mike s
Established Member

im using 1/2" mild steel round bar for the body of the tool. the length of the bar on this tool is 40cm.
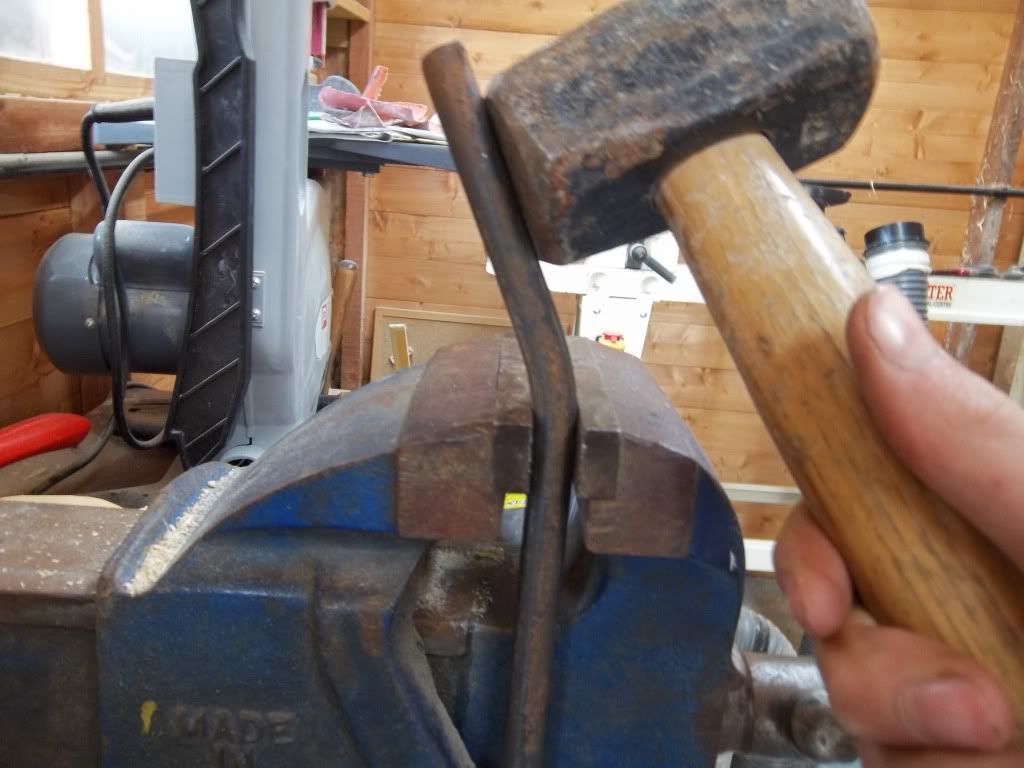
10-12cm down from the top i used a club hammer to make the first bend
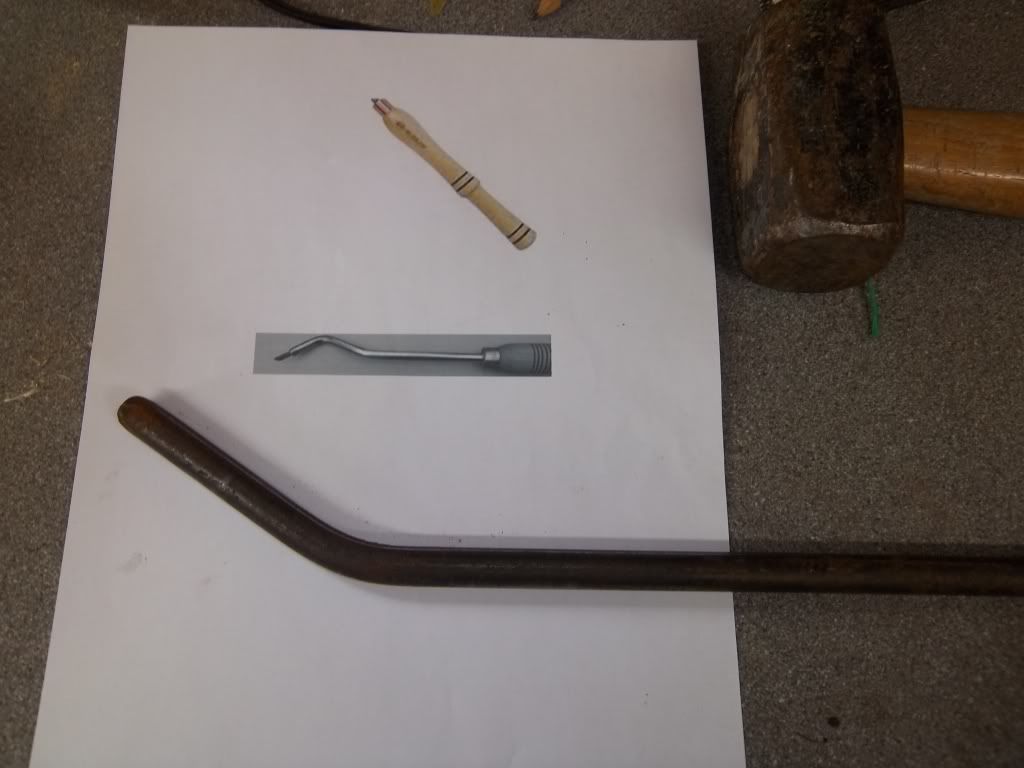
the first bend done
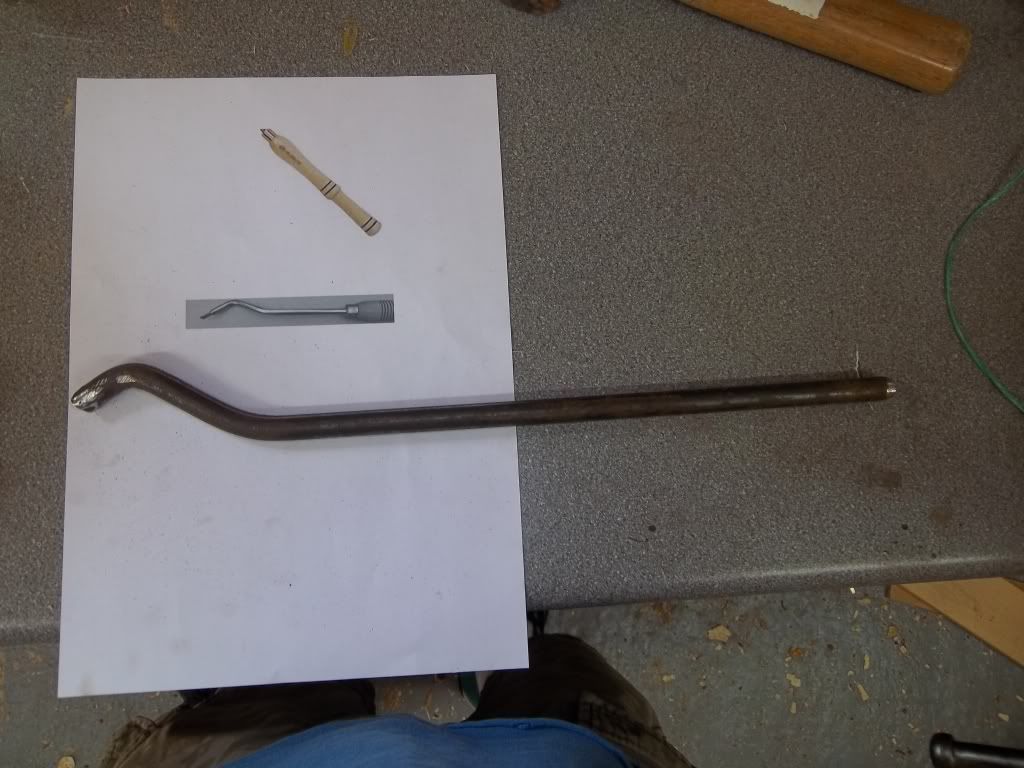
the second bend done
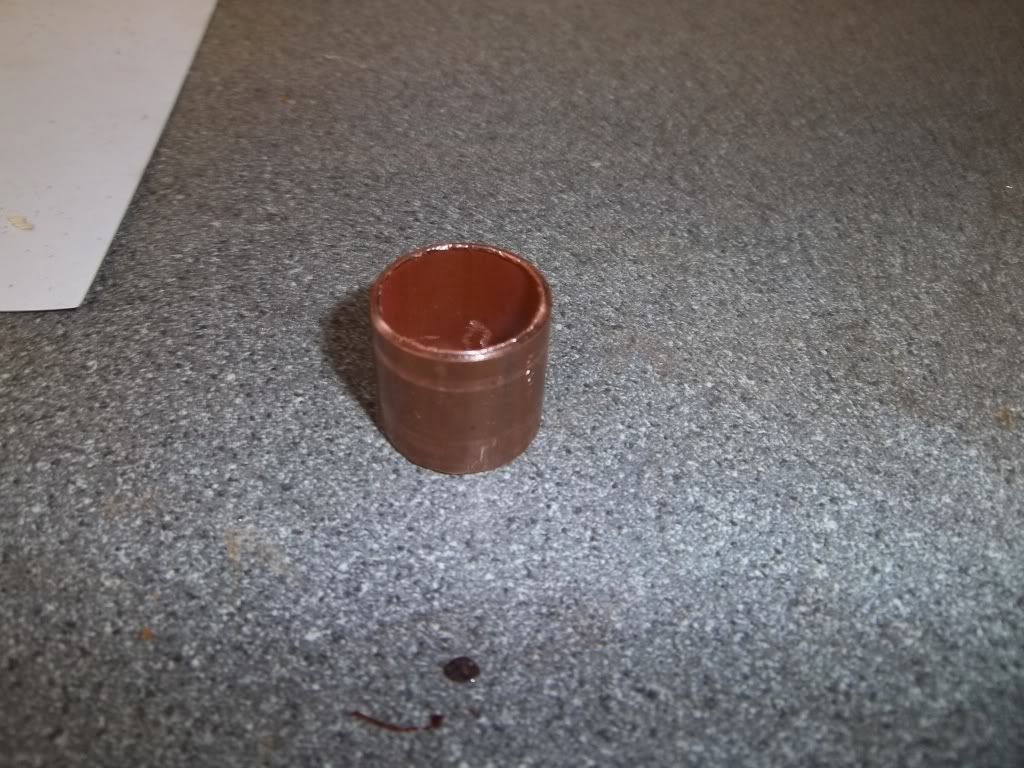
the handle ferrule is 22mm copper pipe, i cut off an inch long section
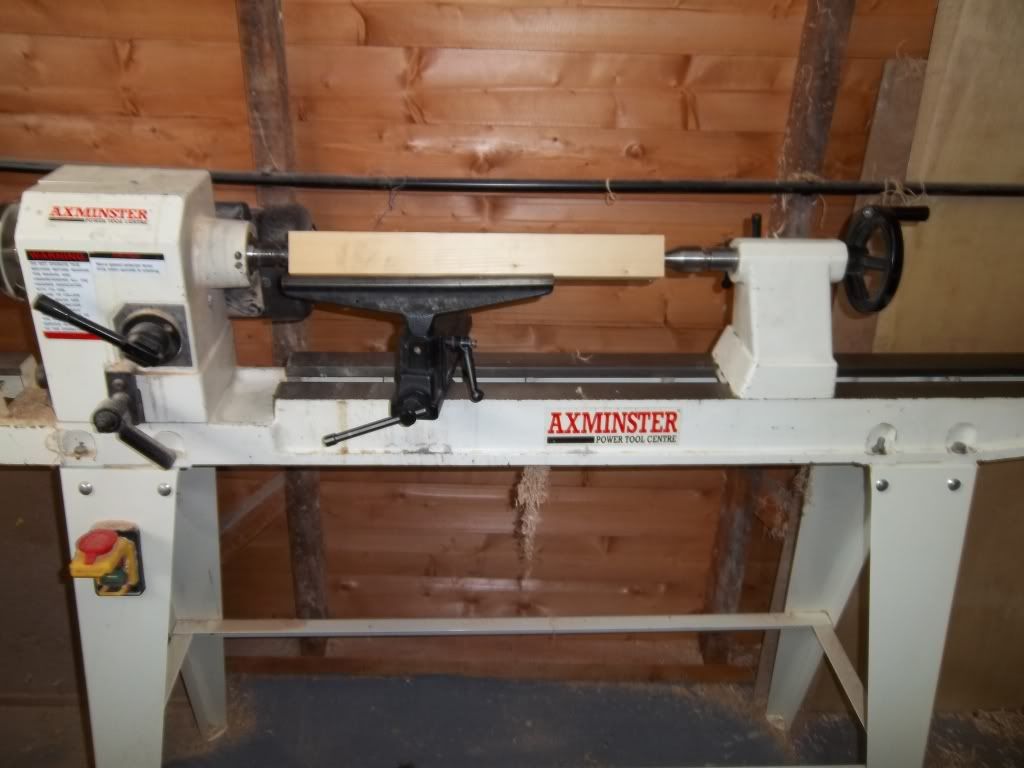
i dont currently have any nice wood big enough so for this handle i used pine
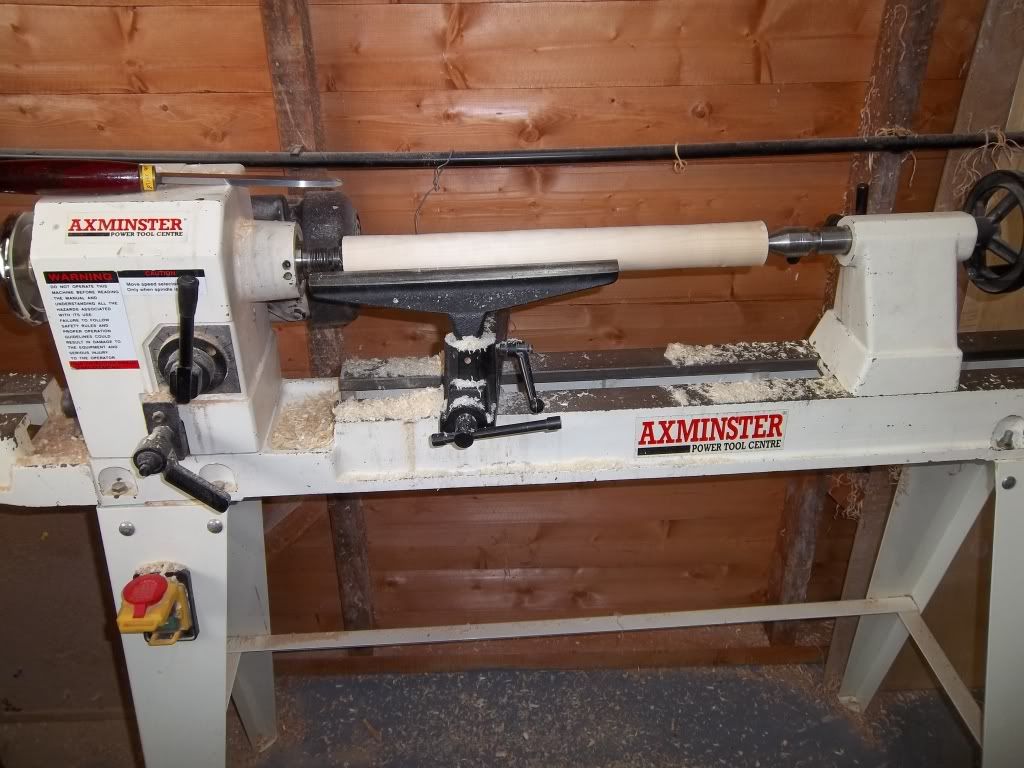
turned to round
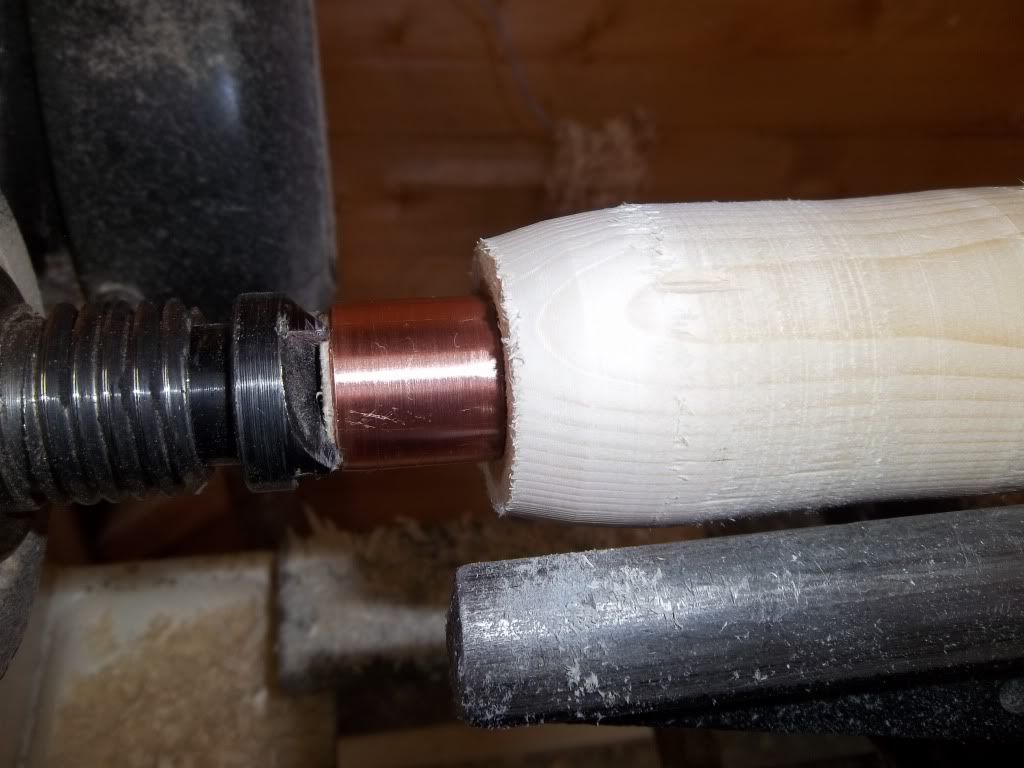
fixing the ferrule
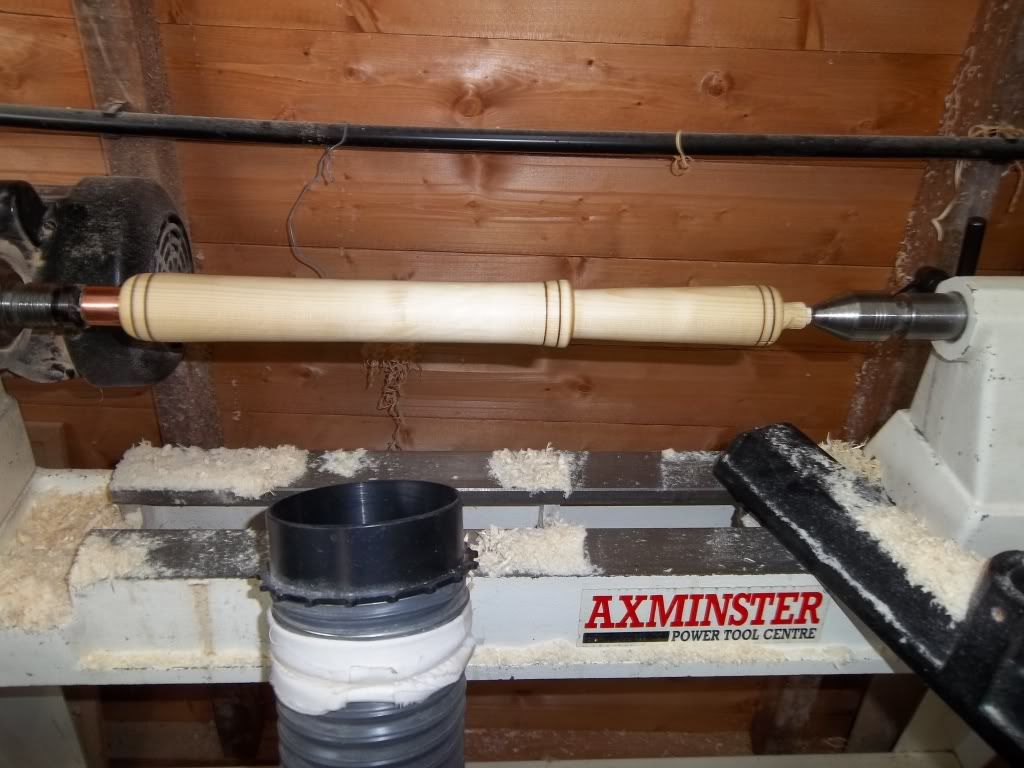
turning done. i copied the easywoodtool handle, only time will tell if i like to turn with it or not.
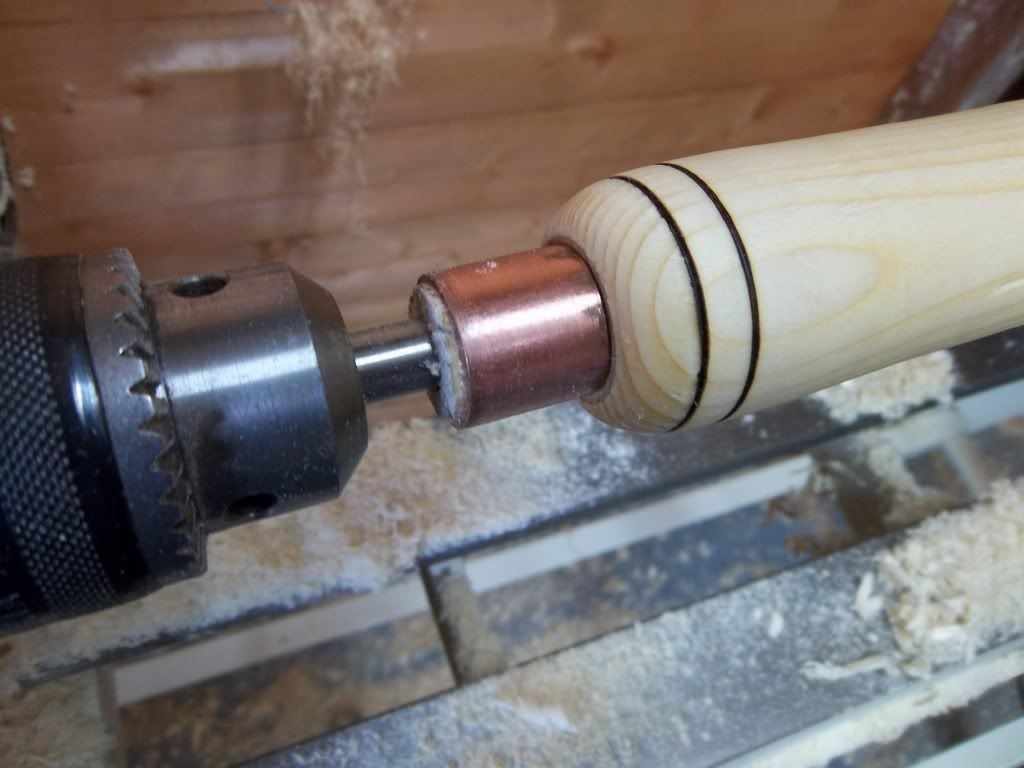
next there was the problem of drilling a straight hole down the handle
i did this by putting the drill chuck in the lathe with a 12mm drill bit and pretty much put the handle between centres while turning the tailstock handle to drive the handle into the turning drill bit
as the tailstock is supporting the handle on the point it was turned on, the hole is directly down the centre of the handle. (or near enough)
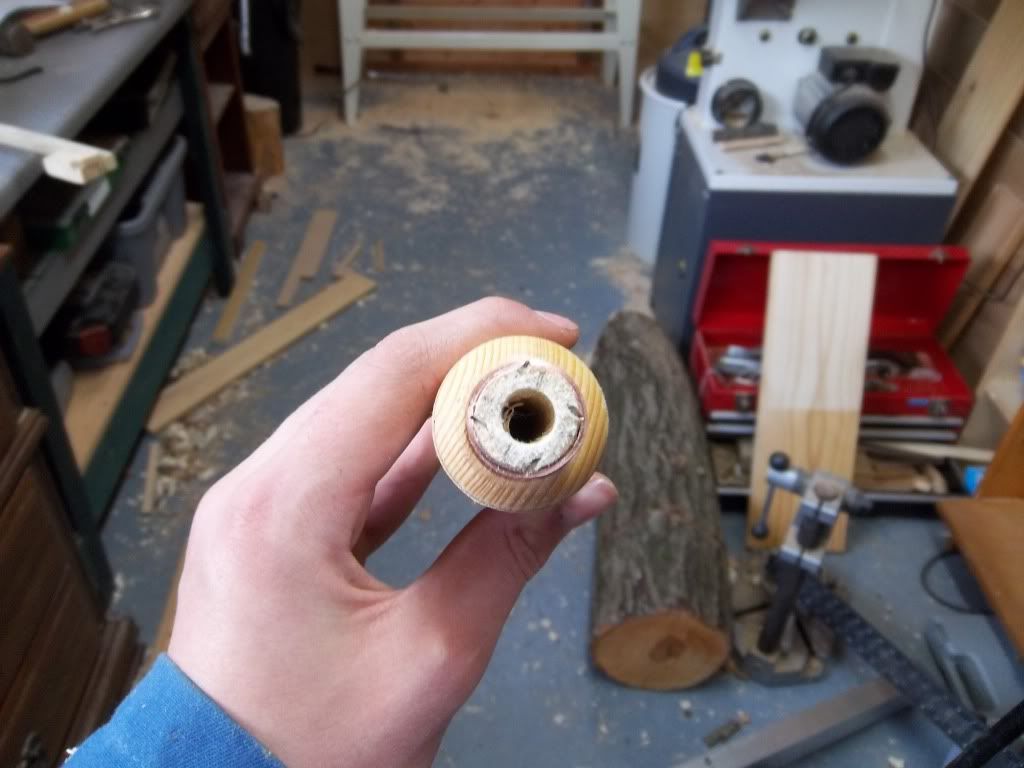
the drilled hole. a few mm less than the 1/2" stock so it is a very tight fit
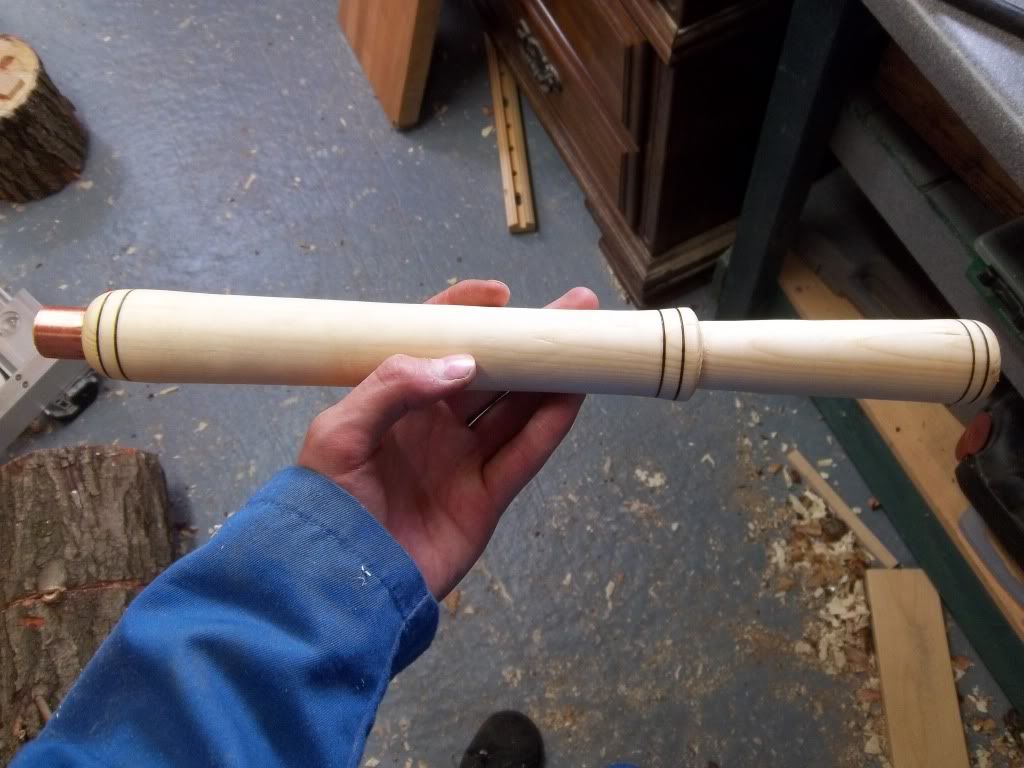
the completed handle
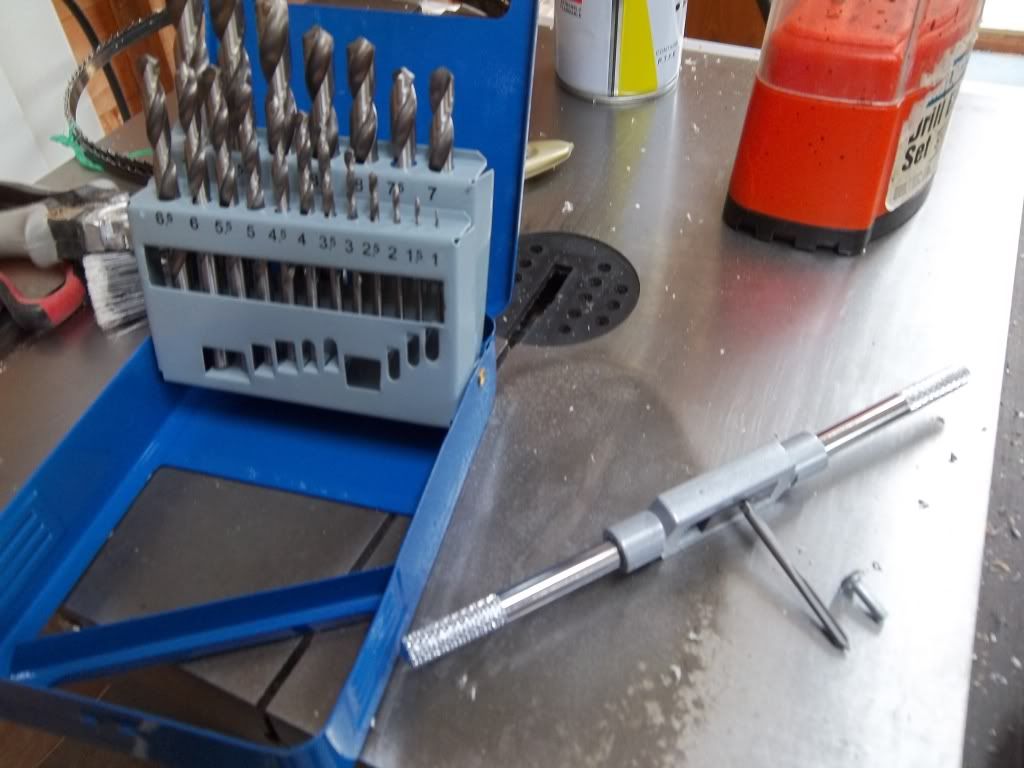
i forgot to take photos of the drilling
the hss tips im using will be 1/4" so i drilled a 1/4" hole about 3cm down the tip of the tool and tapped a set screw to hold the tip in place

the holes and set screw, the end of the steel is a bit battered from the hammering it took when bending

the finished tool
when the hss rod arrives i will cut a 1" section off, sharpen it to the profile i want and then put it into the tool and crank down on the set screw
thanks to silverbirch, jason, chas and others for the tips and advice i needed when making this tool.