Allubo
Established Member
Last week we finished an oak dining table commision, the table was made for a fairly big kitchen to seat a maximum of 12 so settled on the basic 8x4 size. The client wanted something to similar to his original table just bigger.
We settled on a 36mm oak veneered top sitting on 100mm square legs with a triple mitred frame.
Here's how it was done.
The timber used was 65mm prime square sawn oak. So first things first, labelling and machining.
There are two 54mm thick ply runners which go down the centre of the frame for support in the centre of the table. These stop the top from sagging in the middle and give reassurance should the client need to stand on it.
Because I used 65mm stock I planed the leg components down to 54mm and glued together to make 108mm square pieces, because I would machine this again after, I didn't use clamping blocks.
The legs were the centre piece of a triple mitre, we made a scale model of this first to test how well we could do it and were happy so then moved on to the real components. Because the rails were 100x50mm we could allow for the inside of the leg to remain to add to glueing surface.
Two initial cuts gave the outer faces to which the rails would meet up to and the. I removed most of the material with a hand saw,
Then it went back on the dim saw to nibble away the remaining material.
We settled on a 36mm oak veneered top sitting on 100mm square legs with a triple mitred frame.
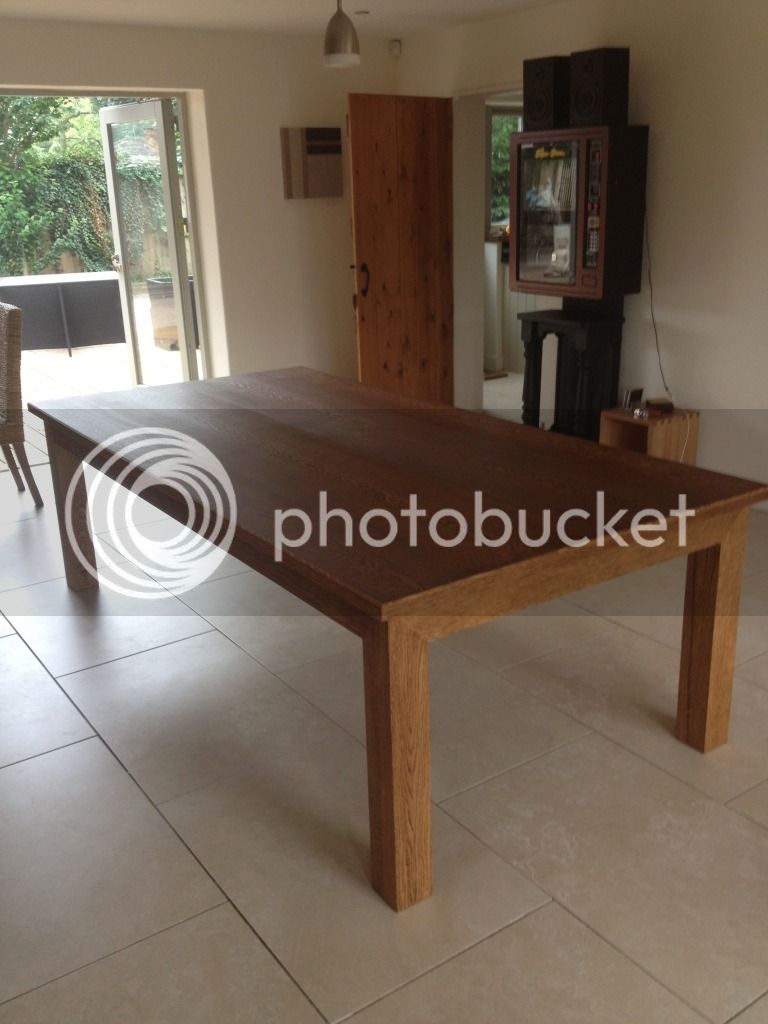
Here's how it was done.
The timber used was 65mm prime square sawn oak. So first things first, labelling and machining.
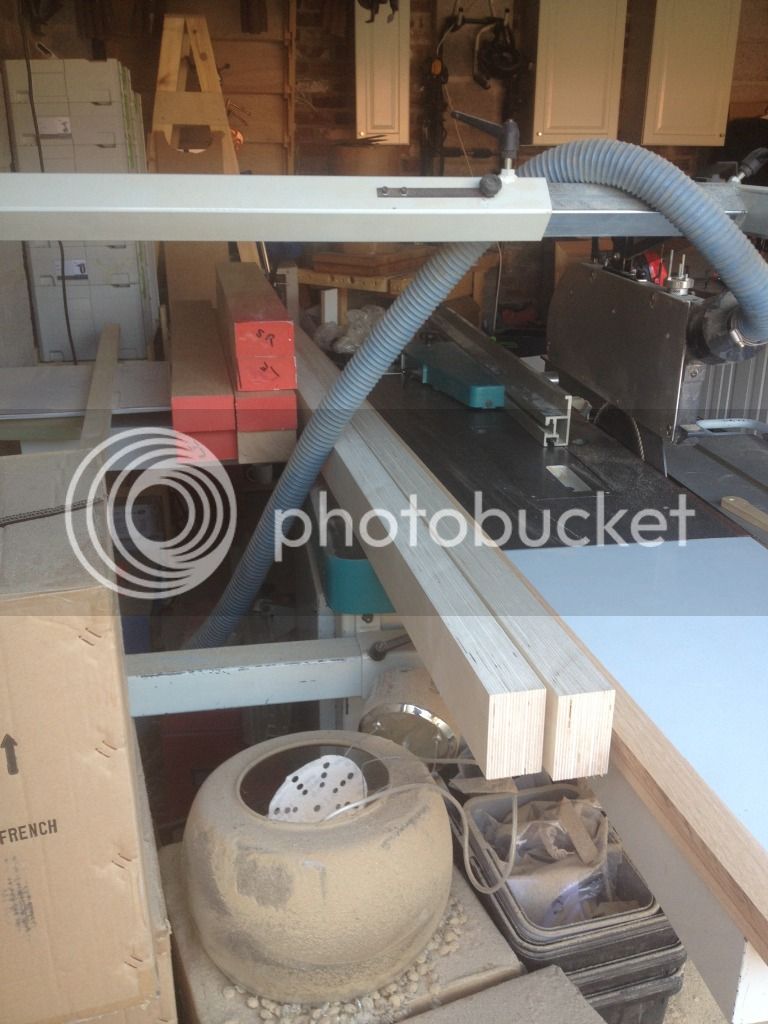
There are two 54mm thick ply runners which go down the centre of the frame for support in the centre of the table. These stop the top from sagging in the middle and give reassurance should the client need to stand on it.
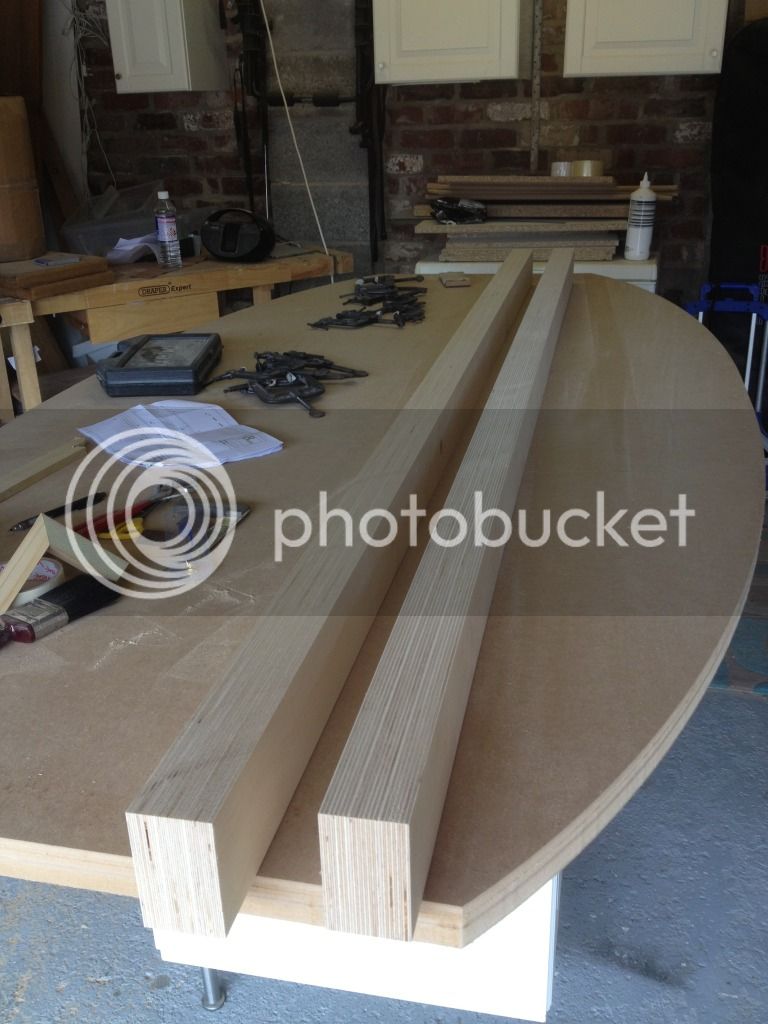
Because I used 65mm stock I planed the leg components down to 54mm and glued together to make 108mm square pieces, because I would machine this again after, I didn't use clamping blocks.
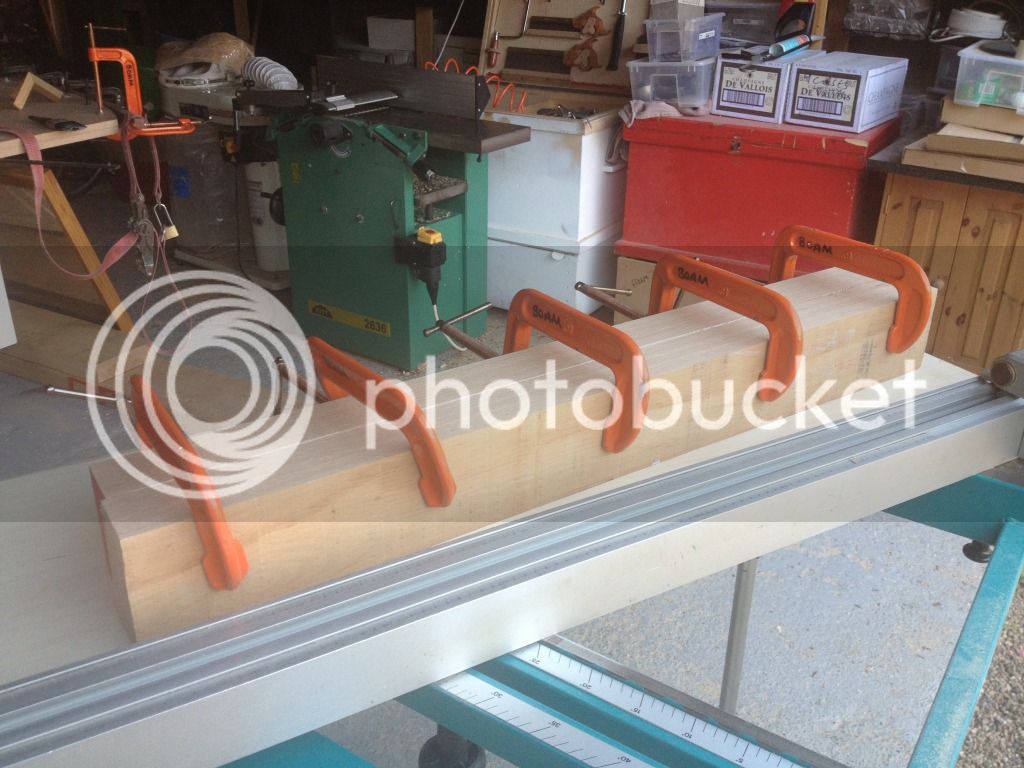
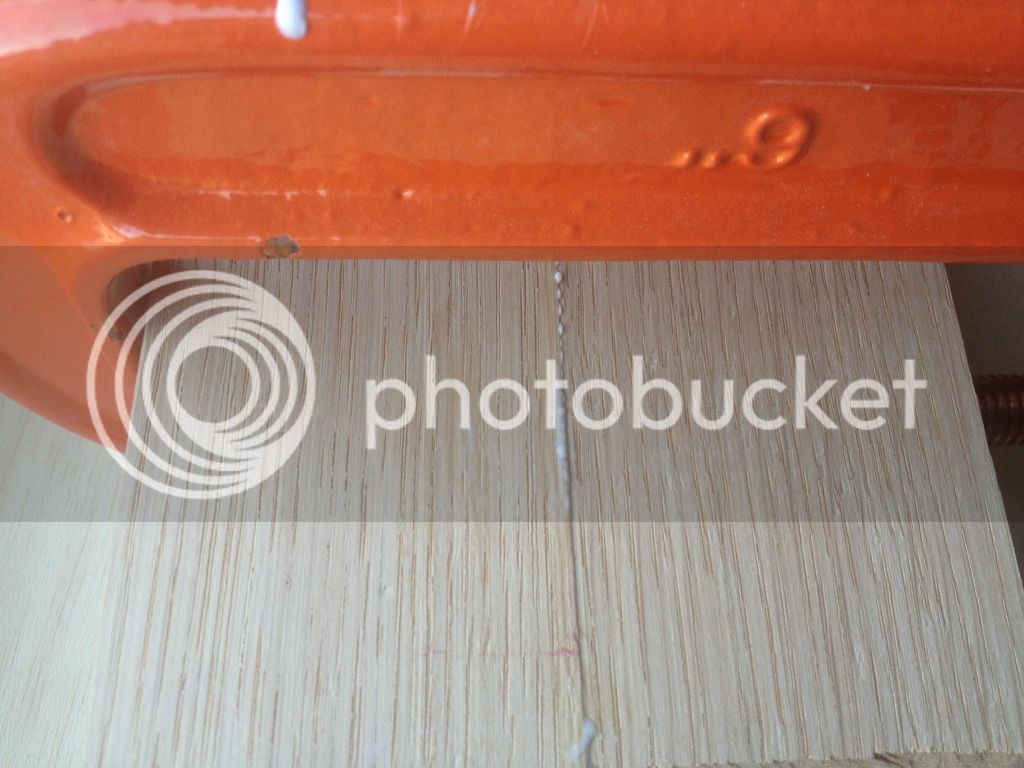
The legs were the centre piece of a triple mitre, we made a scale model of this first to test how well we could do it and were happy so then moved on to the real components. Because the rails were 100x50mm we could allow for the inside of the leg to remain to add to glueing surface.
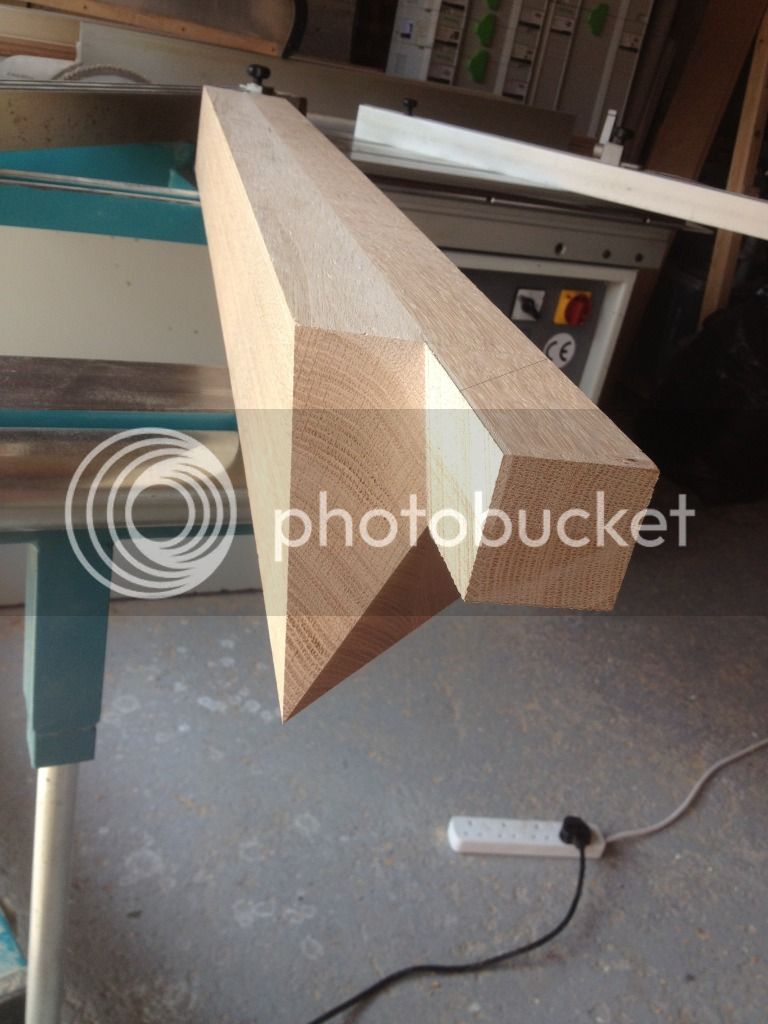
Two initial cuts gave the outer faces to which the rails would meet up to and the. I removed most of the material with a hand saw,
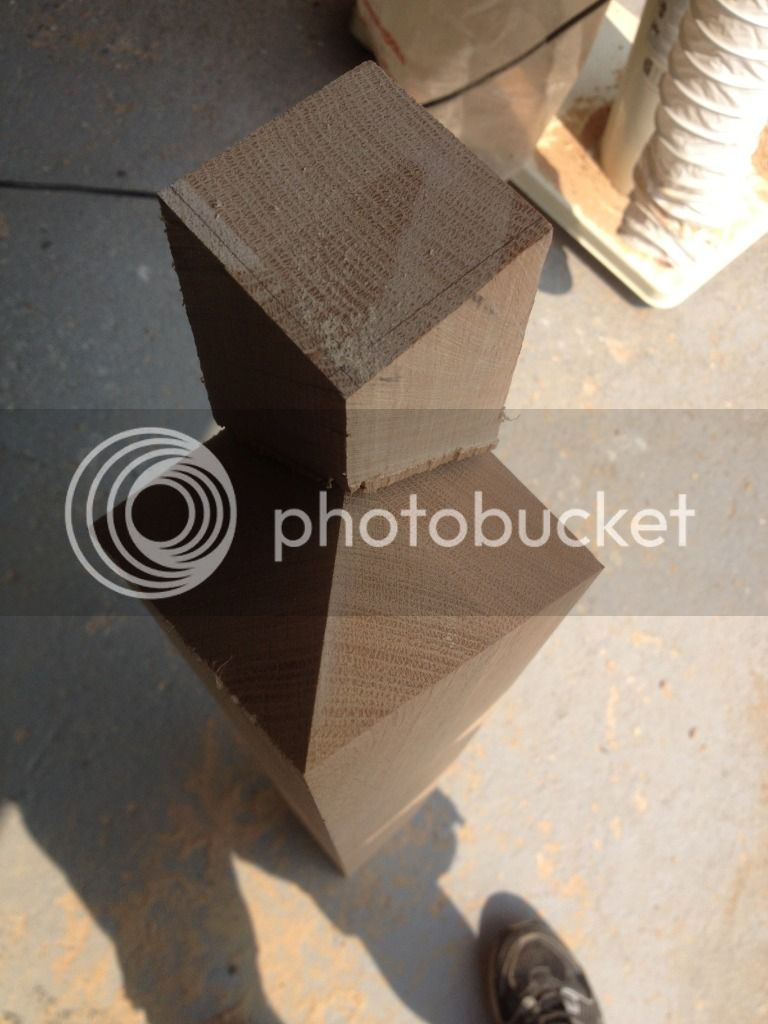
Then it went back on the dim saw to nibble away the remaining material.
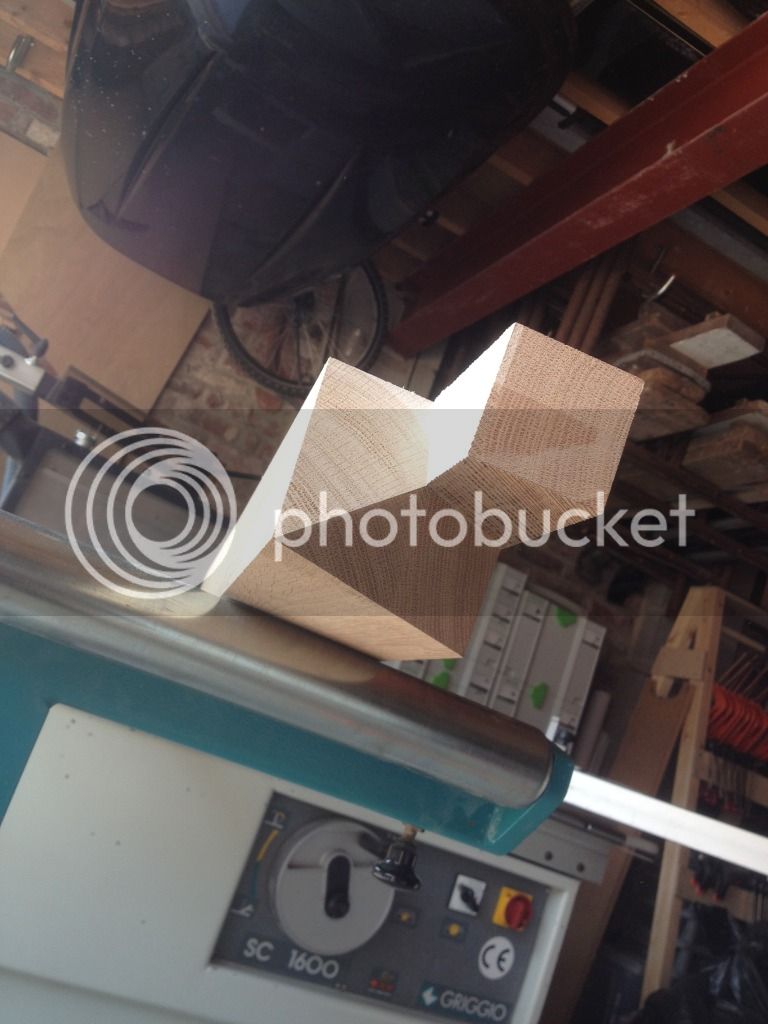