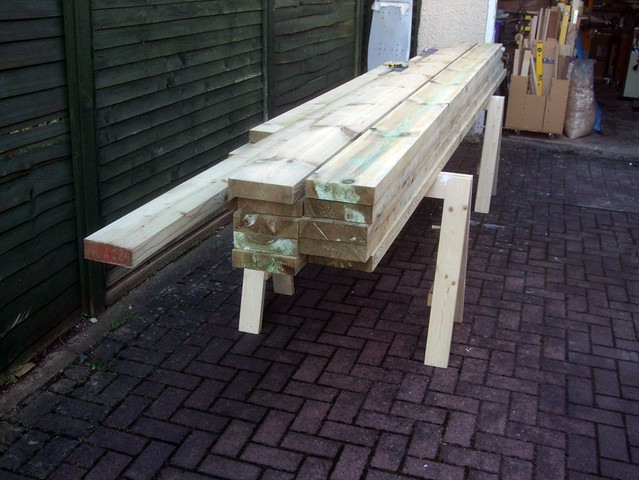
A lot of the timber still feels quite damp and, for stress-graded wood (C24), there are some ruddy great knots - though, they are all live, rather than dead! What I haven't shown you yet are the seven sheets of 2400x600mm chipboard flooring on my workbench, which had to hand-balled off the lorry:

[Exotic turning blanks make for good bearers!! :twisted:]
As my order didn't arrive until just after 14.00, on day one, I only really had time to double-check my measurements and to start cutting the joists to length:
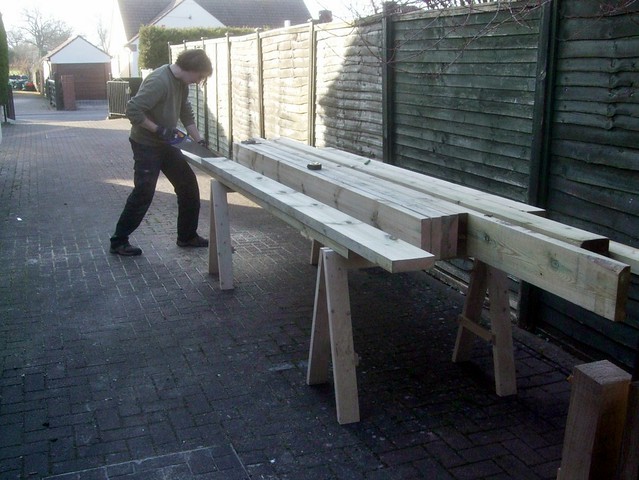
Of course; re-treating any cut ends is very important when working with tanalised timber:
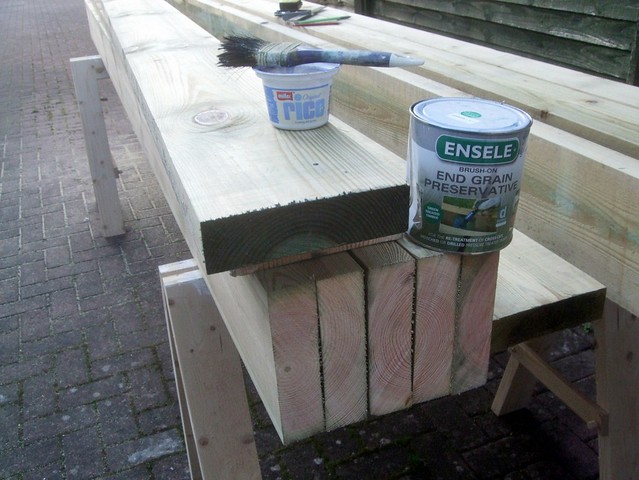
Here are the offcuts I have so far, much of which will be used for noggings:
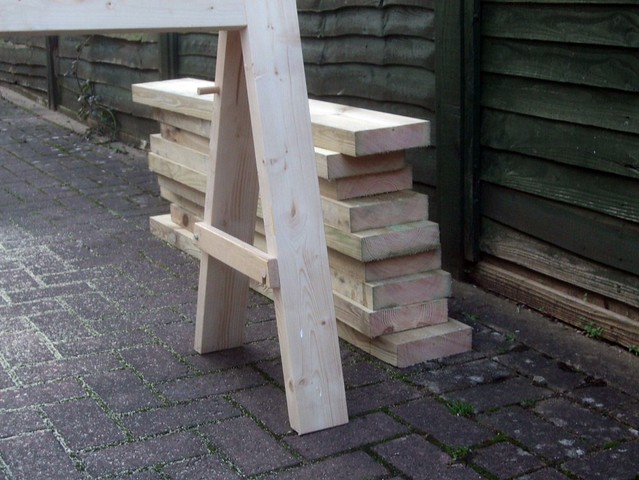
Had I known they were going to supply me with all this extra wood, I would never have ordered that extra 2.4m length, which was purely for blocking and additional noggings around the existing truss. Speaking of that lone truss in the centre of the roof, I've taken Mike's advice by fixing an extra 7x2in to one face. This new joist also had to be notched to fit over the pillars at either end. What you can't see is that I've managed to cut them about 10mm short but, once they're bolted in place, it shouldn't matter. I didn't appreciate how badly bowed the old 4x2in joist was until I sat this new one next to it... So, I've increased the floor level by about 5mm, to remove any further strain on that old bit of wood, which has already been riddled with woodworm in a past life.
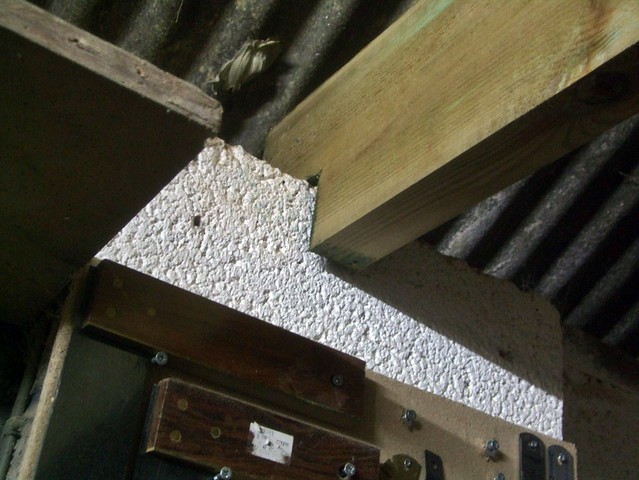
Now, for the joist hangers (Simpson Strong-Tie JHA270). Here's a mock-up of what I wanted to achieve:
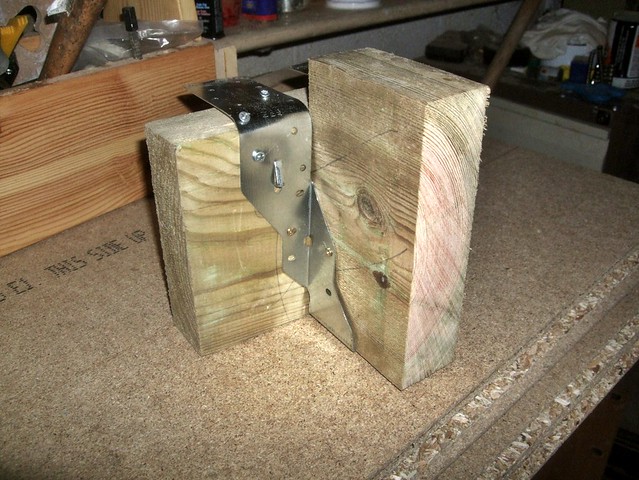
Basically, the new joists need to sit 32mm (1¼in) above the timber wall plates, so they're at the same level as the joist bolted to the truss. My problem was that the 'wraps' are about 20-25mm too long - rather than cutting them off, which would break the galvanising seal, I've bent them all back, as they won't tuck in behind the wall plates with the roof still on. I also had to bend the location tabs back as well, since I can't see them fitting in to a block wall with any ease!
What's worse than this though, was the state of my workshop at the end of the first day (an early finish, as well):
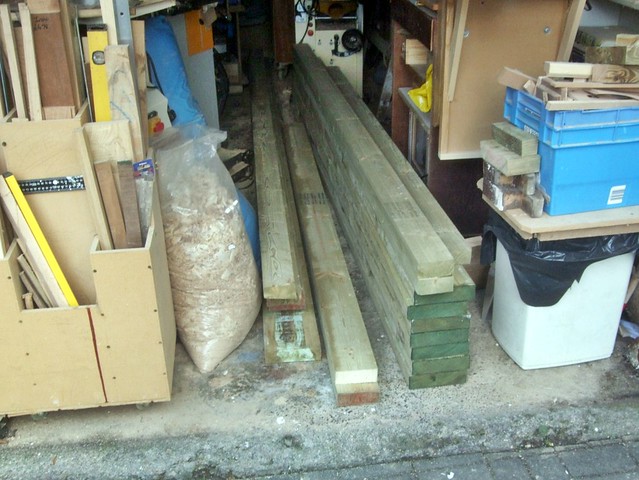
I still need to rip all these 4x2ins down to 2x2in. I was going hoping to do this today but, it's been raining all morning.
Thanks for looking so far. Coming up shortly is an update on yesterday's (Wednesday's) progress.